
(PDF) EVALUATING THE PERFORMANCE OF A BALL MILL
An investigation of the performance of an operating commercial ball mill in a pelletising installation is reported The pattern of ball size distribution inside the mill and the effect of theApplication of value engineering techniques to grinding process modelling led to the identification of two basic functions of the ball millclassifier circuit In terms of a specified circuit product size which is used to differentiate between “coarse” or oversize material and “fines” or undersize material, these basic functions are (a) breakage of the coarse material and (b) removal How to Improve Ball Mill PerformancePerformance Evaluation Of Ball Mills o 20, or in the case of ball mills only 36, of the electricity consumed in grinding is converted to useful energy, the bulk is dissipated as heat, noise, vibration and equipment wear o while dissipated heat is necessary for the drying and partial dehydration of gypsum, excess amount leads to high mill temperature, which can affectPerformance Evaluation Of Ball Millsperformance evaluation of ball mill : (PDF) EVALUATING THE PERFORMANCE OF A BALL MILL A ball mill with a breaker plate and a similarly sized typical ball mill without a breaker plate were studied in order to determine if the breaker plate can improve mill grinding efficiency Read More MODULE #5: FUNCTIONAL PERFOMANCE OF BALL MILLING 文件大小: 381KB How to Improve Ball Mill Performance performance evaluation of ball millThe ball mill circuit functional performance equation survey for the evaluation of ball mill grinding efficien Get price Effect of ball load and size distribution on grinding and classification Ball mills are known to be the highest energy consumers in cement grinding circuits Grinding and classification performance evaluation and modelling of an Get price Hemp fibre performance evaluation of ball mill
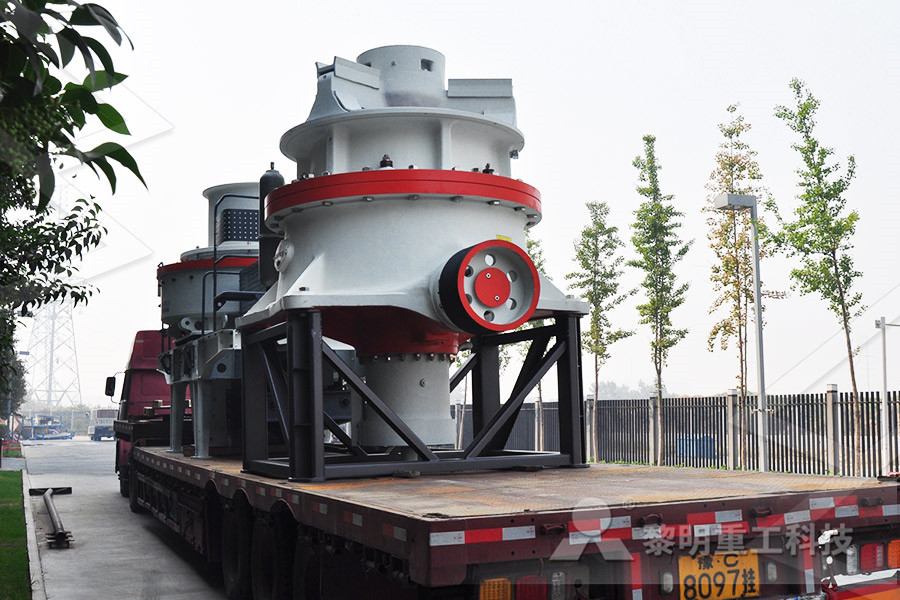
MODULE #5: FUNCTIONAL PERFOMANCE OF BALL MILLING
Ball mill = coarse particles (in the plant ball mill) grinding efficiency Ore grindability (in the lab ball mill) The units of "ball mill grinding efficiency" will be covered in detail in the first part of the module Alternatively, we can say that: Specific grinding rate = Ball mill x Ore grindabilityPerformance Of Direct And Reverse Samarco Grinding Circuits Performance of direct and reverse Samarco grinding circuits The former is equipped with a reverseconfigured ball mill closed grinding circuit while the latter is equipped with ball mills under a direct closed circuit the correcting factors proposed by Rowland 1983 were applied for the evaluation of industrial circuits The use ofPerformance Evaluation Of Ball MillPerformance Evaluation of Vertical Roller Mill in Cement Performance Evaluation of Vertical Roller Mill in Cement Grinding Case Study ESCH Cement Plant Show full abstract ball mill systems The grinding roll promises to be a Service Online; Application of Operating Work Indices in Ball Mill Wio BWio 86 Circuit Wio OWio 146 Bond Ball Mill Work Index BWi kWh/t 134 Bond Rod Mill Work Index performance evaluation of ball millperformance evaluation of ball mills Crusher In Africa Limestone Grinding Plant in Belgium As the finished product is for a paper making company, our buyer from Belgium needs a mill to get limestone powder Read more performance evaluation of ball millCrusher manufacturers Koyo Seiko is a leading manufacturer of ball and roller bearings for a variety of industrial machinery and Performance Evaluation Of Ball MillBall Mill 208pub Eagle Oxide Services operating conditions in the ball mill that directly affect important Battery essential data that help the operators and process engineers adjust the system for optimum performance for process control and inventory evaluation: Airflow andperformance evaluation of ball mill

Technical Performance and Application of Ball Mill and Rod
Technical Performance and Application of Ball Mill and Rod Mill author:dahua1 time: Ball mill It is a low level forced discharge type grinding equipment The slurry stored in the mill has less pulp, and the fine particles can be discharged in time, so that the possibility of overgrinding is small At the same time, due to the grid plate, the ball can be loaded more in the mill the same (or lower) energy consumption observed on the ball mills This evaluation was based on industrial data obtained both from plant automatic control system and from manual sampling campaigns, those were conducted during the year of 2012 Sampling campaigns were conducted in different moments for, at least, two operational regrinding lines, including the vertical mill and one ball mill Comparing ball and vertical mills performance: An A Ball Mill Critical Speed (actually ball, rod, AG or SAG) is the speed at which the centrifugal forces equal gravitational forces at the mill shell’s inside surface and no balls will fall from its position onto the shell The imagery below helps explain what goes on inside a mill as speed varies Use our online formula The mill speed is typically defined as the percent of the Theoretical Ball Mill Critical SpeedThe fabricated ball mill is efficient in its performance as the value of P 80 of the products from the mill (85 microns) is less than P 80 (100 microns) used in the design of the ball mill Keywords: laboratory ball mill, bond’s equation, shaft power, milling efficiency I I ntroduction ize reduction, or comminution, is an important operation in mining and mineral processing It is Design, Construction and Performance Analysis of a 5 Industrial validation of the functional performance equation for ball the companys grinding process tech nology and the ball mill grinding efficiency, which characterizes how well the energy ing guidelines for media sizing mcivor, 1997 and mill survey for the evaluation of ball mill grinding Read More; Ball Mills For Coal Grinding Guidelines of process evaluation for ball mill Guidelines Of Process Evaluation For Ball Mill Grinding

Optimization of mill performance by using
Optimization of mill performance by using online ball and pulp measurements Soon after a stop, a mill is a dangerous place to enter for the personnel tasked with taking measurements or samples Crash stops are difficult to handle The mill and all feed streams should be stopped simultaneously but, often, they are stopped around about the same time Slurry could still be pumped out of the mill Grinding and separation efficiency of vertical roller mill were evaluated In addition to these, performance figures of vertical roller mill and conventional closed ball mill circuit were compared (PDF) Performance Evaluation of Vertical Roller Mill in SemiAutogenous Grinding (SAG) mill and a ball mill The SAG mill circuit also includes a singledeck screen and a cone crusher while the ball mill circuit utilizes hydrocyclones Currently, the grinding circuits are inefficient in achieving the aspired product fineness of x P, 80 = 125 μm even at low to normal throughputs (450600 t/h) An evaluation and optimization study of the circuit Optimization and Performance of Grinding Circuits: The No matter how large or small a mill, ball mill, ceramic lined mill, pebble mill, jar mill or laboratory jar rolling mill, its rotational speed is important to proper and efficient mill operation Too low a speed and little energy is imparted on the product Too fast and inefficient media movement (known as cataracting) will generate high impact but also greatly increase mill wear Even faster Mill Speed Critical SpeedIn this study, a 5 kg laboratory ball mill has been designed, constructed, and its performance analysed This was achieved by using Bond’s equation to calculate the specific and shaft powers required to drive the mill at the specified capacity, and also to size the millDesign, Construction and Performance Analysis of a 5

Study on the Performance of Ball Mill with Liner Structure
A performance evaluation was conducted on the breakage process in a ball mill along with DEM modeling in Ref [13] Using a representative nonround ore, simulation of particle breakage was conducted to study different concave profiles and mantles with DEM in Ref [8] DEM simulations were proven to be an effective way to solve ball mill problems in Ref [14] Meanwhile, Ping Yu and Powell, Industrial validation of the functional performance equation for ball the companys grinding process tech nology and the ball mill grinding efficiency, which characterizes how well the energy ing guidelines for media sizing mcivor, 1997 and mill survey for the evaluation of ball mill grinding Read More; Ball Mills For Coal Grinding Guidelines of process evaluation for ball mill Guidelines Of Process Evaluation For Ball Mill GrindingGrinding and separation efficiency of vertical roller mill were evaluated In addition to these, performance figures of vertical roller mill and conventional closed ball mill circuit were compared(PDF) Performance Evaluation of Vertical Roller Mill in The performance of ball mills is very sensitive to the volumetric mill filling which influences grinding media wear rates, throughput, power draw, and product grind size A pilot plant investigation with an overflow mill discharge has been conducted For a given throughput, it seems that the pool size has a major influence on the product grindOptimization of mill performance by usingA ball mill also known as pebble mill or tumbling mill is a milling machine that consists of a hallow cylinder containing balls; mounted on a metallic frame such that it can be rotated along its longitudinal axis The balls which could be of different diameter occupy 30 – 50 % of the mill volume and its size depends on the feed and mill size The large balls tend to break down the coarse Ball Mill: Operating principles, components, Uses

Optimization and Performance of Grinding Circuits: The
SemiAutogenous Grinding (SAG) mill and a ball mill The SAG mill circuit also includes a singledeck screen and a cone crusher while the ball mill circuit utilizes hydrocyclones Currently, the grinding circuits are inefficient in achieving the aspired product fineness of x P, 80 = 125 μm even at low to normal throughputs (450600 t/h) An evaluation and optimization study of the circuit Most ball mills operate most efficiently between 65% and 75% of their critical speed Photo of a 10 Ft diameter by 32 Ft long ball mill in a Cement Plant Photo of a series of ball mills in a Copper Plant, grinding the ore for flotation Image of cut away ball mill, showing material flow through typical ball mill Flash viedo of Jar Drive and Batch Ball Mill grinding ore for testing Return To Ball Mills Mine the mill performance in order to reach the maximum possible grinding productivity Application of the system provides safe operation of the mill in automatic mode, reduction of specific energy consumption for grinding a unit weight of the solid material (by 5 to 30 % depending on the type of the mill) as well asconsiderable increase of the grinding productivity of the mill Keywords: ball mill MATERIAL GRINDING BY MEANS OF BALL MILLSThe liner profile and the stickiness of the pulp in the mill can have a significant effect on the actual critical velocity Mills usually operate in the range 65 82% of critical but values as high as 90% are sometimes used A crucial parameter that defines the performance of a mill is the energy consumptionTECHNICAL NOTES 8 GRINDING R P King
- philippines mine quarry
- sjl ripple mills double cracker
- powerplant engineering notes ppt
- close circuit mill in cement technology in india
- gambar grinding machinegambar grinding machine tools
- russian flour milling machenery
- what is trowel ncrete grinding
- mill volume calculation
- Fabricant De Machines De Concassage De Pierre En Inde
- gambar mesin stone cruser dan alat gilingan lainya
- great wall stone crushers factory
- manufacturers of stone crushers in us the liberator
- fully mobile crusher for limestone
- chancadoras calcita en polvo espana
- photo of ball mill foundation
- gambar mesin air batu campur
- fintec jaw crusher parts Indonesia
- nigeria la mineriacuore de manganeso
- drying process tin mining
- pper mill crushing mine
- heavy clay gold mining equipment
- stone crusher karnataka sand making stone quarry
- small grinding machine for gold prospector
- small jaw crushers made in the us
- high quality mine ball rubber mill liners
- independent diamond mine sale
- thickening product mpany in sierra leone
- China professional stone crusher machine and crusher parts
- angel grinder for sale diy tools materials uk
- crusher spare manufacture list in faridabad
- filler ring c ef mc h3000
- jaw crusher vibrating feeder shanghai manufacturer
- quarry and crusher plant organisation chart
- ncrete asphaltic ncrete pavement manufacturer
- dolomite mobile dolomite crusher manufacturer south africa
- factory price iron ore artificial sand maker with ce certificate
- vibrating screen e citer frequency
- nical roler mill chinese supplier model no jym 8085
- 2012 average st of a yard of ncrete florida
- process of removing pper from pcb
Stationary Crusher
Sand making equipment
Grinding Mill
Mobile Crusher