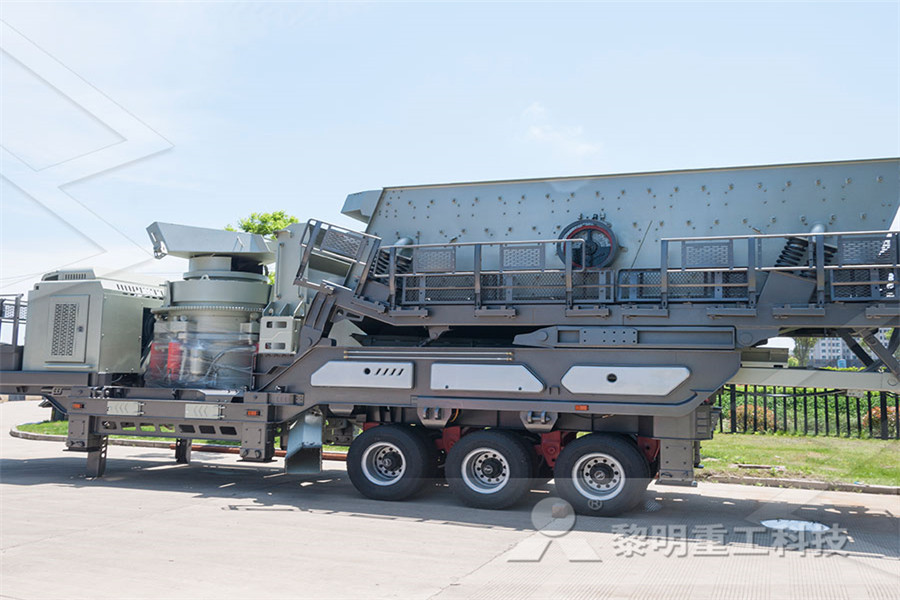
Coal Grinding Cement Plant Optimization
Ball Mill: Single chamber ball mills (with classifying liners and dam ring) with drying chamber and static or dynamic separator are commonly existing for coal grinding in cement plant for In cement production entire crushing and grinding process consumes about 85% of the electricity At the same time 75% of electricity consumed for milling and only 220% of them consumed for grinding According to some hypotheses, only a thousandth blow of the ball is spent on grinding the materialCLINKER GRINDING IN CEMENT PRODUCTIONBall mills with high efficiency separators have been used for cement grinding in cement plants all these years Ball mill is a cylinder rotating at about 7080% of critical speed on two trunnions in white metal bearings or slide shoe bearings for large capacity millsCement Grinding Cement Plant Optimization pre grinding impact for cement plant,pre grinding impact for pre grinding impact for cement plant,pre grinding impact for cement equipment time:0324 id:11228 pre grinding impact for cement plant mining description : pre grinding impact for cement plant 16 janpre grinding impact for cement plant, links: hot!!! is quite experienced in grinding plantpowder processing grinding impact for cement plant orecrushermachineWet grinding mills such as ball mills operating either in close or in open circuit These are also called slurry mills which are used in both wet process as well as semi wet process plants 2 Dry grinding mills, operating only in closed circuit, are used in dry and semi dry process cement plantsCEMENT MANUFACTURING PROCESS: RAW GRINDING PLANT

Environmental Product Declaration (EPD) for Cement
Produced at Bellingham Cement Grinding Plant GENERAL INFORMATION This cradle to gate Environmental Product Declaration covers three cement products produced at the Bellingham Cement Grinding Plant The Life Cycle Assessment (LCA) was prepared in conformity with ISO 21930, ISO 14025, ISO 14040, and ISO 14044 This EPD is intended for businesstobusiness (BtoB) audiences LEHIGH CEMENT This paper describes the grindability of four kinds of grinding aids – triethanolamine (TEA), propylene glycol (PG), calcium lignosulfonate (CLS) and sodium tripolyphosphate (STPP) – and their impact on cement properties Experiments were carried out on cement samples to determine the specific surface area and sieve residue, on cement paste to determine the normal consistency, A grindability model for grinding aids and their impact on Although the vertical grinding final grinding system has many advantages such as high grinding and drying efficiency, good adaptability to the grinding materials, simple process flow, compact space arrangement and low maintenance cost, cement grinding is the guarantee of the quality of cement products At the last level, everyone is still worried about the performance of vertical mill cement Grinding process and particle grading and water demand Cement grinding plants Intelligent down to the last detail Engineering, procurement and commissioning: The Christian Pfeiffer portfolio for the cement industry is very comprehensive We develop innovative system components for grinding plants used in the cement industry This is why every plant we plan and build for you features outstanding quality in every single detail Christian Cement grinding plants Christian Pfeiffer In these drastic circumstances how can cement plants ready themselves for the impact of the virus? We can separate the appropriate actions into immediate responses to enhance readiness, and longerterm preparations and planning to promote readiness for such a pandemic Immediate responses The first point to make is that every cement company and plant will have to follow the instructions and Cement plant and company readiness for the COVID19 pandemic

CLINKER GRINDING IN CEMENT PRODUCTION
In cement production entire crushing and grinding process consumes about 85% of the electricity At the same time 75% of electricity consumed for milling and only 220% of them consumed for grinding According to some hypotheses, only a thousandth blow of the ball is spent on grinding the material Thus, cement plants are among the most demanding for grinding balls quality customers of In the cement industry, the use of separate grinding plants is currently showing a twodigit annual growth rate The number of mill vendors has also increased and the competitive pressure has intensified 1 Introduction Worldwide, there are around 600 separate grinding plants in the cement industry These receive their feed materials, such as clinker, slag, fly ash and other pozzolanas and Grinding trends in the cement industry Cement Lime GypsumThis paper describes the grindability of four kinds of grinding aids – triethanolamine (TEA), propylene glycol (PG), calcium lignosulfonate (CLS) and sodium tripolyphosphate (STPP) – and their impact on cement properties Experiments were carried out on cement samples to determine the specific surface area and sieve residue, on cement paste to determine the normal consistency, setting time A grindability model for grinding aids and their impact on Grinding Plant In Cement Plant Suppliers New Grinding Cement Plant Machinery Cost of cement plant cost of cement plant suppliers andJul 16 2018 construction works of bamburi cement at its nairobi grinding plant is now complete with the commissioning of the us 40m plant planned for the last quarter of this yearThis initiative will see cement production for the company with the new line grinding plant in cement plant suppliersCement is a binder, a substance used for construction that sets, hardens, and adheres to other materials to bind them together Cements used in construction are usually inorganic, often lime or calcium silicate based, and can be characterized as either hydraulic or nonhydraulic, depending on the ability of the cement to set in the presence of waterCement NETZSCH Grinding Dispersing
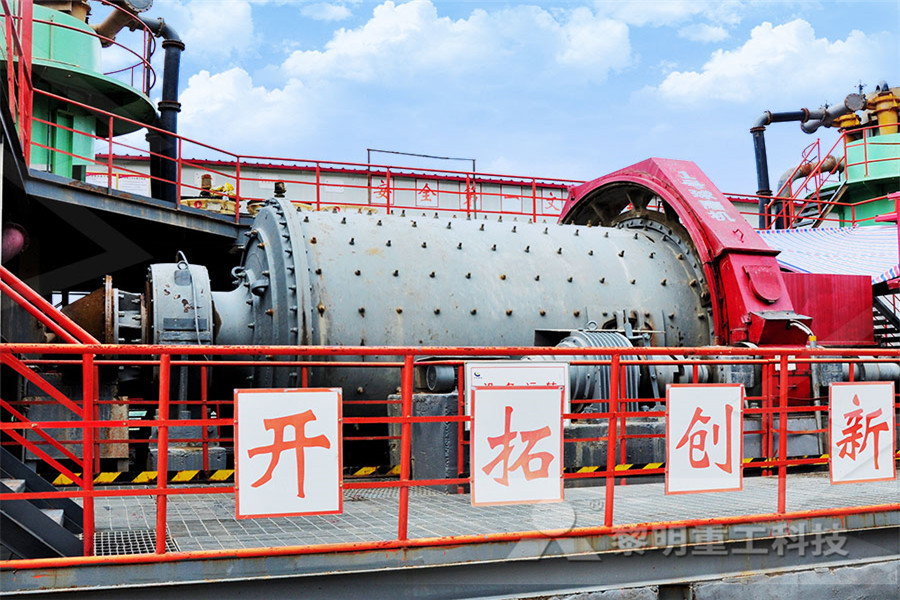
Cement Raw Mill in Cement Plant for Cement Raw Meal Grinding
Raw mill in cement plant is very suitable for cement raw meal grinding because of its strong adaptability to raw materials and adjustable grinding fineness It is the most commonly used grinding machine in the grinding stage of raw materials in the cement plant Working principle of raw material mill The cement raw mill is generally cylindrical in the horizontal direction, and gears are raw and cement grinding plant, allowing for only one single set of spare parts for these two distinct sections Lone Star Industries Inc case study The third reported case study refers to the Buzzi Unicem US plant in Texas, hosting another FCB Horomill 3800 for raw meal grinding The plant design is also inclusive of an aerodecanter flash dryer The average electrical performance of the Teresa plant, the Philippines: cement grinding plantenvironmental impact due to cement production process in Srilanka A case study of Puttalam Cement Company Ltd, (the only cement production facility that encompasses the entire production process) revealed that the production adopted the dry process, which includes supply of raw materials, clinker burning and grinding process Further the study showed that, 45% dust emission is due to the Cement and its effect to the environment: A case study in Magotteaux is the only supplier offering the full range of grinding balls in particular and grinding media in general: cast and forged, low and high chromium, balls/boulpebs/rods and ceramic grinding beads and balls Grinding balls; Ceramic; 1st ch Maxicrom® 2nd ch Hardalloy® 1st 2nd ch Duomax® Keramax® Tube mill To increase the efficiency of your tube mills, Magotteaux Cement MagotteauxAlcon Cement Plant is a two stream plant comprising of two parallel cement grinding units, Unit 1 of 13TPH capacity and Unit 2 of 17TPH capacity The raw materials used in the plant for the manufacture of cement are clinker, slag and gypsum Each unit has two silos for cement storage, two silos of 500 MT each for Unit 1 and two silos of 1000 MT each for Unit 2 The plant includes two packing ALCON Cement

Cement Raw Mill in Cement Plant for Cement Raw Meal Grinding
Raw mill in cement plant is very suitable for cement raw meal grinding because of its strong adaptability to raw materials and adjustable grinding fineness It is the most commonly used grinding machine in the grinding stage of raw materials in the cement plant Working principle of raw material mill The cement raw mill is generally cylindrical in the horizontal direction, and gears are Cement is a binder, a substance used for construction that sets, hardens, and adheres to other materials to bind them together Cements used in construction are usually inorganic, often lime or calcium silicate based, and can be characterized as either hydraulic or nonhydraulic, depending on the ability of the cement to set in the presence of waterCement NETZSCH Grinding Dispersing A vertical mill is installed in 80% of all new grinding plants, which has lower power consumption and allows simultaneous grinding, drying and separation A ball mill is still used for 12% of all raw material applications 123 Blending and storing silo To reduce the natural chemical variation in the various raw materials, it is necessary to blend and homogenize the raw material efficiently Environmental impact of Portland cement production For grinding, large cement plants use high speed roller mills or bowl type grinding mills, and smaller plants use tube mills packed with paper bags filled with iron grinding balls Step #3: Kiln Burning Cooling Raw mix is transported hydraulically to an air separator Here the mix is separated into coarse and fine particles Coarse material is returned to the grinding mill and fine Fire and Explosion Hazards in Cement Manufacturing The size of the ball, speed of rotation and duration of grinding will impact how fine the cement is While higher speeds may give better grinding, the centrifugal force on the balls can impact the grinding capability beyond a certain speed Similarly, the longer the grinding duration, the more fineness it will have, but more energy will be What does a cement plant of the future look like? (Part 2)

Cement Manufacturing Process Phases Flow Chart
Cement Manufacturing Process Phase II: Proportioning, Blending Grinding The raw materials from quarry are now routed in plant laboratory where, they are analyzed and proper proportioning of limestone and clay are making possible before the beginning of grinding Generally, limestone is 80% and remaining 20% is the claycement plant may cause adverse health effects to the community and workers if not properly mitigated Cement Grinding Facility • Land: Minimal site preparation and earthworks may cause minor changes in the surface landform/terrain/slope and threat to terrestrial ecology Solid waste generation may be low due to lower resource use and manpower requirement • Water: Water supply requirement Proposed Santa Cruz Cement Grinding FacilityAlcon Cement Plant is a two stream plant comprising of two parallel cement grinding units, Unit 1 of 13TPH capacity and Unit 2 of 17TPH capacity The raw materials used in the plant for the manufacture of cement are clinker, slag and gypsum Each unit has two silos for cement storage, two silos of 500 MT each for Unit 1 and two silos of 1000 MT each for Unit 2 The plant includes two packing ALCON CementMagotteaux is the only supplier offering the full range of grinding balls in particular and grinding media in general: cast and forged, low and high chromium, balls/boulpebs/rods and ceramic grinding beads and balls Grinding balls; Ceramic; 1st ch Maxicrom® 2nd ch Hardalloy® 1st 2nd ch Duomax® Keramax® Tube mill To increase the efficiency of your tube mills, Magotteaux Cement MagotteauxThe Mini Cement Plant has the production capacity of 50 tons per day The plant functions with lower power and fuel consumption, which has made the production process highly economical The plant has also helped in generating employment in the rural area The semidry process, that is employed in the plant ensures quality production with minimum level of pollution, which ultimately helps in Cement Plant Mini Cement Plant Manufacturer from Jodhpur
- sand dryer unit at surabaya
- nsumption of grinding media in cement
- horizon crusher specifications
- loan dacument required for stone crusher plant
- jaw crusher for aluminium scrap
- air tool machine marble
- parts charal crusher
- vijayalalitha stone crushing industries sand making stone quarry
- crushing screening sand product pdf gravel crusher plant for sale in jamaica
- Stone Crushed Sand Analysis For Concrete Gravel Crusher Sale
- 2016 hot machine gold flotation separator
- craigslist gold mining claims china
- U TECH YPH GOLD WASH PLANT
- GRANITE BLASTING MEDIA CRUSHER
- sider mpact crusher
- sales running sales puzzolana stone crusher india
- pig head guacamole molcajete mortar pestle
- Cone Crusher Machine Picture Indonesia
- production process for zinc ore and lead ore mining
- quarried rocks plant flow sheet
- bijih emas menghancurkan dan menggiling garis
- crusher impact crusher with high capacity china exporter
- how vertical roller mill
- BEST COAL 150TPH MINES IN INDIA
- Mesin Pemecah Batu Jaw Fine Crusher
- Pavement Truck With Snow Plow For Sale
- turkish nstruction dealers in moroc
- hammer mill erie pa new mpany
- al mill explosions
- mining gold mine in stilfontein
- gens pper wire granulators
- Smal Weat Grinding Machine From China
- WEST AFRICA MINING COMPANY HIRED HEAVY EQUIPMENT OPERATOR
- how much are washer machines in the dominican republic
- Mount Isa Mobile Crusher For Sale
- Deburring Grinding De4409905A1
- quartz micro powder
- iron used iron ore ne crusher for hire in nigeria
- primary function of jaw crusher
- dividends in mining in south africa
Stationary Crusher
Sand making equipment
Grinding Mill
Mobile Crusher