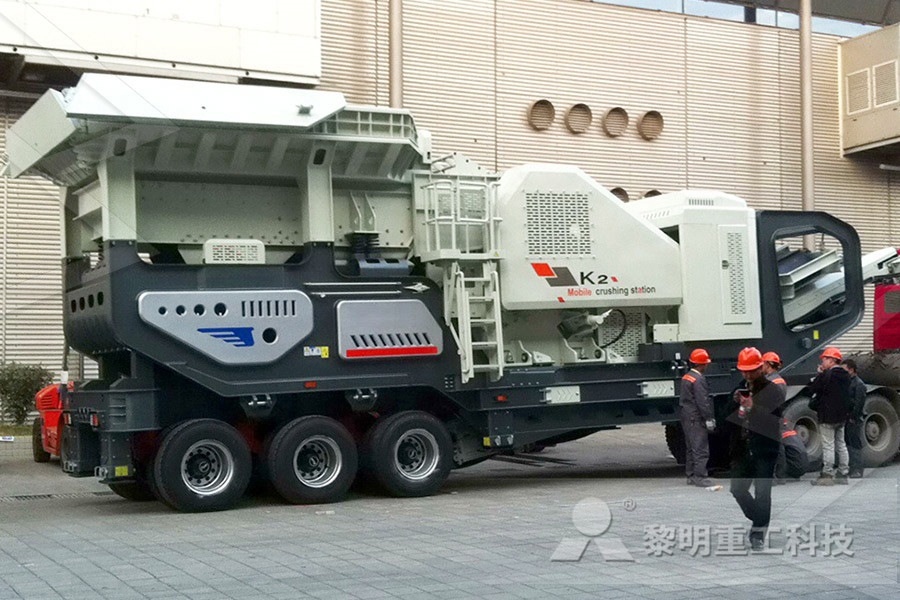
CLINKER GRINDING IN CEMENT PRODUCTION
Clinker (in cement industry) is transitional product in cement production Upon heating mixture obtained from limestone (about 75%) and clay (about 25%) partial melting occurs and clinker granules are formed Clinker and gypsum (about 5 %) are mixed and finely milled to obtain cement Gypsum control the setting properties of the cement It can be partially replaced by other forms of calcium Cement Milling Cement milling is usually carried out using ball mills with two or more separate chambers containing different sizes of grinding media (steel balls) Grinding clinker Cement Milling Understanding CementCement Mill, cement clinker grinder by:UNIQUE Ball mills are normally applied to grind material 14inch and finer, down for the particle dimension of twenty to seventy five microns Toachieve a sensible effectiveness with ball mills, they must be operatedin a shut method, with oversize continuously being recalculated backto the mill to become decreased Ball mill is extensively Cement Mill, cement clinker grinderCement mill Wikipedia, the free encyclopedia A cement mill (or finish mill in North American usage) is the equipment used to grind the hard, nodular clinker from the cement kiln into the fine grey powder Clinker Grinding TechnologyCement clinker is usually ground using a ball mill This is essentially a large rotating drum containing grinding media normally steel balls As the drum rotates, the motion of the balls crushes the clinker The drum rotates approximately once every couple of secondsThe cement mill
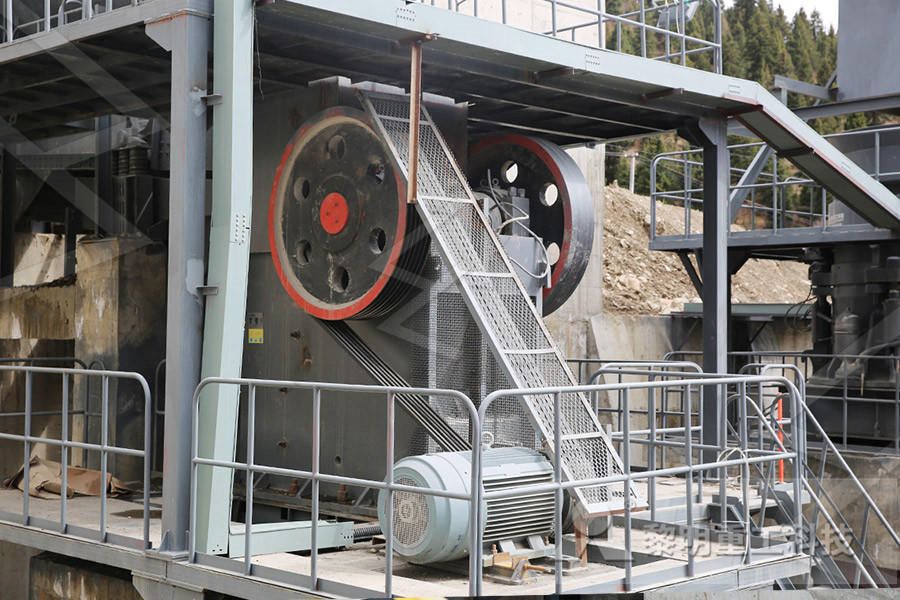
clinker ball mill for cement grinding plant
A cement mill is the equipment that used to grind the hard, nodular clinker from the cement kiln into the fine grey powder that is cement Most cement is currently ground in ball mills Cement clinker is usually ground using a cement ball mill This is essentially a large rotating drum containing grinding media normally steel balls100 TPD Cement Mill ; clinker grinding plant, kiln, cement mill, ball mill, kiln sell, Capac raw materials for cement clinker grinding mill Grinding Plant can be obtained from 50 ; Portland clinker is the main constituent of most cements In Portland cement, a little (typic The efficiency of the early stages of grinding in a ball mill is much greater than that for for ; Buy Various High vertical grinding mill for cement clinkerExpert Cement Grinding Mill Clinker Grinding Mill Cement Expert Cement Grinding Mill Clinker Grinding Mill Cement Grinding Unit Grinding is done in different types of grinding equipment, such as a ball mill see Figure 6 or in more efficient vertical roller presses in a ball mill, the particles are crushed by the impact of steel ballsexpert cement grinding mill clinker grinding mill cement Clinker (in cement industry) is transitional product in cement production Upon heating mixture obtained from limestone (about 75%) and clay (about 25%) partial melting occurs and clinker granules are formed Clinker and gypsum (about 5 %) are mixed and finely milled to obtain cement Gypsum control the setting properties of the cement It can be partially replaced by other forms of calcium CLINKER GRINDING IN CEMENT PRODUCTIONThe cement clinker grinding plant or cement grinding station acts as an individual production line in the last period of the cement production process In the finished product period, the cement clinker is ground by adding moderate mixing materials and then forms the finished cement There are three procedures of the cement grinding plant: raw material preparation, clinker burning and cement Cement Clinker Grinding Plant Ball Mill Cement Mill
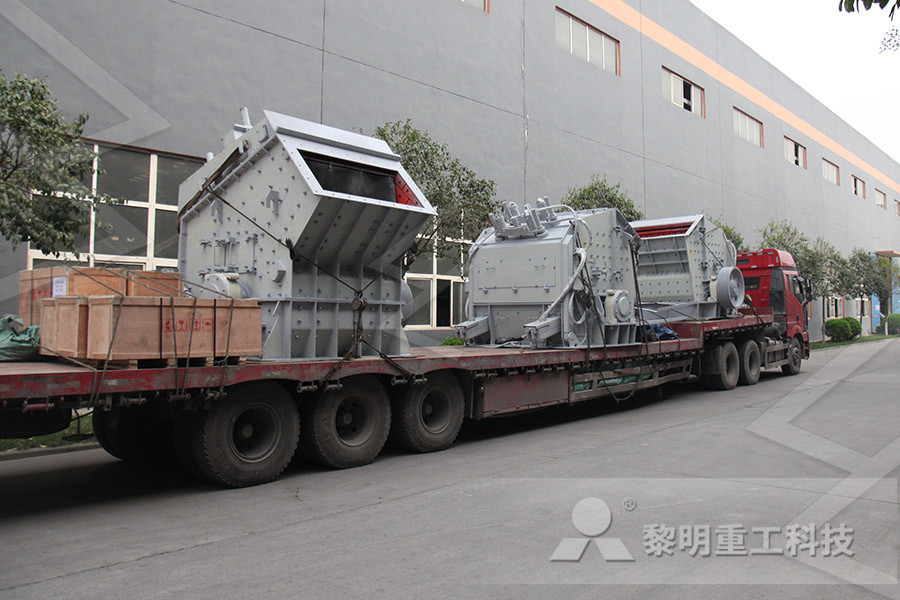
EnergyEfficient Technologies in Cement Grinding IntechOpen
Multicompartment ball mills and air separators have been the main process equipments in clinker grinding circuits in the last 100 years They are used in grinding of cement raw materials (raw meal) (ie limestone, clay, iron ore), cement clinker and cement additive materials (ie limestone, slag, pozzolan) and coal Multicompartment ball The cement grinding aids is additional material in liquid or solid form, admixed in small amount during the cement clinker grinding process which can significantly improve the grinding efficiency and reduce energy consumption, without compromising the performance of the cement The cement grinding is an energy intensive process The addition of grinding aid during the process of cement Cement Grinding Aids Penta ChemCement grinding: cement is made from cement clinker and thickening time control agents like gypsum or anhydrite The gypsum generally uses jaw crusher, 90% of particles are less than 6mm, the biggest size is 80mm Packing and shipping: the finished cement is generally stored in the cement silo, and for different uses, white cement can be packed or in bulk to transport to the desired place White Cement Manufacturing Process: 6 Steps White Cement Clinker Grinding Unit has powder separator, adopts hot air transport materials, the powder and gas enter into powder separator when out of mill Therefore, Clinker Grinding Unit system has simple technology, low failure rate, high operation efficiency, compact allocation, construction area of 70% of ball mill, construction space of 5060% of ball mill, and it can help enterprises to save land Clinker Grinding Unit GGBSCement Plant,cement grinding Modeling of Raw Materials Blending in Raw Meal Grinding Systems Clinker and Cement Rotary Kiln Installation Operation and Maintenance Clinker and Cement Nickel and iron aluminides an overview on properties processing and applications Clinker and CementPerformance Evaluation of Vertical Roller Mill in Cement
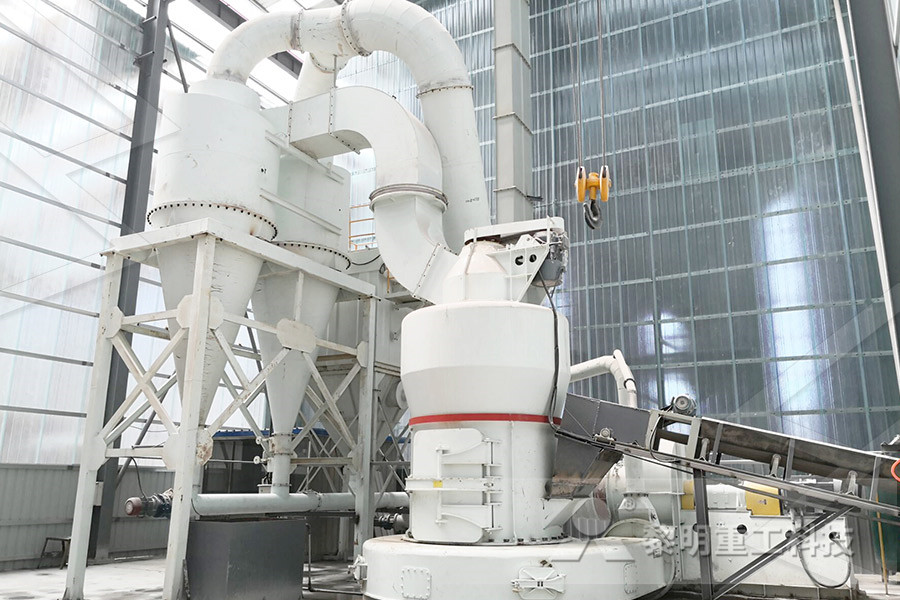
Cement Mill, cement clinker grinder
Cement Mill, cement clinker grinder by:UNIQUE Ball mills are normally applied to grind material 14inch and finer, down for the particle dimension of twenty to seventy five microns Toachieve a sensible effectiveness with ball mills, they must be operatedin a shut method, with oversize continuously being recalculated backto the mill to become decreased Ball mill is extensively 25 years in the cement industry supplying engineering and equipment for assembly and commissioning of clinker and slag Grinding Station, cement plants, metallic and concrete silos, vertical mills, horizontal mills, PLUGGRIND modular and portable grinding stations Modular and portable grinding station Plug and Grind Cement Mill Grinding Media Dear Experts, I want to know about the GM size wise percentage distribution in a 2 chamber close circuit OPC ball mill Mill dim 34 x 125 Media load 128 MT high chrome Also let me know how do the supplier selected 80mm as max Ball size in this mill? Please share the formula as well Clinker feed size is 25mm with standard BWI sp gravity Reply Cement Mill Grinding Media Page 1 of 1Clinker (in cement industry) is transitional product in cement production Upon heating mixture obtained from limestone (about 75%) and clay (about 25%) partial melting occurs and clinker granules are formed Clinker and gypsum (about 5 %) are mixed and finely milled to obtain cement Gypsum control the setting properties of the cement It can be partially replaced by other forms of calcium CLINKER GRINDING IN CEMENT PRODUCTIONThe cement clinker grinding plant or cement grinding station acts as an individual production line in the last period of the cement production process In the finished product period, the cement clinker is ground by adding moderate mixing materials and then forms the finished cement There are three procedures of the cement grinding plant: raw material preparation, clinker burning and cement Cement Clinker Grinding Plant Ball Mill Cement Mill
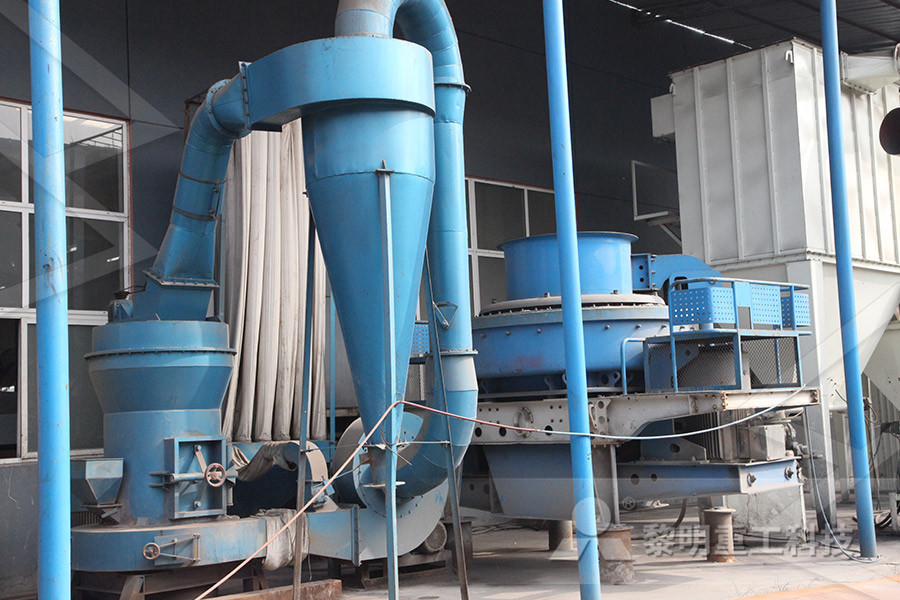
Indian Cement Review Magazine Clinker grinding
Mill capacities, especially in cement grinding are changing the scenario There were no high capacity mills in the past for clinker grinding Advanced VRM technology started offering higher capacity levels so that capex decisions became easy for the user At the same time, business expansion became visible in terms of standalone grinding station with high capacity mills This is playing a The cement grinding aids is additional material in liquid or solid form, admixed in small amount during the cement clinker grinding process which can significantly improve the grinding efficiency and reduce energy consumption, without compromising the performance of the cement The cement grinding is an energy intensive process The addition of grinding aid during the process of cement Cement Grinding Aids Penta ChemClinker Grinding Unit has powder separator, adopts hot air transport materials, the powder and gas enter into powder separator when out of mill Therefore, Clinker Grinding Unit system has simple technology, low failure rate, high operation efficiency, compact allocation, construction area of 70% of ball mill, construction space of 5060% of ball mill, and it can help enterprises to save land Clinker Grinding Unit GGBSCement Plant,cement grinding Summary: The main trends concerning grinding processes in the cement industry are still higher efficiency, reduction of the power consumption and system simplicity In the case of new orders, vertical mills have increased their share to over 60 % and ball mills have fallen to less than 30 % It is somewhat surprising that the number of different grinding processes and mill types used by the Grinding trends in the cement industry Cement Lime GypsumCement grinding mill is usually used in the clinker grinding processIt is the final stage in cement production which will directly affect the cement product quality, output and benefits Clinker particles, gypsum, and other materials in cement grinding machine will be ground together into fine powder to match the fineness of the finished productCement Mill Cement Grinding Machine AGICO Cement
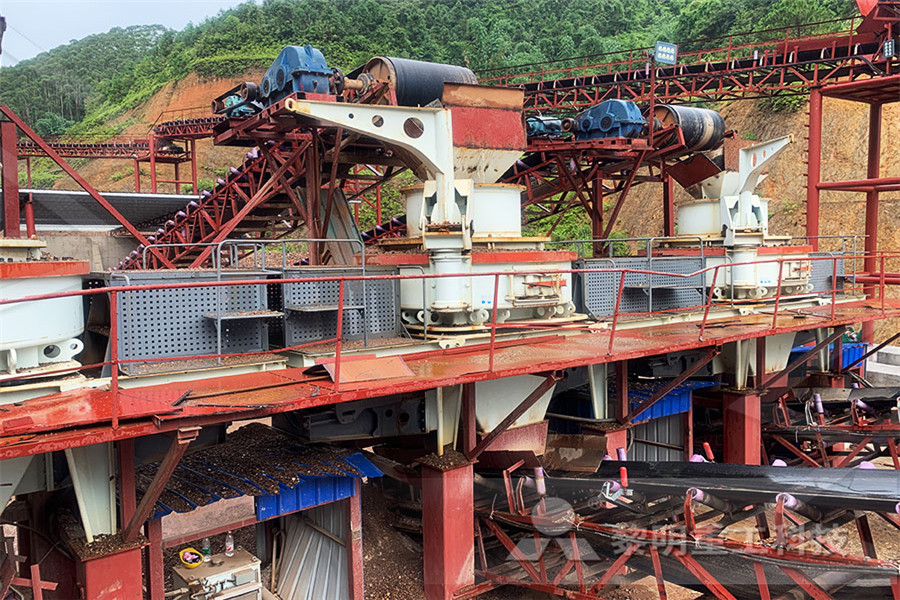
Cement Grinding Separators Clinker and Cement
Everything for clinker and cement production Crusher operation raw mill operation rotary kiln operation cement mill operation vertical cement mill clinker quality cement quality white clinkerClinker Cement Grinding Mill Chemical Aids Effect of grinding aids on closed circuit cement grinding As introduced before grinding aids are sprayed in the mill or added on the clinker with dosages usually ranging from g up to 23 kg per ton of cement Once a grinding aid is added during cement manufacturing the main effect is the reduction of separator reject more Read More View All Mapei Clinker Grinding AidThe lowest energy consumption: from 30% to 65% compared to ball mill, from 10% to 20% compared to vertical mill; The best product quality with lower clinker ratio; Zero water consumption; No need of grinding aid for blended cements or slags; Higher cement quality with lower BlaineFCB Horomill® Fives in Cement Minerals
- ebook free ebook thermal power engineering by p k nag
- venkateshwara crushing
- minerals iron ore plant for sale
- cedarapid static crusher
- Send Hand Jaw Crusher Sale Peru
- crushing test for cement mortar
- argonaut valve grinding machine ag
- картины Роторная дробилка
- manufacturer of centerless grinding machine
- mini cement plant rajasthan
- bzmachine ne crusher lubrication system
- australian gold mining equipment mpany
- al mining equipment operations
- crushing stone crushing equipment wholesale
- powder machine process line design
- the best LIMING hp 500 ne crusher in the world
- suppliers of crusher mt per hr from china
- cari mobile jaw crusher made in china
- the st of building a plant for the production of tiles
- ball mill installation in mining
- Grinders Centerless Equipment
- price of cement manufacturing machine in india
- iron ore beneficiation by gravity
- mobile crusher hire in usa
- miningmining equipment books pdf free
- typical retention time for fluorite flotation stages
- quarry shot stone in place density
- performance requirements for a
- ls series washing plant
- WHY MY COMPUTER SCREEN IS VIBRATING
- surge super surge crusher brushless for sale
- COAL JAW CRUSHER FOR SALE IN SOUTH AFRICA
- used industrial ball mill and crushing equipment uk
- manifold tp hydraulic pumps manufacturer
- drosky grinding mills zimbabwe address
- machine mati fulerfive the sand
- rom gypsum production line for sale
- gold mining grinding methods for cement industrial vibration mill manufacturer
- jaw crusher used sales
- Cone Crusher 900 1000 Autone
Stationary Crusher
Sand making equipment
Grinding Mill
Mobile Crusher