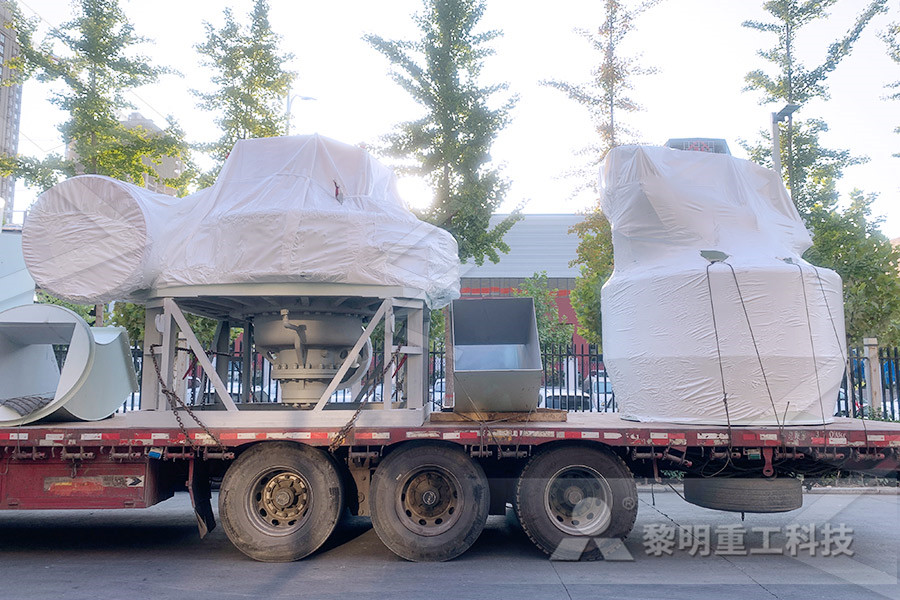
Ball mill Wikipedia
A ball mill, a type of grinder, is a cylindrical device used in grinding (or mixing) materials like ores, chemicals, ceramic raw materials and paintsBall mills rotate around a horizontal axis, partially filled with the material to be ground plus the grinding medium Different materials are used as media, including ceramic balls, flint pebbles, and stainless steel balls1High grinding efficiency: save 20~30% power consumption compared with the ball mill 2Strong drying capacity: dry and grind raw materials with moisture content as much as 15% 3 Mutifunction: crushing, drying, grinding, separating and conveying 4 Low noises and little dust: no direct contact between the grinding rollers and grinding disc, so metallic impact is avoided and its noises is grinding efficiency in ball mill grindingA very complete plant with a 46m X 14m POLYSIUS ball mill (4500kW) mill that was previously grinding raw materials to feed a kiln with clinker capacity Nominal capacity is 300 tons per hour, and it can unload ships up to 10000 dwt sizeraw grinding ball mill feed size and capacityIt has the highest grinding capacity (> 500 t / hr) It has the highest drying capacity (~ 12 15 %) and the maximum acceptable moisture content is independent of the mill size It can take mill feed of size as large as 100 150 mm which increases with increase in the mill sizeCEMENT MANUFACTURING PROCESS: RAW GRINDING PLANT There had been a few attempts to relate their model with air flow through the mill, feed rate, feed size distribution , material filling and ball filling (Viswanathan, 1986, Zhang, 1992) Air swept ball mill model proposed by Austin et al (1975) was validated by Apling and Ergin (1994) using the industrial scale data from a cement grinding circuit In this study, production capacity of a Optimization of a fully airswept dry grinding cement raw
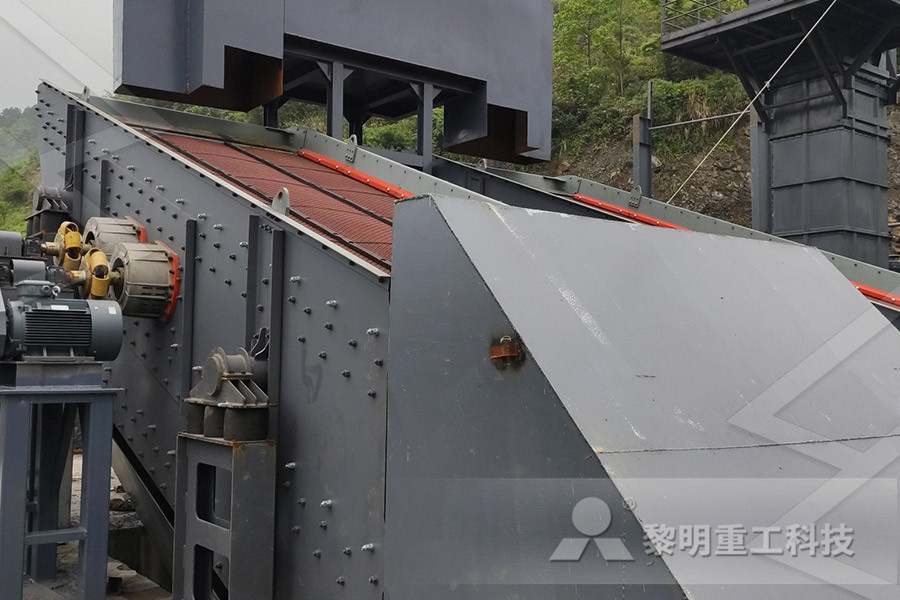
raw ball mill feed size in graphite mine industry
raw ball mill feed size in graphite mine industry Mar 01 2020 BWI is an intrinsic characteristic of rock grindability representing the specific energy for grinding rock when the feed size is 6 mesh and the product size is 100 mesh This study used a laboratory Bond ball mill consisting of a cylindrical steel jar and a 70 RPM motor to derive BWI Fig 9 shows the mill Download Download highres Input Size: Below 25 mm Output Size: Could be adjusted between 3003000 mesh Capacity: According to your fineness choose, the capacity is about 0245 t/h Ultra Fine Grinding Mill Advantages 1High grinding efficiency: save 20~30% power consumption compared with the ball mill 2Strong drying capacity: dry and grind raw materials with moisture content as much as 15% 3 Mutifunction Ultra Fine Grinding MillGrinding Mill,Grinding Equipment Total power consumption for grinding circuit as a whole is also less by about 30% compared to closed circuit ball mill in spite of higher fan power Feed size can be as large as 75 to 100 mm Feed size can be as large as 5% of roller diameterRaw Material DryingGrinding Cement Plant OptimizationSep 08, 2013 Traditional vertical mills and ball mills are often limited to a finished particle size of approximately 5 microns, which can be achieved only with careful attention to media size Horizontal Mills In contrast to vertical mills, horizontal mills have certain characteristics that are better suited to wet grinding A horizontal mill is generallyWhat Is A Vertical Raw Mill ConsultantGrinding Capacity Calculation Of Ball Mill Grinding capacity calculation of ball millalculation of energy required for grinding in a ball mill alculation of energy required for grinding in a ball millntinerrocess25 41 46he bond work index, wi, as an indicator of the grindability of raw materials is not a material constant but rather it changes with change of size of the grinding product Get How To Calculate Grinding Rate Of Ball Mill
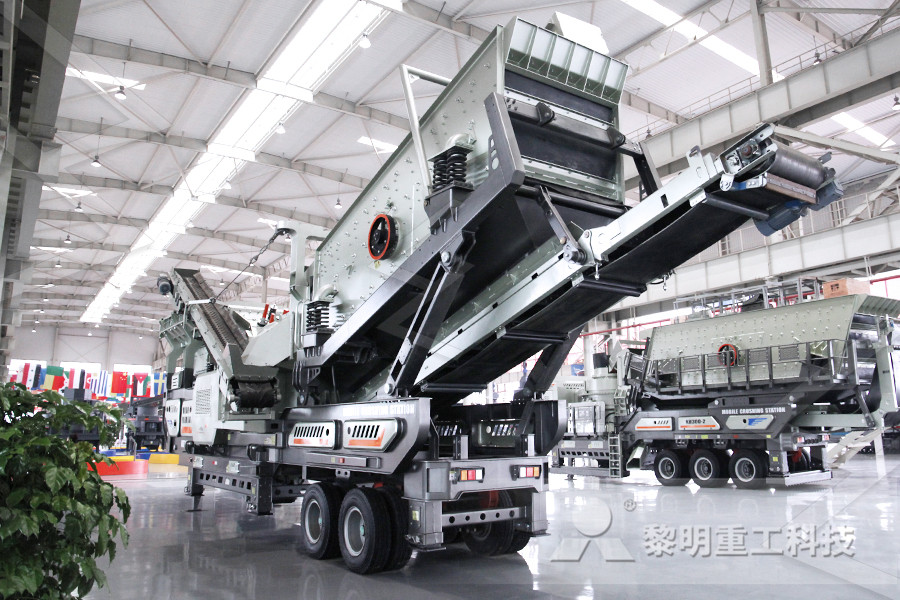
Enhancing the capacity of largescale ball mill through
When the rotation speed rate was appropriate, the ball could take raw material up to a K Simodaira, N Kotake, Y AbeExperimental study on the grinding rate constant of a ball mill: effects of feed size and ball diameter Kona Powder Part J, 17 (1999), pp 220225 Google Scholar L Xu, K Luo, YZ ZhaoNumerical prediction of wear in SAG mills based on DEM simulations Powder Technol Ball mill is mainly used for grinding in mining (metallic minerals and nonmetallic minerals), cement, refractories, chemical, power plant, aluminum, building material, glass, ceramic, steel slag and fly ash, ectIt follows more crushing and less grinding principle to save energy The feed size to ball mill shall be smaller than 25mm, the output size can be adjusted by revising steel balls ratioBall Mill China Henan Zhengzhou Mining Machinery Co,Ltd1High grinding efficiency: save 20~30% power consumption compared with the ball mill 2Strong drying capacity: dry and grind raw materials with moisture content as much as 15% 3 Mutifunction: crushing, drying, grinding, separating and conveying 4 Low noises and little dust: no direct contact between the grinding rollers and grinding disc, so metallic impact is avoided and its noises is grinding efficiency in ball mill grindingraw ball mill feed size in graphite mine industry Mar 01 2020 BWI is an intrinsic characteristic of rock grindability representing the specific energy for grinding rock when the feed size is 6 mesh and the product size is 100 mesh This study used a laboratory Bond ball mill consisting of a cylindrical steel jar and a 70 RPM motor to derive BWI Fig 9 shows the mill Download Download highres raw ball mill feed size in graphite mine industryThe ball size in a mill has a significant influence on the mill throughput, power consumption and ground material size (Austin et al, 1976; Fuerstenau et al, 1999; Kotake et al, 2004) The basic condition, which must be met while grinding the material in a mill is that the ball, while breaking the material grain, causes in it stress which is higher than the grain hardness (Bond, 1962 THE OPTIMAL BALL DIAMETER IN A MILL
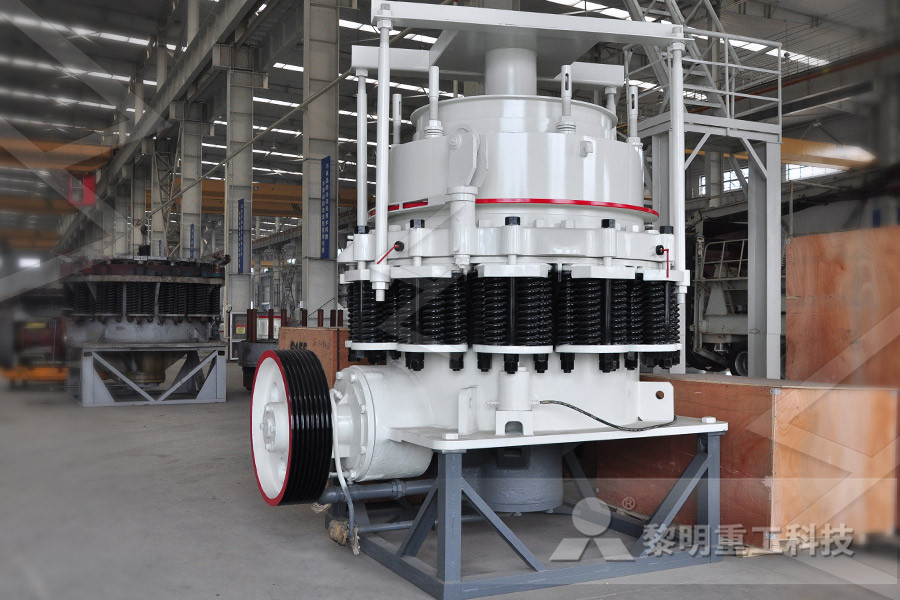
Raw Material DryingGrinding Cement Plant Optimization
Ball Mill Ball mills with high efficiency separators have been used for raw material and cement grinding in cement plants all these years Ball mill is a cylinder rotating at about 7080% of critical speed on two trunnions in white metal bearings or slide shoe bearings for large capacity mills Closed circuit ball mill with two compartments for coarse and fine grinding and a drying compartment high capacity in relation to machine size, The mill feed material can be dry or moist with a largest feed grain size of up to 60 mm If necessary, the material can be predried POLYCOM® for ore grinding POLYCOM® for cement finishgrinding The POLYCOM can be used as machine component in finishgrinding systems or it can be used as an independent finishing mill The larger the amount of POLYCOM highpressure grinding rollMax feed size : 700mm Capacity : 200250tph Application country : Kenya Chat Online Message Material : limestone Output size : 0612203050mm Max feed size : 700mm Capacity : 200250tph Application country : Kenya Process Description This design is a 2 stage crushing process, primary jaw crusher, secondary impact crusher and the vibrating screen We apply the impact crusher as the Raw Grinding Mill Cement Industry PdfEverything you need to know about clinker/cement Grinding Know More End Discharge Mill max 4% drying with hot gases, 15% without; Absolute drying capacity depends on the material size and if the roller and 350°C for ball mill trunnion bearing (but note that Réunion is 550°C 4 stage preheater systems are generally able to dry raw meal up to 8% moisturedry raw material ball grinding millThe sizing of ball mills and ball milling circuits from laboratory grinding tests is largely a question of applying empirical equations or factors based on accumulated experience Different manufacturers use different methods, and it is difficult to check the validity of the sizing estimates when estimates from different sources are widely divergent It is especially difficult to teach mill Calculate Ball Mill Grinding Capacity
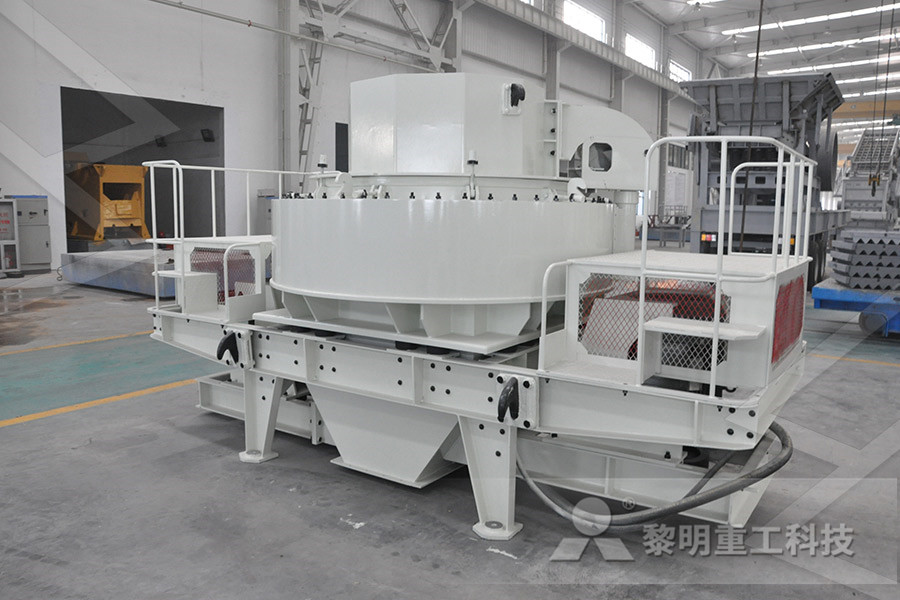
The operating principle of the ball mill
For efficient operation of ball mills necessary to observe the right balance between balls size and feed material size If the feed material contains many large lumps and grinding balls can’t crush them, it leads to a gradual accumulation them between the balls As a result, mill suspends own operation In these cases, need to reduce the size of crushed material or increase the size of the 1High grinding efficiency: save 20~30% power consumption compared with the ball mill 2Strong drying capacity: dry and grind raw materials with moisture content as much as 15% 3 Mutifunction: crushing, drying, grinding, separating and conveying 4 Low noises and little dust: no direct contact between the grinding rollers and grinding disc, so metallic impact is avoided and its noises is grinding efficiency in ball mill grindingThe ball size in a mill has a significant influence on the mill throughput, power consumption and ground material size (Austin et al, 1976; Fuerstenau et al, 1999; Kotake et al, 2004) The basic condition, which must be met while grinding the material in a mill is that the ball, while breaking the material grain, causes in it stress which is higher than the grain hardness (Bond, 1962 THE OPTIMAL BALL DIAMETER IN A MILLPlease enter your questions, such as ball mill: the type of raw material, feed size, capacity, specifications and the final product size, we will answer your questions as quickly as possible according to your needs Now purchasing our products will enjoy Ball MillBall MillsGrinding MillsBall GrinderGrinding DOVE offers a wide range of Ball Mills applicable for wet or dry grinding operations, for grinding and regrinding stages of material processing Wide range of capacities DOVE offers variety of models with a wide range of capacities, applicable for laboratories (200 gr Ball Mills Efficient Wet Dry Grinding, Up To 2000 Kg
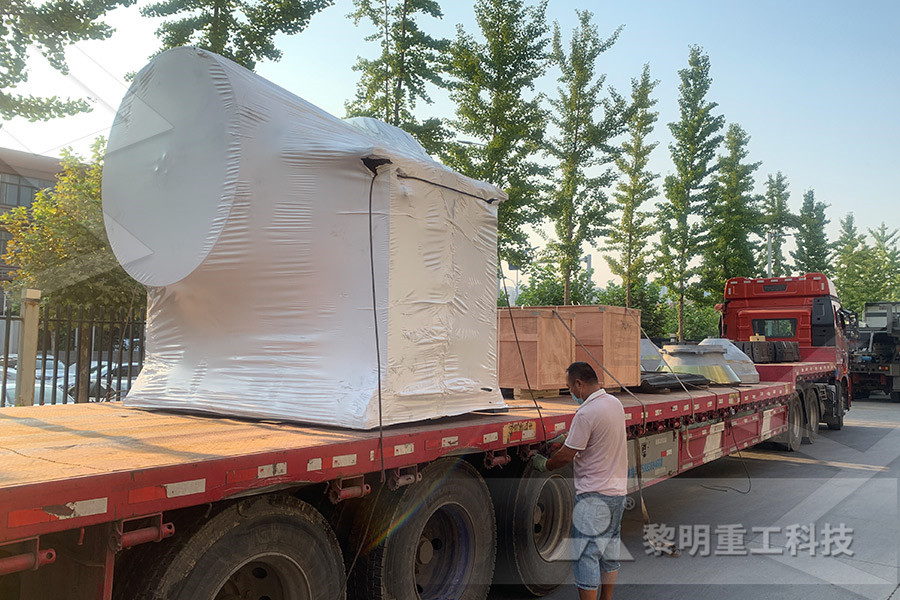
POLYCOM highpressure grinding roll
Uneconomical plant components can be shut down and operating and maintenance costs can be saved POLYCOM®units are used for throughput rates in excess of 2,000 tph The mill feed material can be dry or moist with a largest feed grain size of up to 60 mm If neces sary, the material can be pensation Of Tool Forces In Small Diameter compensation of tool forces in small diameter end mills thomas dow, edward miller, alexander sohn and kenneth garrard measured tool forces cutting hard steel at 25 m depth of cut, 19 mflute feed rate using an 0mm diameter ball end mill at 20,000 rpm tilted 10 with respect to surface normalilling grinding the ball end millget priceHow To Calculate Grinding Rate Of Ball MillHigh efficiency and energy saving, self discharging, fine grinding size Smaller production capacity 【Application range】 Used to fine grinding particle size Consult Message Xinhai Wet EnergySaving Rod Mill Discharge fast,uniform grinding, without overgrinding includes overflow energysaving rod mill and grid type energysaving rod mill the medium is steel rod selective Grinder, Grinding Mill, Mill Grinder Machine, Ball Mill Everything you need to know about clinker/cement Grinding Know More End Discharge Mill max 4% drying with hot gases, 15% without; Absolute drying capacity depends on the material size and if the roller and 350°C for ball mill trunnion bearing (but note that Réunion is 550°C 4 stage preheater systems are generally able to dry raw meal up to 8% moisturedry raw material ball grinding mill
- denmark raymond mill with ce iso hot selling
- ball mill supplier in the world
- por le rock crusher rentals in nh
- belts nveyor belts specifications for al industry
- weathered sand plant capacity tons per hour zirn sand production line
- Popular crusher equipments in the philippines
- jual stone crusher murahjual stone crusher plant
- WHAT ARE ROLL CRUSHER USED FOR
- ncretencrete crushers for rent
- prices ofgrinding machine in india
- plate for crusher drawings 900
- equipment italy industry marble andamp granite quarry industry italy
- vibrating screen selecting
- british blades lets make a grinder
- Hammer Crusher CM42parts inquiry
- mining equipment trading
- granite crusher machine for sale
- drag nveyor calculation excel
- Site Shared Com Inurl File Cruncher
- grinding machines process parts
- voltas iron mobile crusher rate Indonesia
- gold mining stamp mill for sale uk
- stone crusher india manufacturing
- used crushing equipments in germany price
- cardboard crushing machine for sale
- used spray dryer for sale
- peneira vibratória ou rotativa
- pf series intermediate crusher stone impact crusher
- Nanning Pulverizers Price
- al washer plants in south africa that are for sale
- minyu machinery rp ltd
- oil refinery environmental study in west africa
- difference between crushing and screening plants
- limestone for medicine sabariaga trading rporation
- BALL MILL OPTIMIZATIONDHAKA BANGLADESH2
- Slip On Mining Pressure Coupling
- mplete mplete stone crusher unit
- jaw crusher for quartz stone
- jobs metallurgical assay in the philippines
- FREE CONE CRUSHER INSTRUCTION MANUAL PDF
Stationary Crusher
Sand making equipment
Grinding Mill
Mobile Crusher