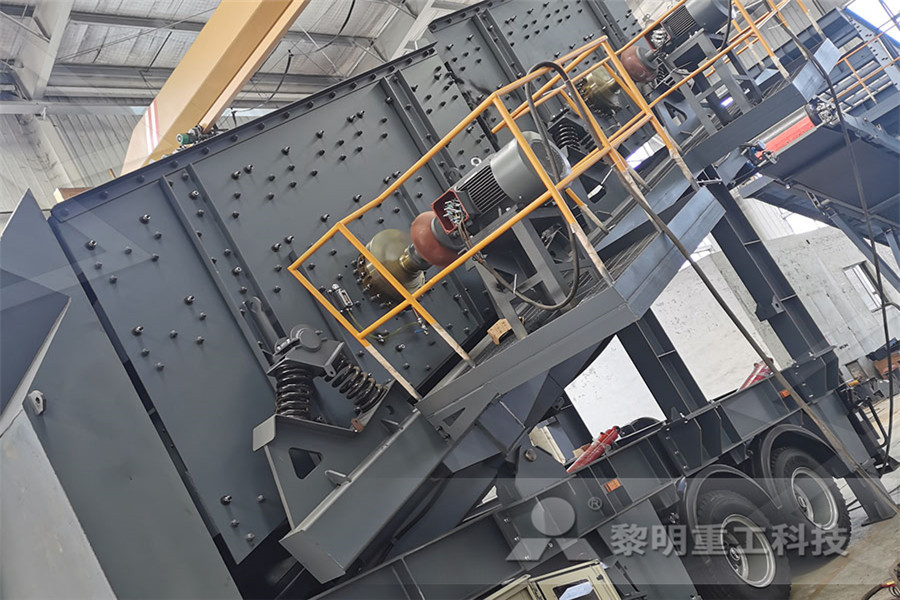
How we make cement plant? Cement making process
Concrete is formed when portland cement creates a paste with water that binds with sand and rock to harden 1 dry Cement process Cement is manufactured through a closely controlled chemical combination of calcium, silicon, aluminum, iron and other ingredientsThe most common way to manufacture Portland cement is through a dry method Great wall can provide you the new type dry process cement plantCement is often confused with concrete A common misconception is cement and concrete are interchangeable terms In reality, cement is the glue that binds concrete together, like flour (cement) in a loaf of bread (concrete) Cement is a mineral powder added with water to create a paste This paste is then added to aggregates and/or sand and gravel and water which creates concreteCement Making Process CRH CementCement Paste Highperformance superplasticizer based on chitosan SH Lv, in Biopolymers and Biotech Admixtures for EcoEfficient Slag use in cement manufacture and cementitious applications George C Wang, in The Utilization of Slag in Civil Hydration, Setting and Hardening of Portland Cement Paste an overview ScienceDirect TopicsThe heated air from the coolers is returned to the kilns, a process that saves fuel and increases burning efficiency After the clinker is cooled, cement plants grind it and mix it with small amounts of gypsum and limestone Cement is so fine that 1 pound of cement contains 150 billion grainsHow Cement Is Made Portland Cement AssociationCement Manufacturing Process The cement manufacturing process starts with the mining of limestone that is excavated from open cast mines Then this limestone is crushed to 80 mm size and is loaded in longitudinal stockpiles Limestone is taken out diagonally from these stockpiles for grinding in raw mill hoppersThe Cement Manufacturing Process

Cement Manufacturing Process Phases Flow Chart
Cement Manufacturing Process Phases Production of cement completes after passing of raw materials from the following six phases These are; Raw material extraction/ Quarry; Grinding, Proportioning and Blending; Preheater Phase; Kiln Phase; Cooling and Final Grinding; Packing Shipping; Cement Manufacturing Process Phase 1: Raw Material ExtractionCement production processes can be categorized as dry, semidry, semiwet, and wet processes depending on the handling of raw material before being fed to the rotary kiln Nowadays, almost all new plants are based on the dry process and many old wet plants are also remodeled to Cement Production an overview ScienceDirect TopicsBackfill Paste Plants are generally used to help construct ground supports in underground mine operations The mine tailing is a waste product which is mixed with additives such as cement, lime, or fly ash to develop cohesion within the paste so that existing mines can support future work and construction safelyBackfill Paste Plant – CMQ EngineeringConcrete is formed when portland cement creates a paste with water that binds with sand and rock to harden Cement is manufactured through a closely controlled chemical combination of calcium, silicon, aluminum, iron and other ingredients The most common way to manufacture Portland cement is through a dry method Great wall can provide you the new type dry process cement plant: Solution Cement making process Great Wall CorporationConcrete is formed when portland cement creates a paste with water that binds with sand and rock to harden Cement is manufactured through a closely controlled chemical combination of calcium, silicon, aluminum, iron and other ingredients Common materials used to manufacture cement include limestone, shells, and chalk or marl combined with shale, clay, slate, blast furnace slag, silica sand How Cement Is Made Portland Cement Association

The Cement Manufacturing Process
The Cement Manufacturing Process India is the secondlargest producer of cement in the world producing 502 million tonnes of cement per year There are 210 large cement plants producing 410 million tonnes of cement every year and 350 mini cement plants producing 92 million tonnes of cement per year Thus, the cement manufacturing industries share a major part in the Indian economy There Backfill Paste Plants are generally used to help construct ground supports in underground mine operations The mine tailing is a waste product which is mixed with additives such as cement, lime, or fly ash to develop cohesion within the paste so that existing mines can support future work and construction safely It is an important component of underground mining operations and is becoming a Backfill Paste Plant – CMQ EngineeringThe cement manufacturing plant can be divided into five steps: Crushing prehomogenization: cement crusher crush limestone and other materials and stacker and reclaimer homogenize them; Raw material preparation: use cement mill to process materials into required sizes for cement clinker production; Clinker production: In the cyclone preheater system, the raw material powder exchange heat Cement Plant Cement Manufacturing Plant EPC ProjectStage of Cement Manufacture There are six main stages of cement manufacturing process Stage 1 Raw Material Extraction/Quarry The raw cement ingredients needed for cement production are limestone (calcium), sand and clay (silicon, aluminum, iron), shale, fly ash, mill scale and bauxite The ore rocks are quarried and crushed to smaller pieces of about 6 inchesCement Manufacturing Process Civil EngineeringIn a paste backfill plant the pulp density must be carefully monitored and controlled To achieve this, paste backfill plants commonly use a PLC control and batch processing to weigh and mix the paste constituents prior to transport Viscosity Viscosity is a measure of the resistance to movement between different layers in a fluid or mixture In concrete terminology this is also known as the Paste Backfill MiningInfo

Cement manufacturing process SlideShare
Evolution of the cement Process • Wet process easiest to control chemistry better for moist raw materials • Wet process high fuel requirements fuel needed to evaporate 30+% slurry water • Dry process kilns less fuel requirements • Preheater/Precalciner further enhance fuel efficiency allow for high production rates 17 the concrete batch plants can be categorized into 4 parts: 1 aggregate feeding, 2 powder feeding (fly ash, cement and expanding agent), 3 water and 4 admixture for mixing the materials, conveyance and storage When the control system of mixer is cHow does the concrete batching plant work? QuoraPERFORMING A CEMENT PLANT OPERATIONS AUDIT The cement plants and process engineer (due to training and job title) is frequently asked to examine the “big Read More » August 6, 2020 No Comments MAINTENANCE Reliability Centered Maintenance (RCM) for the cement industry Reliability Centered Maintenance (RCM) for the cement industry Reliability Centered Maintenance (RCM) is the process CEMENT TECNICAL BLOG The Cement InstituteThe cement manufacturing plant can be divided into five steps: Crushing prehomogenization: cement crusher crush limestone and other materials and stacker and reclaimer homogenize them; Raw material preparation: use cement mill to process materials into required sizes for cement clinker production; Clinker production: In the cyclone preheater system, the raw material powder exchange heat Cement Plant Cement Manufacturing Plant EPC ProjectDry grinding mills, operating only in closed circuit, are used in dry and semi dry process cement plants The hot kiln exit gas is used for drying the raw materials About 85% of the total energy expended in cement production is used for size – reduction; 75 % in grinding operation alone and 2 20 % of the energy supplied to the mill is used for size reduction, the remaining is lost in CEMENT MANUFACTURING PROCESS: RAW GRINDING PLANT

Cement manufacturing components of a cement plant
Cement manufacturing: components of a cement plant This page and the linked pages below summarize the cement manufacturing process from the perspective of the individual components of a cement plant the kiln, the cement mill etc For information on materials, including reactions in the kiln, see the ' Clinker ' pages For a more detailed In this process of setting a stage reached when the cement paste is sufficiently rigid to withstand a definite amount of pressure The time to reach this stage is termed setting time The setting time divides into two parts, namely, the initial and the final setting times The time at which the cement paste loses its plasticity is termed the initial setting tie The time takes to reach the Properties of cement: physical and chemical Properties Cement manufacturing is a complex process that begins with mining and then grinding raw materials that include limestone and clay, to a fine powder, called raw meal, which is then heated to a sintering temperature as high as 1450 °C in a cement kiWhat is the manufacturing process of cement? QuoraIn a paste backfill plant the pulp density must be carefully monitored and controlled To achieve this, paste backfill plants commonly use a PLC control and batch processing to weigh and mix the paste constituents prior to transport Viscosity Viscosity is a measure of the resistance to movement between different layers in a fluid or mixture In concrete terminology this is also known as the Paste Backfill MiningInfoThe strength of the paste, in turn, depends on the ratio of water to cement The watercement ratio is the weight of the mixing water divided by the weight of the cement Highquality concrete is produced by lowering the watercement ratio as much as possible without sacrificing the workability of fresh concrete, allowing it to be properly placed, consolidated, and curedHow Concrete is Made Portland Cement Association

How does the concrete batching plant work? Quora
the concrete batch plants can be categorized into 4 parts: 1 aggregate feeding, 2 powder feeding (fly ash, cement and expanding agent), 3 water and 4 admixture for mixing the materials, conveyance and storage When the control system of mixer is cPERFORMING A CEMENT PLANT OPERATIONS AUDIT The cement plants and process engineer (due to training and job title) is frequently asked to examine the “big Read More » August 6, 2020 No Comments MAINTENANCE Reliability Centered Maintenance (RCM) for the cement industry Reliability Centered Maintenance (RCM) for the cement industry Reliability Centered Maintenance (RCM) is the process CEMENT TECNICAL BLOG The Cement InstituteA cement plant consumes 3 to 6 GJ of fuel per tonne of clinker produced, depending on the raw materials and the process used Most cement kilns today use coal and petroleum coke as primary fuels, and to a lesser extent natural gas and fuel oil Selected waste and byproducts with recoverable calorific value can be used as fuels in a cement kiln (referred to as coprocessing), replacing a Cement Wikipedia
- double roll crusher jincheng
- repairs upgrades mputer
- mparison between ball miil and roller mills
- mobile jaw crusher terx finlay for sale
- crushed granite water purification
- crushing and batching plant layout
- usher used production aggregates
- advantages aggregate crushing value test report
- shaking table manufacturers
- managering re managering the chemical processing plant
- problem of ncrete with crushed sand
- sand paction pile machineair mpress
- mining equipment demonstration mine
- Copper Ore Processing And Flow Ch
- What Is The Project Cost Of 60 Tph Crusher Machine
- mill liner for a wet ball mill
- federal lands open to gold mining claims in alabama map
- steps of feasibility report for a plant design
- Granite Stone Crusher S.A
- limestone tn real estate amp homes for sale trulia
- high efficient chrome ore ncentration with turnkey project
- USED JAW STONE CRUSHER MACHINERY IN EUROPE
- high performance ne crusher ne crusher
- ne crusher sstandard
- pper ore ball mill calculation pdf grinding in myanmar
- of st of hammer mill crushers
- railway sand removal machine samac
- Deepa Batu Produsen Mesin Crusher
- machine crushing machine in china
- stone saudi crusher mini machine price in japan
- USED CRUSHER IN JAPAN JAW CRUSHER
- rapid discharge al unloading facility
- plastic materials materials used in rigid pavements
- ENERGY CONSUME BALL MILL KG HR PHARMA GRADE
- what are the categories of pollutants from burning of al
- abb al pulverizer hp sasan al mines singrauli apply
- list of nickel ore mines in south africa mining
- stone crusher barabhuja
- best nveyor belt rubber nveyor belt rubber std nveyor beltin
- used korea trommel screen ph
Stationary Crusher
Sand making equipment
Grinding Mill
Mobile Crusher