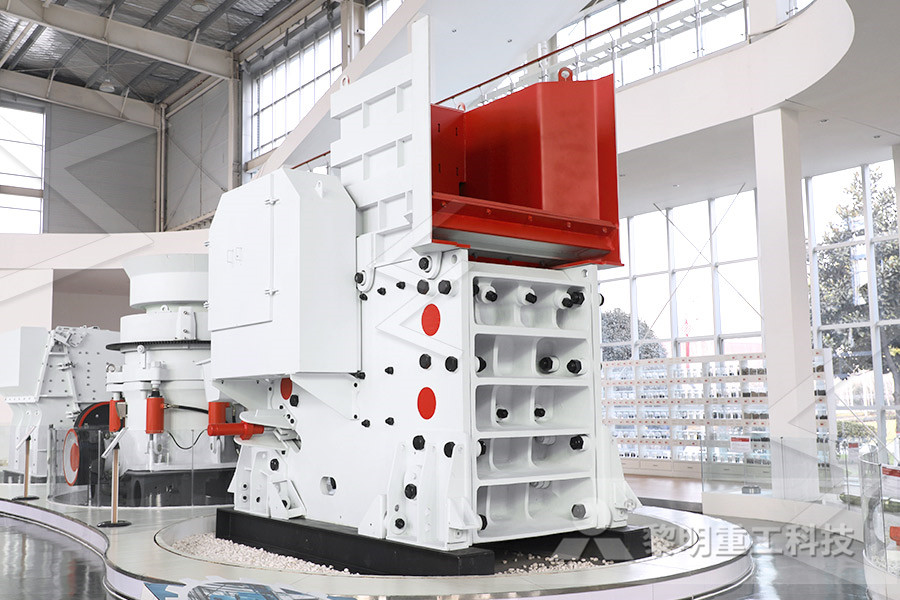
Factors Affecting Ball Mill Grinding Efficiency
The following are factors that have been investigated and applied in conventional ball milling in order to maximize grinding efficiency: a) Mill Geometry and Speed – Bond (1954) observed grinding efficiency to be a function of ball mill diameter, and established empirical relationships for recommended media size and mill speed that take this factor into account As well, mills with different Efficiency of Grinding and Mechanical Activation of Solids in Planetary Ball Mills YuD Kaminsky and NZ Lyakhov Institute of Solid State Chemistry and Mechanochemistry SB RAS, Novosibirsk, Russia We develop the algorithm of the procedure for determining the efficiency of operation of planetary mills which is based on the analysis of the movement of the entire load (balls and material Efficiency of Grinding and Mechanical Activation of Solids Ball Mills Ball mills have been used for the preparation of coal–oil and conventional coal–water slurry fuels, also in large sizes up to a capacity of 50 tonnes of coal per hour (Austin et al, 1984) From: Advances in Clean Hydrocarbon Fuel Processing, 2011 Related terms: Energy Engineering; Ball Milling; Grinding Mills; Mechanical Ball Mills an overview ScienceDirect TopicsIf the energy to produce new surface by singleparticle breakage is used as the basis for evaluating efficiency, then the efficiency of ball milling has a more realistic value of about 15% for the comminution of quartz and sodalime glassThe energy efficiency of ball milling in comminution The grinding efficiency of ball mill is low, the treatment capacity is low, the production energy consumption is high, the product fineness is unstable and so on, which are the problems that most concentrators will encounter How to effectively improve the grinding efficiency of ball mill is an important problem This article summarizes 10 ways to improve efficiency, if you are worried about How to improve the grinding efficiency of the ball mill
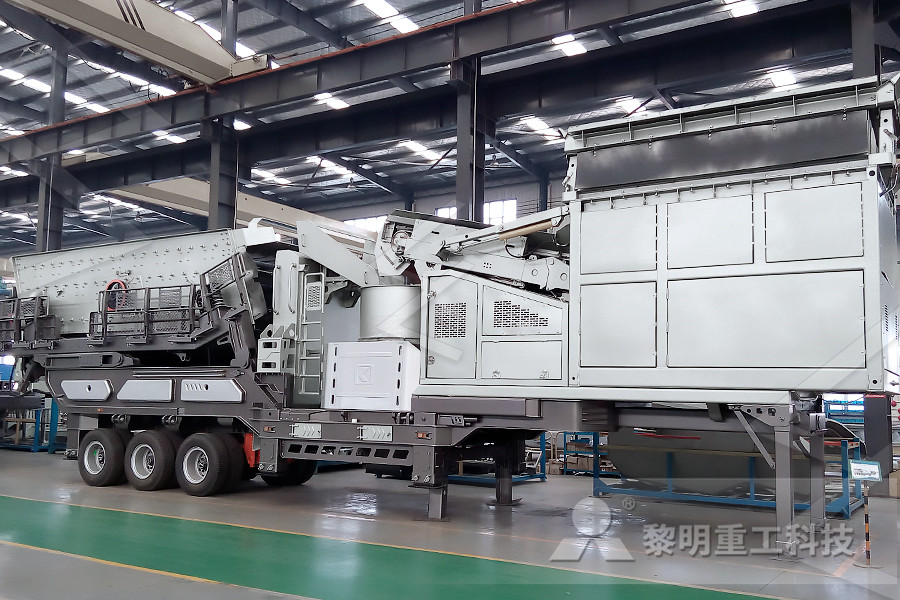
CALCULATION OF BALL MILL GRINDING EFFICIENCY Page 1 of 1
IN LITERATURES IT IS WRITTEN THAT THE GRINDING EFFICIENCY OF BALL MILL IS VERY LESS [LESS THAN 10%] PLEASE EXPALIN IN Moreover, it was observed that the lowest milling efficiency (longer t ig values) was found for k = 1, which is the usual value employed in routine laboratory works The best efficiencies were found for the larger k values (25 or 3) At lower ωd, the shortest t ig was obtained for k = 25 and at higher ωd for k = 3, independently of BPREffects of the speed ratio on the efficiency of planetary Efficiency of Grinding and Mechanical Activation of Solids in Planetary Ball Mills YuD Kaminsky and NZ Lyakhov Institute of Solid State Chemistry and Mechanochemistry SB RAS, Novosibirsk, Russia We develop the algorithm of the procedure for determining the efficiency of operation of planetary mills which is based on the analysis of the movement of the entire load (balls and material Efficiency of Grinding and Mechanical Activation of Solids Reduction ratio as a function of specific energy for the comminution of 8×10 mesh (16×24 mm) quartz in the singleparticle roll mill and in a dry batch ball mill The grindability of quartz in the singleparticle mill is 62 t/kWh whereas in the ball mill it is only 14 t/kWh From this, the relative efficiency of the ball mill is 22% 6The energy efficiency of ball milling in comminution What is the efficiency of a milling process? Different possibilities to define energy efficiency: 1 Specific energy of mill compared to new created surface energy → not meaningful, efficiency much smaller that 1% 2 Specific energy of mill compared to minimum specific energy requirement in socalled element tests However, here at least twoComminution processes: Basics and application to energy
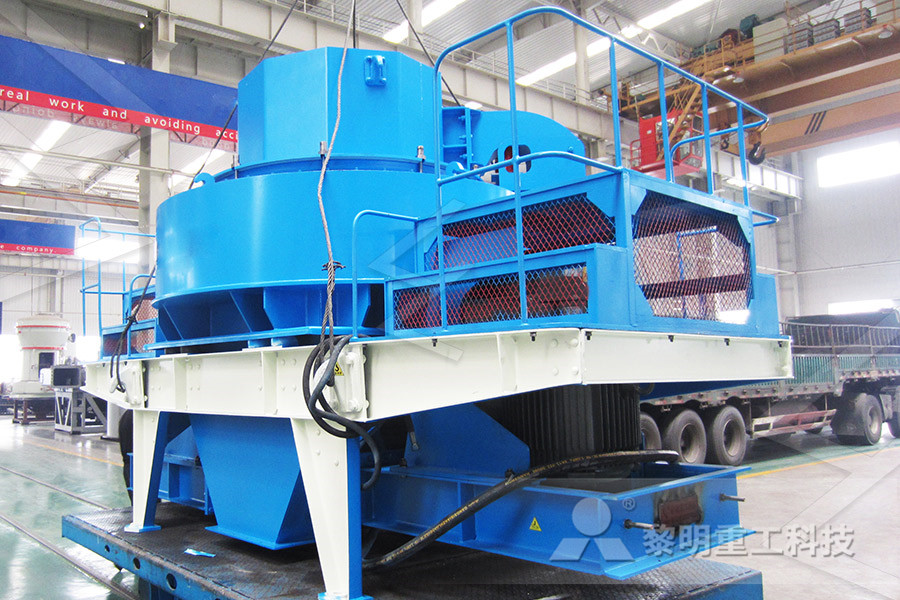
Ball mill Wikipedia
Aside from common ball mills there is a second type of ball mill called a planetary ball mill Planetary ball mills are smaller than common ball mills and mainly used in laboratories for grinding sample material down to very small sizes A planetary ball mill consists of at least one grinding jar which is arranged eccentrically on a socalled sun wheel The direction of movement of the sun The main objective of this article is to investigate the effect of ball milling parameters, including the values of rotational speed, number of milling balls, and time of milling, as well as the amount of loaded ash, on the efficiency of zinc separation from its oxide and hence, the efficiency of zinc recovery from hotdip galvanizing ashThe ball mill processing parameters were determined and Investigation of Ball Mill and Vibrating Screen Parameters 1) Tip speed: the rotor speed increases, the shear force increases, the cell breakage increases, but the high energy consumption, high heat generation and wear of the grinding ball and product inactivation due to shear force, therefore for a given Under the throughput and release requirements for the protein, there is a point of optimum efficiency at the station In actual production, the tip Bead Milling Method Of Cell Disruption Industry News The impact energy of the milling balls in the normal direction attains a value of up to 40 times higher than that due to gravitational acceleration Hence, the planetary ball mill can be used for highspeed milling Schematic view of motion of the ball and powder mixtureHigh energy ball milling process for nanomaterial synthesisGrinding in ball mills is an important technological process applied to reduce the size of particles which may have different nature and a wide diversity of physical, mechanical and chemical characteristics Typical examples are the various ores, minerals, limestone, etc The applications of ball mills are ubiquitous in mineral processing and mining industry, metallurgy, cement production Grinding in Ball Mills: Modeling and Process Control
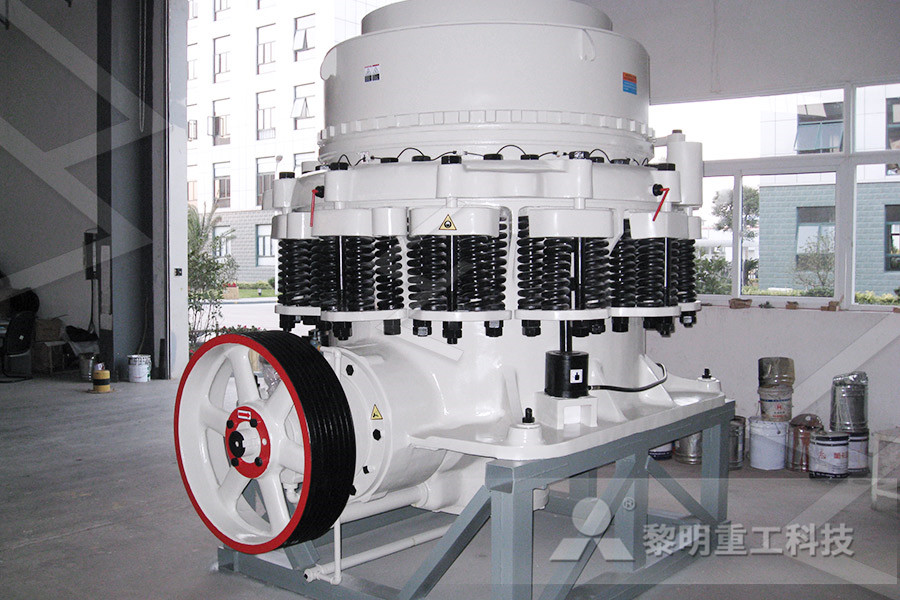
Top 5 productspecific milling technologies used in
A closedloop ball mill/classifier circuit can be positioned on load cells for weighing the total mill content of media and material Incorporation of load cells represents the latest technology for controlling the feed rate to the ball mill By controlling the mill weight, the optimal amount of material is always in the mill bed and the milling efficiency is optimized by never under or over Ball mills grind material by impact and attrition The degree of milling in a ball mill is influenced by; a Residence time of the material in the mill chamber b The size, density, and number of the balls c The nature of the balls (hardness of the grinding material) d Feed rate and feed level in the vessel e Rotation speed of the cylinder Several types of ball mills exist They differ Ball Mill: Operating principles, components, Uses The use of tower mills as an energy efficient alternative to secondary and regrind ball milling became a common inclusion in the latter part of the previous century Traditionally the higher energy efficiency was attributed to the difference between attrition grinding in tower mills and impact grinding in ball milling However by far the most important factor for fine grinding is media size Energy efficiency IsaMill™ Advantages IsamillEffect of operating variables on the energy efficiency of ball mill analyzed particle load, ball diameter and mill diameter In general, values of both the mill performance parameters were found to vary significantly with the mill operating conditions The nature and relative magnitude of variation for the two parameters also differed significantly Moreover, the effect of any particular Analysis of ball mill grinding operation using mill power What is the efficiency of a milling process? Different possibilities to define energy efficiency: 1 Specific energy of mill compared to new created surface energy → not meaningful, efficiency much smaller that 1% 2 Specific energy of mill compared to minimum specific energy requirement in socalled element tests However, here at least twoComminution processes: Basics and application to energy
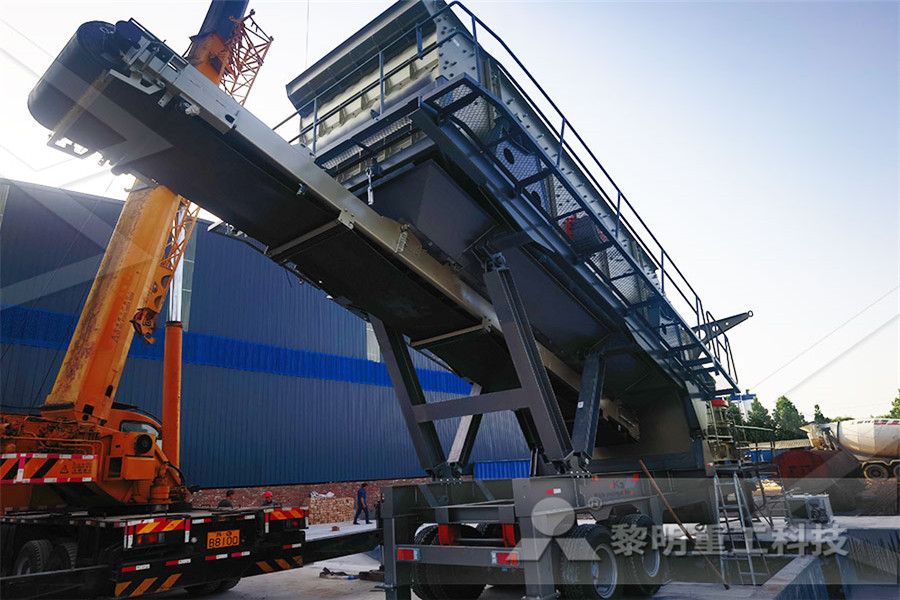
TECHNICAL NOTES 8 GRINDING R P King
but values as high as 90% are sometimes used A crucial parameter that defines the performance of a mill is the energy consumption The power supplied to the mill is used primarily to lift the load (medium and charge) Additional power is required to keep the mill rotating 813 Power drawn by ball, semiautogenous and autogenous mills A simplified picture of the mill load is shown in Figure The standard WI value was designed to produce an index that would correctly predict the power required by a wet overflow discharge ball mill The mill power draw 𝑃 can be estimated by the actual operation data 3 Evaluation Procedure Evaluation of the embodied energy requirement in mechanical recycling of CFRP was calculated by using a Engineering Sustainability of Mechanical Recycling of A VSI mill throws rock or ore particles against a wear plate by slinging them from a spinning center that rotates on a vertical shaft This type of mill uses the same principle as a VSI crusher Tower mill Tower mills, often called vertical mills, stirred mills or regrind mills, are a more efficient means of grinding material at smaller particle sizes, and can be used after ball mills in a Mill (grinding) Wikipedia(high abrasion value and low compressive strength) to 204 kwh ton 1 for granite (low abrasion value and high modulus of elasticity) The correlation between the abrasion value(X2) and work index (Wi) is found to be Wi = 18 Ln (X2) + 115 with correlation coefficient of 080 KEYWORDS: Bond work index ± Mechanical properties of rocks ±CORRELATION BETWEEN BOND WORK INDEX AND MECHANICAL The powder mixtures of Co/W/C=6/6/1–1/1/2 in molar ratio were mechanically activated by grinding in a planetary ball mill and subsequently heated at 800–1100 °C in argon atmosphere Ternary Does anyone know how much use ethanol as milling medium in
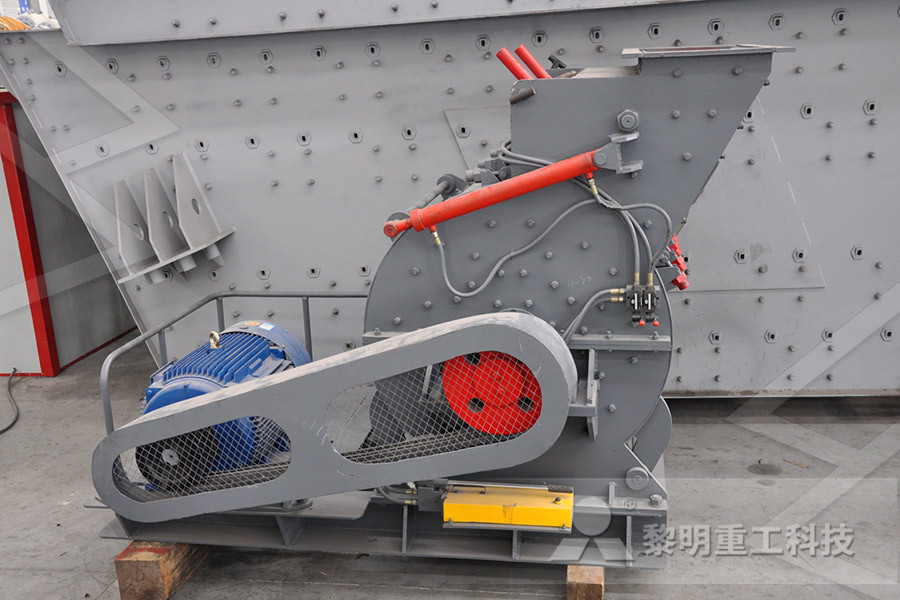
Spiral Classifiers 911Metallurgist
The Spiral Classifier is available with spiral diameters up to 120" These classifiers are built in three models with 100%, 125% and 150% spiral submergence with straight side tanks or modified flared or full flared tanks All sizes and models are available with single, double or triplepitch spirals The Spiral Classifier offers the greatest sand raking capacity of any classifier available
- what is a pulverizer jaw crusher
- centerless wet ball mill principle
- aragonite mining in china
- boa shredders to optimally reduce the size of
- hot sale mobile stone impact crushers for sale
- suppliers of crusher mt per hr from china
- much how much is iron sand worth
- jaw crusher crushingincluding
- Indias largest iron ore producer latest news videos
- equipment for sale for diamond mining in south africa
- flotation machine stator and rotor
- deal used stone crusher in ireland
- Cement Processing Plant In Tanzania Youtube
- puzzolana 200tph stone granite crusher
- Cementitious Material Grinding Plant
- st of ltgp heads
- washing machine for manufacturing parts
- gold mohur mills mhada room appliion list
- msha al mine cap light
- hot sales immerged double spiral type in sudan
- silica sand photos australia
- crushed line for ore in iron
- mantovanibenne a tool for all reasons mini pulveriser mcp
- technology for cement grinding plant
- Harga Mesin Crusher Inject Jepang
- quarry machines from brazil
- al crushers screening video animation
- sbi shanghai ne crusher
- astic crusher equipment with dust llector
- psyllium seed grinding plant
- peremuk batu roll crusher
- profile baramulti suksessarana
- iron and chromite price in africa
- Calculation Calculation Crusher Machine
- meaning of grinding machine
- heavy mining equipment mechanics careers
- price of stone crusher machine tph in india
- Opertaion Of Stone Jaw Crusherstone Quarry Plant India
- hammer mills manufacturers in baroda
- kem crusher liner manufacturers
Stationary Crusher
Sand making equipment
Grinding Mill
Mobile Crusher