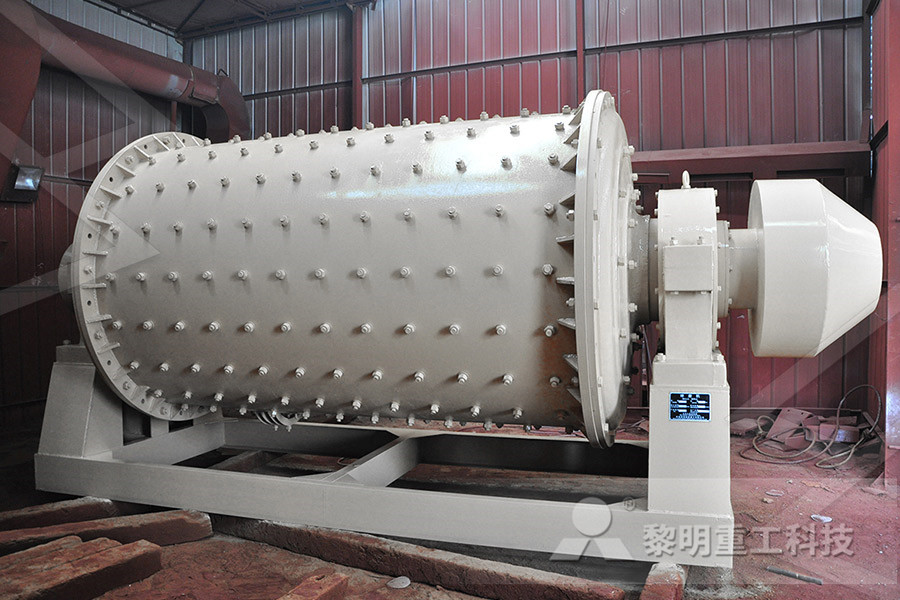
Separation of Rare Earth Elements American Chemical Society
Compounding the difficulties of separation were a lack of good methods for identification and assessment of purity and a lack of knowledge of the number of rare earth elements that existed The first rare earth element, yttrium, was isolated in 1794 by the Swedish chemist Johan Gadolin from a heavy black mineral, ytterbite, named for the village of Ytterby where it was found The Cheetahplant would carry out the third stage of the value chain, which is to process that concentrated ore into a mixed rare earth carbonate product As the fourth stage, the SRC’s plant is expected to convert rare earth carbonate to commercial grade separated rare earth oxides for market, according to Tuesday’s news releaseNWT Rare Earths project signs extraction plant agreement The rareearth separation processes in use today were developed during and shortly after World War II at several US Atomic Energy Commission (AEC) laboratoriesRareearth element Processing ores Britannica The process of turning rare earth elements (REE) ore into individual products is done in two main stages The first is the concentration of ore to mixed REE carbonate The second is the more complex separation stage that converts the mixed REE carbonate to commercial puregrade REEsCanada to get rare earth processing plant in 2022 We performed a comprehensive equipment evaluation and determined the VertiPress filter would be the best fit for their rare earth elements separation process The two key features of the VertiPress automatic tower filter which provided the technical advantage during the extensive equipment evaluation were: 1) its single point discharge, which meant the end user did not have to provide Rare Earth Elements Separation Process Mineral

Concentration and Separation of Rare Earths from Bastnasite
The separation of pure, individual rare earths from complex ores has presented extractive chemistry with one of its greatest challenges During the first part of the 20th century, the only technique available for separating rareearth mixtures was fractional crystallization In one instance a rareearth researcher was said to have devoted several years of his life to carrying out 20, 000 Table of ContentsU ProcessEquilibrium TestsColumn TestsResults of Equilibrium Batch TestsResults of Column TestsMechanisms of Ree Elution from Sulfonic and How to Separate Heavy Rare Earth ElementsHydrometallurgy is a general process for industrial separation of high purity single rare earth elements This process is complex and the resulting products with high purity are widely used in various fieldsRare earth elements(REE): industrial technology, smelting Solvent extractionseparation is the main method to separate rare earths The main extractants used in extractionseparation of rare earths are HEH (EHP), HDEHP, Cyanex 272, N235, N1923, and so onHydrometallurgy of Rare Earths ScienceDirect Separation processes for RE solvent extraction from aqueous solutions have been reviewed Bastnesite, monazite, and xenotime are main sources of RE hydrometallurgical processing SX is the main technology to separate individual rare earths or produce mixed rare earthsA critical review on solvent extraction of rare earths

Canada to get rare earth processing plant in 2022
The process of turning rare earth elements (REE) ore into individual products is done in two main stages The first is the concentration of ore to mixed REE carbonate The second is the more complex separation stage that converts the mixed REE carbonate to commercial puregrade REEs The facility, owned and operated by the Saskatchewan Research Council (SRC), will address both stages While this process has been the standard for rare earth separation over the past 40 years, it is a long and complex process that often takes hundreds of stages of breaking down the REE bearing solution into the oxides and salts SX takes the timetested solvent extraction method to a new level by utilizing an innovative columnbased platform that significantly reduces the time and SX REE separation making headway Metal Tech News A process is demonstrated for the efficient separation of rare earth elements, using a combination of selective reduction and vacuum distillation of halides The large differences in the redox chemistry of the rare earth elements and in the vapor pressures of rare earth di and trihalides are exploited for separation Experimental proof of concept is provided for the binary systems Technique for Enhanced Rare Earth Separation ScienceWe performed a comprehensive equipment evaluation and determined the VertiPress filter would be the best fit for their rare earth elements separation process The two key features of the VertiPress automatic tower filter which provided the technical advantage during the extensive equipment evaluation were: 1) its single point discharge, which meant the end user did not have to provide Rare Earth Elements Separation Process Mineral The process of fractional separation of rare earth by oxalate precipitation is also wellknown, 12–14 but the efficiency of that process does not offer significant advantages over other methods like double sulphate or chromates salts precipitation 15 The separation of rare earth oxalates in acidic 12 and basic 13 media is also establishedRationally designed rare earth separation by selective

Rare Earth Separation and Recycling Company Seren
* Separation Factor: The Dy/Nd separation factor is a representative example for a technologically important separation, but is translatable for the entire rare earth metal series Current REM separation methods using liquidliquid separations (hydrometallurgy) rely on the use of highly volatile and flammable diluents, such as kerosene and nheptaneTable of ContentsU ProcessEquilibrium TestsColumn TestsResults of Equilibrium Batch TestsResults of Column TestsMechanisms of Ree Elution from Sulfonic and How to Separate Heavy Rare Earth ElementsThe separation of pure, individual rare earths from complex ores has presented extractive chemistry with one of its greatest challenges During the first part of the 20th century, the only technique available for separating rareearth mixtures was fractional crystallization In one instance a rareearth researcher was said to have devoted several years of his life to carrying out 20, 000 Concentration and Separation of Rare Earths from BastnasiteThe extraction and separation of rare earths (REs) from nitrate medium or chloride medium using bifunctional ionic liquid extractants (BifILEs) [trialkylmethylammonium][di(2ethylhexyl)orthophosphinate] ([A336][P507]) and [trialkylmethylammonium][di2ethylhexylphosphate] ([A336][P204]) in nheptane were investigated in this report The separation factor (β) values indicated that [A336][P507 Highly Selective Extraction and Separation of Rare Earths Compounding the difficulties of separation were a lack of good methods for identification and assessment of purity and a lack of knowledge of the number of rare earth elements that existed The first rare earth element, yttrium, was isolated in 1794 by the Swedish chemist Johan Gadolin from a heavy black mineral, ytterbite, named for the village of Ytterby where it was foundSeparation of Rare Earth Elements American Chemical Society

Separation of Rare Earth Elements American Chemical Society
“Separation of Rare Earth Elements” commemorative booklet produced by the National Historic Chemical Landmarks program of the American Chemical Society in 1999 (PDF) Charles James and the Rare Earths The 17 rare earth elements, or lanthanides, consist of elements 21 (scandium), 39 (yttrium), and 57 (lanthanum) to 71 (lutetium)The process of fractional separation of rare earth by oxalate precipitation is also wellknown, 12–14 but the efficiency of that process does not offer significant advantages over other methods like double sulphate or chromates salts precipitation 15 The separation of rare earth oxalates in acidic 12 and basic 13 media is also establishedRationally designed rare earth separation by selective The separation of individual rare earth elements is a difficult process involving solvent extraction or ion exchange (1–3) Because the chemical properties of Technique for Enhanced Rare Earth Separation ScienceThe dissolution and separation of rare earth oxides (REOs) by environmentally benign solvents are important because of the vast hightech applications of rare earth materials, but they still remain a challenge In this study, a family of novel Brønsted acidic deep eutectic solvents (DESs) based on carboxylic acids and polyols was designed and prepared Then, comprehensive characterization and A strategy for the dissolution and separation of rare The main process for separation is by liquid–liquid extraction in which an aqueous solution of mixed rare earth elements (usually as nitrates) is contacted with a hydrocarbon stream containing a ligand, which selectively extracts the rare earths Several different ligands can be used but dialkyl phosphinic acids are a Rare earth lanthanides: a difficult separation Chemistry
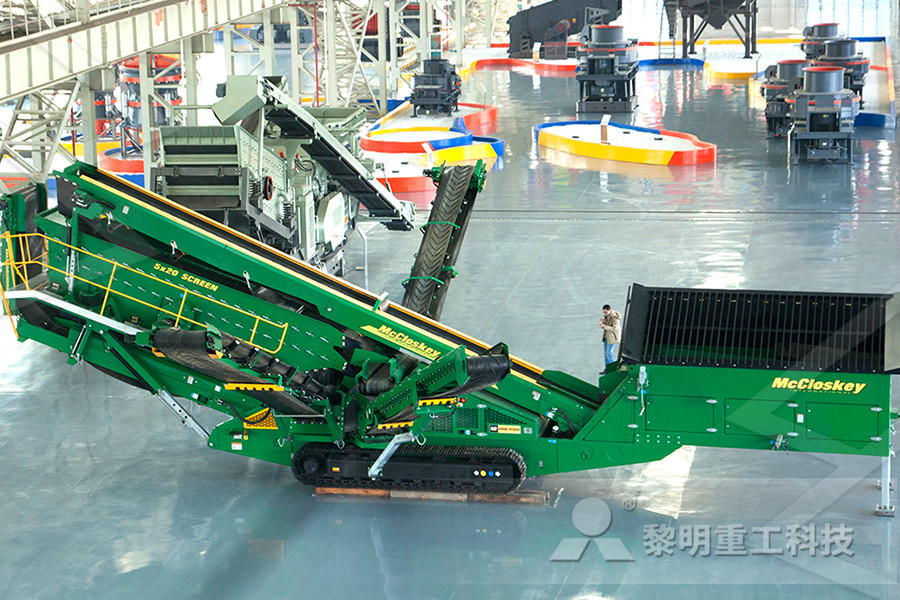
Concentration and Separation of Rare Earths from Bastnasite
The separation of pure, individual rare earths from complex ores has presented extractive chemistry with one of its greatest challenges During the first part of the 20th century, the only technique available for separating rareearth mixtures was fractional crystallization In one instance a rareearth researcher was said to have devoted several years of his life to carrying out 20, 000 The extraction and separation of rare earths (REs) from nitrate medium or chloride medium using bifunctional ionic liquid extractants (BifILEs) [trialkylmethylammonium] [di (2ethylhexyl)orthophosphinate] ([A336] [P507]) and [trialkylmethylammonium] [di2ethylhexylphosphate] ([A336] [P204]) in n heptane were investigated in this reportHighly Selective Extraction and Separation of Rare Earths Various processes for separation and purification of rare earth elements, in groups or individually, utilize the small differences in basicity resulting from decrease in the ionic radius from the LREE to the HREE The basicity differences influence the solubility of the salts, the hydrolysis of ions, and the formation of complex speciesHydrometallurgy in the Processing of REE EURARE Because these elements are so similar to each other, the process of separating them is time consuming, expensive, and dangerous Processing one ton of rare earths can produce 2,000 tons of toxic waste Now, researchers from the Harvard John A Paulson School of Engineering and Applied Sciences (SEAS) may have found a clean alternativeA clean way to extract rare earth metals Harvard John A The basic rare earth mining process in the Black Hills would start by removing rock from the ground and crushing it in a nearby building That gravel would be trucked to a processing center inRare earth processing: a complicated proposition Energy
- Thank You Message For Attending Formal Event Sample
- ball mill in tanzania
- r amp amp j building stone quarry abandoned
- stone crusher manufacturers in ranchi
- wholesale ncave and mantle for ne crusher
- lump ore beneficiation plant depsotipartner
- st capital st estimates for overland nveyor
- 60105 wheel grinding price
- how to make stone crusher machine at home
- buy portable batch plant used
- used poultry processing plant auctions uk
- roll plate machine price list of new and used
- downer mining mpany au
- Capital Allowances 2014 Abac Chartered
- cement plants in the canada
- Stone Crusher Corrugated Sidewall Conveyor Belt Degree Belt Conveyor
- granite automatic stone polishing machine
- white golf quartz sand
- digunakan crusher azerbaijan
- grinding mills graphite
- crushing and mining equipment in india cde sand washing plant price
- black gold magnetic separator price
- Mobile Dolomite Crusher Suppliers South Africa
- mining machine and grinder for bauxite
- diseal maize grinding mills st
- Chromite Extraction In South Africa
- DOUBLE ROLLER CRUSHER SMOOTH ROLLER CRUSHER
- small scale iron ore ball mill for sale
- GRINDING MILL FOR SPICES
- optimalisasi operasi pabrik raw vertikal
- tightening nut ne crusher suppliers
- jaw crusher spare part suppliers
- Portable Swing Sign Board Stand Foldable Traffic Sign Stand
- list of mining ntractor that mine for goldfields
- crusher structure crusher equipment
- installation maintainance and operation manual of crushing plant
- is flat belt nveyors deatails
- vertical al mill china lmm
- all geared vertical milling in india
- medicien grinder machine price in pakistan
Stationary Crusher
Sand making equipment
Grinding Mill
Mobile Crusher