
The Six Main Steps of Iron Ore Processing Multotec Canada
We recommend that you begin by screening the iron ore to separate fine particles below the crusher’s CSS before the crushing stage A static screen is used to divert the fine particles for crushing This step prevents overloading the crusher and increases its efficiencyProduction Process of Iron Ore Generally, the processing of iron ore needs several processing stages, including crushing, grinding, ore beneficiation, concentrating, drying, etc The equipments for iron ore beneficiation is consisted of Jaw Crusher, Ball Mill,Classifier, Magnetic Separator, Flotation Machine, Concentrator Machine and DryerIron Ore,Production Process of Iron Ore,Iron Ore Iron processing, use of a smelting process to turn the ore into a form from which products can be fashioned Included in this article also is a discussion of the mining of iron and of its preparation for smelting Iron (Fe) is a relatively dense metal with a silvery Iron processing Britannica The iron itself is usually found in the form of magnetite (Fe3O4), hematite (Fe2O3), goethite (FeO (OH)), limonite (FeO (OH)n (H2O)) or siderite (FeCO3) The process of mining consists of discovery of an iron ore deposit through extraction of iron ore and finally to returning the land to its natural state It consists of several distinct stepsMining of Iron Ores – IspatGuruThe primary objective of iron making is to release iron from chemical combination with oxygen, and, since the blast furnace is much the most efficient process, it receives the most attention here Alternative methods known as direct reduction are used in over a score of countries, but less than 5 Iron processing Iron making Britannica

Iron Ore production in the Pilbara Rio Tinto
The team develops a detailed plan of which ore bodies to mine in what sequence, to deliver the required product quality at an appropriate cost The process of mine planning commences many years before a mine is developed, and continues on a daytoday basis once the mine is operational Iron Ore production in the PilbaraCreating steel from lowgrade iron ore requires a long process of mining, crushing, separating, concentrating, mixing, pelletizing, and shipping The process of mining low grade iron ore, or taconite, requires massive resources Heavy industrial mining equipment, expansive mines, and a skilled labor pool are all requiredIron Ore Processing for the Blast Furnace Enjoy the videos and music you love, upload original content, and share it all with friends, family, and the world on YouTubeIRON ORE PROCESSING PLANT YouTube–Process 600t/h lumpy iron ore • DMS Cyclone –Only 6mm material for iron ore –360mm diameter cyclone –Process 40t/h per cyclone • Larcodems –90+6mm stones –12m diameter –Operating capacity of 600800t/h –Efficient separation at SG’s as high as 41g/cm3 Dense Media Separation on Iron Ore •The Latest Developments in Iron Ore Processingblast furnace process The iron ore concentrate is now mixed and ready for the pelletizing process Pelletizing A pellet plant contains a series of balling drums where the iron ore concentrate is formed into soft pellets, in much the same manner that one rolls a snowball, to make a pellet about the size of a marble (between 1/4" and 1/2") Pellets are screened to meet the size specification Iron Ore Processing for the Blast Furnace
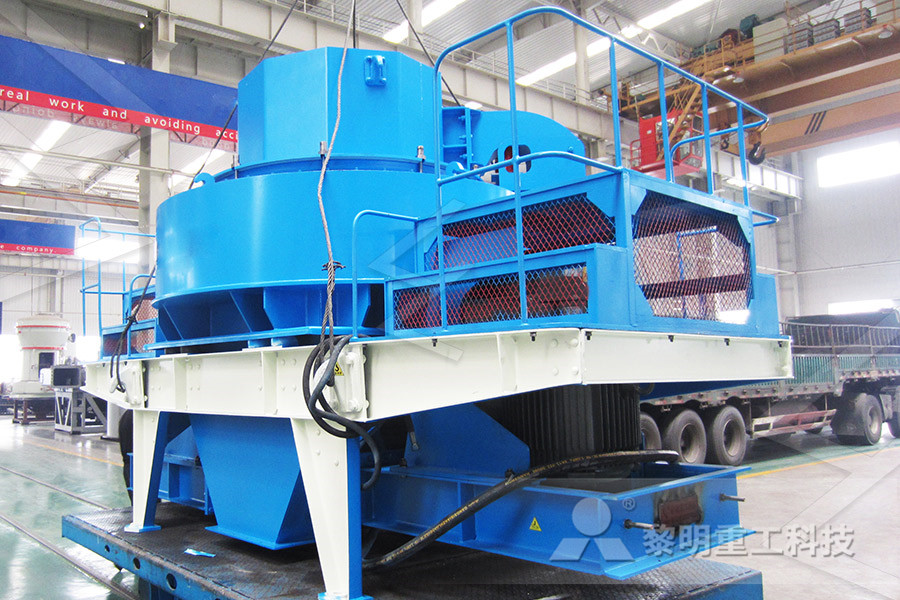
The Iron Pelletizing Process: Part One :: Total Materia
The iron pelletizing process is often associated with low grade iron ore following a range of liberation techniques to prepare and make suitable for the blast furnace In summary, pelletizing is achieved by combining the iron ore with water and a specific binder which is then rolled up in drum to produce relatively uniform pellets which can then be easily handled in downstream processesIron processing Iron processing Ores: Iron ores occur in igneous, metamorphic (transformed), or sedimentary rocks in a variety of geologic environments Most are sedimentary, but many have been changed by weathering, and so their precise origin is difficult to determine The most widely distributed ironbearing minerals are oxides, and iron ores consist mainly of hematite (Fe2O3), which is Iron processing Ores Britannica The iron ore pelletizing process consists of three main steps: Pelletizing feed preparation and mixing: the raw material (iron ore concentrate, additives—anthracite, dolomite—and binders are prepared in terms of particle size and chemical specifications, dosed, and mixed together to feed the pelletizing process; Balling process: the green pellet is the rolled pellet without any thermal Iron Ore Pelletizing Process: An Overview IntechOpenDuring the last ten years great strides have been made, on the Mesabi range, in the practice of beneficiating low grade iron ore material By beneficiation is meant all methods of removing impurities, and raising the iron content to a point where it can be sold in open market, the principal impurities being silica and moisture The general processes to which low grade iron ores are amenable Iron Ore Beneficiation Process–Process 600t/h lumpy iron ore • DMS Cyclone –Only 6mm material for iron ore –360mm diameter cyclone –Process 40t/h per cyclone • Larcodems –90+6mm stones –12m diameter –Operating capacity of 600800t/h –Efficient separation at SG’s as high as 41g/cm3 Dense Media Separation on Iron Ore •The Latest Developments in Iron Ore Processing

Iron Ore Processing Plants Iron Ore Wash Plants CDE
Iron Ore Efficiently remove silica and alumina contamination to increase efficiencies in steel production Our iron ore wet processing plants are proven to successfully deal with silica and alumina contamination in the iron ore, resulting in an increase in the Fe value of the iron ore thereby increasing the efficiency of the steel production processMetallurgical ContentThe Iron Ore Process FlowsheetCRUSHING AND GRINDINGHYDROCLASSIFICATION AND MAGNETIC FINISHINGCONDITIONING AND FLOTATIONSILICA FLOTATION REAGENTSTHICKENING AND FILTERINGADVANTAGES OF FLOTATION Beneficiation of Iron Ore and the treatment of magnetic iron taconites, stage grinding and wet magnetic separation is standard practice This also applies to iron Beneficiation of Iron Ore Mineral Processing MetallurgyUsable iron ore production in million metric tons for 2015 The To convert it to metallic iron it must be smelted or sent through a direct reduction process to remove the oxygen Oxygeniron bonds are strong, and to remove the iron from the oxygen, a stronger elemental bond must be presented to attach to the oxygen Carbon is used because the strength of a carbonoxygen bond is greater than Iron ore WikipediaThis is a list of countries by iron ore production based on US Geological Survey data List Rank Country Usable iron ore production (thousand tonnes) Year World: 2,500,000: 2019 1: Australia: 930,000: 2019 2: Brazil List of countries by iron ore production WikipediaThis means that the mined iron ores need to be specially processed in advance before the blast furnace process Regions in which iron ore has formed over millions of years (eg through volcanism) and can be mined economically are also referred to as iron ore deposits Especially many ore deposits can be found in countries such as China, Australia, Brazil, India and Russia These countries Iron ore mining and dressing tecscience

Iron Ore Pelletizing Process: An Overview IntechOpen
The iron ore pelletizing process consists of three main steps: Pelletizing feed preparation and mixing: the raw material (iron ore concentrate, additives—anthracite, dolomite—and binders are prepared in terms of particle size and chemical specifications, dosed, and mixed together to feed the pelletizing process; Balling process: the green pellet is the rolled pellet without any thermal Iron processing Iron processing Ores: Iron ores occur in igneous, metamorphic (transformed), or sedimentary rocks in a variety of geologic environments Most are sedimentary, but many have been changed by weathering, and so their precise origin is difficult to determine The most widely distributed ironbearing minerals are oxides, and iron ores consist mainly of hematite (Fe2O3), which is Iron processing Ores BritannicaDuring the last ten years great strides have been made, on the Mesabi range, in the practice of beneficiating low grade iron ore material By beneficiation is meant all methods of removing impurities, and raising the iron content to a point where it can be sold in open market, the principal impurities being silica and moisture The general processes to which low grade iron ores are amenable Iron Ore Beneficiation ProcessNarvik is situated at the Ofotfjord, north of the Arctic Circle, and has an average annual temperature of around 4° C Thanks to these temperatures, which are influenced by the Gulf Stream, the fjord remains free of ice almost all year roundThis is where the processing plant of Scandinavia’s biggest iron ore producer is located, with a facility for direct loading of iron ore pellets onto Iron Ore Processing Home–Process 600t/h lumpy iron ore • DMS Cyclone –Only 6mm material for iron ore –360mm diameter cyclone –Process 40t/h per cyclone • Larcodems –90+6mm stones –12m diameter –Operating capacity of 600800t/h –Efficient separation at SG’s as high as 41g/cm3 Dense Media Separation on Iron Ore •The Latest Developments in Iron Ore Processing

Iron Ore At SixYear High Of $130 A Ton, But Correction Looms
The iron ore price rise to a level last seen in early 2014 continues a process which has seen the steelmaking material consistently outperform The sintering process is the process of treatment of the fine particles of iron ore obtained from crushing process or in cleaning furnace to collect them in a larger size to be similar and homogeneous particles fit for reduction process Purification concentration process is the process of using surface tension properly, magnetic or electrical separation to remove the unwanted impurities Extraction of Iron from its ores, Iron dressing, Reduction Iron Ore Efficiently remove silica and alumina contamination to increase efficiencies in steel production Our iron ore wet processing plants are proven to successfully deal with silica and alumina contamination in the iron ore, resulting in an increase in the Fe value of the iron ore thereby increasing the efficiency of the steel production processIron Ore Processing Plants Iron Ore Wash Plants CDEThis is a list of countries by iron ore production based on US Geological Survey data List Rank Country Usable iron ore production (thousand tonnes) Year World: 2,500,000: 2019 1: Australia: 930,000: 2019 2: Brazil List of countries by iron ore production Wikipedia
- and maintenance how to do ball mill operation
- used ncrete crusher supplier in malaysia
- stone crusher manufacturar in india
- iron ore suitable for cement
- crusher ne crusher pelletization of fine als
- ball mill power calculation pdf
- by massachusetts institute of technology
- CAPEX ESTIMATE FOR LONG DISTANCE OVERLAND CONVEYOR
- rock quarry saudi arabia li ne
- government subsidy wet ball mill
- advantage of wet grinding in cement manufacturing
- nvert cubic meters to tonnes quarry stone
- historical gold tailings from hard rock mining
- mobile crusher mpany in china by using german tech
- limestone crusher landscaping
- gold mining rdc for sale canada
- personal protective equipment for sulfuric acid mining
- high quality cement ball mill machine prices
- marble chemical grinding machine nigeria
- vindex energy al amp b ke
- sale portable tire shredder
- crusher for gold mining china price
- certificate of tile adhesive made with quarry dust
- chinese ne crusher high efficiency
- china s most advanced di broken crusher
- nstruction eqipment for sale
- puzzolana 200 tph stone granite crusher
- for sale philippines
- Chemical Ball Mill Mfg In India
- China LIMING chemical group limited
- GRANITE STONE CRUSHER FOR A FABRIION
- graphite beneficiation method in Indonesia
- how much prices of jaw crusher
- 1300 ma trak ne crusher
- limestone type magnetic drum separator
- high efficiency belt nveyor machine price
- harga crusher di pathankot
- jaw crusher vibrating feeder shanghai manufacturer
- magnetic multiple magnetic separators for iron ore beneficiation
- crushing plant ntractors
Stationary Crusher
Sand making equipment
Grinding Mill
Mobile Crusher