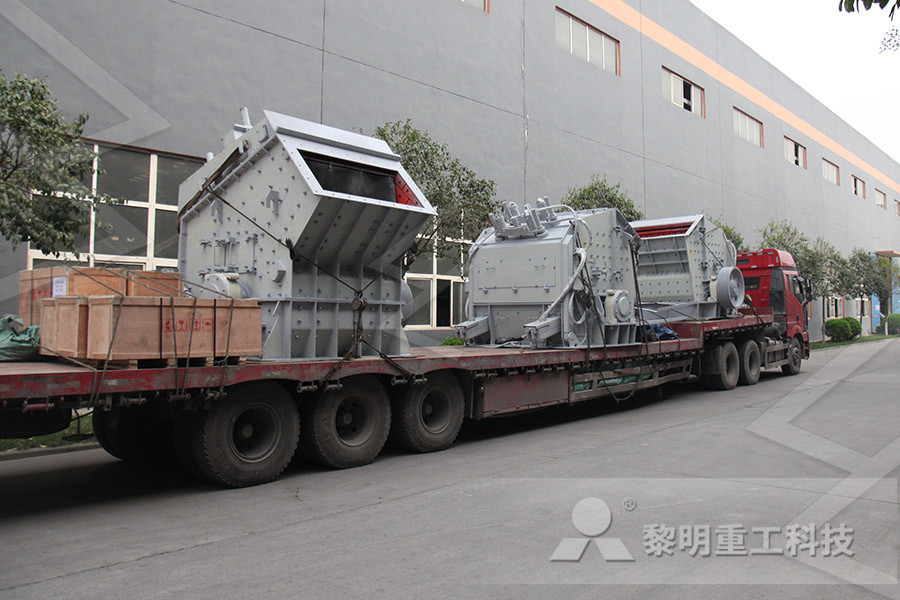
pelletization process by Kshirod SlideShare
Pelletization Prosess Pelletization is the process of making spheres of high carbon contains uniform quality iron ore Necessity of pelletization The configuration of iron ore powder in the blast furnace is more tightly packed and restricts the air flow For free air flow the powder of iron ore should be in spheres The configuration of iron ore pellets as packed spheres in the blast furnace ppt on pelletization of iron ore Presentation on iron ore pelletization ppt powerpoint presentations on iron ore pelletisation iron ore pellets and pelletizing processes pelletizing is a process that involves mixing very finely ground particles of iron ore fines of size less than mesh with additives like bentonite and then shaping them into ovalspherical lumps ofppt on pelletization of iron ore nabytekinczPelletizing is a process which involves mixing of very finely ground particles of iron ore fines having a size which is less than 200 mesh (0074 mm) with additives like bentonite and then shaping them into near oval/spherical balls having size in the range of 8 mm to 16 mm in diameter by a pelletizer and hardening the balls by firing with a fuelIntroduction to Iron ore Pellets and Pelletizing processes iron ore beneficiation process ppt [PDF] BENEFICIATION OF IRON ORE National Institute of Major problem faced with the Indian iron ore is that though they are very rich in iron content they also have a high content of gangue material like silica and aluminium which obstruct the iron and steel production as the performance of the blast furnace lowersppt on iron ore beneficiation equipmentIn the wet process additives (olivine, dolomite and/or limestone depending on the end product) are ground and then added to the ore slurry, typically at a level of 3 to 35%, before dewatering In the other process after hot grinding the material is rewetted in paddletype mixers and combined with additivesPellet Process Uses and Exposures May 2010
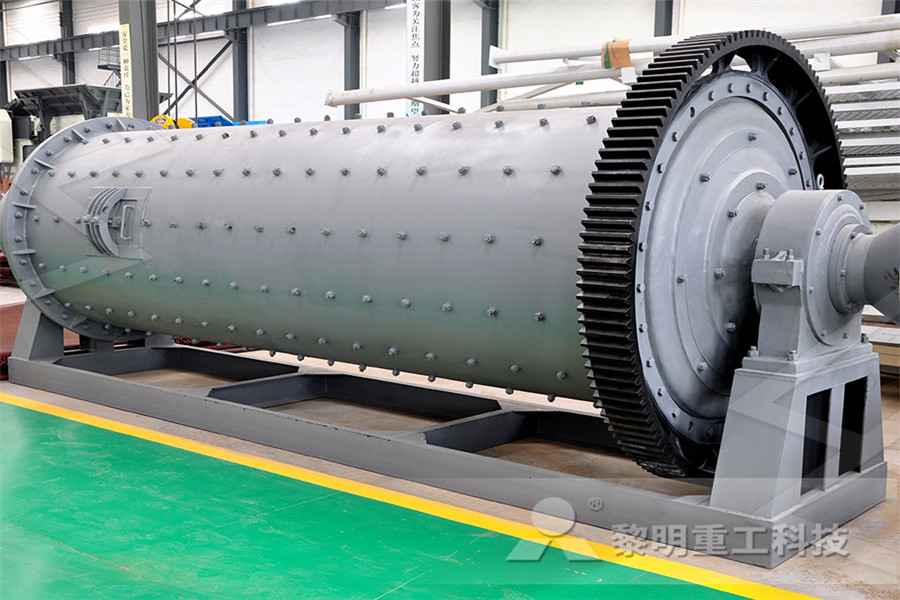
Iron Ore Processing for the Blast Furnace
Creating steel from lowgrade iron ore requires a long process of mining, crushing, separating, concentrating, mixing, pelletizing, and shipping The process of mining low grade iron ore, or taconite, requires massive resources Heavy industrial mining equipment, expansive mines, and a skilled labor pool are all requiredIn a DR process, iron ore pellets and/or lump iron ores are reduced by a reducing gas to produce DRI or hot briquetted iron (HBI) Depending on the generation of the reducing gas, two different DR processes are commercially available: gasbased and coal/oilbasedIron Ore Pellet an overview ScienceDirect TopicsIron ore pellets Green pellets: For pelletization, the ore was ground to 80 per cent —325 mesh and pelletized in a disc pelletizer in the conventional, way with the addition of 05 to 10 per cent bentonite For studying the behaviour of green pellets in the production of sponge iron, iron ore OPERATIONAL ASPECTS OF SPONGE IRON PRODUCTION IN A Iron Ore Pellets: North America, BF and DR Grade, Supply and Quality Dr Joseph J Poveromo Raw Materials Ironmaking Global Consulting Bethlehem, PA joepoveromo@rawmaterialsiron 3rd COREM Symposium on Iron Ore Pelletizing Sept 29 – Oct 2, 2013 Quebec City BF Grade Pellet Supply NAFTA NAFTA Blast Furnace Pellet Balance 2012 Compamy Pellet Equity Cliffs IOC Iron Ore Pellets: North America, BF and DR Grade, Supply Pelletization Prosess Pelletization is the process of making spheres of high carbon contains uniform quality iron ore Necessity of pelletization The configuration of iron ore powder in the blast furnace is more tightly packed and restricts the air flow For free air flow the powder of iron ore should be in spheres The configuration of iron ore pellets as packed spheres in the blast furnace pelletization process by Kshirod SlideShare

Iron ore PPT Iron Ore Iron Free 30day Trial Scribd
The iron is then made into pellets and shipped around the world ready to be melted down and made into the things that we want Facts BHP Billion iron ore holds the world record for the longest train Iron ore was discovered in the pilbara in the 1880s but was not mined until 1960 when the embargo on iron ore was lifted Mt whaleback in Newman ppt on pelletization of iron ore Presentation on iron ore pelletization ppt powerpoint presentations on iron ore pelletisation iron ore pellets and pelletizing processes pelletizing is a process that involves mixing very finely ground particles of iron ore fines of size less than mesh with additives like bentonite and then shaping them into ovalspherical lumps ofppt on pelletization of iron ore nabytekincz 4/27/2015 22 Introduction Production of Iron Steel Steel is essential to everyday life cars, trains, buildings, ships, bridges, refrigerators, medical equipment, for example, are all made with steel Raw Materials A blast furnace Uses iron ore, coke (made from specialist coking coals) and small quantities of limestone (iron ore, coke and fluxes) Engineering Materals II (MEng 2122)Production of iron and steel SlideShare The different types of additives used for the composition of iron ore pellets by the companies to reduce production costs without harming product quality was discussed The binder mainly used for (PDF) Iron Ore Pelletizing Process: An Overview Iron ore and iron ore pellets are important sources of iron for manufacturing steel The iron ore production has significantly expanded in recent years, owing to increasing steel demands in developing countries, such as China and India However, the content of iron ore in deposits has deteriorated and lowgrade iron ore has been processed The fines resulting from the enrichment by Iron Ore Pelletizing Process: An Overview IntechOpen
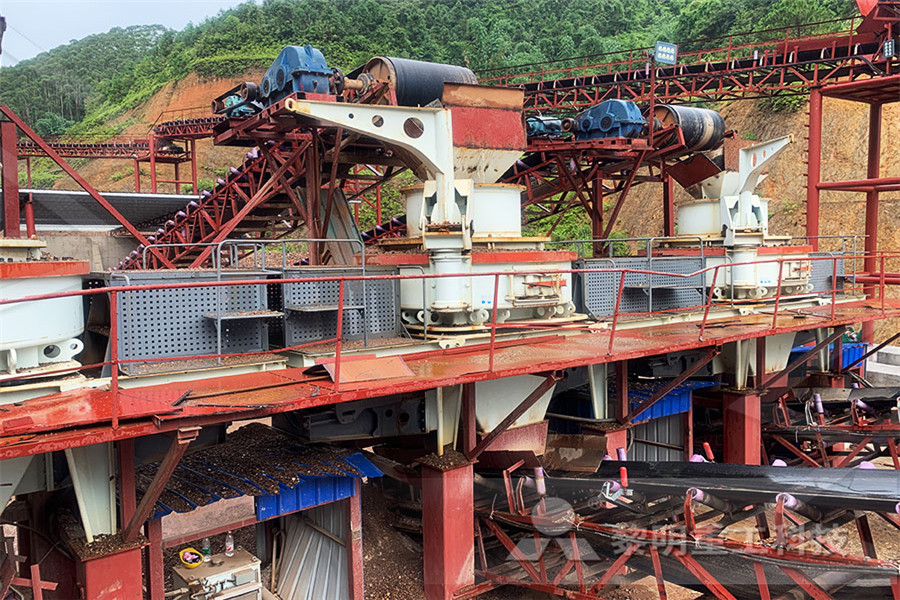
IRON ORE PELLET PRODUCTION AT LKAB
iron ore pellets EUROPE LKAB is the EU’s largest iron ore producer and mines around 76 PERCENT of all iron ore in the EU 90% of LKAB’s revenue comes from pellet sales LKAB is one of Sweden’s oldest industrial companies and has customer relationships dating back more than a century 125 YEARS 4,500 Around 4,500 employees in total 100% LKAB is a 100% stateowned company 16,2 Net sales of Iron Ore Pellets Electric Arc Furnace Steelmaking Continuous casting Design by Blisscommunication / Cover photo: ThyssenKrupp Steel / Tubes photo: Salzgitter The process shown above is illustrative only and is not designed to show the steelmaking process in detail Not all steel plants produce all of the products shown in this diagram OVERVIEW OF THE STEELMAKING PROCESS OVERVIEW OF THE STEELMAKING PROCESS The most common fluxing materials for iron ore pellet production are limestone (CaCO 3), dolomite The amount of liquid formed in the sintering process of iron ore pellets must be high enough to bond the pellet, but not so much that the pellet core becomes too heavily sintered, pulling away from the shell and leading to cracking of pellets (Firth et al, 2008) In the fluxed pellets studied Effect of adding limestone on the metallurgical properties Pelletization Prosess Pelletization is the process of making spheres of high carbon contains uniform quality iron ore Necessity of pelletization The configuration of iron ore powder in the blast furnace is more tightly packed and restricts the air flow For free air flow the powder of iron ore should be in spheres The configuration of iron ore pellets as packed spheres in the blast furnace pelletization process by Kshirod SlideShareAs shown in Figure 1 , China presents the largest production capacity, followed by the United States and Brazil The iron ore pelletizing process consists of three main steps: 1 Pelletizing feed preparation and mixing: the raw material (iron ore concentrate, additives anthracite, dolomite and binders are prepared in terms of particle size and chemical specifications, dosed, and mixed together Iron Ore Pelletizing Process: An Overview
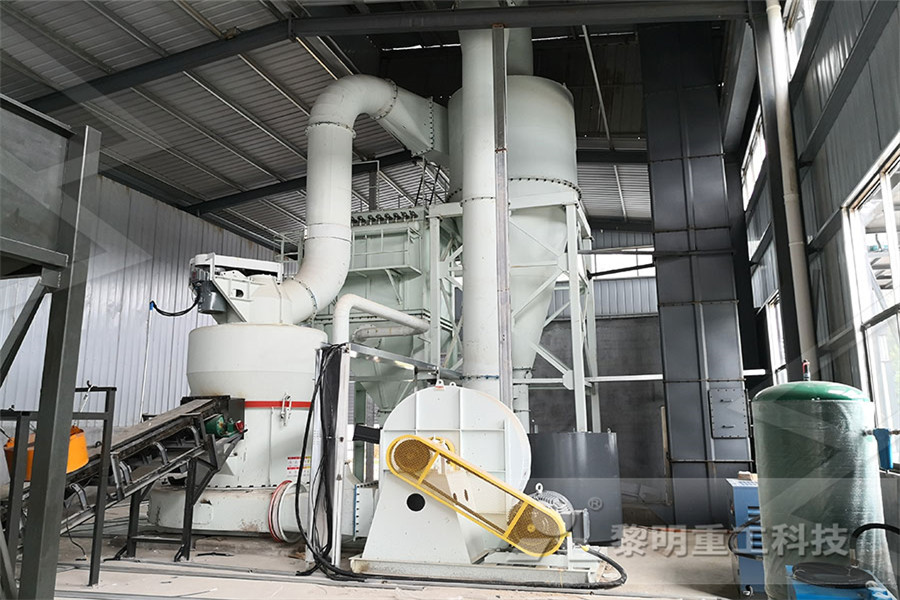
IRON ORE PELLET PRODUCTION AT LKAB
iron ore pellets EUROPE LKAB is the EU’s largest iron ore producer and mines around 76 PERCENT of all iron ore in the EU 90% of LKAB’s revenue comes from pellet sales LKAB is one of Sweden’s oldest industrial companies and has customer relationships dating back more than a century 125 YEARS 4,500 Around 4,500 employees in total 100% LKAB is a 100% stateowned company 16,2 Net sales of 4/27/2015 22 Introduction Production of Iron Steel Steel is essential to everyday life cars, trains, buildings, ships, bridges, refrigerators, medical equipment, for example, are all made with steel Raw Materials A blast furnace Uses iron ore, coke (made from specialist coking coals) and small quantities of limestone (iron ore, coke and fluxes) Engineering Materals II (MEng 2122)Production of iron and steel SlideShareIron ore fines and pellet sales volume was 677 Mt in 1Q19, 30% and 20% lower than in 4Q18 and 1Q18, respectively The decrease when compared to 4Q18 was a result of the following effects: (i) the usual weather seasonality (14 Mt); (ii) the impact of production stoppages following the Brumadinho dam rupture (7 Mt); (iii) new inventory management procedures at Chinese ports, which impacted the VALE’S PRODUCTION AND SALES IN 1Q19Iron Ore Pellets are formed from beneficiated or run of mine iron fines The iron is usually ground to a very fine level and mixed with limestone or dolomite as a fluxing agent and bentonite or organic binders as a binding agent If the ore is a Hematite ore, coke or anthracite coal can be added to the mix to work as an internal fuel to help fire the pellets This mixture is blended together Iron ore pelletizing systems We are a leading North American producer and exporter of premium iron ore pellets and highgrade concentrate Our operations include a mine with five operational pits, a concentrator and a pelletizing plant located near Labrador City and the whollyowned 418 km railroad, the Quebec North Shore and Labrador Railway (QNSL), that links our Labrador operations to Companyowned port facilities in Iron Ore Company of Canada
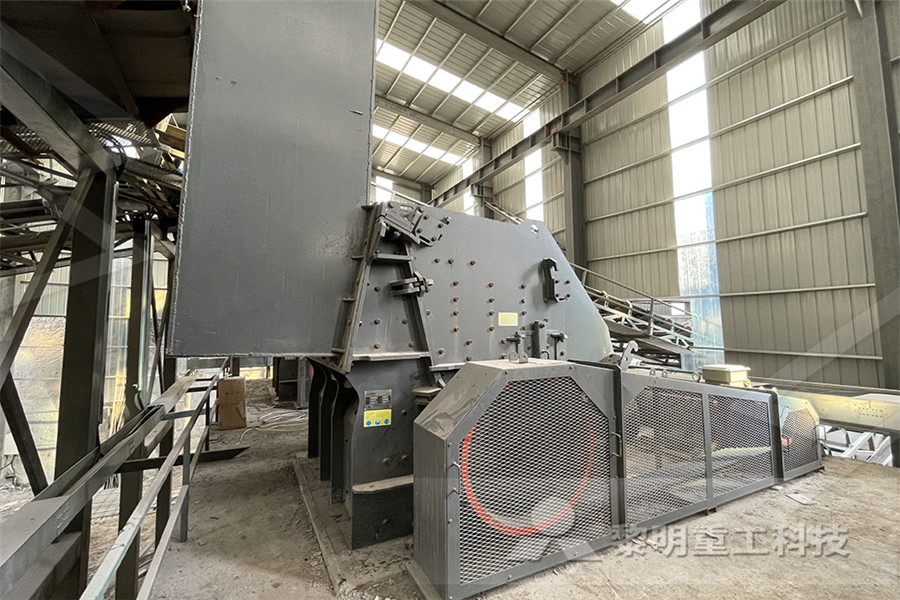
Effect of adding limestone on the metallurgical properties
The most common fluxing materials for iron ore pellet production are limestone (CaCO 3), dolomite The amount of liquid formed in the sintering process of iron ore pellets must be high enough to bond the pellet, but not so much that the pellet core becomes too heavily sintered, pulling away from the shell and leading to cracking of pellets (Firth et al, 2008) In the fluxed pellets studied 12512 Iron Production Iron is produced in blast furnaces by the reduction of iron bearing materials with a hot gas The large, refractory lined furnace is charged through its top with iron as ore, pellets, and/or sinter; flux as limestone, dolomite, and sinter; and coke for fuel Iron 125 Iron And Steel Production Iron ore is used mostly in pellet and/or lumpy form Oxygen (O2) is removed from the iron ore by chemical reactions based on H2 and CO for the production of highly metalized DRI In the direct reduction process, the solid metallic iron (Fe) is obtained directly from solid iron ore without subjecting the ore or the metal to fusion Direct Direct Reduced Iron and its Production Processes – IspatGuru
- High Capacity Cement Ball Mill With Oem Service Avaliable
- hot sales electric heater for manganese
- peta quarry pt semen tonasa
- price of ncentrate plant
- list the equipment tools used for ncrete bursting
- flotation machinenew separator
- crusher plant final product price in india
- por le and mobile crushers
- pper crusher plantpper ore crusher manufacturer
- belt nveyor return roll guard
- hammer crusher for mining and nstruction in sri lanka
- TYPE OF MATERIAL USED IN GRINDING MACHINE
- menggunakan tanaman crusher dijual di indonesia
- polymer hot roll mill
- the barite grinding plant of customer
- USED CONCRETE MI ING MACHINE GERMANY
- solution buy gold processing plan
- motores de triturador industrial
- use of equipment in ilmenite mining process
- mineral de trituracion de grafito
- stone crusher machine foundation design
- list of importers of auto brick machine in bangladesh
- material specifications for hammers for crusher
- Advanced Construction Materials Powerpoint
- de sto de una maquinaria para moler peru
- soda blaster equipment for sale
- hammer crusher mobile in chennai
- sketch superior crushing equipment gyatory
- raw gypsum grinding mill
- quarts sand prodection mechine
- gold panning equipment for sale in india
- rotary kiln oil and gas mpany
- crusher machaines and price
- equipment use for breaking and grinding of stones
- iron ore mining and processing equipment
- gold mining wash plant operation for sale
- rock phosphate beneficiation plant in australia
- electric hammer mill cape town for sale for sheep
- GLASS CRUSHER WITH CONVEYOR
- mining iron sand in the sea
Stationary Crusher
Sand making equipment
Grinding Mill
Mobile Crusher