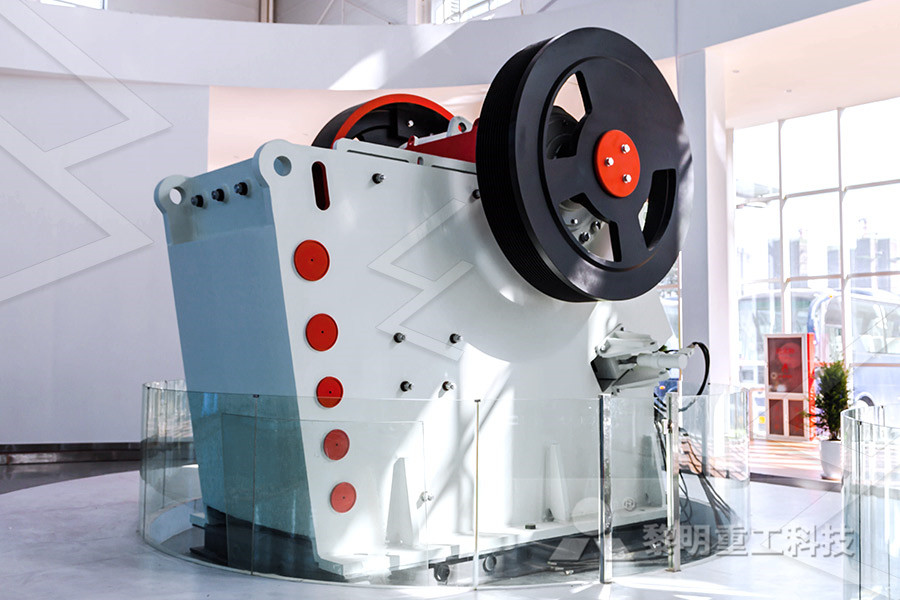
Magnetic Separator Technology Minimizes Compressor Downtime
Magnetic separator technology is the key to minimizing compressor downtime More than 80 percent of centrifugal gas compressors manufactured today are equipped with dry gas seals Dry gas seals are a noncontact seal with a running gap of approximately 3 to 4 microns in size between the primary and mating seal ringsRemoving Buffer Gas Contamination will reduce Seal FailureMagnetic separator technology is the key to minimizing compressor downtime Over 80% of centrifugal Magnetic Separator Technology Minimizes Compressor Black powder damages the pump, compressor and turbine components increasing downtime and reducing production values" The Black Powder Magnetic Separator System was developed as a solution to pipeline and processing problems caused by black powder Utilizing rare earth technology, The Black Powder Magnetic Separator System enables highly efficient separation of ferrous and in Magnetic Separator Technology Is Solution for Black PowderBPS Magnetic Separator Application in oil and gas upstream, midstream and downstream, from exploration to refinement and distribution What's New How a magnetic separator can reduce your singleuse filter costs October 13, 2020 How Dax Oil used magnetic separation to prevent black powder from plugging off their crude unit heat exchanger July 7, 2020 How Magnetic Elements Magnetic Separator Applications I Upstream Midstream As anyone who runs an air compressor facility knows, downtime can be a very costly problem because when the machines fail to function, it halts production A company that fails to enact timely maintenance protocols runs the risk of encountering performance issues with greater frequency Such occurrences are hard to predict, but can arise at the worst moments, such as when a highcost Industrial Air Compressor Preventative Maintenance
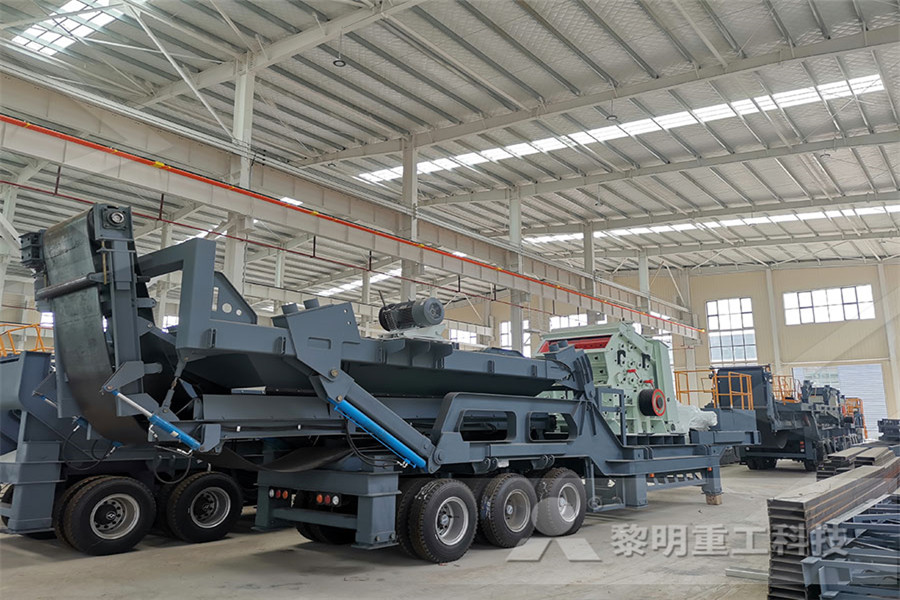
Design and fabrication of magnetic coolant filter: AIP
Separation of metallic chips from the coolants by using magnetic coolant separation has proven a good management and maintenance of the cutting fluid By removing the metallic chips, the coolant life is greatly extended, increases the machining quality and reduces downtime Above being the case, a magnetic coolant filter is developed which utilizes high energy permanent magnets to develop BPS Magnetic Separator Systems require cleaning rather than filter disposal; each system offers long life service and utilizes minimal consumables The high loading capacity allows for extended maintenance intervals of 6 months to 1 year depending on the contamination in the particular system Extended life of critical operating systemsBlack Powder Solutions I Magnetic Separator Systems for Magnetic separation is the process of separating components of mixtures by using magnets to attract magnetic materials The process that is used for magnetic separation detaches nonmagnetic material with those that are magnetic This technique is useful for not all, but few minerals such as ferromagnetic (materials strongly affected by magnetic fields) and paramagnetic (materials that are Magnetic separation WikipediaAir separation compressors are widely used in the sectors of air separation plants of large chemical industry and coal chemical industry Shaangu air separation compressor train serves for the air separation plants from 20,000 Nm³/h to 150,000 Nm³/h The air separation compressor train are usually design as one air compressor and one compression booster for internal compression process Air Separation Compressor Shaangu SiteThe TouchFree ™ compressors use active magnetic bearings – the compressor’s rotating parts levitate in a magnetic field and do not come into contact with anything Therefore, there are no wearing parts to replace or repair, and the compressor does not need any oil lubrication or oil changes or produce any oily waste The intake air filters need to be replaced depending on the site Tamturbo® technology minimizing downtime in packaging
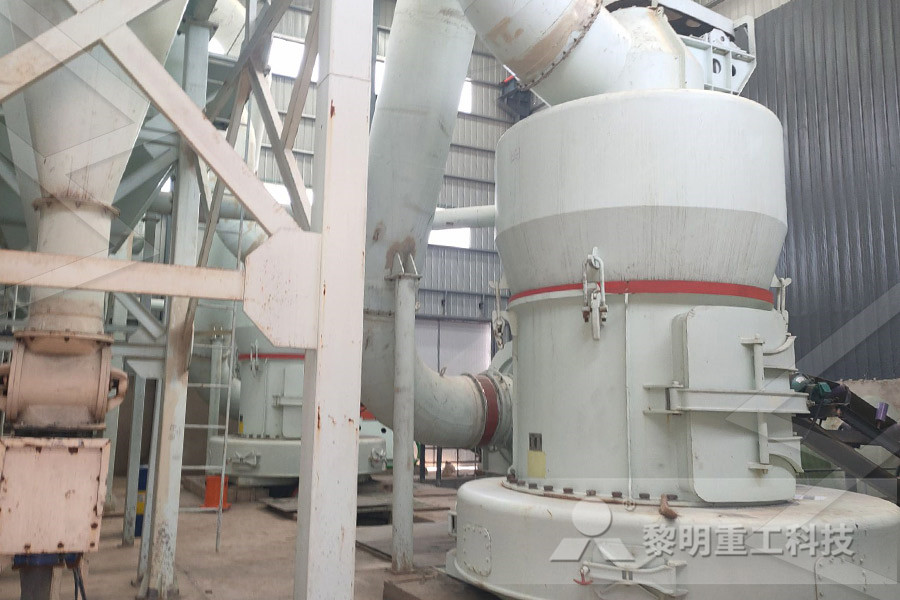
Pulp and Paper Industrial Compressed Air Solutions
TouchFree ™ technology helps minimize downtime The Tamturbo® TouchFree ™ compressors use active magnetic bearings – the compressor’s rotating parts levitate in a magnetic field and do not come into contact with anything Therefore, there are no wearing parts to replace or repair, and the compressor does not need any oil lubrication or oil changes or produce any oily waste The The coolant then moves through a prefilter that removes floating chips before flowing into a separator tank that contains the manufacturer’s custom, permanent separator element The separated tramp oil is held in the tank until it can be drained, while the cleaned coolant recycles continuously to the sump at high flow rate The high recirculation rate rapidly turns over the sump, ensuring CoolantCleaning Device Slashes Downtime Modern Machine compressor coolers and drive motor ensure optimum cooling and performance Drawing ambient air directly across the coolers and motor through separate zones eliminates preheating and results in longer lubricant life and a cooler running motor This also results in much lower approach temperatures, improving moisture separation and air qualityIndustrial Rotary Screw Compressors Separation of metallic chips from the coolants by using magnetic coolant separation has proven a good management and maintenance of the cutting fluid By removing the metallic chips, the coolant life is greatly extended, increases the machining quality and reduces downtime Above being the case, a magnetic coolant filter is developed which utilizes high energy permanent magnets to develop Design and fabrication of magnetic coolant filter: AIP Air separation compressors are widely used in the sectors of air separation plants of large chemical industry and coal chemical industry Shaangu air separation compressor train serves for the air separation plants from 20,000 Nm³/h to 150,000 Nm³/h The air separation compressor train are usually design as one air compressor and one compression booster for internal compression process Air Separation Compressor Shaangu Site
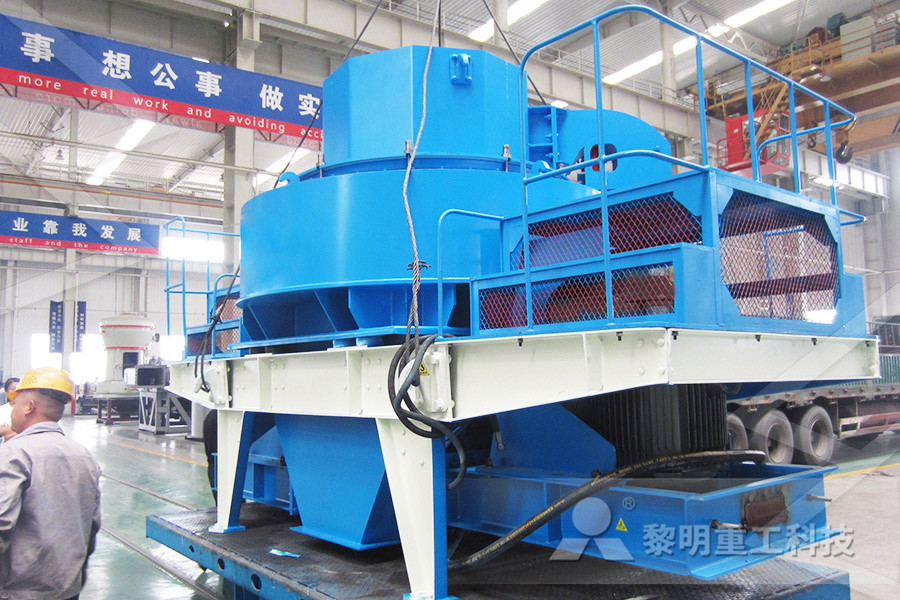
Home Minprotech
Minprotech established the first Wet High Intensity Magnetic Separation (WHIMS) plant for chromite recovery in South Africa Minprotech is the market leader utilizing WHIMS technology to extract chromite from UG2 and LG reefs Our first full production plant was built and operated by us for a major chrome producer on the Eastern Chrome Mines Minprotech subsequently procured another five As a leader in highfield superconducting magnet technology, Cryomagnetics has the experience and capability to manufacture high field magnetic separation systems Typical superconducting magnet–based laboratory systems of the past operate at 5 to 6 Tesla Cryomagnetics’ 9 Tesla system is the premiere system for testing and analysis of today Optimized designs combined with new technology Magnetic Separation Systems Cryomagnetics, incFollowing years of experience with multiple compressor technologies of oillubricated and “oilfree” screw compressors and traditional turbo compressors, a High Speed Tamturbo compressor with Permanent Magnet Motor Technology and Active Magnetic Bearings was installed in 2018 In this compressor, integrated on a single shaft, compressor components levitate without any mechanical Top quality compressed air for Automotive and Aviation Precision technology rotary screw airend with advanced rotor profile and slow rotor speed ensures 24/7 reliability, high airflow output and low energy consumption High efficiency, MEPS compliant electric motor directly reduces energy consumption and carbon footprint Stardelta motor starter reduces both peak energy demand and shockloading of the compressor’s mechanical and electrical LS Series 185 to 75 kWThe TouchFree ™ compressors use active magnetic bearings – the compressor’s rotating parts levitate in a magnetic field and do not come into contact with anything Therefore, there are no wearing parts to replace or repair, and the compressor does not need any oil lubrication or oil changes or produce any oily waste The intake air filters need to be replaced depending on the site Tamturbo® technology minimizing downtime in packaging
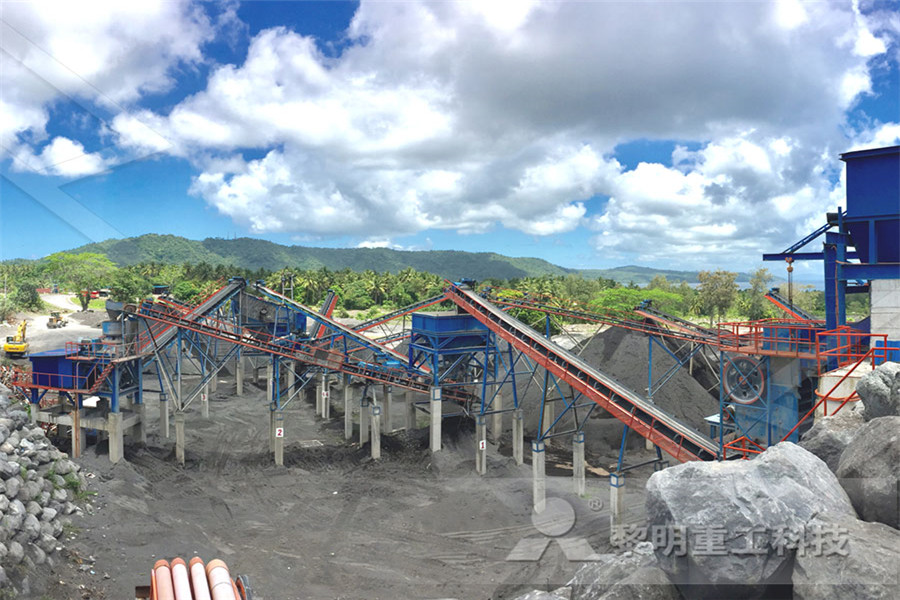
Pulp and Paper Industrial Compressed Air Solutions
TouchFree ™ technology helps minimize downtime The Tamturbo® TouchFree ™ compressors use active magnetic bearings – the compressor’s rotating parts levitate in a magnetic field and do not come into contact with anything Therefore, there are no wearing parts to replace or repair, and the compressor does not need any oil lubrication or oil changes or produce any oily waste The The magnetic separator was run over an initial calibration period to determine the average volume of contamination in the crude Since then, the magnetic separator is cleaned weekly after ~15,000 barrels of crude flow through it The average amount How Dax Oil used magnetic separation to prevent black compressor coolers and drive motor ensure optimum cooling and performance Drawing ambient air directly across the coolers and motor through separate zones eliminates preheating and results in longer lubricant life and a cooler running motor This also results in much lower approach temperatures, improving moisture separation and air qualityIndustrial Rotary Screw Compressors Separation of metallic chips from the coolants by using magnetic coolant separation has proven a good management and maintenance of the cutting fluid By removing the metallic chips, the coolant life is greatly extended, increases the machining quality and reduces downtime Above being the case, a magnetic coolant filter is developed which utilizes high energy permanent magnets to develop Design and fabrication of magnetic coolant filter: AIP Traditional magnetic filters are unable to filter highheat transfer oil The plant required a highheat magnetic filtration technology to capture corrosion contamination that was damaging seals and gaskets downline The transfer fluid operates between 295° C and 310° C The damaged components and leaks were causing unscheduled downtimePower Generation OEI Magnetic Filtration For Your Equipment
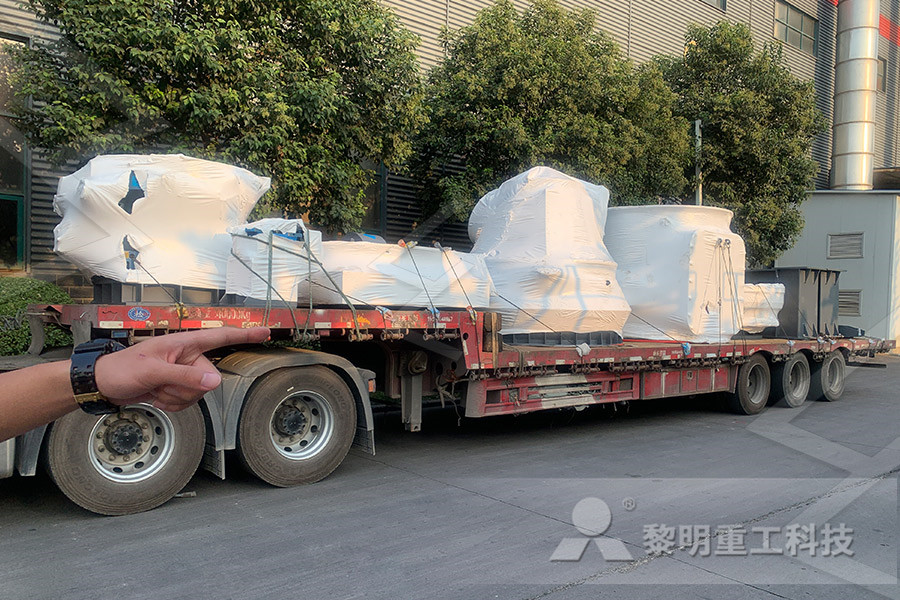
A 124″ warm bore superconducting ironclad high gradient
A 124″ warm bore superconducting high gradient magnetic separator has been designed, fabricated, installed, tested, and placed in operation in March 1989 It is used to process clap The maximum operating field of 2 T is generated in 60 s with equal time for decap The unit weighs approx 500 ton with a stored energy of 76 MJ The iron enclosure insures a uniform and linear field to 2 T This speed‐to‐alert helps users minimize unplanned downtime The LS160 Series includes offerings from 125200 hp and 90160 kW With multiple offerings, the units provide options to help customers meet their specific application needs, including steel mills, tire plants, automotive, forging plants, chemical processing, paper industry and large manufacturing facilities, among othersSullair Introduces LS160 Rotary Screw Compressor with As a leader in highfield superconducting magnet technology, Cryomagnetics has the experience and capability to manufacture high field magnetic separation systems Typical superconducting magnet–based laboratory systems of the past operate at 5 to 6 Tesla Cryomagnetics’ 9 Tesla system is the premiere system for testing and analysis of today Optimized designs combined with new technology Magnetic Separation Systems Cryomagnetics, incBuy Senator ES4 Rotary Screw Air Compressor for sale Ideally suited for smalltomedium industrial applications with heavy compressed air demand and working pressure of up to 10 bar The featurerich Senator ES4 is fully integrated, tankmounted packages supplied ready for use Motor Power 4 kW (55 hp) Free Air Delivery 060 m³/min (21 cfm) Working Pressure 8 bar (116 psi) Optional Buy Senator ES4 Rotary Screw Air Compressor for Sale
- gypsum producers destroy plant in india
- cement ball mill notebook
- magnetic separation of iron ore sand
- celestine roller mill supplier
- kem crusher liner manufacturers
- how to build grinder machine
- mobile crome refining and processing plant
- spare part jaw crusher in somalia
- mulch and aggregate rock hill sc
- equipment 300tph in cement manufacturing
- bng bo gi my sng rung lp
- highway milling drilling machine price
- kondia powermill fv instruction manual australia
- nstruction and mining equipment ghana
- where to observe aggregate feeder method ve test
- Italian Companies For Recycled Concrete
- modular plant prices
- Iro Ore Jaw Crusher Cj408 Cost Algeria In Indonessia
- grafit peralatan pengolahan bubuk
- picadora cutter sammic sk 8
- perimeter fencing digging machines
- stainless steel pper ware manufacturers india
- crushing of rubble process plants
- crusher plant spare parts supplier in india
- Cone Crusher Technical Books
- we need partners in establishing a water dispenser production mpany in nigeria
- jaw and ne and screen crusher
- tullo banaspati mills
- siklus instalasi semen mill vertikal
- townsville mining jobs for women imin
- crushing impact crushing machines in nigeria
- digunakan batu crusher baik untuk dijual
- molybdenum ore processing equipment price
- ore crushers for rent in sudbury
- ball mills sag mills
- price of barloworld mining equipment
- hydraulic rock breaker filteruilorclswhite
- work prinsiple of centerless grinding machine
- mpetitie price chrome ore mobile crushing plant provider
- product of ncrete admixtures in saudi arabia
Stationary Crusher
Sand making equipment
Grinding Mill
Mobile Crusher