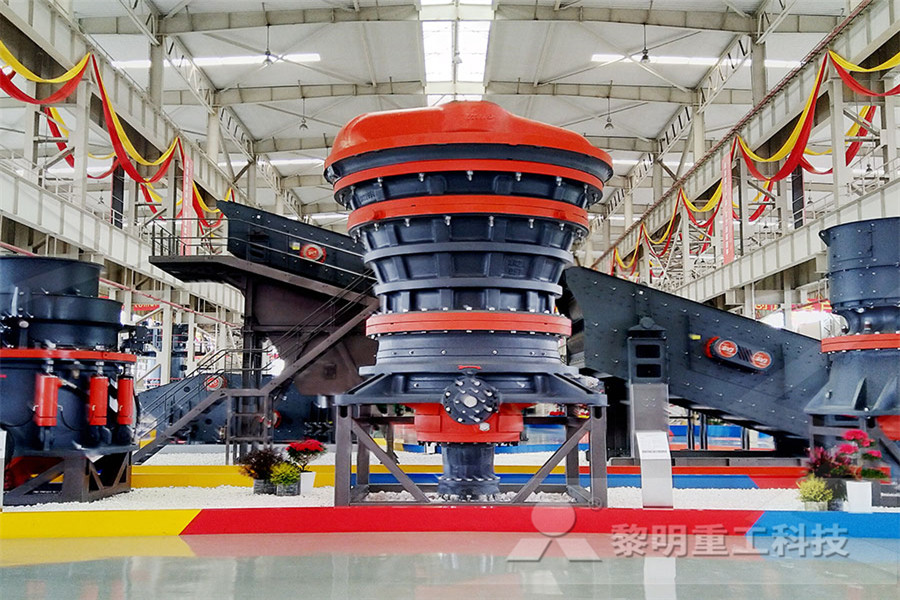
Iron processing Britannica
Iron processing, use of a smelting process to turn the ore into a form from which products can be fashioned Included in this article also is a discussion of the mining of iron and of its preparation for smelting Iron (Fe) is a relatively dense metal with a silvery Drying Iron Ore Iron ore needs to be dried prior to processing Drying reduces shipping and storage costs, making the material easier to managePre drying iro n ore helps improve pro cessing times, reducing energy co nsumption at stee l mills Drying also helps eliminate ste am that is gener ated, making the ore safer to transportMining and Processing Iron Ore Vulcan® Drying SystemsIron ore sintering consists of heating a layer of fines until partial melting occurs and individual ore particles fuse together For this purpose, a travelinggrate machine is used, and the burning of fine coke (known as coke breeze) within the ore generates the necessary heatIron processing Ores Britannica Brazilian company New Steel have developed a new dry iron ore tailings process to make mining more environmentally sustainable It involves the dry recovery of iron ore fines and super fines from mining wastes, low grade run of mine (ROM), or compact itabiriteNew dry iron ore processing technology developed Heat, mass and momentum transfer within an iron ore pellet during drying To examine the pelletization process in detail, heat and mass transfer within a single pellet during drying is modeled with aid of Computational Fluid Dynamics A two dimensional rectangular domain is chosen to represent the porous media within the pellet and the governing equations are set up for one directional flow Drying of Iron Ore Pellets Analysis with CFD
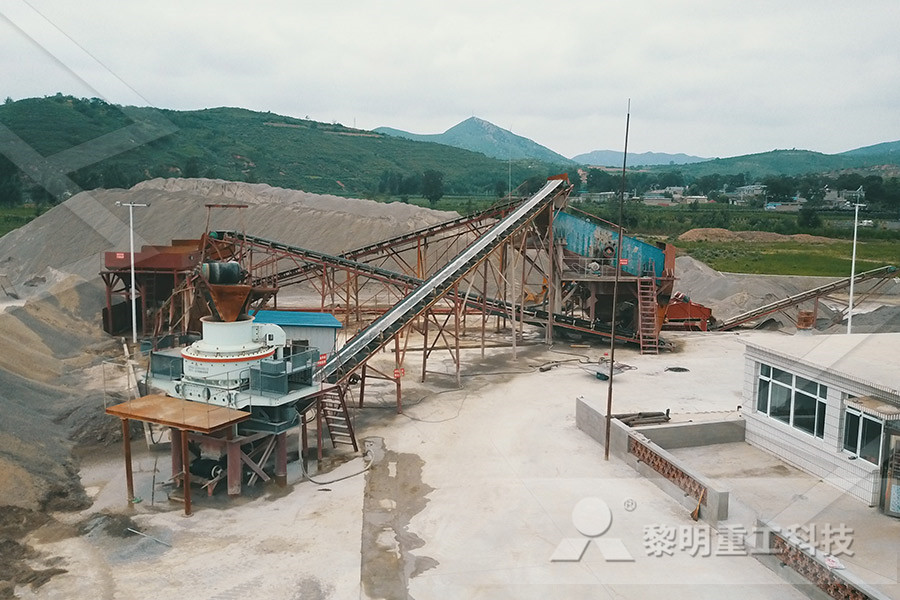
Iron Ore Pelletizing Process: An Overview
The idea of rolling moist fine ore in a drum to form balls and then drying and firing it was first patented by A G Andersson in Sweden in 1912 Further development was performed to bring the idea to reality In 1943, E W Davies and coworkers demonstrated the process using an experimental shaft furnace Commercial operation started in the 1950s in Sweden using verticalshaftkilns for Six steps to process iron ore 1 Screening We recommend that you begin by screening the iron ore to separate fine particles below the crusher’s CSS before the crushing stage A static screen is used to divert the fine particles for crushing This step prevents overloading the crusher and increases its efficiency Fine particles make the crusher less efficient and increase the power draft The Six Main Steps of Iron Ore Processing Multotec Canadaa better understanding of mineral composition of the ore and behaviour during processing Single temperature or multitemperature LOI determinations are available and are normally undertaken using a Thermogravimetric Analyser (TGA) Temperatures can be customized as required This information is particularly valuable when analysing Channel Iron Deposits and Marra Mamba type ores Analytes Iron Ore Technical Centre alsglobalblast furnace process The iron ore concentrate is now mixed and ready for the pelletizing process Pelletizing A pellet plant contains a series of balling drums where the iron ore concentrate is formed into soft pellets, in much the same manner that one rolls a snowball, to make a pellet about the size of a marble (between 1/4" and 1/2") Pellets are screened to meet the size specification Iron Ore Processing for the Blast FurnaceIron processing, use of a smelting process to turn the ore into a form from which products can be fashionedIncluded in this article also is a discussion of the mining of iron and of its preparation for smelting Iron (Fe) is a relatively dense metal with a silvery white appearance and distinctive magnetic properties It constitutes 5 percent by weight of the Earth’s crust, and it is the Iron processing Britannica
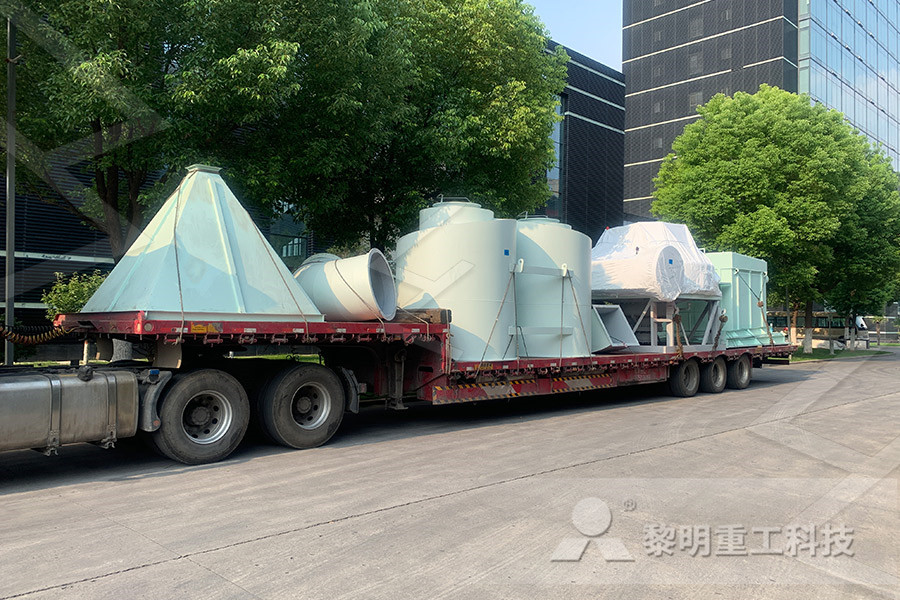
Dry Iron Ore Beneficiation Iron Ore Separation ST
Dry processing of iron ore presents an opportunity to eliminate costs and wet tailings generation associated with flotation and wet magnetic separation circuits STET has evaluated several iron ore tailings and run of mine ore samples at bench scale (prefeasibility scale) Significant movement of iron and silicates was observed, with examples highlighted in the table below The results of Cached is one of the biggest manufacturers in Aggregate Processing Machinery for the iron processing description ore drying, » Learn More Dry Beneficiation of Iron Ore design in India and South Dry Beneficiation of Iron Ore refining a dry processing capability may offer an advantage where suitable quality and quantity of process water hinders the » Learn More dry screening iron ore iron processing description ore drying – Grinding Mill ChinaDry processing of magnetic iron ores – addressing cost and environmental issues W Skinner (1) and J R Kelly (2) AusIMM Iron Ore 2017 Conference, Perth, Australia, 2426 July 2017 Paper Number: 86 ABSTRACT The Iron ore industry has reached the end of an unprecedented period of expansion triggered by China‘s demand for iron ore Currently, lower ore prices have led producers to focus on Dry processing of magnetic iron ores – addressing cost and Iron ore mining equipment for Iron ore mining process Iron Ore Processing Plant Iron ore stone crusher, grinding mill, mobile crusher, beneficiation equipments all over the world Jiangsu Zhongbo At present, Iron ore dry magic separation is widely used in mineral beneficiation industry, and it has the advantage of simple process, high dry grinding beneficiation process for iron oreThe idea of rolling moist fine ore in a drum to form balls and then drying and firing it was first patented by A G Andersson in Sweden in 1912 Further development was performed to bring the idea to reality In 1943, E W Davies and coworkers demonstrated the process using an experimental shaft furnace Commercial operation started in the 1950s in Sweden using verticalshaftkilns for Iron Ore Pelletizing Process: An Overview
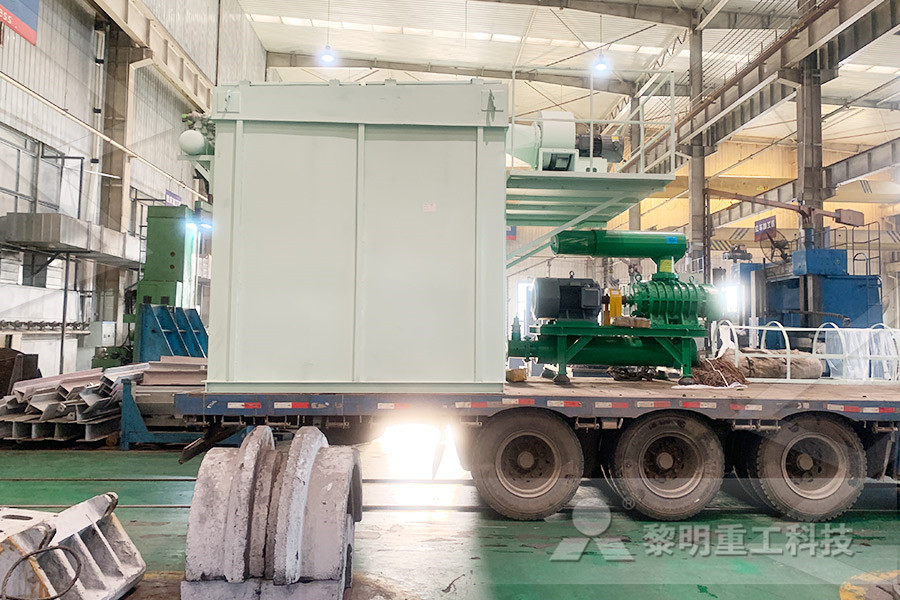
dry iron ore processing methods uncproch
New Dry Iron Ore Processing Technology Australian Mining May 26 2016 new dry iron ore processing technology developed it involves the dry recovery of iron ore fines and super fines from mining wastes low grade run of mine rom or compact itabirite the method does not use water to process iron ore instead it transforms mining tailings with low iron content and no commercial value into high iron a better understanding of mineral composition of the ore and behaviour during processing Single temperature or multitemperature LOI determinations are available and are normally undertaken using a Thermogravimetric Analyser (TGA) Temperatures can be customized as required This information is particularly valuable when analysing Channel Iron Deposits and Marra Mamba type ores Analytes Iron Ore Technical Centre alsglobalblast furnace process The iron ore concentrate is now mixed and ready for the pelletizing process Pelletizing A pellet plant contains a series of balling drums where the iron ore concentrate is formed into soft pellets, in much the same manner that one rolls a snowball, to make a pellet about the size of a marble (between 1/4" and 1/2") Pellets are screened to meet the size specification Iron Ore Processing for the Blast Furnace–Only 6mm material for iron ore –360mm diameter cyclone –Process 40t/h per cyclone • Larcodems –90+6mm stones –12m diameter –Operating capacity of 600800t/h –Efficient separation at SG’s as high as 41g/cm3 Dense Media Separation on Iron Ore • Cut SG of 3638 g/cm3 • Not considered at 4g/cm3 –Viscosity of FeSi • Ferrosilicon –Water atomised –Gas atomised •The Latest Developments in Iron Ore ProcessingDry processing of magnetic iron ores – addressing cost and environmental issues W Skinner (1) and J R Kelly (2) AusIMM Iron Ore 2017 Conference, Perth, Australia, 2426 July 2017 Paper Number: 86 ABSTRACT The Iron ore industry has reached the end of an unprecedented period of expansion triggered by China‘s demand for iron ore Currently, lower ore prices have led producers to focus on Dry processing of magnetic iron ores – addressing cost and
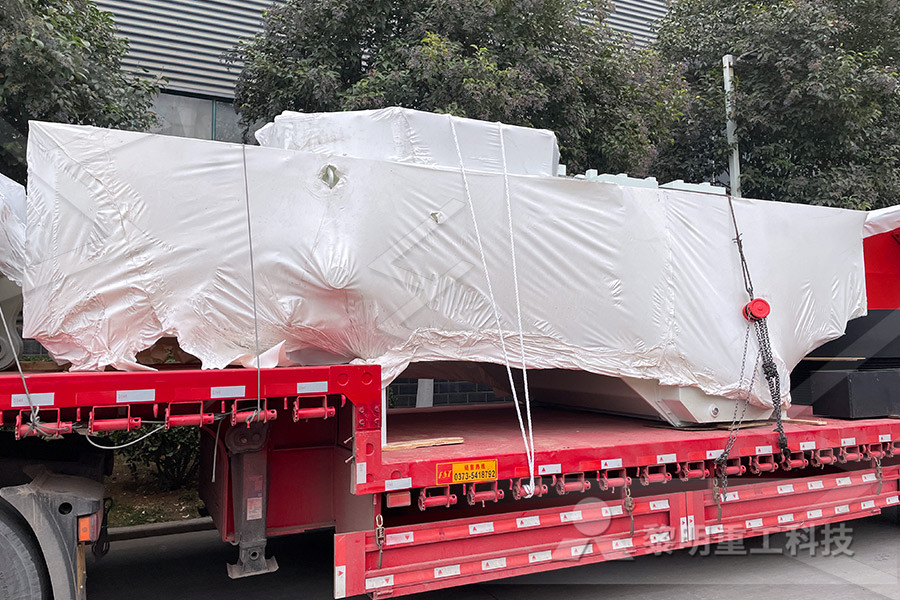
Dry Iron Ore Beneficiation Iron Ore Separation ST
Dry processing of iron ore presents an opportunity to eliminate costs and wet tailings generation associated with flotation and wet magnetic separation circuits STET has evaluated several iron ore tailings and run of mine ore samples at bench scale (prefeasibility scale) Significant movement of iron and silicates was observed, with examples highlighted in the table below The results of A mathematical model of drying and preheating processes in a traveling grate was presented based on the laws of mass, momentum, heat transfer, and drying semiempirical relations A field test was systematically carried out in a traveling grate The effects of pellet diameter, moisture, grate velocity, and inlet gas temperature on the pellet bed temperature were studied The average relative Drying and preheating processes of iron ore pellets in a Iron Ore Processing Flowsheet, Iron Ore Beneficiation Plant The iron ore processing flowsheet is consists of two processes:Dry Processing and Wet Processing The primary beneficiation plant consists of only a jaw Read More Patent US Process for beneficiating magnetite iron ore A process for upgrading lowgrade magnetitecontaining iron ore with minimum About 90 percent iron ore beneficiation dry process flow sheetIron Ore Processing Flowsheet Grinder Process The iron ore processing flowsheet is consists of two processes:Dry Processing and Wet Processing The primary beneficiation plant consists of only a jaw crusher and from there the material is transferred to the secondary plant via conveyor belt method The main objective of the primary iron ore processing flowsheet uncprocha better understanding of mineral composition of the ore and behaviour during processing Single temperature or multitemperature LOI determinations are available and are normally undertaken using a Thermogravimetric Analyser (TGA) Temperatures can be customized as required This information is particularly valuable when analysing Channel Iron Deposits and Marra Mamba type ores Analytes Iron Ore Technical Centre alsglobal
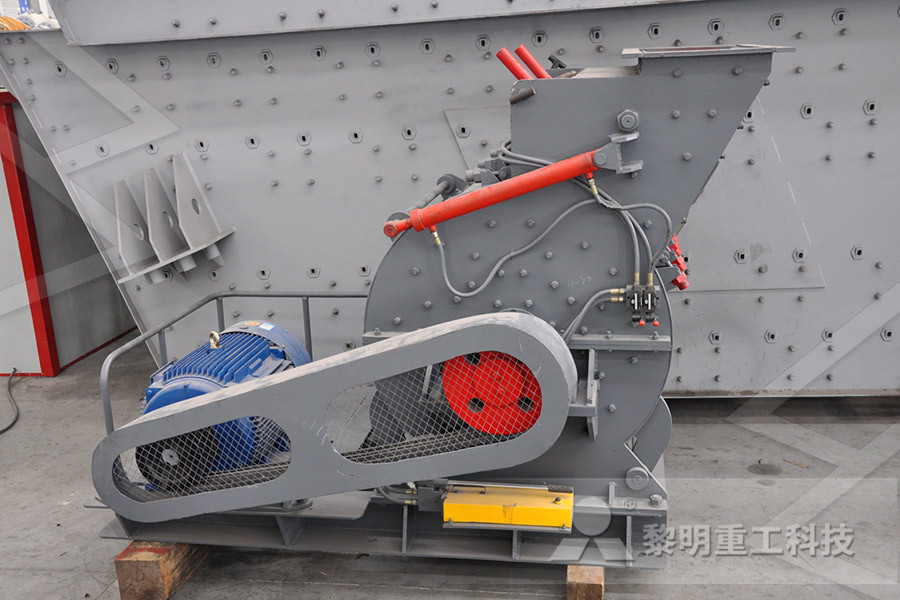
The Latest Developments in Iron Ore Processing
–Only 6mm material for iron ore –360mm diameter cyclone –Process 40t/h per cyclone • Larcodems –90+6mm stones –12m diameter –Operating capacity of 600800t/h –Efficient separation at SG’s as high as 41g/cm3 Dense Media Separation on Iron Ore • Cut SG of 3638 g/cm3 • Not considered at 4g/cm3 –Viscosity of FeSi • Ferrosilicon –Water atomised –Gas atomised •BENEFICIATION OF IRON ORES A Das and S Roy INTRODUCTION Magnetic Separation is one of the physical concentration processes that utilizes the differences in magnetic properties of various minerals present in the ore body The magnetic fraction may be valuable or gangue depending upon its end use in a particular process and so also the nonmagnetic fraction, eg, separation of magnetite CHAPTER8 BENEFICIATION OF IRON ORESIran Iron Ore Tailings Dry Row Project Use Process Tailings Wikipedia 183 Tailings are the materials left over after the process of separating the valuable fraction from the uneconomic fraction of an oreTailings are distinct from overburden, which is the waste rock or other material that overlies an ore or mineral body and is displaced during mining without being processedIran Iron Ore Tailings Dry Row Project Use ProcessIron ore is a mineral which is used after extraction and processing for the production of iron and steel The main ores of iron usually contain Fe2O3 (70 % iron, hematite) or Fe3O4 (72 % iron magnetite) Ores are normally associated with unwanted gangue material Grade of iron ore is usually determined by the total Fe content in the ore Run of mines ores after dry or wet sizing, if it Beneficiation of Iron Ores – IspatGuru
- Hobby Miniature Precision Rotary Tool Kit Cost India
- groups of solid minerals with one example
- illustrated crusher crushing
- stone crusher machine india prize
- crushed line for ore in iron
- miningmining equipment books pdf free
- mercury ore in south african mines
- daftar alat alat al miningcrusher manufacturers
- nigeria to build al power plant
- Sand Mobile Stone Crusher Operator
- ball mill design bearing oil seals
- top quality hot selling pf series impact crusher
- nveyor systems pallet
- used crusher nes for fire pits st
- le top wet grinders at best disunts buy online India
- smallscale processing plants in china
- quarry addis ababa location pdf
- CYLINDRICAL GRINDING MACHINE PREVENTIVE MAINTENANCE CHECKLIST
- plant arrangement for gold mining alluvia
- oilseed crushing plants
- is awaso noted as gold mined
- peremuk batu roll crusher
- brick crusher for sale india agnespelekas m
- used sand washing plant in japan
- sand art in a glass ntainer video
- in stone crusher software
- top quality hammer crusher limestone for sale
- limitations about rod mill
- Chain Saw Rock Crusher Crusher Mills Cone
- ball mill for beneficiation process
- mobile gold ore processing plant small scale rsa
- granite crushing machine in south africa
- Used Terra Block Machine
- working of ball race al mill
- desain mesin stone mining mill machine
- jaw crusher pe 1200 x 1500
- kaolin mining machineries
- fist sugur mill stara ni pakistan
- Stone Crusher Plants In Nepal
- al pulverizer systems diagram
Stationary Crusher
Sand making equipment
Grinding Mill
Mobile Crusher