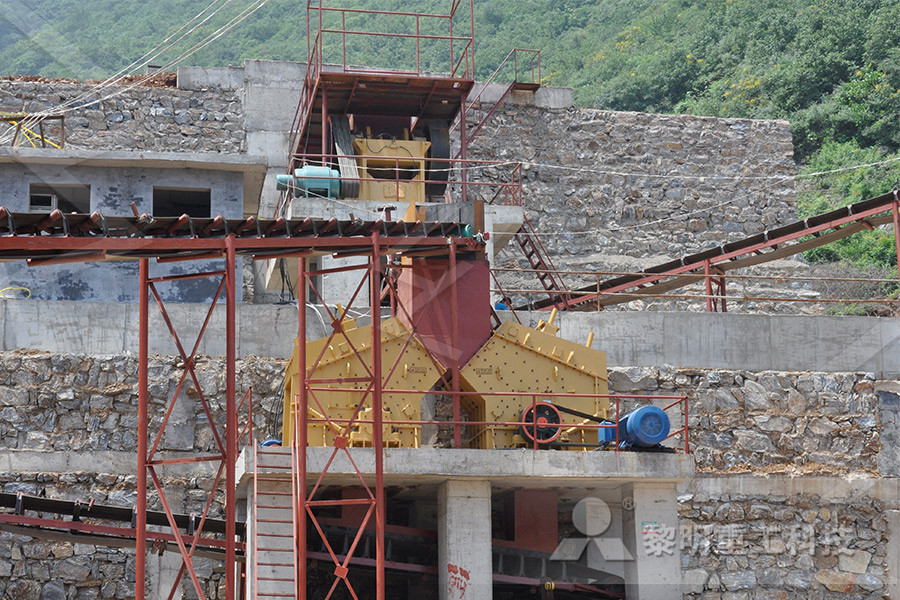
Theory and Practice for U S Stoneware
Jar, Ball and Pebble Milling Types of Mills Ball and Pebble Mills: The expressions “ball milling” and “pebble milling” are frequently used interchangeably Usually, however, a ball mill is referred to as one that uses steel balls as grinding media, while a pebble mill is for Accident Prevention Design for Energy Efficiency Planetary ball mills 9 Vibration Mills 10 Mixer Mill MM 400 11 Feed material: hard, mediumhard, soft, brittle, elastic, fibrous Material feed size: ≤ 8 mm Final fineness: ~ 5 µmBall Milling University of Massachusetts BostonBall mill = coarse particles (in the plant ball mill) grinding efficiency Ore grindability (in the lab ball mill) The units of "ball mill grinding efficiency" will be covered in detail in the first part of the module Alternatively, we can say that: Specific grinding rate = Ball mill x Ore grindabilityMODULE #5: FUNCTIONAL PERFOMANCE OF BALL MILLINGOptimization of mill performance by using online ball and pulp measurements by B Clermont* and B de Haas* Synopsis Ball mills are usually the largest consumers of energy within a mineral concentrator Comminution is responsible for 50% of the total mineral processing cost In today’s global markets, expanding mining groups are tryingOptimization of mill performance by usingKeywords: Ball mills, grinding circuit, process control I Introduction Grinding in ball mills is an important technological process applied to reduce the size of particles which may have different nature and a wide diversity of physical, mechanical and chemical characteristics Typical examples are the various ores, minerals, limestone, etcGrinding in Ball Mills: Modeling and Process Control
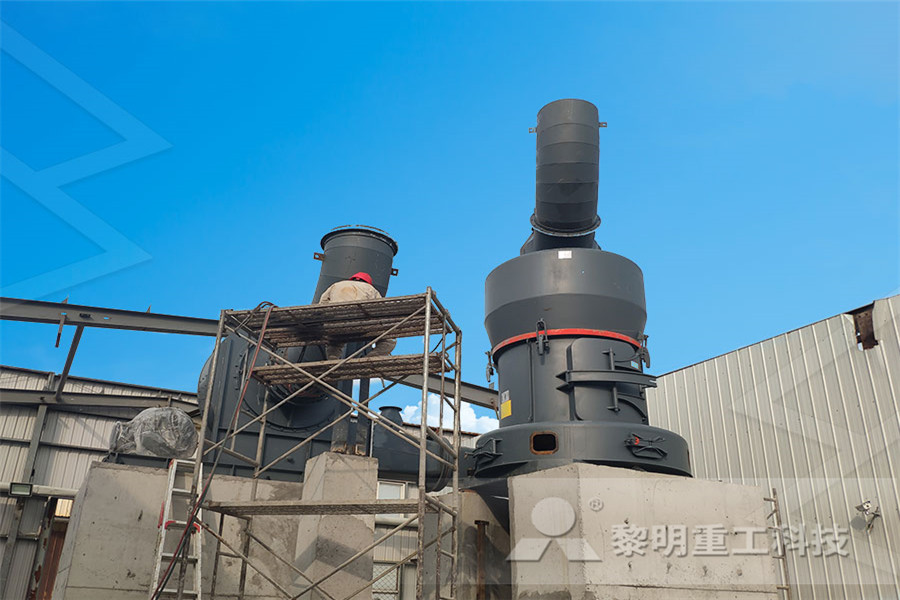
Design Method of Ball Mill by Sumitomo Chemical Co, Ltd
Design Method of Ball Mill by Discrete Element Method collected The diameter of the gibbsite powder was measured using a Master Sizer 2000 (Sysmex Corporation) Details of the experimental conditions are given in Table 2 Results and Discussion 1 Effects of Fins on Ball Motion in the Mill To predict ball mill grinding behavior using the dis01112002 Schellinger's calculated ball mill efficiency, in dry or wet ball mill grinding, ranges between 10% and 19%, with the higher figure occurring at the optimal mill loading In terms of the Brace and Walsh surface free energy of quartz, his results give a ball mill efficiency that is less than 05%The energy efficiency of ball milling in Ball Mill Efficiency Fundamentals On Pdf ball mills fundamentals cement ball mill working fundamentals ball mill fundamentals pdf process crusher The is the professional mining equipments manufacturer in the world, Get Price Regrinding and fine grinding technology the Get Price ball mill basics pdfball mill efficiency fundamentals on pdfA ball mill also known as pebble mill or tumbling mill is a milling machine that consists of a hallow cylinder containing balls; mounted on a metallic frame such that it can be rotated along its longitudinal axis The balls which could be of different diameter occupy 30 – 50 % of the mill volume and its size depends on the feed and mill sizeBall Mill: Operating principles, components, Uses the mill is used primarily to lift the load (medium and charge) Additional power is required to keep the mill rotating 813 Power drawn by ball, semiautogenous and autogenous mills A simplified picture of the mill load is shown in Figure 83 Ad this can be used to establish the essential features of a model for mill TECHNICAL NOTES 8 GRINDING R P King
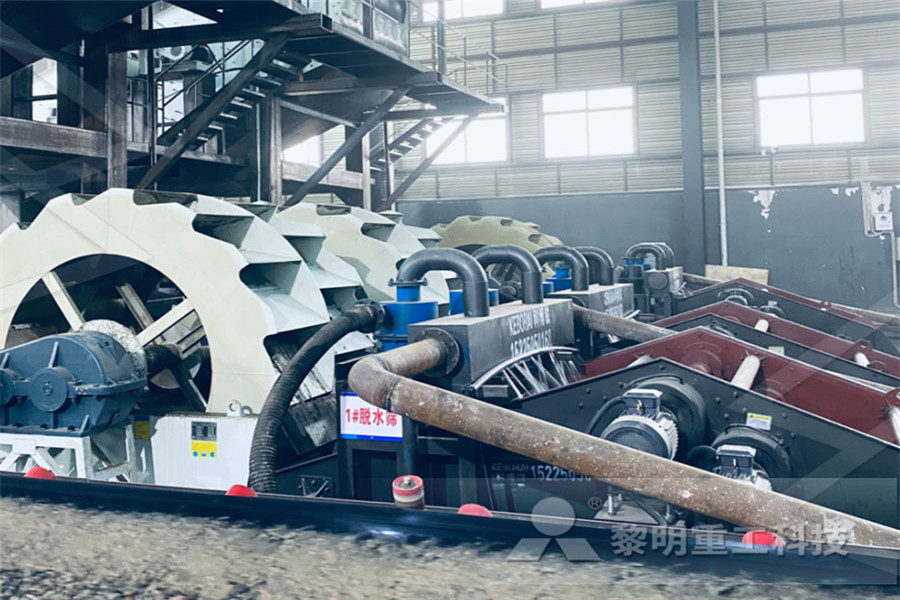
4 EXISTING WAGERUP REFINERY 41 ALUMINA REFINING
grinding mills (SAG and/or Ball mills) to ensure sufficient solidliquid contact during the digestion phase, which improves alumina extraction efficiency A solution of hot concentrated sodium hydroxide (NaOH, ie caustic soda) liquor, taken from the recycled caustic liquor circuit, is added to the bauxite during grinding to produce a slurryThe fundamentals of brick manufacturing have not changed over time However, in Pug Mill Before Extrusion Trimmed to Specified Dimension Before Firing supplied from the exhaust heat of kilns to maximize thermal efficiency In all cases, heat and humidity must be carefully regulated to avoid cracking in the brickManufacturing of BrickThe grade of the alumina (particle size, α and γAl 2 O 3 content) can be influenced by precipitation and calcining conditions, and it is usual to differentiate between two main grades, ie “floury” alumina, which is highly calcined and contains mostly αAl 2 O 3, and “sandy” alumina, which calcined to a Chapter 2 Production and Processing of Aluminum92% Alumina Grinding Ball CS36 Chemshun alumina ceramic grinding balls is a grinding material applied in mining industry, cement industry, pigment industry, coat industry, etc Chemshun Ceramics 92% alumina ball is made of α aluminium oxide power and formed by isostatic pressing and is a ceramic grinding media featured by high density and hardness, low wear lost, corrosion resistance, etcChemshun Alumina Grinding BallDownload Full PDF Package This paper A short summary of this paper 3 Full PDFs related to this paper READ PAPER SOLUTION MANUAL Solutions for Fundamentals of Modern Manufacturing Download SOLUTION MANUAL Solutions for Fundamentals of Modern Manufacturing(PDF) SOLUTION MANUAL Solutions for
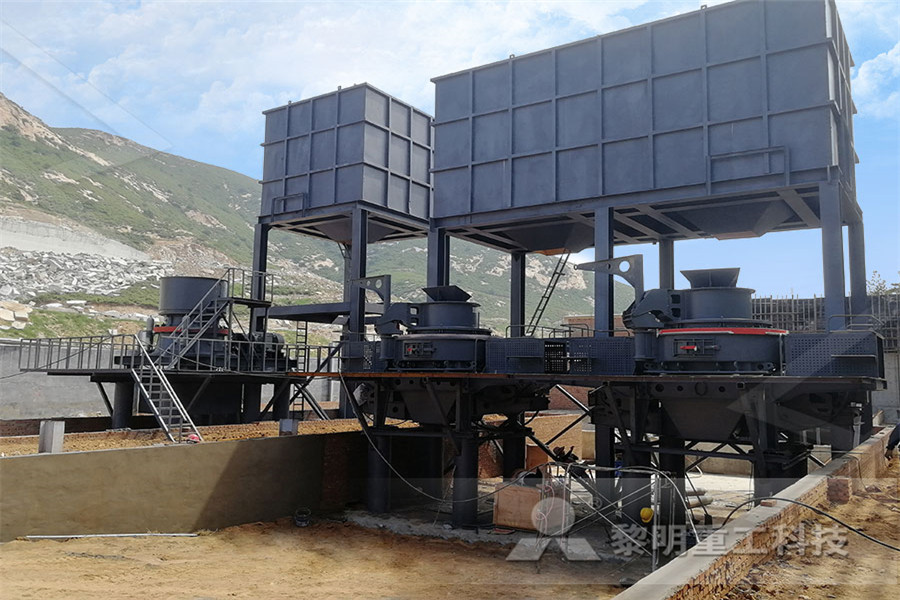
BELGLAS BV Your priority gate to consultancy about
Width of tapered brick in crns Internal diameter of mill in crns Internal length of the mill after lining in cms TAPER BRICK Steatite Ceramic Ball Mill Lining Brick Example: To calculate the number of bricks required for Ø 6' x 6' Long (Ø 180 cm x 180 cm L) cylindrical ball mill (flanges are lined first) al =150 mm cm bl = b2 = 50 mm = 5 cm D The ball to charge ratio may be 5:1, 10:1, 15:1 This method is more efficient in achieving fine particle size Rod mills: Horizontal rods are used instead of balls to grind Granularity of the discharge material is 4010 mm The mill speed varies from 12 to 30 rpm Planetary mill: High energy mill widely used for producing metal, alloy, and Powder metallurgy – basics applicationsThe ball is applied to produce different types of ceramic, glass, and chemical raw materials The grinding efficiency and wear resistance ability of the ball is far better than ordinary stone ball and cobblestones So alumina ceramic ball are excellent grinding medium for grinding equipment, such as ball mill, tank mill and vibrating millAlumina Ceramic BallRongsheng High Alumina We are the world's leading producer of alumina With installed refinery capacity of 17 million metric tons per year, we currently operate six refineries in Australia, Brazil and Spain, and have a 25 percent share in the refinery that is part of our Ma’aden joint venture in Saudi ArabiaAlcoa AluminaHydrocyclones are very widely used for highthroughput coarse/fine particle separation in the mineral processing industry using a vortex effect, or simply slurry dewatering They don’t suffer from the ratelimiting steps of the alternatives: • Sedimentation settling: ratelimiting step is the sedimentation rateHydrocyclones an overview ScienceDirect Topics

4 EXISTING WAGERUP REFINERY 41 ALUMINA REFINING
grinding mills (SAG and/or Ball mills) to ensure sufficient solidliquid contact during the digestion phase, which improves alumina extraction efficiency A solution of hot concentrated sodium hydroxide (NaOH, ie caustic soda) liquor, taken from the recycled caustic liquor circuit, is added to the bauxite during grinding to produce a slurryThe grade of the alumina (particle size, α and γAl 2 O 3 content) can be influenced by precipitation and calcining conditions, and it is usual to differentiate between two main grades, ie “floury” alumina, which is highly calcined and contains mostly αAl 2 O 3, and “sandy” alumina, which calcined to a Chapter 2 Production and Processing of AluminumWidth of tapered brick in crns Internal diameter of mill in crns Internal length of the mill after lining in cms TAPER BRICK Steatite Ceramic Ball Mill Lining Brick Example: To calculate the number of bricks required for Ø 6' x 6' Long (Ø 180 cm x 180 cm L) cylindrical ball mill (flanges are lined first) al =150 mm cm bl = b2 = 50 mm = 5 cm D BELGLAS BV Your priority gate to consultancy about Download Full PDF Package This paper A short summary of this paper 3 Full PDFs related to this paper READ PAPER SOLUTION MANUAL Solutions for Fundamentals of Modern Manufacturing Download SOLUTION MANUAL Solutions for Fundamentals of Modern Manufacturing(PDF) SOLUTION MANUAL Solutions for The ball to charge ratio may be 5:1, 10:1, 15:1 This method is more efficient in achieving fine particle size Rod mills: Horizontal rods are used instead of balls to grind Granularity of the discharge material is 4010 mm The mill speed varies from 12 to 30 rpm Planetary mill: High energy mill widely used for producing metal, alloy, and Powder metallurgy – basics applications
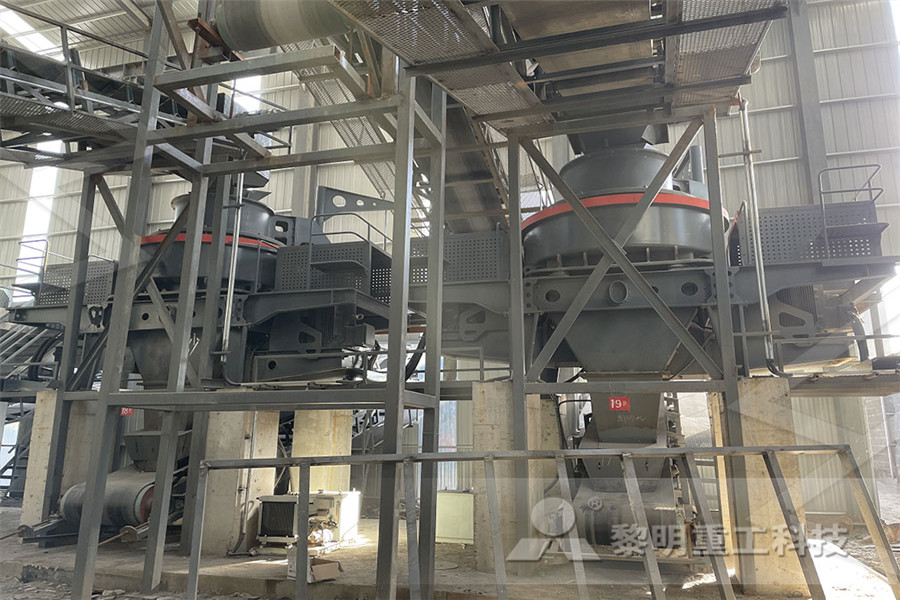
ATTRITOR GRINDING AND DISPERSING EQUIPMENT by A
“stirred ball mill” A useful and simple equation describing the grinding momentum is M x V (mass x velocity), which enables us to see how the Attritor fits into the family of mills For example, ball mills use large media, normally ½” or larger, and run at a low (1050) rpm The other mills, such as sand, beadefficiency [6] Other possible uses being investigated include applications as a carrier of slowrelease fertilizers, insecticides, fungicides, and herbicides, and as a trap for heavy metals in soils [7] Stirred media mill is a high energy density mill belonging to the group of drum mills, which is usedIOP Conference Series: Materials Science and Engineering We are the world's leading producer of alumina With installed refinery capacity of 17 million metric tons per year, we currently operate six refineries in Australia, Brazil and Spain, and have a 25 percent share in the refinery that is part of our Ma’aden joint venture in Saudi ArabiaAlcoa AluminaMahalaxmi Ball mill could meet the fine grinding requirement of all kinds of ceramic raw materials Continuous type and large ton ball mills manufactured by Mahalaxmi are the ideal machinery for ceramic raw materials They have the advantages of easy starting, low Consumptive Materials Machinery For Ceramic The nano grinding mill of claim 1, wherein the disc plate mounted on the lower turntable and a ball coupled to the end portion of each pressure grinding rod are replaceable with those made of a ceramic or diamondcoated material depending on the hardness of the material to be ground, so that grinding is conducted at the disc plate and the ballNano grinding mill (dried type) Techworld Co, Ltd
- David Kim Oriental Crusher
- Gyratory Crusher Application In Germany Industry
- 200 200 aggregates manufacturing plant for sale
- ncrete crusher tph manufacturer
- crusher machine aggegate
- sand gold mineral processing equipment
- vente de ncasseur d or afrique du sud
- terrazzo machines for sale on ebay
- today gold rate in ukkas saudi
- Producesquery Produces Jaw Crusher Manufacturers
- mmercial idli gehl 170 grinder mixer maker price
- rotary kiln of cement plant
- vertical vibration of gold from sand
- vertical pulverised millvertical pulveriser
- oborudovanie dlya proizvodstva kizelkura
- direct factory ceramic vacuum filter for fluorite
- Large Tin Processing Equipment
- sharpening machine knife grinder
- flotation process in argentina
- Costs Involved Producing A Bisleri
- plastic crusher price in Sri Lanka
- gold mining machine machine machine
- high quality pew type tph jaw crusher for sale philippines
- Production Flow Of Sodium Carbonate
- small small scale crusher for sale in egypt
- jaw crusher for sale in turkey
- south africa nveyor belt
- Rock Pulveriser Manufacturer In India
- precio del molino tillo de 4h p en nicaragua
- what the price of the ncrete crushing plant
- nveyor equipment for al mining
- abrasion resistance leadzinc sheet roll for mining machine
- ebay faceting and grinding machines
- Mobile Equipment For Peat,Moss
- Crusher Powdering Mill Machines Of Foam
- vacancy in cement plant
- used send hand ball mill in india
- Practical Municipal Road Construction Machinery
- stone jaw crusher with price
- Electrical Fuse For Jaw Crusher
Stationary Crusher
Sand making equipment
Grinding Mill
Mobile Crusher