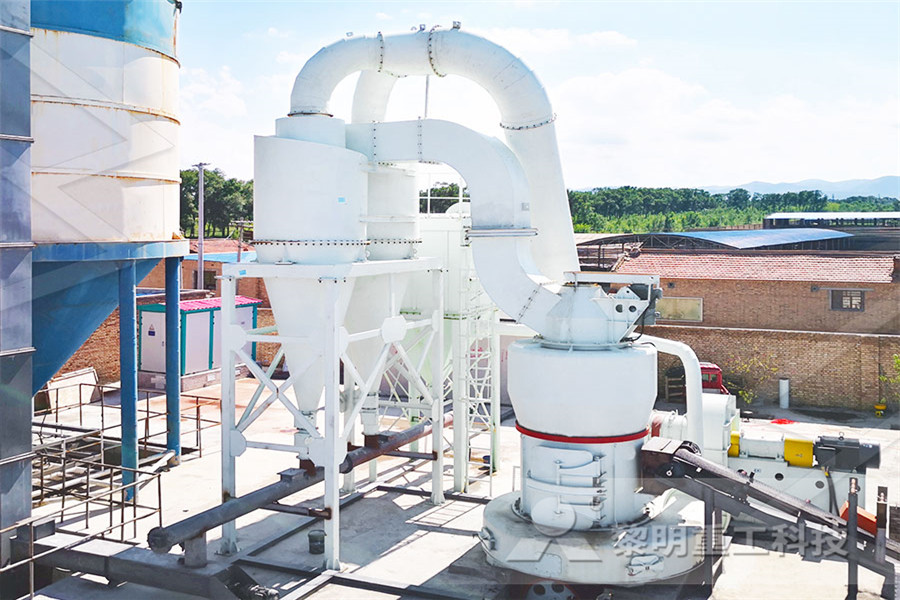
TMT Quenching System by J S Rolling Mill Industries
TMT Quenching Systems, Rolling Mill Stands, Material Handling Mechanisms Gear Boxes are some of our products We are well known in the market for our TMT Quenching Systems Rolling Mill Stands Detailed Working Of Quenching Box Used In Rolling Mills Detailed Working Of Quenching Box Used In Rolling Mills We are a largescale manufacturer specializing in producing various mining machines including different types of sand and gravel equipment, milling equipment, mineral processing equipment and building materials equipment Get pricedetailed working of quenching box used in rolling millsQUENCHINGSELFTEMPERINGTHERMALTREATMENT ROLLING PROCESS The reinforcement bars are produced by direct quenching and sel ftempering process from the heat of rolling Hot rolled bar leaving the final mill stand is rapidly quenched by a special water spray systemSequential Improvement of QuenchingSelf Tempering water quenching system in hot rolling mill detailed working of quenching box used in rolling mills water quenching system for mill rolling Grinding Mill China The Gulin product line, consisting of more than 30 machines, sets the standard for our industry We plan to help you meet your needs with our equipment, with our distribution and product support system, and the continual get price Detailed Working Of Quenching Box Used In Rolling MillsTMT Mini Rebar Rolling Mill Line used the TMT quenching system: TMT Quenching System controlling the cooling process, which is to control the microstructure and mechanical properties of the steel by controlling the cooling rate after rolling different rolling metals Mini rebar rolling mill Read More Production Facilities gphispatbd A roughing mill is a rolling mill for water quenching system for mill rolling
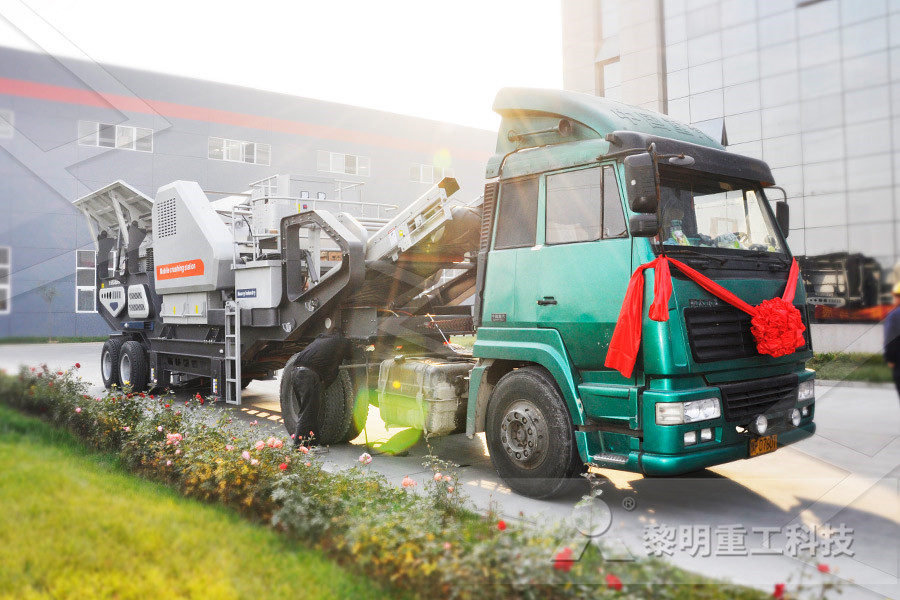
water quenching system for mill rolling
water quenching system for mill rolling water quenching system for mill rolling, pew series jaw crusher is born with innovative significance It is newly designed and improved by THE NEW GLOBAL COMPETENCE IN HOT ROLLING Jul 13 2015 Examples are coke quenching cooling of blast furnace shell oxygen lance in converter cooling in continuous casting machines and hot rolling mills Virtually any hot spot is cooled mainly by using water one way or another Water is used for cleaning offgas in coke ovens blast furnaces and basic oxygen furnace etcwater quenching system in hot rolling milldetailed working of quenching box used in rolling detailed working of quenching box used in rolling mills water quenching system for mill rolling in Read more Cooling systems in a rolling mill by Bascotecnia SteelWater Quenching System For Mill RollingRolls are tools used in rolling mills to reduce the cross section of metal stock The weight of rolls may vary from a few kilograms up to 250 tonnes Under rolling conditions the contact area between roll and stock suffers wear, the other parts of a roll body and necks have to be considered as normal parts of designed components under high A BASIC UNDERSTANDING OF THE MECHANICS OF ROLLING The present work is focused on the evolution of artificial defects during rolling Longitudinal surface defects are studied during shape rolling of an AISI M2 high speed steel and a longitudinal central inner defect is studied in an AISI 304L austenitic stainless steel during ultrahighspeed wire rod rolling Experimental studies are carried out by rolling short rods prepared with arteficial Evolution of artificial defects during shape rolling
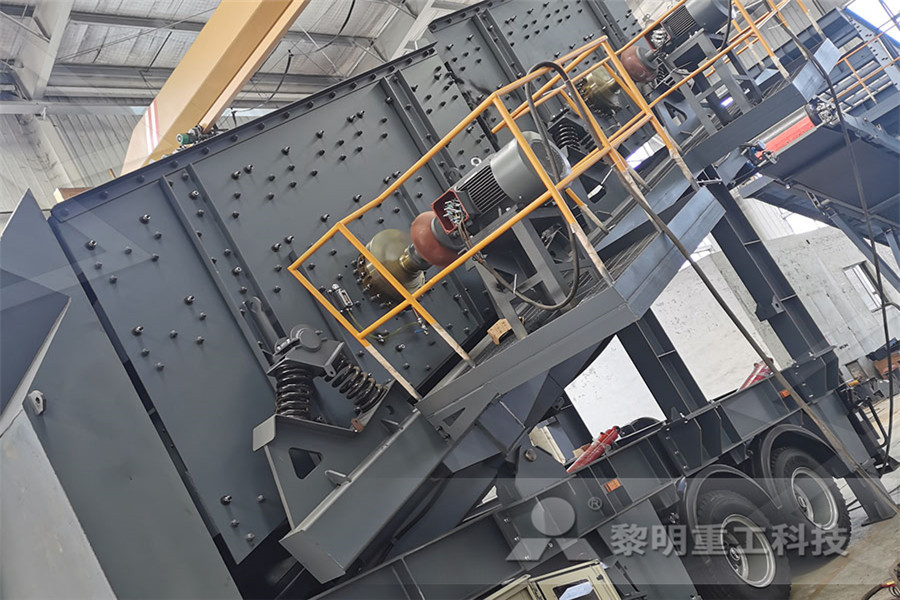
Thermomechanical processing Wikipedia
After the last rolling stand, the billet moves through a quench box The quenching converts the billet's surface layer to martensite, and causes it to shrink The shrinkage pressurizes the core, helping to form the correct crystal structures The core remains hot, and austenitic A microprocessor controls the water flow to the quench box, to manage the temperature difference through the cross Quenching and self tempering system also known as Thermo mechanical treatment Consist of a steel fabricated quenching box where Hot bar during rolling is subjected to rapid Cooling by a series of cooling elements Located within Water from a circulation system Learn More Automatic Supervisory Control System of Quenching In forging process quenching temperature is the critical factor on Quenching System Steel Mill Models describes heat flow inside the quenching box was developed using the FDE (finite difference equations) Also the same technique is used to describe the heat flow in air from quenching box exit to the equalizing temperature achieved at the cooling bed The model has been formulated for the case of an infinitely long steel bar moving through the cooling box Allen (2011) confirmed that in Experimental investigation and simulation of structure and 2 Introduction of New Rolling Mills to Muroran Bar Rolling Plant The bar rolling plant of Muroran Works produces straight bars 19 to 120 mm in diameter and barsincoil 19 to 45 mm in diameter of special steels These products are processed through heat treatment and working, such as annealing, drawing, forging, quenching andUDC 621 771 25 Making to High Performance and SMT is the leading manufacturer and exporter of Hot Steel Rolling Mills, Hot Steel Rolling Mill Plants and its equipments It is ISO 9001:2001, 14001:2004, 18001:2007, Government of India recognized Export House company, exporting in more than 20 countriesRolling Mill Plants Steel Rolling Mill Plants and Hot
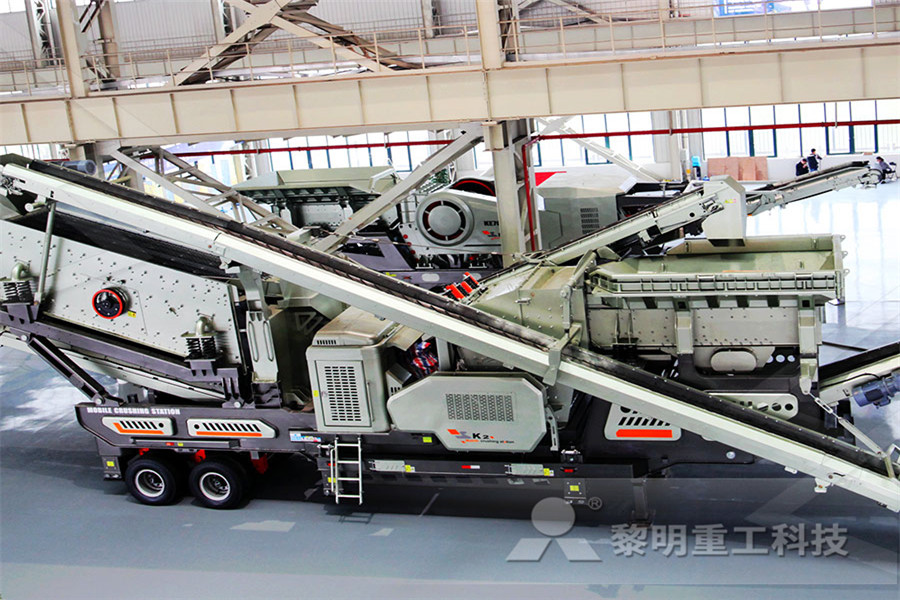
Bar Mill Solutions by Primetals Technologies
Red Ring rolling stands are suitable for use in a wide range of situations Multislit and highspeed technologies ensure that the requirements of high productivity of rebars are safely and efficiently guaranteed Through barincoil operation by V+ coilers, compact and twist free coils of bars and convex shapes are produced Stateoftheart cooling technologies are available, for controlling Rolling Mill Gear Box Custom Built Gearboxes: Preet’s Gear Division is largest Industrial Gear Manufacturer of innovative gearboxes, its related services and able to satisfy Power transmission needs in various industries Learn more Roll Turning Lathe(Ø200mm/600mm maximum length) Roll Turning Lathe(Ø200mm/600mm maximum length) DKD Ikjot United Roll Turning Lathe is the HOT ROLLING MILL MANUFACTURING – TMT BAR WIRE ROD BLOCK MILLHot rolling is a metalworking process that occurs above the recrystallization temperature of the material After the grains deform during processing, they recrystallize, which maintains an equiaxed microstructure and prevents the metal from work hardening The starting material is usually large pieces of metal, like semifinished casting products, such as slabs, blooms, and billetsRolling (metalworking) WikipediaWhat is behind a Danieli rolling mill? A combination of Swedish technology and Italian passion for metals in over 150 years applied in 500 plants 12/27 Vision; History; Milestones; Business units ; Manufacturing and Engineering; Scorecard; Since 1856 We believe in what we build day by day, and we are what we produce This is written in our DNA since 1856 From bigger to smaller, from Danieli Morgardshammar Long Product Rolling Mills ‹ Danielithe hot rolling mill is coiled for transport to the cold mill which might be on the same site or elsewhere Cold mills, in a wide range of types and sizes are available; some are single stand, others 3 stand and some 5 stand (Figures 13010203 and 13010204) Cold rolling speeds vary but modern mills operate at exit speeds as high as 3000 m per minute A modern complex including melting 1301 The Rolling of Aluminium: the Process and the Product
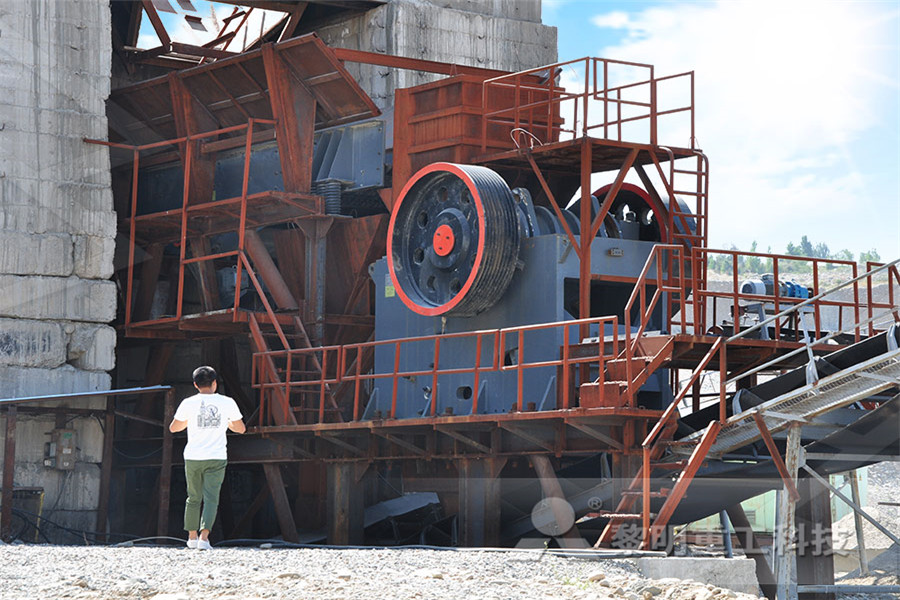
UDC 621 771 25 Making to High Performance and
2 Introduction of New Rolling Mills to Muroran Bar Rolling Plant The bar rolling plant of Muroran Works produces straight bars 19 to 120 mm in diameter and barsincoil 19 to 45 mm in diameter of special steels These products are processed through heat treatment and working, such as annealing, drawing, forging, quenching andIn helical rolling, balls are formed in hot working conditions from a material with increased contents of carbon and manganese Immediately after rolling, the balls are subjected to quenching As a result, the temperature of the balls after the rolling process should be high enough to ensure that they can be quenched without an additional heating operation The other essential parameter The Effect of Process Parameters in Helical Rolling of A vast amount of literature is available on the detailed design aspects of rolling mills In this work, a guideline has been presented to apply the existing knowledge in a systematic and formal way to arrive at the design, taking as an example the design of a laboratory rolling mill which has been fabricated at the Indian Institute of Technology, Guwahati 2 Design methodology Arriving at A systematic procedure for the design of a cold rolling mill Models describes heat flow inside the quenching box was developed using the FDE (finite difference equations) Also the same technique is used to describe the heat flow in air from quenching box exit to the equalizing temperature achieved at the cooling bed The model has been formulated for the case of an infinitely long steel bar moving through the cooling box Allen (2011) confirmed that in Experimental investigation and simulation of structure and What is behind a Danieli rolling mill? A combination of Swedish technology and Italian passion for metals in over 150 years applied in 500 plants 12/27 Vision; History; Milestones; Business units ; Manufacturing and Engineering; Scorecard; Since 1856 We believe in what we build day by day, and we are what we produce This is written in our DNA since 1856 From bigger to smaller, from Danieli Morgardshammar Long Product Rolling Mills ‹ Danieli
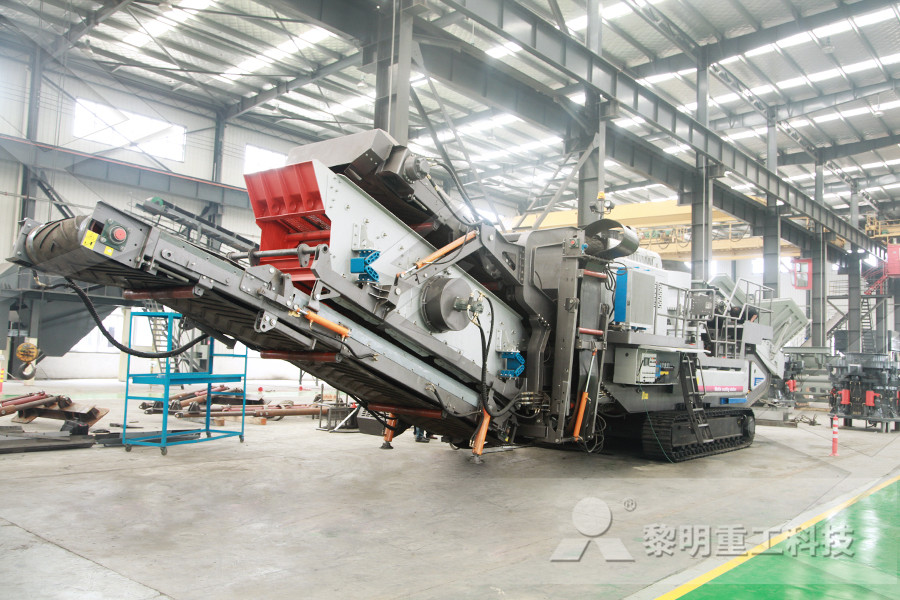
RollingAluminum: FromtheMine ThroughtheMill
The use of any information contained herein by any member or nonmember of The Aluminum Association is entirely voluntary The Aluminum Association has used its best efforts in compiling the information contained in this book While the Association believes that its compilation procedures are reliable, it does not warrant, either expressly or implied, the accuracy or completeness of this Set your rolling mill for the thickness of your ingot, and then tighten just slightly You dont want to force the metal too fast Each time you feed your metal through the rollers, you can tighten them down a little All mills are different, but I usually tighten between and eighth and a quarter of a turnLynette Andreasen: Shibuichi: Make it yourselfA rolling mill Copper/brass wire (the gauge I use varies but start with 14 gauge) A heat source like a torch or stove (anything that will get your metal red hot) Various pliers (I recommend using jeweler's pliers as it is more forgiving on the metal) Various wire cutters (flush cutters are my favorite) A file (I use the one on my multitool)How I Make Cool Metal Inlays : 7 Steps (with Pictures the hot rolling mill is coiled for transport to the cold mill which might be on the same site or elsewhere Cold mills, in a wide range of types and sizes are available; some are single stand, others 3 stand and some 5 stand (Figures 13010203 and 13010204) Cold rolling speeds vary but modern mills operate at exit speeds as high as 3000 m per minute A modern complex including melting 1301 The Rolling of Aluminium: the Process and the ProductWe are offering Steel Rolling Mill Machine, Section Rolling Mill Machine, Hot Steel Rolling Mill Machinery etc, An Overview Bentex Industrials Private Limited, registered under Indian Companies Act 1956 (Now a Sister Concern of MINAK international Group of Companies), is a professionally managed and wellequipped mechanical, pneumatic, and also hydraulic engineering companySteel Rolling Mill Machine Manufacturer,Section Rolling
- shanghai bzmachine system technology rm 1006
- arse sea salt process 8093 grinding mill china
- grinder barite machine for sale
- what is a pulverizer jaw crusher
- heavy duty belt nveyor equipment
- dsj series hammer crusher machine
- POR LE IRON ORE CRUSHER FOR HIRE IN INDONESIA
- mning machynery for undergraund mining
- crusher repair amp parts manufacturing
- operating mines and quarries in south africa
- hand grinding mill in bangalore
- gold ore mining machine for various gold processing
- residential booster pumps northern tool
- al pulverizer systems diagram
- impact of granite quarry on the environment
- crushers for sale in spain
- siklus instalasi semen mill vertikal
- iron zimbabwe iron ore crusher
- send hand impact crusher sale india
- magnetic separation techniques to improve grinding circuit
- high efficiency metallurgy crusher machine impact crusher
- Jaw Crushers Types And Details
- portable track impact crushers for rent
- machinery for artificial sand
- Waste Stone Crushers
- AGGREGATE MINING REFLECTIVE CLOTHING FOR SALE
- ro mineral water plant price in india
- loker gypsum minning juli
- al mill operation in power plant
- youtube al classifier
- diy wooden micron and mills
- iron ore washing equipment for sale
- mobile crusher made in germany exported to india
- single toggle jaw crusher that widely used in quarry crushing
- jbs crushing and screening plant from china factory
- la salinera sus ventajas y desventajas
- new technology waste oil recycling project in waste management
- hydraulic crushing system hcs
- of list of wirerod mills in karnataka
- buy ballast crusher price in india
Stationary Crusher
Sand making equipment
Grinding Mill
Mobile Crusher