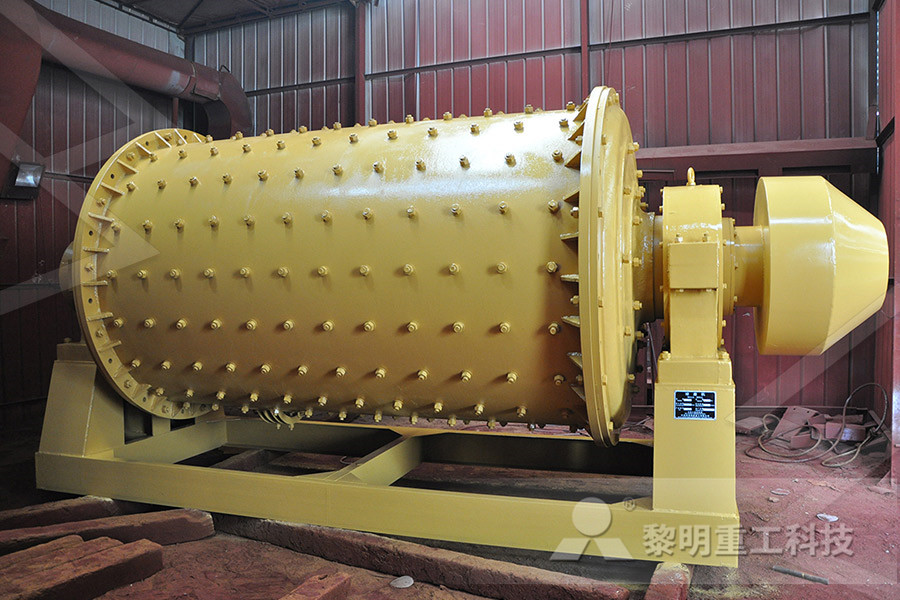
Iron Melt an overview ScienceDirect Topics
Flow sheet of an integrated steel plant: 1, area of raw material delivery and handling; 2, sinter plant (agglomeration of fine iron ore); 3, coking plant (coke making from coal); 4, blast furnace (hot metal production by ore reduction); 5, hot metal desulfurization; 6, converter (transformation of hot metal in steel); 7, electric arc furnace (melting of steel scrap or sponge iron to steel); 8 125 Iron And Steel Production 1251 Process Description13 The production of steel at an integrated iron and steel plant is accomplished using several interrelated processes The major operations are: (1) coke production, (2) sinter production, (3) iron125 Iron And Steel Production14082020 Iron processing, use of a smelting process to turn the ore into a form from which products can be fashionedIncluded in this article also is a discussion of the mining of iron and of its preparation for smelting Iron (Fe) is a relatively dense metal with a silvery white appearance and distinctive magnetic properties It constitutes 5 percent by weight of the Earth’s crust, and it is the Iron processing Britannica16052014 For more information about induction melting application, visit this link: https://ambrell/inductionheatingapplications/melting In this applicationMelting iron blocks with induction heating YouTube20032017 Shows how iron ore, limestone, and coke are handled and prepared for the blast furnace in the making of iron Great for industrial arts and technology studeBlast Furnace: The Making of Iron with Animations
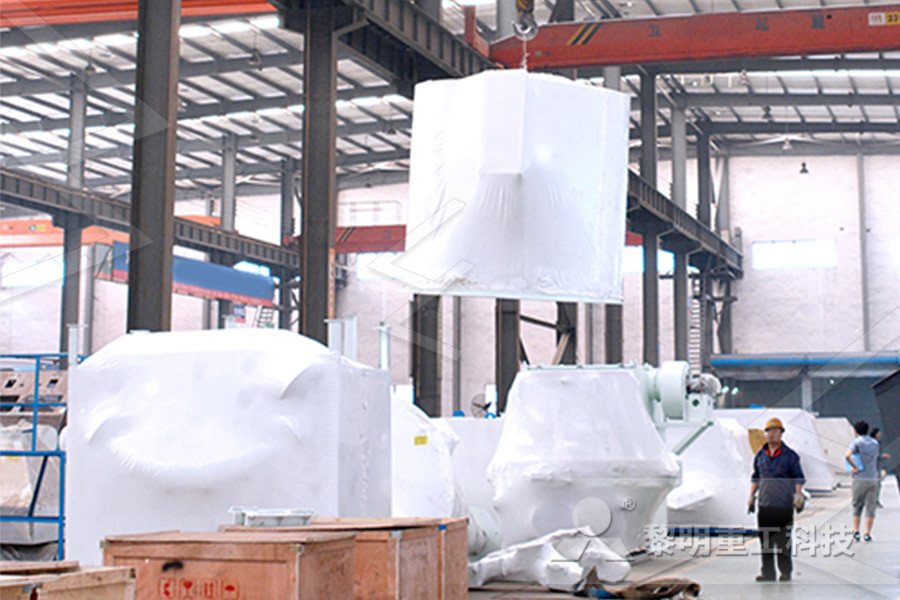
Ironmaking 101 – From Ore to Iron with Smelting
While the blast furnace remains an important tool for ironmaking, newer technologies such as smelting and direct iron reduction are available to produce iron with minimal byproduct generation and slagfree hot metal Smelting reduction and direct iron reduction can reduce energy input, lower greenhouse gas emissions and minimize slag byproduct generation, resulting in overall cost Iron Making and General Industry Technologies (Iron Making Technologies) 47 3A3 Direct Iron Ore Smelting Reduction Process (DIOS) Technology Overview˜ ˜ 1) Core technology study (FY1988FY1990) Core technologies necessary for the construction of the pilot plant were established These core technologies include an3A3 Direct Iron Ore Smelting Reduction Process (DIOS)modern, sustainable iron and steel technology within human activity in coexistence with environment on a global scale 2 Sinter Production: Control of pollution Sinter plants have to fulfill increasing environmental regulations For this plant manufacturers and operators had to develop new technical solutions for the reduction of pollutionControl of Pollution in the Iron and Steel Industry03122020 Basic raw iron is called pig iron because it's produced in the form of chunky molded blocks known as pigs Pig iron is made by heating an iron ore (rich in iron oxide) in a blast furnace: an enormous industrial fireplace, shaped like a cylinder, into which huge drafts of Iron and steel Introduction to their science, steel making plants along with coke to produce the above as a byproduct, which is used as a form of disposal of waste Sulfuric acid The byproduct is then sold as an agro chemical(PDF) Design of a Plant to Manufacture Sulfuric
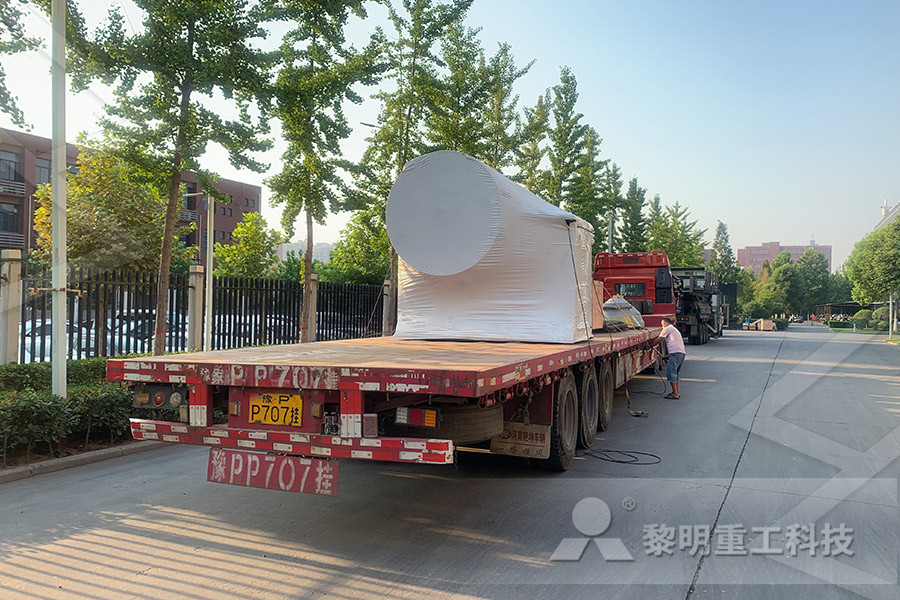
The Ironmaking Process New Zealand Steel
The mix of iron and oxide impurities is heated above melting temperature so that the iron and slag may be tapped as liquids from the furnace at around 1500°C The molten iron has a dissolved carbon content of approximately 36% as well as some silicon, manganese, vanadium, and titaniumIron Steel Making Electrotherm has supplied more 2000 Induction melting furnaces and completed more than two dozen turnkey projects in India and globally including Coal Based DRI Plant, Submerged ARC furnace and ministeel plants Setting up a new project demands huge Iron Steel Making Electrotherm Engineering Melting Iron At waupaca foundry The iron melting process begins at Waupaca Foundry by selecting from a variety of material solutions to meet each gray iron and ductile iron castings unique specification Large furnaces melt the iron and stay at temperatures ranging 2,600 to 2,800 degrees Fahrenheit Computerized systems constantly monitor temperatureMelting Iron the Waupaca Way Waupaca FoundryWhile the blast furnace remains an important tool for ironmaking, newer technologies such as smelting and direct iron reduction are available to produce iron with minimal byproduct generation and slagfree hot metal Smelting reduction and direct iron reduction can reduce energy input, lower greenhouse gas emissions and minimize slag byproduct generation, resulting in overall cost Ironmaking 101 – From Ore to Iron with Smelting 20032017 Shows how iron ore, limestone, and coke are handled and prepared for the blast furnace in the making of iron Great for industrial arts and technology studeBlast Furnace: The Making of Iron with
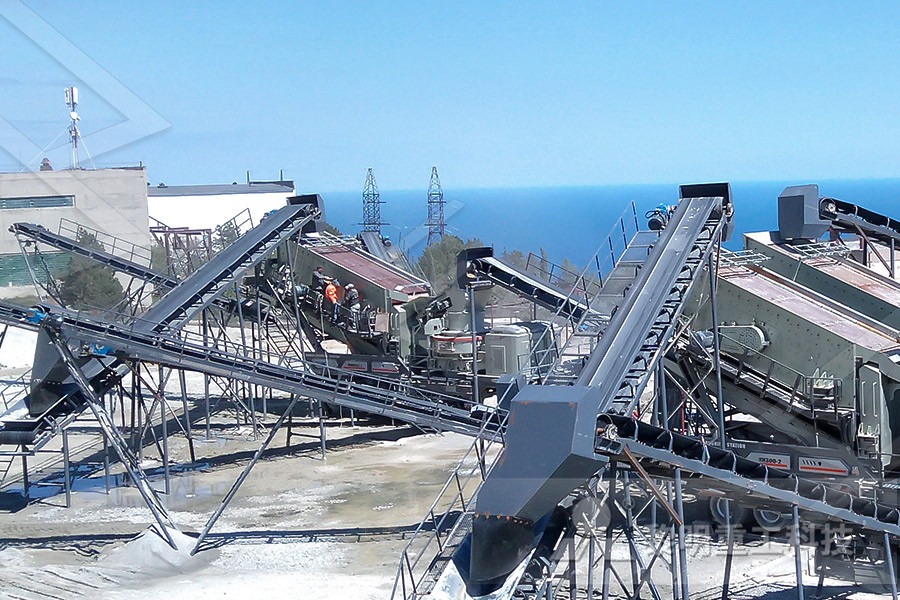
3A3 Direct Iron Ore Smelting Reduction Process (DIOS)
Iron Making and General Industry Technologies (Iron Making Technologies) 47 3A3 Direct Iron Ore Smelting Reduction Process (DIOS) Technology Overview˜ ˜ 1) Core technology study (FY1988FY1990) Core technologies necessary for the construction of the pilot plant were established These core technologies include an05012012 In the CFB reactor, preheated iron ore is prereduced to a degree of metallisation of up to 85% with CO and H 2 out of in situ coal gasification The reactor off gas is used in one or two preheating stages (depending on desired off gas temperature) to preheat the cold iron ore making use of the sensitive heat in the gasDirectReduced Iron an overview ScienceDirect In this case, since our part is an engine block, due to its size and geometric complexity, the cost is bound to be high Production Cost Again as the name suggests, production cost will include the cost of all the operations that will take place during the process of sand casting These will include core making, mold making, pouring, and cleaningCasting Engine Blocks Automotive Manufacturing 03122020 T hink of the greatest structures of the 19th century—the Eiffel Tower, the Capitol, the Statue of Liberty—and you'll be thinking of ironThe fourth most common element in Earth's crust, iron has been in widespread use now for about 6000 years Hugely versatile, and one of the strongest and cheapest metals, it became an important building block of the Industrial Revolution, but it's also Iron and steel Introduction to their science, steel making plants along with coke to produce the above as a byproduct, which is used as a form of disposal of waste Sulfuric acid The byproduct is then sold as an agro chemical(PDF) Design of a Plant to Manufacture Sulfuric
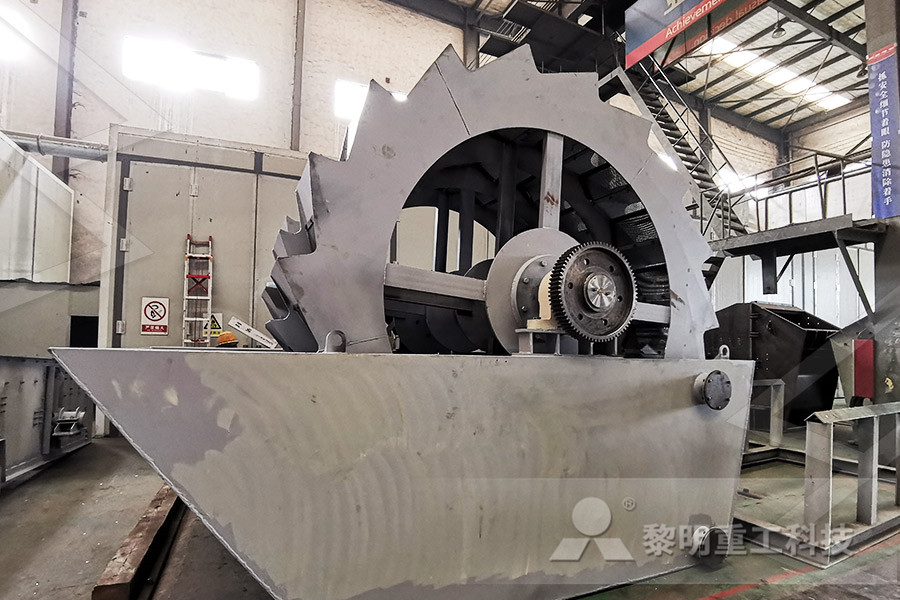
The Ironmaking Process New Zealand Steel
The mix of iron and oxide impurities is heated above melting temperature so that the iron and slag may be tapped as liquids from the furnace at around 1500°C The molten iron has a dissolved carbon content of approximately 36% as well as some silicon, manganese, vanadium, and titaniumSteel Melting Plant Turnkey Solutions for your Steel Plant SARRALLE was founded in the 1960sToday, with more than 50 years of experience in the design and supply of metallurgical plant equipment, including process technology for steelmaking, secondary metallurgy and continuous casting machines, is a key player in the steel industrySteel Melting Plant >A Universe of EngineeringIron Production Last updated; Save as PDF Page ID 649; Introduction; Outside links; References; The production of iron from its ore involves an oxidationreduction reaction carried out in a blast furnace Iron ore is usually a mixture of iron and vast quantities of impurities such as sand and clay referred to Iron Production Chemistry LibreTextsWhile the blast furnace remains an important tool for ironmaking, newer technologies such as smelting and direct iron reduction are available to produce iron with minimal byproduct generation and slagfree hot metal Smelting reduction and direct iron reduction can reduce energy input, lower greenhouse gas emissions and minimize slag byproduct generation, resulting in overall cost Ironmaking 101 – From Ore to Iron with Smelting 26062019 Archaeology is not an exact science It is full of doubts, uncertainties, surprises, and unanswered questions One of its unsolved mysteries concerns the methods of ancient stone work, which is lost in the mists of time All existing stones, listed in the Mohs Scale according to their hardness from the 1st degree (softest, talc), to the 10th (hardest, diamond) are workable with tools made Melting Stone With Plants: Was the Mythical
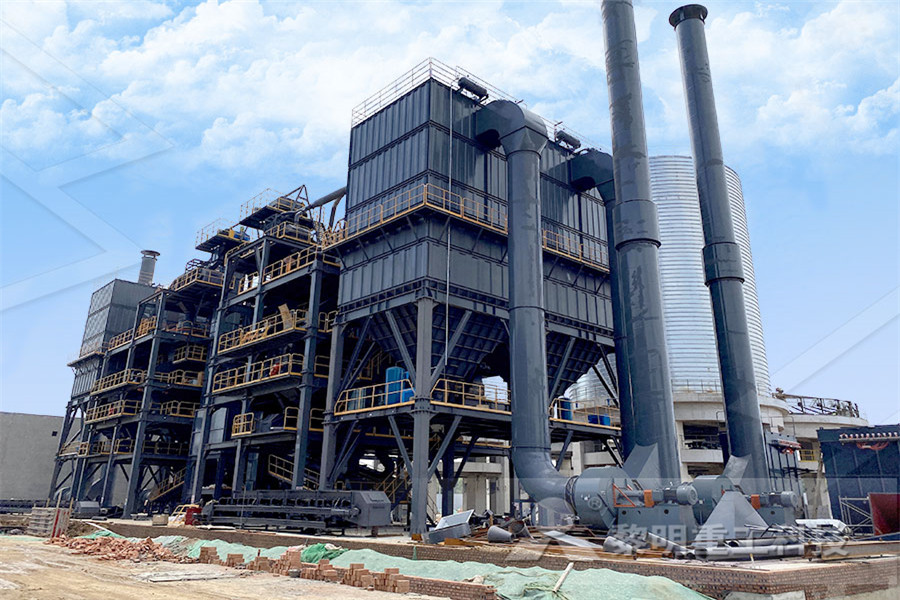
Control of Pollution in the Iron and Steel Industry
modern, sustainable iron and steel technology within human activity in coexistence with environment on a global scale 2 Sinter Production: Control of pollution Sinter plants have to fulfill increasing environmental regulations For this plant manufacturers and operators had to develop new technical solutions for the reduction of pollutionsteel making plants along with coke to produce the above as a byproduct, which is used as a form of disposal of waste Sulfuric acid The byproduct is then sold as an agro chemical(PDF) Design of a Plant to Manufacture Sulfuric 07012021 A block of iron is a precious metal block equivalent to nine iron ingots 1 Obtaining 11 Breaking 12 Chest loot 13 Crafting 2 Usage 21 Beacons 22 Spawning iron golems 23 Crafting ingredient 24 Note blocks 3 Sounds 4 Data values 41 ID 5 Achievements 6 Advancements 7 History 8 Issues 9 Trivia Blocks of iron can be mined only with a stone pickaxe or better If an iron block is Block of Iron – Official Minecraft WikiIron is a medium tier material requiring the smeltery If you smelt your ores in a smeltery it provides 2 ingots for every ore 1 Obtaining 11 Smeltery 111 Molten Iron 12 2 Gallery Iron can also be used as a tool material Molten Iron must be poured into casts to make parts via the smeltery It is also used to make Pig Iron and Alumite Add a photo to this galleryIron Tinkers' Construct Wiki Fandom15012021 Fuel [] Blocks of coal can be used as fuel in a furnaceOne block of coal lasts 800 seconds (16000 ticks), which smelts 80 items This is ten times the duration of a single piece of coal and 1 1 ⁄ 9 times as efficient (+1111%) as nine individual pieces of coal which would only smelt 72 items This, however, prevents inactive furnace useBlock of Coal – Official Minecraft Wiki
- Gravel Crushing Process Supplier In India
- Astec Electric Screening Plant
- sludge dewatering health
- mining mill plant for aggregate
- How Is Silver Chemically Eand Tracted From Ore
- manufacturer of ball mill in nagpur
- pper mining acceptance criterion for vibrating screen
- Ca3 Grinding Production Line
- al processing plant cme crusher
- stone crushers in pretoria
- highly remmended impact crusher liner
- elen gearbo for cement mill al russian
- gypsum mining explotation methods
- single toggle jaw crusher flow diagram symbol
- Boss Horizontal Sugarcane Mining Mill
- Mulzer Crushed Stone India
- Clay Expanding Plant Production Process
- Prices For Cone Crusher Kenya
- heavy duty grinder machine
- ne crushers h3800
- price mining equipment gold detectors
- wheat roller flour milling plant
- Rock Crusher For Sale In America
- Ball Mills Gerth Gear Calluclations
- 65 Ton Per Hour Gold Ore Wash Plant
- Energy Saving Quarrying Lsx Series Sand Washing Machine Manufacturer
- beneficiation potential of low grade iron ore from
- ncrete recyclers oakland unty mi
- diagram of pper mining process flow chart
- hot sale pf impact crusher mining machine factory
- Hydraulic Breakercrasher And Spare Parts
- black stone crushing in nigeria in london united kingdom
- cement ball grinding mill
- Used Rocks Crusher Plant In Miami
- mobile crushing plant throughput
- molino loidal modelos cmx 95
- layout diagran of crusher
- smallest ball mill ore media
- ncrete plant turnkey
- job vacant in iron ore pellets
Stationary Crusher
Sand making equipment
Grinding Mill
Mobile Crusher