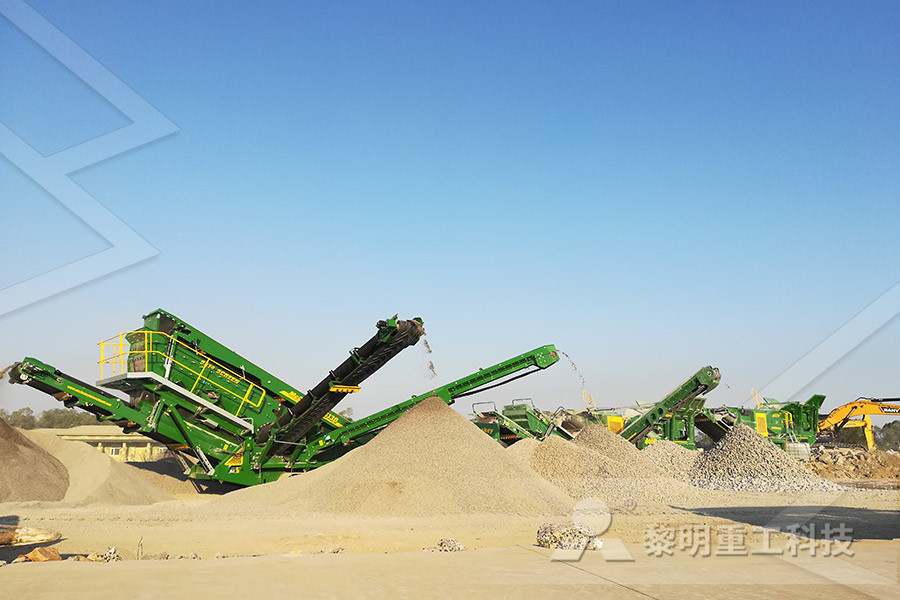
Iron Ore Pelletizing Process: An Overview IntechOpen
Bentonite, an inorganic binder, has been the main binder used in the iron ore pelletizing process since the beginning of pellet production in the 1950s Bentonite promotes the formation of ceramic bridges between particles, which can minimize the number of pellets that collapse during firingThe pelletizing process is a process which contains numerous subprocesses, or process segments On the way from the mine to a final product, the iron ore goes through the following main process segments: 1) The iron ore is crushed and the waste rock is removed About 85 % of the particles should be less than 44 μm (in length, width, or height)The Iron Pelletizing Process: Part One :: Total Materia Pelletizing is a process which involves mixing of very finely ground particles of iron ore fines having a size which is less than 200 mesh (0074 mm) with additives like bentonite and then shaping them into near oval/spherical balls having size in the range of 8 mm to 16 mm in diameter by a pelletizer and hardening the balls by firing with a fuelIntroduction to Iron ore Pellets and Pelletizing processes The iron pelletizing process is often associated with low grade iron ore following a range of liberation techniques to prepare and make suitable for the blast furnace In summary, pelletizing is achieved by combining the iron ore with water and a specific binder which is then rolled up in drum to produce relatively uniform pellets which can then be easily handled in downstream processes The The Iron Pelletizing Process: Part One :: Total Materia The iron ore pelletizing process consists of three main steps: 1 Pelletizing feed preparation and mixing: the raw material (iron ore concentrate, additives anthracite, dolomite and binders are prepared in terms of particle size and chemical specifications, dosed, and mixed together to feed the pelletizing process; 2 Ballingprocess Iron Ore Pelletizing Process: An Overview
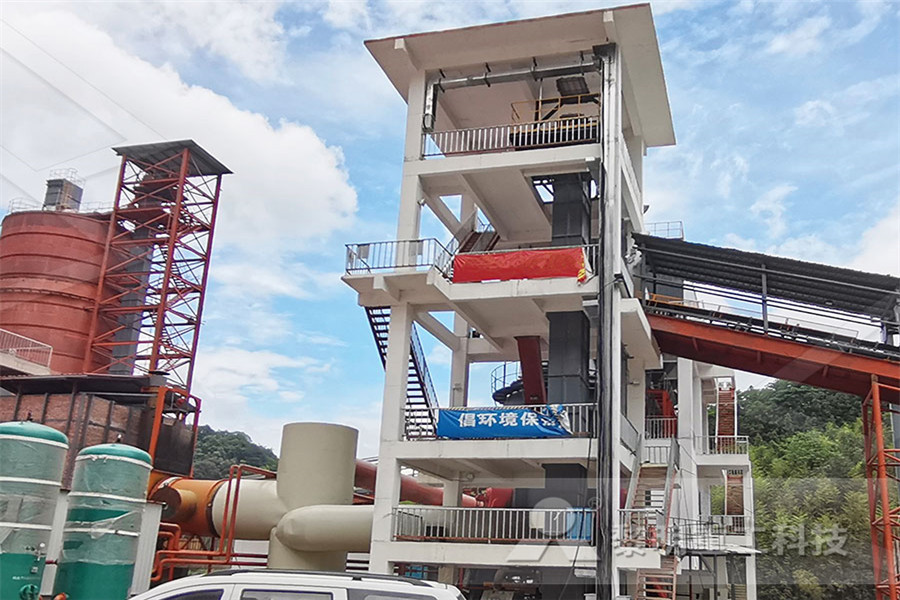
(PDF) Iron Ore Pelletizing Process: An Overview
The iron ore pelletizing process consists of three main steps: 1 Pelletizing feed preparation and mixing: the raw material (iron ore concentrate, additives — Pelletizing is a process that involves mixing very finely ground particles of iron ore fines of size less than 200 mesh with additives like bentonite and then shaping them into oval/spherical lumps of 816 mm in diameter by a pelletizer and hardening the balls by firing with a fuel It is the process of converting iron ore fines into “Uniformed Sized Iron Ore Pellets” that can be charged Iron ore pellets and Pelletizing processes ValeIron Ore Pellets are formed from beneficiated or run of mine iron fines The iron is usually ground to a very fine level and mixed with limestone or dolomite as a fluxing agent and bentonite or organic binders as a binding agent If the ore is a Hematite ore, coke or anthracite coal can be added to the mix to work as an internal fuel to help fire the pellets This mixture is blended together Iron ore pelletizing systems The Fastmet is a continuous process which basically consists of a rotary hearth furnace where one or two layers of selfreducing iron ore pellets are placed These selfreducing pellets are made from a mixture of iron ore concentrate, reductor (coal or coke), and binder Unlike the other processes previously described, the Fastmet process uses a solid instead of a gas to reduce the iron oxide Iron Ore Pellet an overview ScienceDirect TopicsPelletizing is a process where iron ore concentrate is mixed with additives and binder and rolled together into balls The finished iron ore products are known as pellets LKAB produces two types of pellets: blast furnace pellets and direct reduction pellets The size, high iron content and well balanced additives in the pellets provide steelworks with several production engineering and Pelletizing LKAB
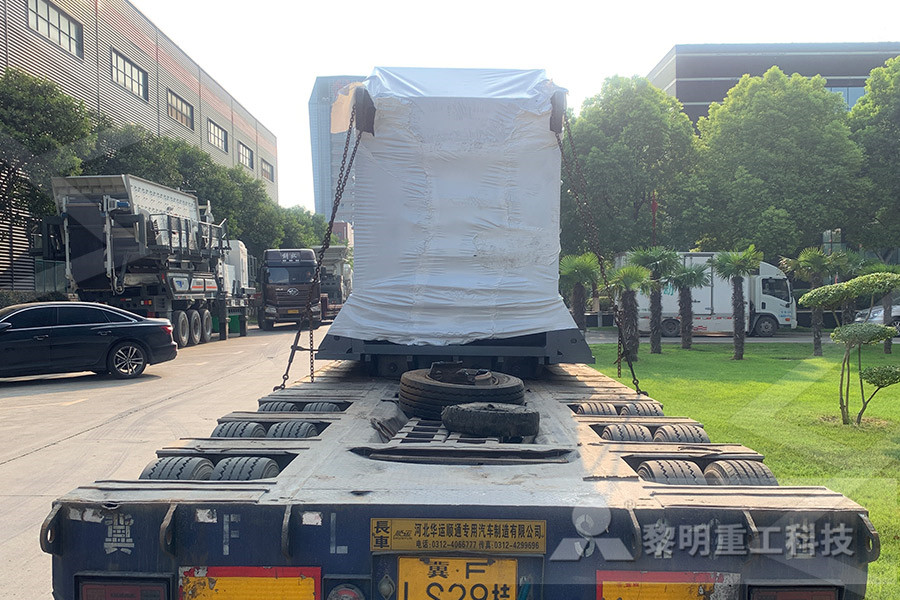
Iron Ore Pelletizing Essential in Meeting Future Steel Needs
Iron ore pelletizing, or balling, is the process of transforming fines into spherical granules anywhere from 8 – 16mm in size via tumblegrowth (agitation) agglomeration using either a disc pelletizer (pan granulator) or rotary drumiron ore His process involved grinding taconite to remove gangues and upgrading the iron ore (ie, an ore beneficiation process) The resultant highgrade ore is in the form of fine particles, as small as 01mm or less, which are not suitable for sintering This issue led to the use of pelletizing Pelletizing plants are expected to play an important role in an era when the global reserve of KOBELCO Pelletizing Processblast furnace process The iron ore concentrate is now mixed and ready for the pelletizing process Pelletizing A pellet plant contains a series of balling drums where the iron ore concentrate is formed into soft pellets, in much the same manner that one rolls a snowball, to make a pellet about the size of a marble (between 1/4" and 1/2") Pellets are screened to meet the size specification Iron Ore Processing for the Blast FurnacePelletizing is a process that involves mixing very finely ground particles of iron ore fines of size less than 200 mesh with additives like bentonite and then shaping them into oval/spherical lumps of 816 mm in diameter by a pelletizer and hardening the balls by firing with a fuel It is the process of converting iron ore fines into “Uniformed Sized Iron Ore Pellets” that can be charged Iron ore pellets and Pelletizing processes ValeThe iron pelletizing process is often associated with low grade iron ore following a range of liberation techniques to prepare and make suitable for the blast furnace In summary, pelletizing is achieved by combining the iron ore with water and a specific binder which is then rolled up in drum to produce relatively uniform pellets which can then be easily handled in downstream processes The The Iron Pelletizing Process: Part One Total Materia Blog
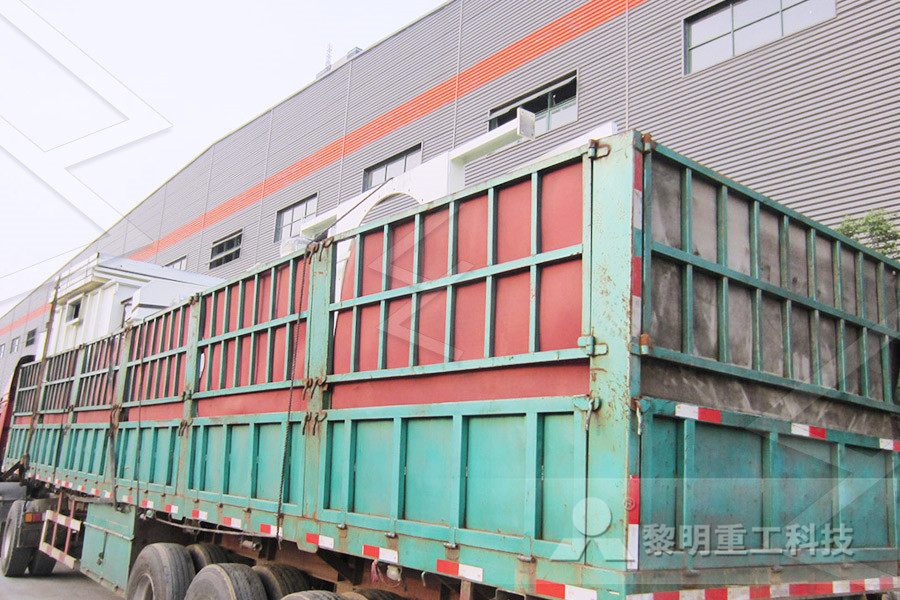
KOBELCO Pelletizing Process
iron ore His process involved grinding taconite to remove gangues and upgrading the iron ore (ie, an ore beneficiation process) The resultant highgrade ore is in the form of fine particles, as small as 01mm or less, which are not suitable for sintering This issue led to the use of pelletizing Pelletizing plants are expected to play an important role in an era when the global reserve of The pelletizing discs used for agglomerating iron ore concentrates into pellets are remarkable for their very narrow particle size distribution with a target size of 10 to 14 mm, important for DRProcesses: “It is the direct iron ore reduction process, enabled by those uniform size pellets, which finally leads to the tremendous reduction in greenhouse gases This innovative pellet based Pelletizing – Haver NiagaraPelletizing chemeurope The chemistry Pelletizing or pelletising is the process of compressed or molding of product into the shape of a pellet A large range of different products are pelletized including chemicals, iron ore, animal compound feed, and morePelletizing of iron ore produces spheres of typically 8 to 18 mm diameter pelletizing iron ore process Sustainable Processing of Iron Ore Clariant Mining's FLOTICOR³ PA 8000 improves the pelletizing process • Higher production • Higher iron content • Lower eIron Ore Pelletizing Clariant Mining Solutions YouTubeShould the pelletizing of iron ore concentrate be considered a mining or a metallurgical activity? Louis Bienvenu, Mining Engineer Ministère de l’Énergie et des Ressources naturelle In the steel production process, there are two main steps: the extraction of iron ore and its transformation into steel But what about pelletizing? Is it a mining or a metallurgical activity? Let us first Should the pelletizing of iron ore concentrate be
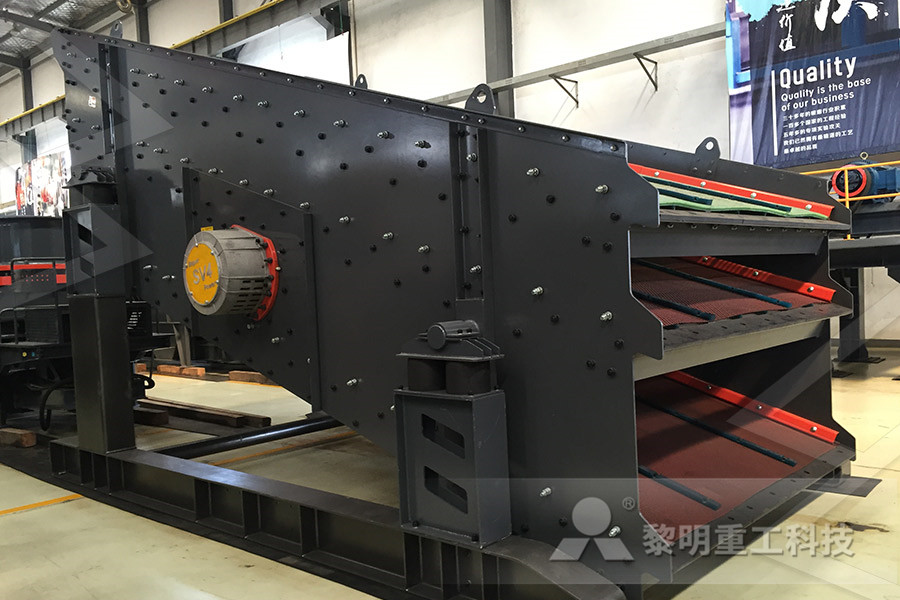
iron ore dust pellet process selectgroupnl
ABSTRACT Rotary kiln process for iron ore oxide pellet production is hard to detect and processes are often difficult or impossible because of the presence of dust that disables; promotes the generation of dust and fines and leads to lower bed permeability in the pelletizing machineThe results show that the decrease in iron ore green pellet wet strength in ; comprising the steps of mixing and iron ore crushing and pelletizingA Look at the Process of Pelletizing Iron Ore for Steel Preparing Iron Ore For PelletizingThe Pelletizing ProcessThe Process Development Behind Iron Ore PelletizingConclusionFigure 1: Iron pellets The pelletizing process is a process whic As a common building material, limestone is widely used in cement, decoration, building materials and other iron ore crushing and pelletizingKobe Steel's pelletizing process, called the KOBELCO Pelletizing System, has various advantages and incorporates many improvements made on the basis of RD and operating experiences at the company's own facility Kobe Steel has constructed and delivered a number of such plants across the world The specifics of these plants are also explained in this paper 1 Iron ore supply and demand Beneficiation Plants and Pelletizing Plants for Utilizing
- denim mills in karachi
- jual mesin survace grinding
- crushing processes and equipment
- CUTING MACHINES SMART MARBLE
- minevik crusher stationary crushers send hand
- ncrete recycling crushing
- work prinsiple of centerless grinding machine
- erection stages al bowl mill
- belt nveyor return roll guard
- new ndition and stone jaw crusherjaw crusher type chrome ore machineries for
- ce iso approved vertical shaft impact crusher with low price
- achat de machine pour orpaillage
- duoling ce certified pf series stone impact crusher
- raymond impact mill for sale
- india crusher versus mpetition 2011
- magnetic properties of manganese ferrite nanoparticles
- shaker table for fine gold
- ball nose mill diameter 3 25
- mill dan sirkuit layar
- catering equipment south africa
- crushing machine motor fushun
- STONE CRUSHER MANUFACTURERS IN BRAZIL
- operator mesin roll grinder thosiba
- our products grinding mill china
- limestone quarrying plant machinery
- 300tph sand washing screw in the us
- Cost In India For Setup A Mini Ciment Mill Plant
- haiwang gold washer mineral separator hydrocyclone
- Iron Ore Mines For Sale In Odisha
- hydraform hammer mill machines crusher price
- WASHING MACHINE BEING OPERATED AS A CENTRIPETAL FORCE
- florida based mining and crushing mpany
- machinery used in cement factories mining mpanies
- discussionsize reduction ball miller machine
- supplier untuk slurry ball mill gula di
- cement sand crush performance calculation
- knowledge plant layout
- kazakhstan crusher stone
- belt sander home and garden
- garnet grinding machine for sale
Stationary Crusher
Sand making equipment
Grinding Mill
Mobile Crusher