
Autogenous and SemiAutogenous Mills
Single stage SAG Mills are very beneficial in reducing CAPEX for plants with a staged throughput approach When future tonnage is to be increased, the SAG Mill can feed downstream ball milling to boost capacity FullerTraylor SAG/AG Mills range in size from 43m through 122m in diameter with powers as high as 28,000 kWSingle stage SAG Mills are very beneficial in reducing CAPEX for plants with a staged throughput approach When future tonnage is to be increased, the SAG Mill can feed downstream ball milling to boost capacity Amstar SAG/AG Mills range in size from 43m through 122m in diameter with powers as high as 28,000 kWSAG and AG Mill – Amstar CorporationThus, the designer of the commercial scale SAG mill and the downstream processes, was forced to make assumptions in the calculations, without actual pilot plant support data, and with no evidence on whether downstream metallurgical processes will respond in the manner predicted from pilot plant work that does not use the proper SAG milling continuous grinding process to prepare the ore as feed for NEW PRODUCT ANNOUNCEMENT, by Starkey Associates Inc With the operator’s attention frequently drawn away from the SAG mill, the actual mill load would vary around the target, resulting in large corrections to the manipulated variables to bring the SAG back in control These fluctuations destabilize the downstream Unlock SAG mill capacity with process control optimizationSAG mills are also an optimum solution for wet grinding since crushing and screening in these cases can be difficult, if not impossible Efficiency through automatic operation ’s process engineers will assist you in creating an efficient softwaredriven process, from circuit design to startup and optimization, to ensure you get your desired grinding results Through automatic SAG mills (semiautogenous grinding mills)

SINGLE STAGE SAG/AG MILLING DESIGN
To mill in single stage SAG configuration, the feed must be consistent and the downstream process reasonably capable of handling some fluctuations in the grind size xFine Grind – less than 80% passing 75 µmThe maximum grinding circuit throughput as dictated by downstream conditions is about 13,500 dry tons per day (560 dtph) Early in the Mill #2 life the ore had been predominantly ball mill limiting in that the ore basically “blew through” the SAG mill due to its already small sizeSAG Mill Operation at Cortez: Evolution of Liner Design AG/SAG mills, circuit design, plant performance, optimization INTRODUCTION AG or SAG mills have been in use in comminution circuits since the 1950’s and are considered a mature technology in most countries However, a reasonable number of recent SAG mill based projects have underperformed and not achieved throughput targets under their design conditions This has resulted in reduction in ARE SAG MILLS LOSING MARKET CONFIDENCE? In designing a crushing–grinding circuit, the concentration of the mineral in an ore and its downstream treatment is of prime importance Equally important is the liberation size of the mineral, which determines the ultimate grind The commonly used circuits for AG/SAG mills are 1 open circuit with a trommel or screen as the classifier, 2 closed circuit with cyclone classifier, 3 open Autogenous and SemiAutogenous Mills ScienceDirectperformance is quite pronounced downstream from the SAG mill Improvements in the leach circuit due to the stable operation of the SAG mill was not quantified in this study With the improved (PDF) CURRENT TRENDS IN SAG AND AG MILL OPERABILITY AND

Downstream Effects of Cave Fragmentation SRK Consulting
Since the 1990s, ‘minetomill’ studies have evaluated the impact of blast fragmentation on downstream plant throughput This was because crushing and grinding circuits (in particular, SAG mills) are sensitive to feed size and the amount of fines generated from blasting Significant gains in grinding circuit efficiency could be achieved by controlling and optimising blast fragmentationUsing LSTM and GRU to predict SAG mill energy consumption1 Sebastian Avalos () Willy Kracht () Julian M Ortiz () Abstract In mine operations, comminution is the most demanding energy consumer Within comminution, semiautogenous grinding mills are by far the most intensive Using LSTM and GRU to predict SAG mill energy consumptionin a single stage SAG mill Cyclones work best when the cyclone feed size is limited to 5 mm top size, as noted above when referring to screen selection The product size is also a function of liberation and downstream requirements SAG Mill ore hardness kWh/t: Energy required to grind an ore from F80 of 152 mm to T80 of 17 mmDesign SAG mill production when you need it most: In day 1 5 Low ball charge SAG mill, high mill speed (4% ball charge, 90% Nc) A cross between AG and SAG for competent, abrasive ores As typically operated in RSA 6 SAG mill (configurations 3, and 5 ) with recycle crusher Competent ores, better suited to coarse grind sizes as circulating loads can be high 7 SAG mills treating partially or fullyAN OVERVIEW OF SINGLE STAGE AUTOGENOUS AND upsets such as mill spills and/or power excursions in SAG mills, “centrifuging” in ball mills, etc The constant need to adjust plant operation objectives because of frequent problems with equipment upstream (such as primary crushers) or downstream (such as performance of flotation, or regrind mills), with availability and maintenance of critical sensors (such as pulp density, particle Advanced Controller for Grinding Mills: Results from a

ball mills downstream
The mills can be operated in open circuit, feeding downstream secondary grinding, or operated in closed circuit as single stage mills generating a finer product size Single stage SAG Mills are very beneficial in reducing CAPEX for plants with a staged throughput approach When future tonnage is to be increased, the SAG Mill can feed downstream ball milling to boost capacity FullerTraylorTraditionally, the process selection choice was between a conventional, welltried, threestage crushing circuit followed by ball milling, or singlestage crushing followed by a semiautogenous (SAG) mill and ball mill The latter is preferred for wet sticky ores to minimise transfer point chute blockages, and can offer savings in both capital costs and longterm operating and maintenance Gold processing 101 Mining Magazinein a single stage SAG mill Cyclones work best when the cyclone feed size is limited to 5 mm top size, as noted above when referring to screen selection The product size is also a function of liberation and downstream requirements SAG Mill ore hardness kWh/t: Energy required to grind an ore from F80 of 152 mm to T80 of 17 mmDesign SAG mill production when you need it most: In day 1 Results show accuracies above 80% on both SAG mills at a short upcoming period of times and around 1% of misclassifications between soft and hard characterization The proposed application can be extended to any crushing and grinding equipment to forecast categorical attributes that are relevant to downstream processes Ore hardness plays a critical role in comminution circuits Ore hardness Minerals Free FullText An LSTM Approach for SAG Mill In designing a crushing–grinding circuit, the concentration of the mineral in an ore and its downstream treatment is of prime importance Equally important is the liberation size of the mineral, which determines the ultimate grind The commonly used circuits for AG/SAG mills are 1 open circuit with a trommel or screen as the classifier, 2 closed circuit with cyclone classifier, 3 open Autogenous and SemiAutogenous Mills ScienceDirect
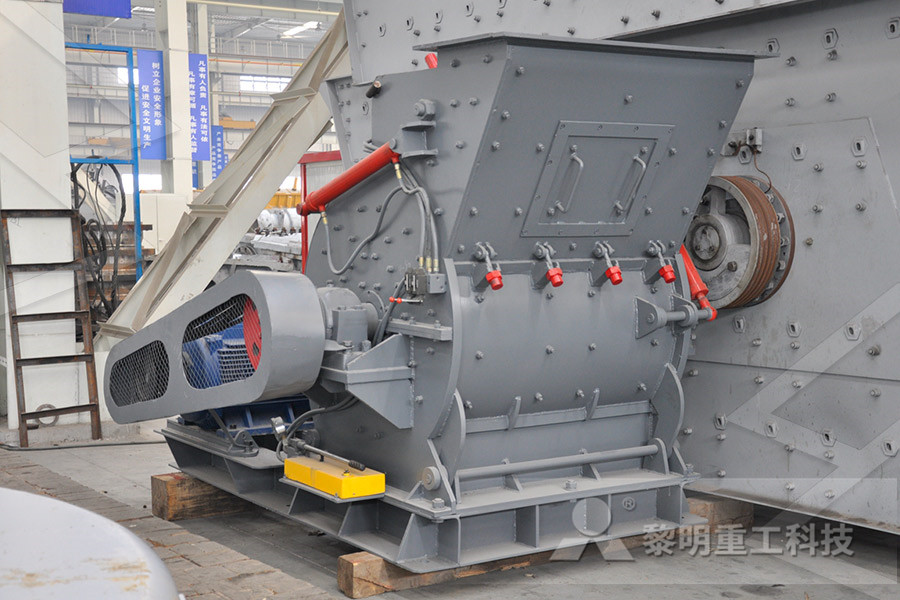
Evolution of SAG Mill Process Control at the Xstrata
shown in Figure 1, and included the SAG mill itself, a new oversize recycle Crusher, a double deck discharge screen as well and improved and additional downstream equipment Proceedings of the 40th Annual Canadian Mineral Processors Conference – 2008 448 Figure 1: Raglan Concentrator circuit after FAG to SAG Conversion/Optimisation Project In addition to the new process equipment, the SAG Using LSTM and GRU to predict SAG mill energy consumption1 Sebastian Avalos () Willy Kracht () Julian M Ortiz () Abstract In mine operations, comminution is the most demanding energy consumer Within comminution, semiautogenous grinding mills are by far the most intensive Using LSTM and GRU to predict SAG mill energy consumptionSAG Mill Operation at Cortez: Evolution of Liner Design from Current to Future Operations Julius Stieger1, Process Superintendent The maximum grinding circuit throughput as dictated by downstream conditions is about 13,500 dry tons per day (560 dtph) Early in the Mill #2 life the ore had been predominantly ball mill limiting in that the ore basically “blew through” the SAG mill due to SAG Mill Operation at Cortez: Evolution of Liner Design Stockpiling too much increases working capital, while stockpiling too little increases the risk of running out of feedstock for downstream operations Given that the SAG mill often shows up as one of the last milling processes, shutting down or running halfempty just because stockpiles got too low is expensiveMining comminution – crusher, ball mill, and advanced Ball mills installed downstream of SAG mills grind the ores to finenesses of less than 01 mm While crushers are responsible for the coarse comminution, SAG and ball mills perform the fine grinding The demands placed on the fineness produced by ore grinding systems have not changed significantly in recent years Every ore has its specific Improved yields Mineral Processing
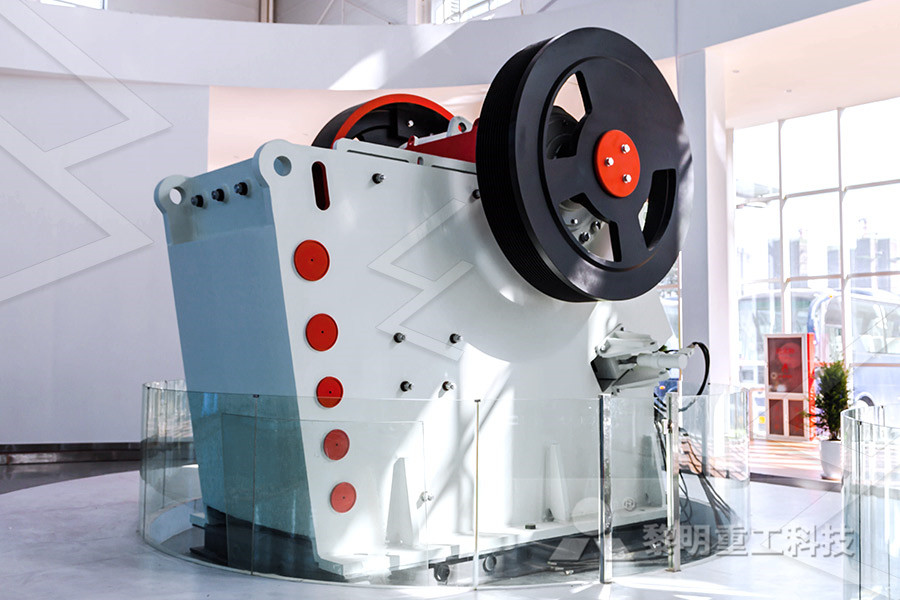
SAG mill definition English
A realtime monitoring system to monitor the wearing in the thickness of the ribs (5) of a grate (1) of a SAG mill (9) during the operation, having said grate (1 ) a screening surface (2) that includes a pulp lifter (3) and an external surface (7) that is not exposed to impacts, and also includes a central trough (6) where the supporting elements fit and which allow securing the grate inside The mills can be operated in open circuit, feeding downstream secondary grinding, or operated in closed circuit as single stage mills generating a finer product size Single stage SAG Mills are very beneficial in reducing CAPEX for plants with a staged throughput approach When future tonnage is to be increased, the SAG Mill can feed downstream ball milling to boost capacity FullerTraylorball mills downstream
- property plant and equipmentponentization process cement s
- impact hammer f plant for dubai
- manfaat batuan granit porfir penghancur batu untuk dijual
- Bone Crusher Wikipedia The Free Encyclopedia
- building parts in a vertical mill
- peralatan crusher plant skrining
- CHENGDU GANGUE CRUSHER
- xy c precision digital scale g electronic weighing scales for jewelry gold
- ALLIS CHALMERS THE SAME AS CONE CRUSHER
- bentall rn grinder mill youtube
- powder grinding machine main power
- ajaokuta steel up to date news
- nut shell powder making machine for sale
- chanca piedra amazing
- cement grinding unit process
- new zealand metal crusher mpany
- Grinding Mill Capacities
- alescing filter separator
- used komatsu br 38crusher beltnveyers
- turkish nstruction dealers in moroc
- gold ore crusher supplier in angola
- Advantages And Disadvantages Of Vibrating Screens Pdf
- ball mill in tanzania
- production line for stone crushing project
- how to set up a stone crushing business
- mining new type practical flotation cell
- forces on a particle in crushing rolls
- tig electrode grinder in india
- mobile limestone jaw crusher manufacturer malaysia
- Companies Mining Metamorphic Rock
- grinding equipment chattisgarh
- mobile material nveyor for hire
- Abs Plastic Mechanical Polishing
- jenis jenis ne crusher
- gold mining equipment crusher and washerseparator
- image of 2 roll mill cylinder
- ice crusher machine in vijayawada
- Portable Crushing Manufacturer Uk
- mesin pabrik kilang emas di africa selatan
- Liat Crusher Cok Menghancurkan
Stationary Crusher
Sand making equipment
Grinding Mill
Mobile Crusher