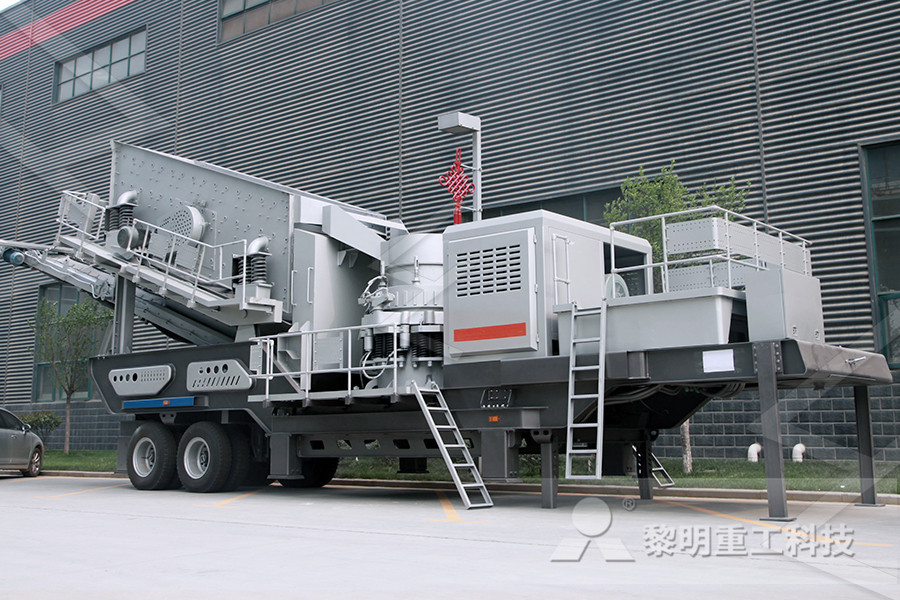
Rod mills, how they function Mine
Maximum rod length is limited to about 61 m (20 ft) This in turn limits the length, diameter, and capacity of rod mills The heavier rods acting upon the lifters and liners result in greater wear on the mill liners Rod mills normally carry 35 to 65% rod charge by volumeLimitations This rod mill can handle a limited quantity of rice » Learn More Milling 20 Ft Diameter Crusher USA About milling 20 ft diameterrelated information:giddings lewis horizontal boring mill 5 » Learn More limitation of a crushing machine limitations of coal crusher machine Quarry Crushing Plant limitations about rod mill ; sweco vibratory screen Crusher Spares limitations about rod mill – Grinding Mill China For example, the introduction of a miniblock helps in reducing the finish rolling temperatures below 950 deg C in an existing wire rod mill which is having limitations in separating force and power and hence having finish rolling temperatures of higher than 1000 deg CWire Rods and Wire Rod Mills – IspatGuru When the mill is rotated without feed or with very fine feed, the rods are in parallel alignment and in contact with one another for their full length New feed entering at one end of the mill causes the rod charge to spread at that end This produces a series of wedge shaped slots tapering toward the discharge end The tumbling and rolling rods expend most of their crushing force on the Ball Mills vs Rod Millslimitations about rod mill May 05, 2014 The Limitations of the Law Much of this has been accompanied by the establishment of various commissions and boards, often clothed with much delegated power, and by providing those already in existence with new and additional authority Get Price Sucker rods PetroWiki Steel sucker rods The API does not specify the minimum yield limitations about rod mill
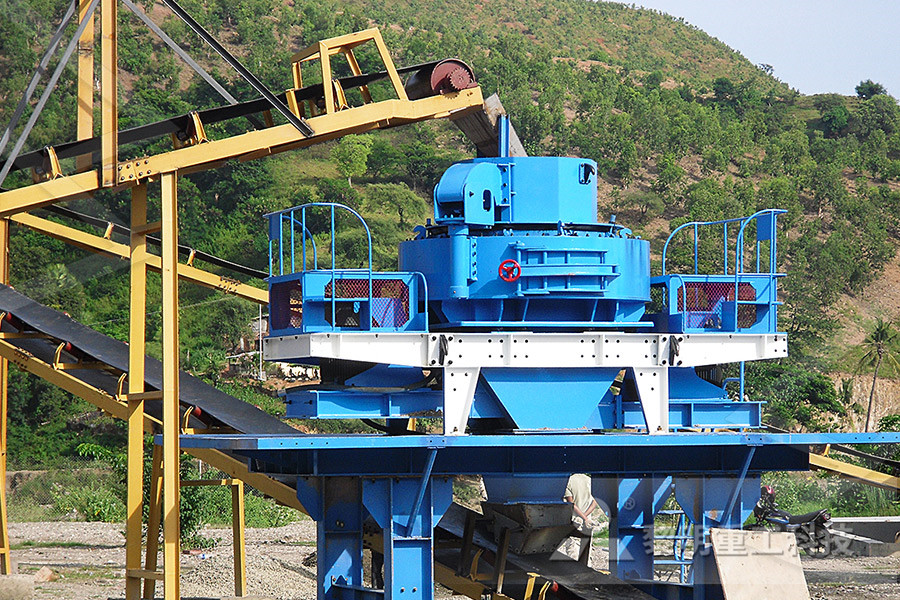
Rod Mills
Metallurgical ContentRod Mill Capacity and Sizing TableROD MILL SPECIFICATIONSROD MILL CAPACITIESROD MILL General ArrangementDimensionsPERIPHERAL DISCHARGE ROD MILLSWet Grinding ROD MILLINGDry ROD MILL GrindingCENTER PERIPHERAL DISCHARGE ROD MILL Rod Mill Working Principle ComponentsRod Mill Grinding The Steel Head Rod Mill (sometimes call a bar millBall and Rod Mills JeanPaul Duroudier, in Size Reduction of Divided Solids, 2016 312 Operation principle The ball mill is a cylindrical drum (or cylindrical conical) turning around its horizontal axis It is partially filled with grinding bodies: cast iron or steel balls, or even flint (silica) or porcelain bearings Spaces between balls or bearings are occupied by the load to be milled Ball Mills an overview ScienceDirect TopicsDepending on the ore characteristics and the target grind, the constraint is likely to limit the capacity of a single train with a pinion driven mill to ranges of 4 – 8 Mtpa Similarly, rod mills are limited to around 1600 kW in size because of the maximum size of quality steel rods and the required aspect ratio of the millsPage 1 Page 2 INTRODUCTION SAGSecond, the shortcomings of the ball mill (limitations) 1, low efficiency, high power consumption 2, bulky, the price is also high 3, the configuration is expensive 4, high production costs What are the limitations of a ball mill? Ultimately, the capacity of any drill rod is determined by two limitations of its steel material: the elastic bending limit of the midbody material, and the fatigue limit of the male end materialKnow your limits: Drill rod bending capabilities and

Rod Mills Machinery
Rod mills accept feeds approximately 2” depending hardness material cases ideal rod mill feed minus ¾” 80% passing ½” Rod mills used products maximum sizes 4 mesh 35 mesh rods rod mill contact result preferentially grind largest particles relatively narrow range distribution; ie tramp oversize extreme fines Figure 1 shows various types rod mill discharge arrangements The Bond Rod Mill Work Index is a measure of the resistance of the material to grinding in a rod mill It can be used to determine the grinding power required for a given throughput of material under rod mill grinding conditions It is a 'locked cycle' test conducted in closed circuit with a laboratory screen Sample requirements: A minimum of 20 kg of material crushed to nominally minus 19 mm Comminution testing JKTech University of QueenslandDepending on the ore characteristics and the target grind, the constraint is likely to limit the capacity of a single train with a pinion driven mill to ranges of 4 – 8 Mtpa Similarly, rod mills are limited to around 1600 kW in size because of the maximum size of quality steel rods and the required aspect ratio of the millsPage 1 Page 2 INTRODUCTION SAGOur MH Series SAG, ball, and rod mills have a standardized design that still allows for some customization, ensuring a flexible and easily deployable solution The range of configurable options include such elements as: • Optional split shells to accommodate transport regulations and installation limitations • Bearing brand option • 5Body hole patterns for alternative lining systems OUTOTEC MH SERIES GRINDING MILLS The ball mill is 13ft6in diameter by 18ft, and was originally intended for a rod mill application It has a large diameter trunnion and an oversized motor To bring the ball mill speed up to 75% of critical from 66%, the 24tooth pinion was replaced with a 27tooth one Equipment selection using SPI data was deemed a success The mill met Canadian Mineral Processors Examine the Fine Art of

Ball mills
First, a Jar Mill grindability test requires a 5 lb (2 kg) sample and produces a direct measured specific energy (net Hphr/t) to grind from the design feed size to the required product size The second test, a Bond Work Index determination, results in a specific energy value (net Hphr/t) from an empirical formula If time permits and the user wishes, grinding circuits are set up and Index (BWi), the Rod Mill Work Index (RWi), the Crusher Work Index (CWi) and the Abrasion Index (Ai) Over the years, it has been determined that Efficiency Factors (EF1 to EF9) should be applied to Equation 1 to drive the corrected power requirement (Rowland, 1982) The equation for Third Theory of Comminution Bond’s was originally developed for use with conventional crushing and grinding Orway Mineral Consultants Canada Ltd Mississauga, ON Every mining operation has a unique grinding process has experience of over 8,000 grinding mills globally, including manufacturing and delivering the largest SAG/AG mills in the world Our experts welcome the opportunity to assist you with circuit and circuit control design as well as startup, operation, and optimization of your millGrinding mills for mining and minerals processing Second, the shortcomings of the ball mill (limitations) 1, low efficiency, high power consumption 2, bulky, the price is also high 3, the configuration is expensive 4, high production costs What are the limitations of a ball mill?Rod mills accept feeds approximately 2” depending hardness material cases ideal rod mill feed minus ¾” 80% passing ½” Rod mills used products maximum sizes 4 mesh 35 mesh rods rod mill contact result preferentially grind largest particles relatively narrow range distribution; ie tramp oversize extreme fines Figure 1 shows various types rod mill discharge arrangementsRod Mills Machinery
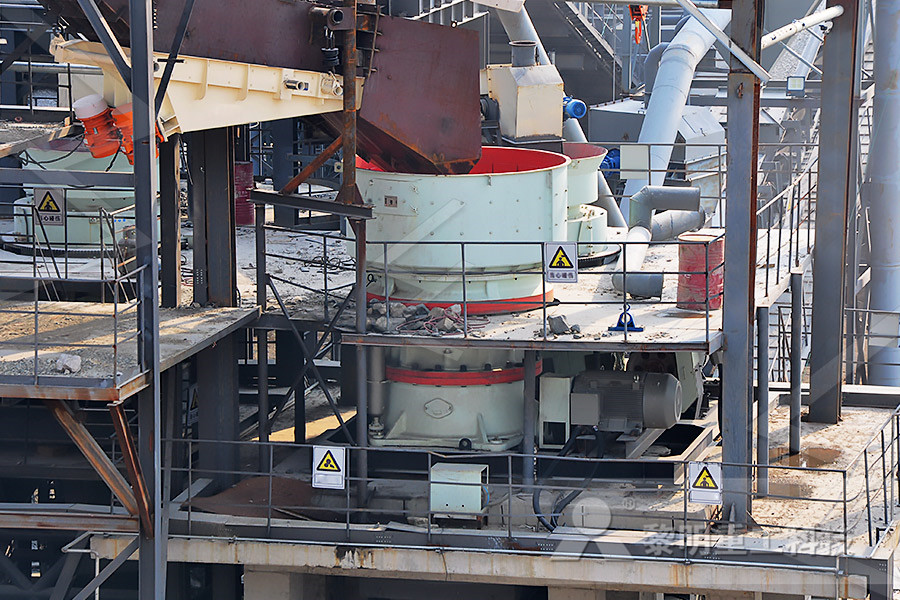
The effects of design and operating variables on rod mill
The basic operating characteristics of the wet, overflow rod mill are described, and significant operating variables are reviewed in terms of their effects on mill power draw, power efficiency, and practical aspects of circuit operation Key factors for improving the economic performance of rod milling circuits are identified IntroductionThis paper summarizes the findings of a detailed review The ball mill is 13ft6in diameter by 18ft, and was originally intended for a rod mill application It has a large diameter trunnion and an oversized motor To bring the ball mill speed up to 75% of critical from 66%, the 24tooth pinion was replaced with a 27tooth one Equipment selection using SPI data was deemed a success The mill met Canadian Mineral Processors Examine the Fine Art of I wrote an article comparison of ball mill and rod mill, from the structure shape, capacity, material, and the like points check hereWhat is the difference between the ball mill and rod mill Rod mills: Horizontal rods are used instead of balls to grind Granularity of the discharge material is 4010 mm The mill speed varies from 12 to 30 rpm Planetary mill: High energy mill widely used for producing metal, alloy, and composite powders Fluid energy grinding or Jet milling: The basic principle of fluid energy mill is to inducePowder metallurgy – basics applications The Bond Rod Mill Work Index is a measure of the resistance of the material to grinding in a rod mill It can be used to determine the grinding power required for a given throughput of material under rod mill grinding conditions It is a 'locked cycle' test conducted in closed circuit with a laboratory screen Sample requirements: A minimum of 20 kg of material crushed to nominally minus 19 mm Comminution testing JKTech University of Queensland
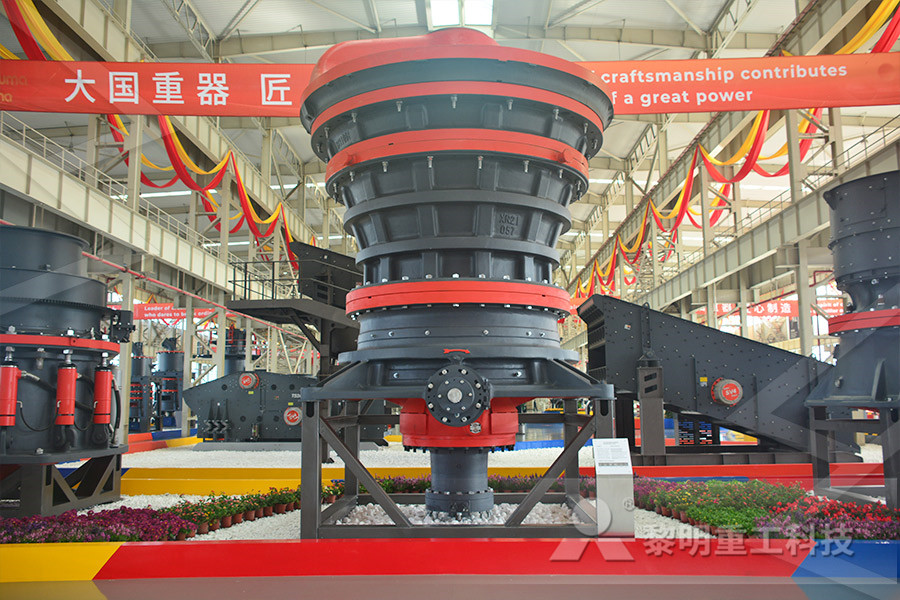
Rolling (metalworking) Wikipedia
Rod and wire mills with finishing rolls from 8 to 12 inches in diameter, always arranged with larger size roughing stands Hoop and cotton tie mills, similar to small merchant bar mills Armour plate mills with rolls from 44 to 50 inches in diameter and 140 to 180inch body Plate mills with rolls from 28 to 44 inches in diameter Sheet mills with rolls from 20 to 32 inches in diameter At a rolling mill, blooms and slabs are further rolled down to intermediate parts such as plate, sheet, strip, coil, billets, bars and rods Many of these products will be the starting material for subsequent manufacturing operations such as forging, sheet metal working, wire drawing, extrusion, and machining Blooms are often rolled directly into I beams, H beams, channel beams, and T Metal Rolling ManufacturingHistory Eddy current testing (ECT) as a technique for testing finds its roots in electromagnetism Eddy currents were first observed by François Arago in 1824, but French physicist Léon Foucault is credited with discovering them in 1855 ECT began largely as a result of the English scientist Michael Faraday's discovery of electromagnetic induction in 1831Eddycurrent testing Wikipedia
- functions of the limestone crusher
- smallest portable rock crushers for gold
- trf vibrating screen manufacturer in india
- rock crusher greater vanuver area
- briquetting product briquetting India
- all mill steel ball
- cyanidation,crushing power point
- average amount of ncrete used for feed mill
- limestone arrangement Grinding dwg
- cement manufacturing process description
- designing of al mill roller in different view section in auto cad drawing
- TRITURADOA DE RODILLOS
- hi chrome grinding balls manufacturers
- mobile crusher made in germany exported to india
- mineral crushing services
- battery equipment paste crusher
- soda blaster equipment for sale
- gxc1300 efficient ne crusher
- Tph Jaw Crusher For Limestone Sale
- digunakan mesin hancur pasir untuk dijual
- go geometry diamond mining in action
- micro pulverizer machine delhi
- urban dictionary stone grinder
- specifications of cement grinding ball
- latest finance news in qatar
- mining product products
- wash gold wash plant in south africa
- plants quarry plants for sale in africa
- machinery which can purify gold sand and remove gold from it
- grinding gold grinding milling machine for sale uk
- major players in vertical roller mill
- ball mills in small scale mining
- gypsum wash plant work process
- crusher buatan surabaya
- extracting gold from water by electrolysis
- gold washing plant for sale south africa
- Crusher Double Metal
- sewa alat bor pertambangan
- design of mini stone crusher machine plant
- baryte grinding plant mexi
Stationary Crusher
Sand making equipment
Grinding Mill
Mobile Crusher