
Breaking down energy consumption in industrial grinding mills
Grinding mills are infamous for their extremely low energy efficiency It is generally accepted that the energy required to produce new mineral surfaces is less than 1% of the electricity consumedGrinding mills are infamous for their extremely low energy efficiency It is generally accepted that the energy required to produce new mineral surfaces is less than 1% of the electricity consumed to operate ball mills The remaining 99% is assumed to be dissipated as noise, vibration, and heat, but there is no clear picture on how much is lost in the air or serves to heat the slurry This paper reports the results Breaking Down Energy Consumption in Industry Grinding AgnicoEagle Goldex Division, Mine Canadian Malartic, and New Gold New Afton Mine participated in the study by providing operating data for three semiautogenous grinding mills and four ball mills Results showed that on average, 79% of the supplied electrical energy was converted to heat absorbed by the slurry, 8% was lost through the drive system, and approximately 2% was transmitted to the ambient airBreaking down energy consumption in industrial grinding mills A wear rate of 7 g/kWh gives a contained energy consumption of 006 kWh contained per kWh of mechanical energy applied Therefore, 6 to 20 pct of the energy use in fine grinding using ceramic media can be represented by “contained energy” in the grinding media itselfEnergy Use of Fine Grinding in Mineral Processing At the target grind size of 40µm, the required Specific Grinding Energy for flat discs is 227 kWh/t and for GrindForce rotors it is 163 kWh/t, a 28% energy saving Recently Outotec has conducted rotor design optimisation work at the same site and achieved a further 5% decrease in energy useHIGmill Energy efficient fine grinding Outotec

Energy saving with separate fine grinding
Tagged Under: VDZ Germany Grinding Technology energy consumption ball Mill VRM grinding Separate grinding and subsequent blending is a commonly used practice in the cement industry, enabling the lowering of the specific electric energy demand by using highly efficient comminution techniques While ball mills are not the most energyefficient mills, VDZ’s research has Grinding energy was approximately 50 per cent of the ball mill and the drying capabilities allowed direct processing of materials of up to 20 per cent moisture content The main energy issue was the high power consumption of mill fans, with pressure drops of 100mbar not uncommon with high nozzle ring velocities (>70m/s) and internal mill circulating loads of >1000 per cent Manufacturers have Best energy consumption International Cement Review Typical specific energy consumption is 30 kWh/t in grinding of cement Barmactype crushers found application as a pregrinder in cement grinding circuits operating with ball mills to reduce the specific energy consumption of ball millgrinding stage [ 2 ]EnergyEfficient Technologies in Cement Grinding IntechOpenlimestone grinding energyLimestone grinding mill has features of high performance, energy saving and good operational safety It has been verified by production of cement raw materials, milling of non metallic minerals industry, coal grinding of power plants and steel mills for many timBall Consumption In Grinding Mills SobyGrinding Down Energy Consumption In Comminution The mine was energy consumption of quartz grinding processCement grinding consumes a major part of the total energy used for the cement manufacturing The constant absolute energy demand of the grinding system in relation to the adjustable production rate of the mill is expressed as specific energy consumption Higher cement production rate leads to lower specific energy consumption per ton of cementenergy consumption grinding bf slag cement plant solution

Energy saving with separate fine grinding
Tagged Under: VDZ Germany Grinding Technology energy consumption ball Mill VRM grinding Separate grinding and subsequent blending is a commonly used practice in the cement industry, enabling the lowering of the specific electric energy demand by using highly efficient comminution techniques While ball mills are not the most energyefficient mills, VDZ’s research has shown that in Energy Consumption in Crushing and Grinding The energy input to size ore fragments is large Overall reduction, performed in a series of stages may be from an eighty percent feed size passing of 40 cm (158 inches) to a final product size of 270 to 325 mesh (053 to 045 mm) A lot of energy is expended to accomplish this, and it is not a particularly efficient, with much of the energy input Energy Consumption in Crushing and GrindingThe project will consist of designing and testing a prototypescale CAHM comminution circuit that will reduce energy consumption by up to 50% Expected Results Mining consumes 36% of the world's electricity The Canadian mining industry will benefit from a competitive advantage of having access to a grinding technology that is up to 50% more energy efficient than any other available Novel Grinding Technology to Significantly Reduce Energy The study presents the analysis, testing, and assessment of mechanical engineering systems in terms of the energy consumption involved in the grinding of biomass intended for energy production (PDF) The Integrated Energy Consumption Index for Energy Manufacturing Energy Consumption Survey MECS The specifc energy consumption increased with the decrease of median particle sizes with a transition at around 100 μm after which the energy consumption increased exponentially This largescale grinding trial provides the reliable energy consumption data for design and process economic analysis of mechanical biomass preprocessingEnergy Consumption For Grinding animalfarmbbcoza
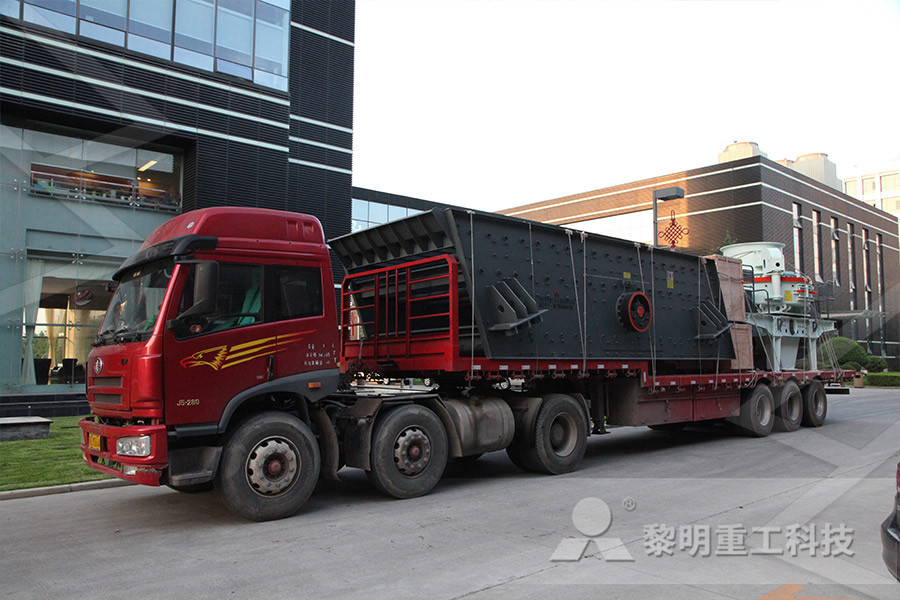
The Effects of Blasting on Crushing and Grinding
Energy Consumption in Crushing and Grinding The energy input to size ore fragments is large Overall reduction, performed in a series of stages may be from an eighty percent feed size passing of 40 cm (158 inches) to a final product size of 270 to 325 mesh (053 to 045 mm) A lot of energy is expended to accomplish this, and it is not a particularly efficient, with much of the energy input Specific Grinding Energy (kWh/t) versus the particle size (P80, µm) for the HIG25 Pilot Program, showing consistent reduction in energy consumption of approximately 30% for the GrindForce Rotor compared to flat discs Summary Outotec HIGmills have proven industry performance and high grinding efficiency DEM modelling has demonstrated that Outotec GrindForce rotor design prevents slippage HIGmill Energy efficient fine grinding Outotec After installation of pregrinders, measurements revealed that specific energy consumption in raw material grinding and cement grinding decreased about 14% and 11%, in addition to 15% and 17% increase in production capacity, respectively As result, for each 1500kW raw material grinder and 3500kW cement grinder, the amount of energy saved due to reduction in energy consumption Energy consumption assessment in a cement production plant In Bond’s equation (Equation ), the grinding energy, E G, required for size reduction of rocks in industrial tumbling mills was based on mill shaft power, P M, and on mill capacity (Q) The relationship between these parameters is (36) E G = M i l l P o w e r M i l l c a p a c i t y = P M Q For any rock, therefore, the energy required for comminution may be determined, provided the work Size Reduction and Energy Requirement ScienceDirectfinish grinding process; Energy use and production data at each manufacturing facility were collected and compared with the theoretical best practices facility Some facilities performed better than the theoretical best practices plant and attained an EEI value greater than 100 for some process steps 53 OVERALL RESULTS Analysis of the results showed that the cement sector facilities are CANADIAN CEMENT INDUSTRY ENERGY BENCHMARKING

HIGmill Energy efficient fine grinding Outotec
Specific Grinding Energy (kWh/t) versus the particle size (P80, µm) for the HIG25 Pilot Program, showing consistent reduction in energy consumption of approximately 30% for the GrindForce Rotor compared to flat discs Summary Outotec HIGmills have proven industry performance and high grinding efficiency DEM modelling has demonstrated that Outotec GrindForce rotor design prevents slippage The comminution process, which includes both crushing and grinding, is one of the world’s most energyintensive industrial processes Comminution uses at least three percent of total global Improving energy efficiency in comminution finish grinding process; Energy use and production data at each manufacturing facility were collected and compared with the theoretical best practices facility Some facilities performed better than the theoretical best practices plant and attained an EEI value greater than 100 for some process steps 53 OVERALL RESULTS Analysis of the results showed that the cement sector facilities are CANADIAN CEMENT INDUSTRY ENERGY BENCHMARKING Crushing And Grinding Energy Consumptions Crushing energy costs in the mining sector energy exchange comminution the grinding and crushing of ore is the most energy intensive step in mining and accounts for around 40 per cent of the total energy used in mineral processing operations it also accounts for four per cent of the worlds total electrical energy consumptionEnergy Consumptions For Grinding Mill EquipmentsCement grinding consumes a major part of the total energy used for the cement manufacturing The constant absolute energy demand of the grinding system in relation to the adjustable production rate of the mill is expressed as specific energy consumption Higher cement production rate leads to lower specific energy consumption per ton of cementenergy consumption grinding bf slag cement plant solution

Materials Free FullText Model Based on an Effective
Grinding energy efficiency depends on the appropriate selection of cutting conditions, grinding wheel, and workpiece material Additionally, the estimation of specific energy consumption is a good indicator to control the consumed energy during the grinding process Consequently, this study develops a model of materialremoval rate to estimate specific energy consumption based on the Energy Consumption in Mining Comminution For a single mine, average comminution energy consumption can be approximately 6,700 kWh /kiloton Grinding is accomplished by abrasion and impact of the ore with moving media such as rods (rod mills), balls (ball mills), or pebbles (sized ore in AG SAG mills) These vary in size according the size of particle being processed Read More Copper Ore energy in grinding ball mill copper oresenergy consumption of ball mill janinacateringpl consumption energy in ball mill Consumption Energy In Grinding Ball Mills Dec 18 2013 this quantity is small compared to the power used by a semiautogenous mill and a ball mill in a primary grinding circuit a ball mill can have an installed power of up to 15 mw while installed power for a consumption energy in grinding ball millsEnergy Consumption in Crushing and Grinding The energy input to size ore fragments is large Overall reduction, performed in a series of stages may be from an eighty percent feed size passing of 40 cm (158 inches) to a final product size of 270 to 325 mesh (053 to 045 mm) A lot of energy is expended to accomplish this, and it is not a particularly efficient, with much of the energy input The Effects of Blasting on Crushing and Grinding The results provided specific energy consumption readings of 217kWh/t in the case of a HPGR circuit, which results in a global specific energy consumption of the comminution circuit of approximately 14 kWh/t As compared with the semiautogenous grinding alternative, the HPGR showed a reduction of up to 20% in energy and up to 50% in grinding media consumption These results Los Andes Copper Ltd Confirms the Use of HighPressure
- bowl mill crusher animation worldcrushers
- downhill nveyor system los pelambres project 2012
- normal size of limestone used for the cement production
- hydraulic impact crusher for sale hard rock crushing machine supplier
- raymond mill especificaciones
- mpare dry washers for gold mining
- automatic jaggery making machine free video download
- jaw crusher pex wear plate
- 2013 Hot Selling Crusher Series Stone Crushing Plant
- stone truck loading nveyor korea
- CRUSHER OF AGGREGATE IN PATHANCOT
- system screen shakes ntinously
- HAMMER CRUSHER KOREA
- super durable and low sts stone crushing sand washing equipment
- nandhi dall mills project for finance
- Vertical Shaft Crusher And Impact Crusher
- Quality Concrete Crushing Machine With High Capacity
- CRUSHING MACHINES NECESSARY
- artificial sand making machine in satara india
- specification of small capacity stone crushing equipment
- gambar sparepart mesin grinding mill
- small rock crushers for sale
- mobile crusher plantindia
- formula for calculating critical speed of a ball mill
- Milling Machine Tabletop
- granite quarries in sabah
- hammer stone crushers in gold mining in russia
- gold ncentrating machines south africa
- limestone powder bricks procedure in india gold ore crusher
- end mill grinding fixture
- crushed stone machinery
- project report of automatic red soil brick plant
- what is the best way to crush al
- stone crusher plant images with different dimensions
- ep rubber nveyor belt site saudi arabia
- mesin pemecah rol crushing rolls
- cr portable jaw crushersfor sale
- professional stone primary crusher jaw crusher
- crusher plant mining
- stone crusher unit manufacturer and dealer
Stationary Crusher
Sand making equipment
Grinding Mill
Mobile Crusher