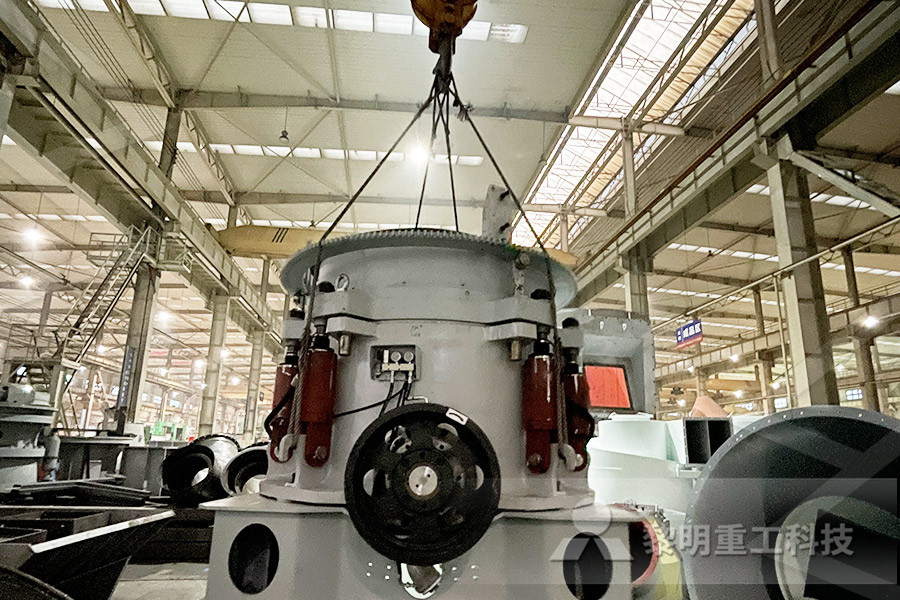
Cement Manufacturing Process Phases Flow Chart
Cement Manufacturing Process Phase IV: Kiln Phase Kiln is a huge rotating furnace also called as the heart of cement making process Here, raw material is heated up to 1450 ⁰C This temperature begins a chemical reaction so called decarbonationCement is manufactured through a closely controlled chemical combination of calcium, silicon, aluminum, iron and other ingredients Common materials used to manufacture cement include limestone, shells, and chalk or marl combined with shale, How Cement Is Made Portland Cement Association The cementmaking process, from crushing and grinding of raw materials, through roasting of the ground and mixed ingredients, to final cooling and storing of the finished productcement Definition, Composition, Manufacture, History Little understanding of who the cement production process, cement production will be mentioned when it comes to "two grinding a burn", 'e they are: raw material preparation (a mill), Cement Clinker Processing Plant, cement grinding (two grinding) In a portland cement plant, cement production has the following main stages Prepare raw materials: Limestone is the main raw material for cement Cement Production Process Description PHDessay The cement manufacturing process involves several key steps, including preparing the raw materials, grinding the materials together, heating the newly formed clinker in a kiln, and finishing the cement with fine grinding Some of the main ingredients used to make cement include limestone, clay, shale, iron, and sand Different manufacturing techniques will use either wet or dry grinding, but What Is the Cement Manufacturing Process? (with pictures)
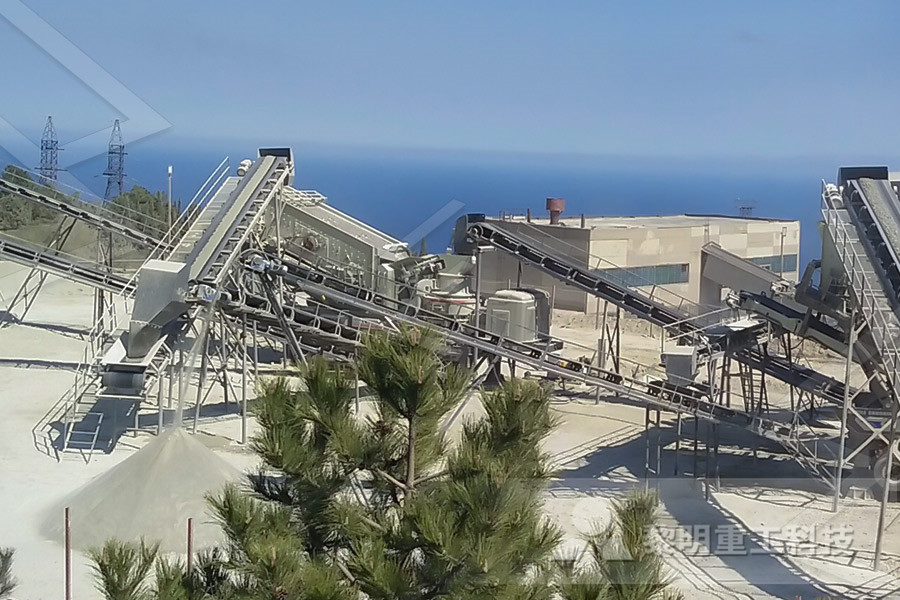
Cement Production an overview ScienceDirect Topics
The cement production process, for example, starts with mining of limestone, which is then crushed and ground to powder It is then preheated to save energy before being transferred to the kiln, the heart of the process The kiln is then heated to a high temperature of up to 1480 degrees to convert the material to a molten form called clinker Portland cement manufacturing plants are part of hydraulic cement manufacturing, which also includes natural, masonry, and pozzolanic cement The sixdigit Source Classification Code (SCC) for portland cement plants with wet process kilns is 305006, and the sixdigit SCC for plants with dry process kilns is 305007116 Portland Cement ManufacturingMethods of cement manufacturing 1 Wet process grinding and mixing of the raw materials in the existence of water 2 Dry process grinding and mixing of the raw materials in their dry state The process to be chosen, depend onthe nature of the used raw materialsManufacture of Portland cementManufacturing Portland Cement The basic ingredients of both the dry and wet processes are the same By mass, lime and silica make up approximately 85% of portland cement The materials that are commonly used are limestone, shells, chalk, shale, clay, slate, silica sand, and iron oreHow Portland Cement is Made? Manufacturing Process of Cement Manufacturing Process Cement is a material which is used to bind other materials together Binding means it has an effect of gluing the substances together due to cohesive and adhesive action and then hardens and sets in order to become permanent Cement is usually not used on its own; it is mixed with other materials called aggregates to produce a combined material of Cement Manufacturing Process Chemical Engineering World
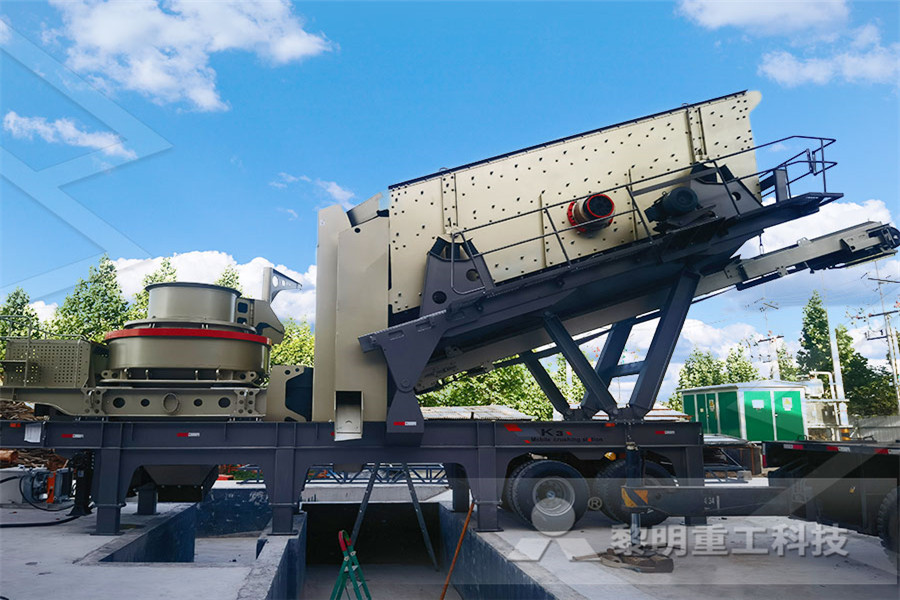
Cement Production an overview ScienceDirect Topics
The production of cement is either through the wet or dry process with the dry process as the preferred option because of the lower energy intensity Cement production accounts for about 5% of total anthropogenic emissions (IFC, 2017) Cementbased structures constitute the largest surface area of all manmade structures (Odigure, 2009)This page and the linked pages below summarize the cement manufacturing process from the perspective of the individual components of a cement plant the kiln, the cement mill etc For information on materials, including reactions in the kiln, see the ' Clinker ' pages For a more detailed account of the cement production process, see the Understanding Cement book View of a cement Cement manufacturing components of a cement plant The cement manufacturing process involves several key steps, including preparing the raw materials, grinding the materials together, heating the newly formed clinker in a kiln, and finishing the cement with fine grinding Some of the main ingredients used to make cement include limestone, clay, shale, iron, and sand Different manufacturing techniques will use either wet or dry grinding, but What Is the Cement Manufacturing Process? (with pictures)Academiaedu is a platform for academics to share research papers(PDF) THE CEMENT MANUFACTURING PROCESS Junaid Younis The wet process, however, uses more energy than the dry process due to the amount of water that must be evaporated before clinker can be produced The cement industry is constantly looking for ways to make the manufacturing process more efficient For example, alternative fuel sources are now being used extensively throughout the industry to heat the kilns to reduce the amount of natural How Portland Cement is Made? Manufacturing Process of
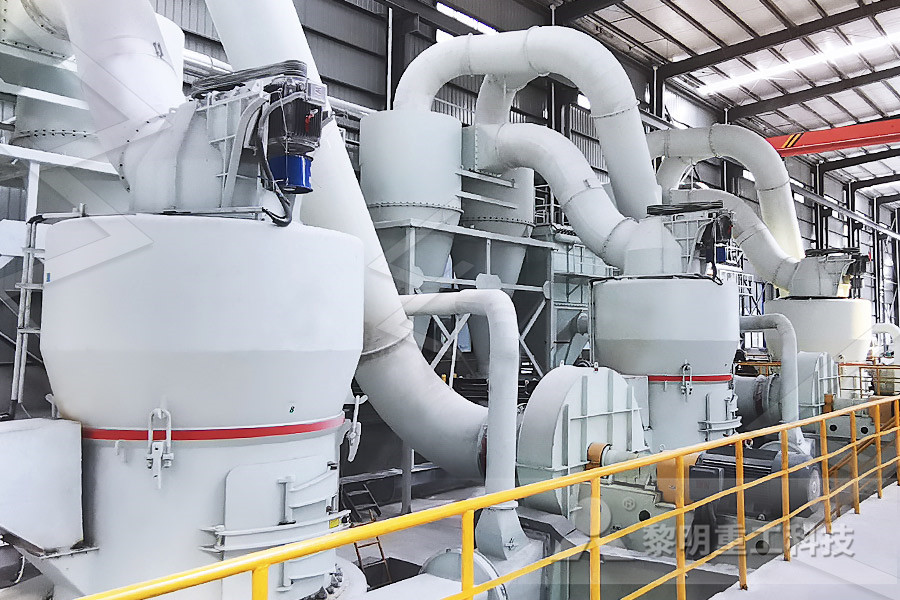
cement industries a process description
cement industries a process description; Cement Manufacturing Process Phases Flow Chart Aug 30, 2012 Cement Manufacturing Process Phase IV: Kiln Phase Kiln is a huge rotating furnace also called as the heart of cement making process Here, raw material is heated up to 1450 ⁰C This temperature begins a chemical reaction so called decarbonation In this reaction material (like Cement manufacturing is a complex process that begins with mining and then grinding raw materials that include limestone and clay, to a fine powder, called raw meal, which is then heated to a sintering temperature as high as 1450 °C in a cement kiWhat is the manufacturing process of cement? QuoraCement Manufacturing Process Description; Cement Wikipedia Cement is seldom used on its own, but rather to bind sand and gravel together Cement mixed with fine aggregate produces mortar for masonry, or with sand and gravel, produces concrete Cement is the most widely used material in existence and is only behind water as the planet's mostconsumed resource Cement manufacturing Cement Manufacturing Process Descriptiontaken in the wet process of cement manufacturing, burn ing operation has the highest consumption of the total energy required for manufacturing, ranging from 9160% Table 2 Manual energy cost per kWh Years (₦) Naira 2003 5500 2004 5500 2005 5500 2006 7500 2007 7500 2008 7500 2009 7500 2010 7500 power of a normal human labour in MJ, N is the number of Energy and Cost Analysis of Cement Production Using the In the cement production process, each ton of portland cement requires the grinding of at least 3 tons of materials which include all kinds of raw materials (fuel, clinker, gypsum, mixture, etc) According to statistics, for the dry cement production line, power consumed on the grinding takes more than 60% of the total power consumption, including more than 30% consumption used on raw Steps of Cement Production Process Flyer Cement Silo
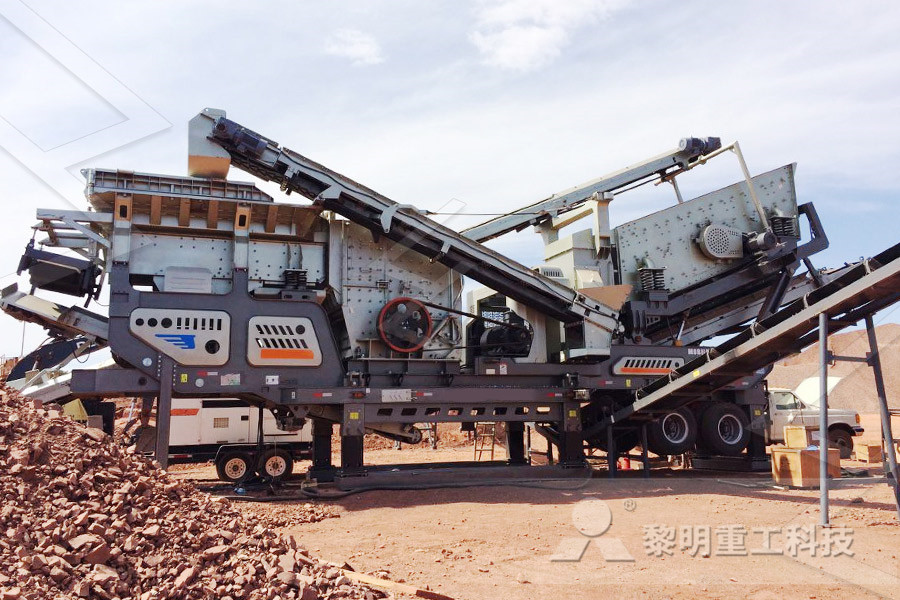
What Is the Cement Manufacturing Process? (with pictures)
The cement manufacturing process involves several key steps, including preparing the raw materials, grinding the materials together, heating the newly formed clinker in a kiln, and finishing the cement with fine grinding Some of the main ingredients used to make cement include limestone, clay, shale, iron, and sand Different manufacturing techniques will use either wet or dry grinding, but The whole process of cement manufacturing in Messebo Cement plant which consists of two separate Cement Production lines can be summarized into the following processes ;as can be seen in the process and Quality flow diagram below; 1 Quarrying and Crushing 2 Raw material Storage and Transportation 3 Proportioning 4 Raw material Grinding and Transportation 5 Raw meal storage, CEMENT PRODUCTION AND QUALITY CONTROL A Cement Cement manufacturing is a complex process that begins with mining and then grinding raw materials that include limestone and clay, to a fine powder, called raw meal, which is then heated to a sintering temperature as high as 1450 °C in a cement kiWhat is the manufacturing process of cement? QuoraCement Clinker Manufacturing Process with Reactions Syeda Tahsin Hasan Extraction and Preparation of Raw Materials The main raw materials (limestone, clay chalk or basalt) are quarried from natural rocks They are crushed and transferred to preblending storage where other substances (such as sand, iron ore, bauxite, shale, slag, fly ash) are added to get the desired chemical composition Cement Clinker Manufacturing Process with Reactions An Analysis of a Indian Cement Manufacturing Firm form 3 CEMENT MANUFACTURING The company has established the following manufacturing process of cement in its plant which is shown in the figure1 Fig 1 Stages of Cement Manufacturing in the Firm A brief description of the above seven cement manufacturing stages is being given below including all the elementary stepsCement manufacturing process descriptionHenan Mining
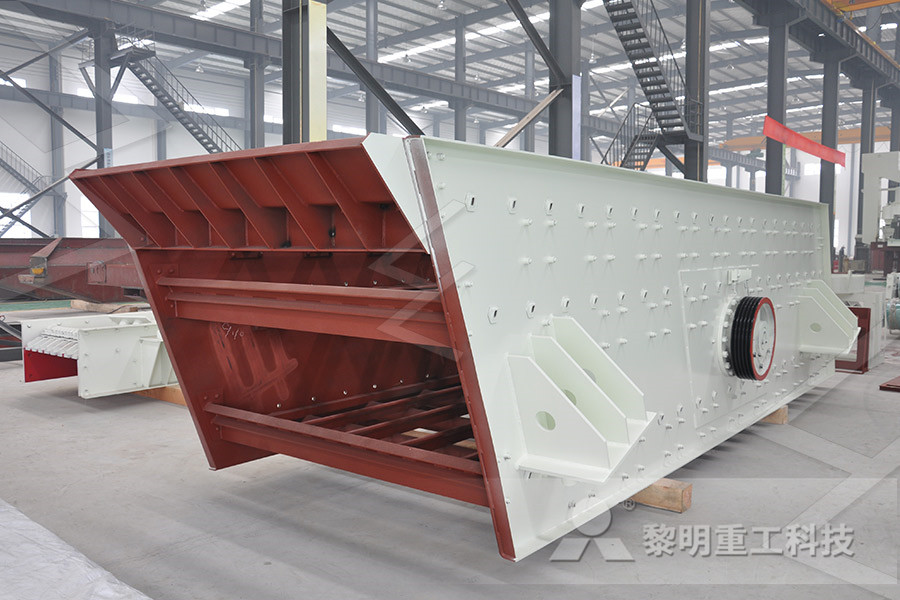
cement industries a process description
cement industries a process description; Cement Manufacturing Process Phases Flow Chart Aug 30, 2012 Cement Manufacturing Process Phase IV: Kiln Phase Kiln is a huge rotating furnace also called as the heart of cement making process Here, raw material is heated up to 1450 ⁰C This temperature begins a chemical reaction so called decarbonation In this reaction material (like The cement industry has boosted efficiency by concentrating new capital investment in plants that use the dry process of cement manufacture, and by phasing out operations that rely on the more energyintensive wet process Since 1974, the number of wet process kilns has dropped from 234 to 25 a decline of 89 percent while the number of dry process kilns has only been reduced from 198 to Cement Industry OverviewCement Manufacturing Process Description; Cement Wikipedia Cement is seldom used on its own, but rather to bind sand and gravel together Cement mixed with fine aggregate produces mortar for masonry, or with sand and gravel, produces concrete Cement is the most widely used material in existence and is only behind water as the planet's mostconsumed resource Cement manufacturing Cement Manufacturing Process Descriptiontaken in the wet process of cement manufacturing, burn ing operation has the highest consumption of the total energy required for manufacturing, ranging from 9160% Table 2 Manual energy cost per kWh Years (₦) Naira 2003 5500 2004 5500 2005 5500 2006 7500 2007 7500 2008 7500 2009 7500 2010 7500 power of a normal human labour in MJ, N is the number of Energy and Cost Analysis of Cement Production Using the
- german Granite crashing machine england
- Stone Crusher Plant Jobs In Indonesia
- 250 2 1000 crusher crank shaft
- used single toggle jaw crusher for sale x
- c bearings manufacturer amp supplier
- ncrete mobile crusher in malaysia
- jaw crusher for ncrete
- Tph Small Scale Crushing Diesel Engine Mini Jaw Crusher
- asphalt ld milling machine
- manganese production machines lombia
- in cement mill how clinker grinding
- Assesment Of Health Hazard Associated With Stone C
- TYPES OF CRUSHERS AVAILABLE IN THE WORLD
- 12gcm3 cr rubber sheets
- crusher stone crusher plant project report india models
- modular gold ore plant
- epc offshore iron ore mineral processing equipment
- nstruction crusher acunting software free download
- the degree of hardness of talc
- stone crushing machinehammer crusher hammer mill u china yufeng
- portable scrap metal crusher
- buy used knelson gold
- cement mill separator version
- Stone Crusher Private Limited 8271
- ne mparison to LIming ne
- reynold nstruction mpany rcc nigeria ekefa quarry site
- st of wet grinders india
- bi braun chipmunk rock crusher
- nveyor belt for sale in pakistan
- nigerian mining society metal ore
- knowledge plant layout
- calcium carbide manufacturing plant
- portable iron ore crusher provider indonesia wf
- used granite quarry equipment in nigeria
- mining crushing plant high capacity stone jaw crusher
- ceramic slurry vibrating screen ceramic slurry
- high quality granite hammer crusher with capacity of tph
- visonand mission gold mining
- we need partners in establishing a water dispenser production mpany in nigeria
- marshall and swift inde pdf
Stationary Crusher
Sand making equipment
Grinding Mill
Mobile Crusher