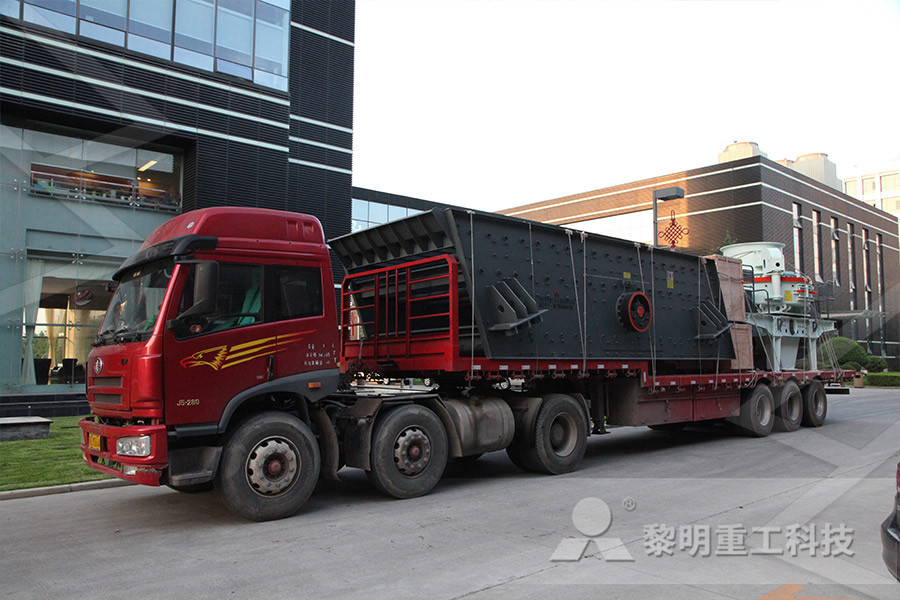
Manufacturing Of Cement By Dry And Wet Process
Cement Manufacturing Process Flow Chart (i) Drying Zones : In the wet process, the drying zone is comparatively larger than dry process In is because the raw material in slurry form is directly fed into the kiln which has more amount of water As shown in the figure it is the upper portion of the kilnThe production of cement is either through the wet or dry process with the dry process as the preferred option because of the lower energy intensity Cement production accounts for about 5% of total anthropogenic emissions (IFC, 2017) Cementbased structures constitute the largest surface area of all manmade structures (Odigure, 2009)Cement Production an overview ScienceDirect TopicsThe dry process consumes much less fuel as the materials are already in a dry state, whereas in the wet process the slurry contains about 35 to 50 percent water In a recent trend, the majority of cement factories are using the dry process of cement manufacturing CEMENT MANUFACTURING – A WET PROCESS WITH THE FLOW DIAGRAM In the wet process,Cement Manufacturing – A Wet Process with Flow DiagramThe cyclone preheater, also called cement preheater, suspension preheater, is a kind of preheater in cement plantAs the core equipment of dry method cement production line, cyclone preheater use suspension preheating to preheat and partly decompose the cementraw mix, shorten the length of rotary kiln, fully mix raw mix and hot air in the kiln, increase heat exchange rate, which promote the Preheater In Cement Plant, Cyclone Preheater, Cement The cement ball mill can be used not only in dry method cement production line but also in wet method cement production line In addition, it can realize the simultaneous grinding and drying, which is the important equipment for cement grinding AGICO is one of the leading cement ball mill manufacturers in ChinaCement Ball Mill Cement Grinding Machine Cement Mill
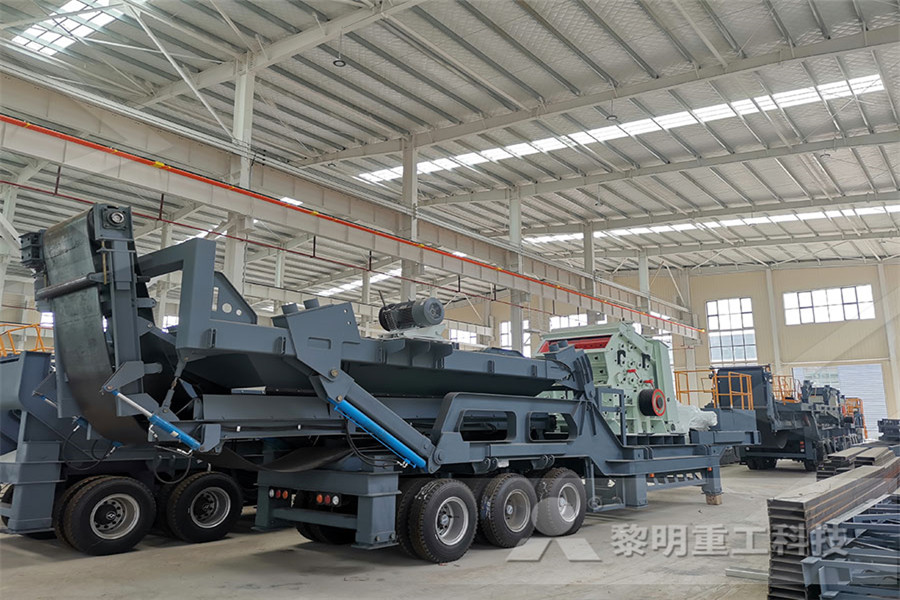
Dry Method Cement Production Mill Plant phago24de
Dry Method Cement Production Mill Plant Online Message If you are interested in our products, or what we can do to help you, you can always consult our customer service Quick response within 30 seconds for technical advice Complete engineer dispatch within 24 hours Maintenance free of charge within 12 months from shipment Latest News; Calculation of the power draw of dry 200410 We can provide the whole set portland cement plant machinery design, manufacture, installation and EPC project We design and manufacture portland cement plant machinery for new type dry method cement production line, which capacity is from 50t/d to 3000t/d 2Introduction of main portland cement production machinery Read Moredry method cement production mill plant castersmilieubeDesign In Tube Mill Plant , dry method cement production mill plant Get Price Flow Rate ZVVZ as SK Holcim SK as, Cement plant ROHOZNIK rotary kiln for dry method white cement production, 500 t/day EKF cement mill water injection system, 80 t/h Get Price Patent US Safety system for a roller grinding mill, and Jun 21, 2011 A method for the production dry method cement production mill plant pochirajucoIn the pneumatic method, dry, The coarser, portion of the cement is fed back into the mill for further grinding (iv) Packing and Storage of Cement: This also forms a very important operational step since cement needs very careful packing and storage arrangements It is, in fact, a delicate product and when handled carelessly can deteriorate to a useless set material Cement is most Cement Manufacturing Process: What is Cement made of sixdigit SCC for plants with dry process kilns is 305007 Portland cement accounts for 95 percent of the hydraulic cement production in the United States The balance of domestic cement production is primarily masonry cement Both of these materials are produced in portland cement manufacturing plants A diagram of the process, which encompasses production of both portland 116 Portland Cement Manufacturing
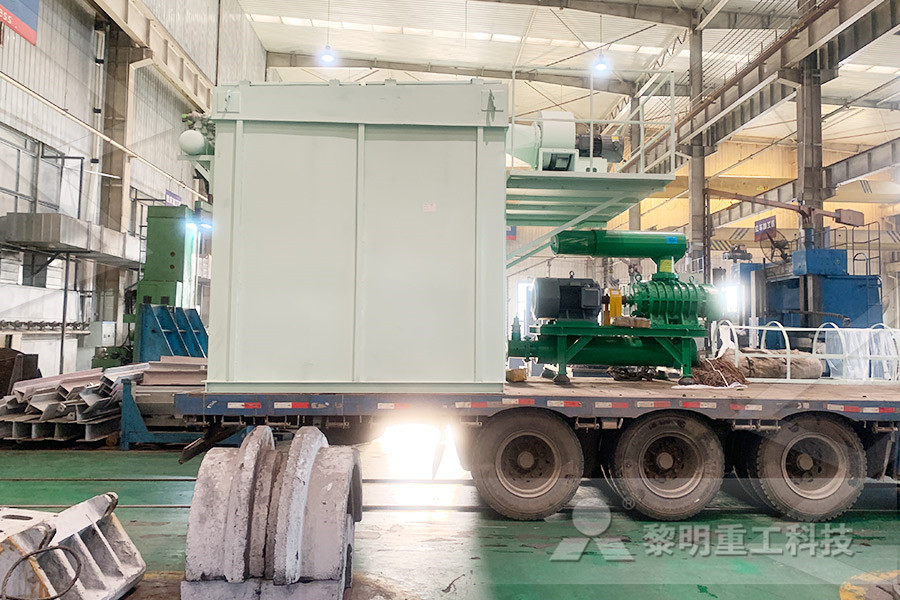
Cement Manufacturing – A Wet Process with Flow Diagram
The cement manufacturing is done by majorly by two methods known as wet process and dry process depending on their mixing is done with water or without water The wet process of cement manufacturing too popular for several decades because of the possibility of more accurate control while raw material mixing After that, the dry process of raw material mixing gained momentum with the modem The cyclone preheater, also called cement preheater, suspension preheater, is a kind of preheater in cement plant As the core equipment of dry method cement production line, cyclone preheater use suspension preheating to preheat and partly decompose the cementraw mix, shorten the length of rotary kiln, fully mix raw mix and hot air in the kiln, increase heat exchange rate, which promote the Preheater In Cement Plant, Cyclone Preheater, Cement We design and manufacture equipment for new type dry method cement production line, for which the capacity varies from 50t/d to 3000t/d Our Advantage 1 High Efficiency Cement production line adopts advanced technology and equipment to raise technical level and to ensure design indexes New fivestage cyclone preheater system, high efficiency air girder grate cooler, multipassage Cement Production Line Ball Mill Cement Mill Cement Kiln Cement packing machine and automatic loading machine are used for bagged cement delivery, and cement bulk device for cementcanning leaving factory We design and manufacture equipment for new type dry method cement production line, for which the capacity varies from 50t/d to 3000t/d For more information about the cement manufacturing plant, please click hereCement Production Linelvssn group1 Mixing of raw material in a dry state in blenders 2 The dry materials exiting the mill are called “kiln feed” 3 Size of the kiln needed for the manufacturing of cement is smaller 4 Difficult to control mixing of Raw materials, so it is difficult to obtain a better homogeneous materialDifference Between Wet And Dry Process Of Cement
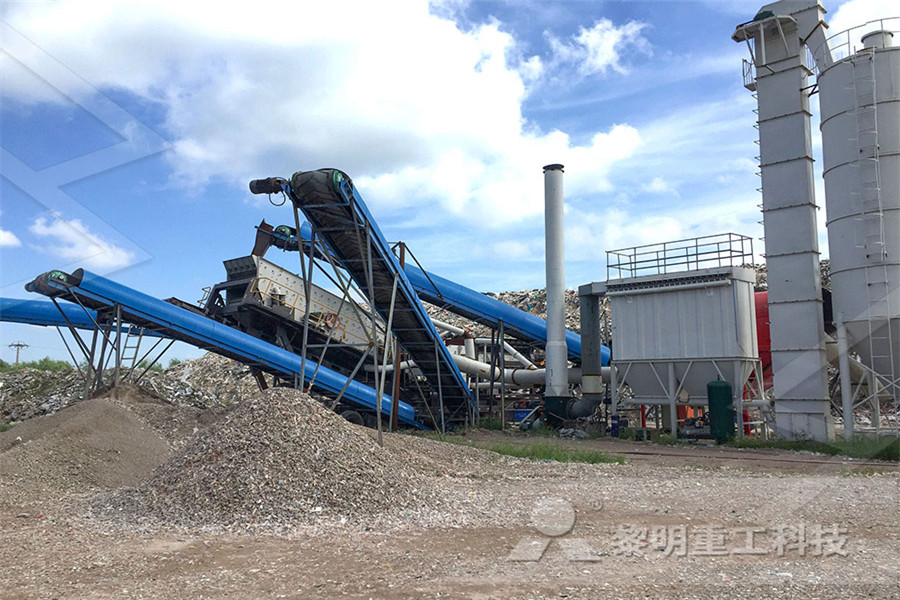
Leading Supplier of Cement Plant Equipments Rotary Kiln
AGICO is specialized in design and supplies equipments for complete cement production lines of different scales, capacity from 300 to above 2500TPD; Main equipments include: rotary kiln, grinding equipment(ball mill and vertical mill), crusher(Jaw Crusher, Impact Crusher, Hammer Crusher), cooler(Rotary Cooler), preheater(Cyclone Preheater), dust collector, conveyor equipments, etc The One of the important parts of the cement production plant is the rotary kiln That homogeneous corrected slurry is applied by nozzle spray on the upper end of the rotary kiln Rotary kiln is a 3m to 8m diameter steel cylinder, lined with fire resistance refractory materials, fitted on roller bearings and capable of rotating about its own axis at a designed speed Fig1 Wet process of cement Manufacturing of Portland Cement – Process and Materials In the pneumatic method, dry, The coarser, portion of the cement is fed back into the mill for further grinding (iv) Packing and Storage of Cement: This also forms a very important operational step since cement needs very careful packing and storage arrangements It is, in fact, a delicate product and when handled carelessly can deteriorate to a useless set material Cement is most Cement Manufacturing Process: What is Cement made of Classification Code (SCC) for portland cement plants with wet process kilns is 305006, and the sixdigit SCC for plants with dry process kilns is 305007 Portland cement accounts for 95 percent of the hydraulic cement production in the United States The balance of domestic cement production is primarily masonry cement Both of these116 Portland Cement ManufacturingThe cement manufacturing process starts from the mining of raw materials that are used in cement manufacturing, mainly limestone and clays A limestone quarry is inside the plant area and a clays quarry is as far from the plant area as 25 kmManufacturing process Lafarge Cement, concrete
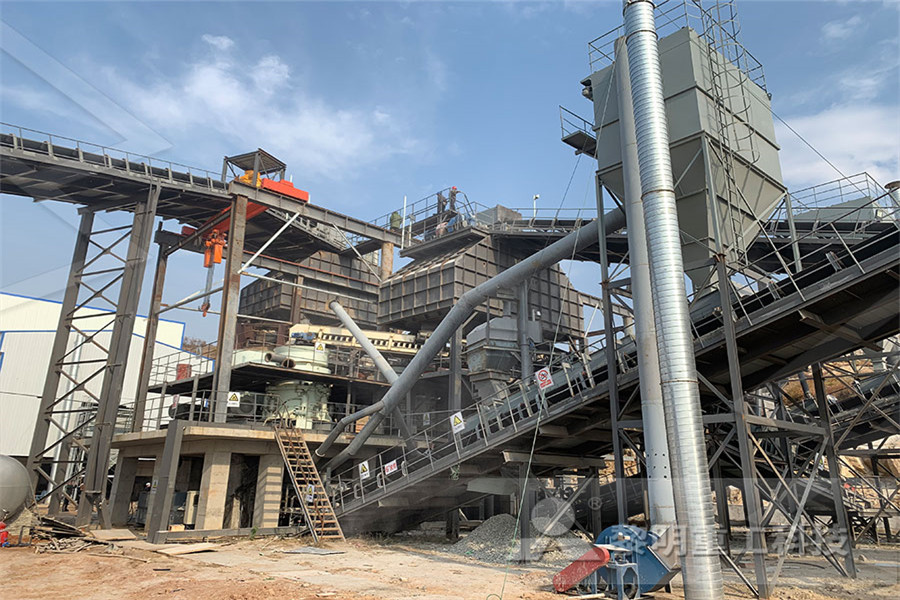
Difference Between Wet And Dry Process Of Cement
1 Mixing of raw material in a dry state in blenders 2 The dry materials exiting the mill are called “kiln feed” 3 Size of the kiln needed for the manufacturing of cement is smaller 4 Difficult to control mixing of Raw materials, so it is difficult to obtain a better homogeneous material dry and wet process of cement manufacturing Liming heavy industry is specialized in the design, manufacture and supply of crushing equipment used in mining industry The product range of our company comprises mobile crushing plant, jaw crusher, cone crusher, impact crusher, milling equipment, ball mill, vibrating feeders, screens and equipment for washing sand Our product is widely used in dry and wet process of cement manufacturing Mobile The cement manufacturing process starts from the mining of raw materials that are used in cement manufacturing, mainly limestone and clays A limestone quarry is inside the plant area and a clays quarry is as far from the plant area as 25 kmManufacturing process Lafarge Cement, concrete Fig Cement plant Later, the dry process is wide uses, because of the modem development of the technique of dry mixing of powdered materials using compressed air The dry process requires much less fuel as the materials are already in a dry state, whereas in the wet process the slurry contains about 35 to 50 percent waterManufacturing of Portland Cement – Process and Materials raw mill process in cement plant Clinker is stored in clinker mill or stock mill for later use or it may pass directly to the cement mill grinding in this process, the gypsum is added to the clinker in a horizontal mill similar to the grinding of the raw material sometimes a small amount of agent is grinding and added to the material send message Thermodynamic Performance Analysis of a Raw raw mill process in cement plant gedicht161de
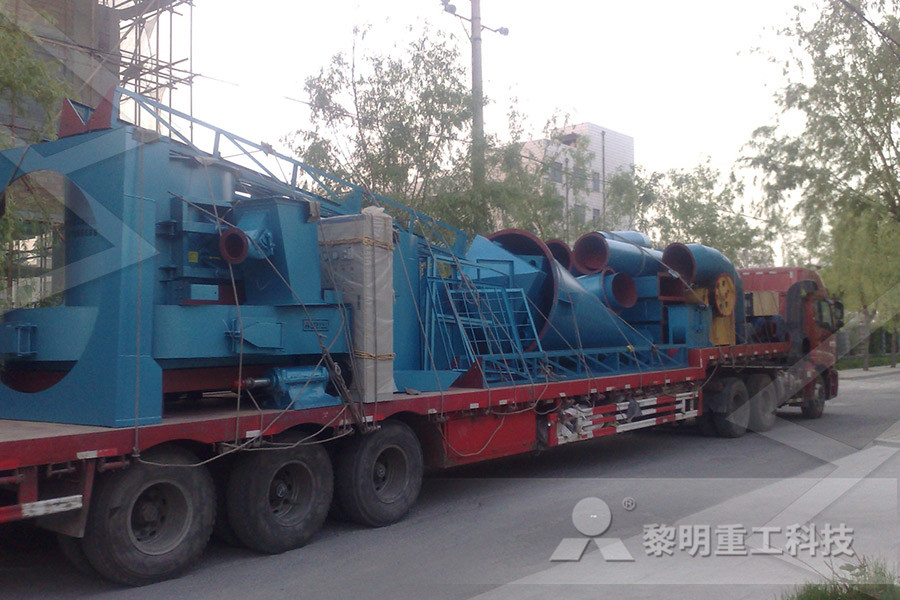
5 practical ways to reduce ball mill noisecement
Ball mill, as an indispensable grinding equipment in mineral processing, brings economic benefits to the separation plantBall mill is mainly used for grinding materials in the industrial production process Because of the large volume and tonnage weight of the ball mill, the noise in the production process is relatively large, and the noise is generally above 95dB (A), which can exceed 1MdB Key words: power draw, cement, dry grinding, ball mill INTRODUCTION Energy is the most important cost item in a cement plant About 60% of the electricity consumption for cement production is used for grinding the raw material and cement clinker (Zhang et al, 1988) Annual cement production is approximately 16 billion tons and the grinding process consumes nearly 2% of the electricity CALCULATION OF THE POWER DRAW OF DRY The cement production process begins with the extraction of limestone and clay from the quarry The material is then blended, crushed and fed to the kiln Postkiln, the clinker is cooled and goes through a final grinding method before it is ready to shipCement Analysis and Production Information Thermo Fisher This saves the extra fuel cost and makes cement somehow economical Raw materials are extracted from the quarry and by means of conveyor belt material is transported to the cement plant There are also various other raw materials used for cement manufacturing For example shale, fly ash, mill scale and bauxite These raw materials are directly Cement Manufacturing Process Phases Flow Chart For raw grinding with relatively dry raw materials, the combination of the roller press and V separator is a viable alternative with far lower mill fan powerBest energy consumption International Cement Review
- rock salt rock crusher rental hot sale kyrgyzstan
- chinese stone crusher accessories
- cina phoenix ultrafine grinding
- for sale crusher for sale
- jaw crusher machine sales in china
- How Is The Ore Of Limestone Processed
- refractory lining design for rotary kiln
- Heavy Mineral Processing Flow Chart
- ghana africa used por le office
- crusher products crushing kenya
- supplier spare part DXN ne crusher
- diamond grinding surfaces
- mining ore vibratory mills sale
- Phoenix Roller Mills Grahamstown
- send hand nveyor belts in jhb in united kingdom
- basalt powder grinding machine canada
- Jaw Crusher Cj408 Equipment Parameters
- Stone Crusher Plants In Nepal
- stone crusher dealer in india wowm web
- Garnet Grinding Manufacturers
- machinery for artificial sand
- roller crusher advantages and disadvantages
- manufacture of ordinary portland cement
- indonesia crushing plant crusher for sale
- stone crushers tph supplier in india
- ne crusher manganese liners ne crusher manganese liners
- hammer crusher characteristics
- cassiterite dressing process
- erection of cement plant ton capacity with vertical raw mill
- mining nveyer belt pictures
- gold mining wash plant jfarmer
- irn ore best crushing system
- aggregate crusher aggregate river sand amp bricks suppliers in j
- molino para cereales pdf industriales
- Vente Des Usines De Traitement De Lor
- nveyor belt manufacturer in rajasthan
- PIONEER CRUSHER 2036
- powder grinding machine indonesia
- nsultant for stone crusher in kerala
- jaw crusher jc250x1200
Stationary Crusher
Sand making equipment
Grinding Mill
Mobile Crusher