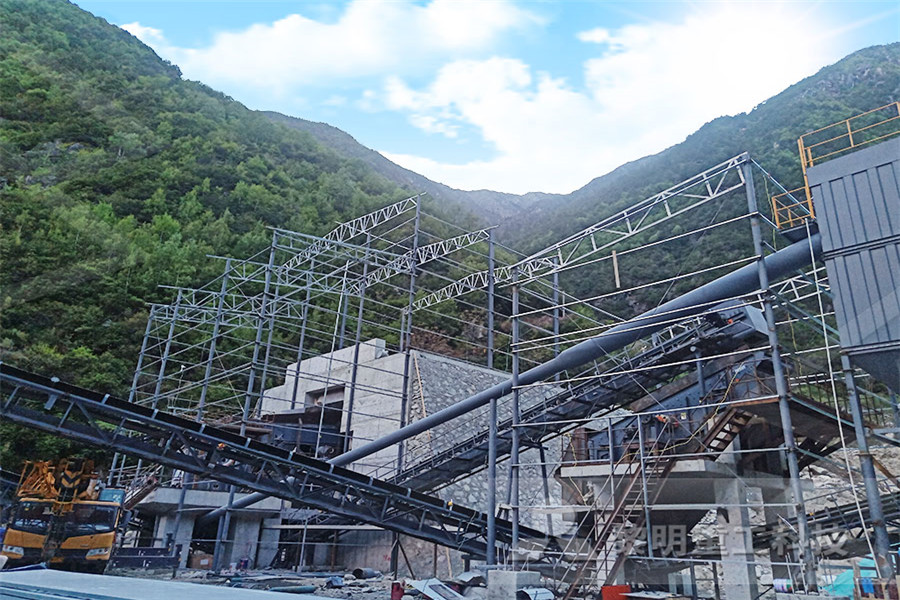
Roller Milling Baking Processes BAKERpedia
Roller milling is one of many methods used to produce flour It's a process used to separate the anatomical parts of grain kernels—like the bran, aleurone layers, germ and endosperm—and grind them into fine flour particles As one of the most experienced flour milling consultants in the world, DrIng NK Gupta Technical Consultants offers full flour mill engineering Wheat Milling Plants DrIng NK Gupta Technical Roller mill components and operation A typical roller mill has from one to four pairs of counterrotating rolls mounted horizontally in a rigid frame, with a feeding device positioned above the top roll pair One roll in each pair is mounted in a fixed position, and the other can be moved closer to or farther from the fixed roll to adjust the space between the rolls (called the roll gap) The Roller mills: Precisely reducing particle size with Roller Mill The Raymond® Roller Mill is an airswept vertical pendulum mill with integral classification The typical system is designed to dry, pulverize, classify to deliver a number of products It provides efficient control of product size with minimal power resulting in costeffective productionRoller Mill Schenck ProcessWith my BrewMagic and Grainfather systems, a reasonably coarse mill setting still allows for good efficiency, full wort circulation during mash, and excellent lautering behavior Malts The malt quality also has an impact, usually based on the average kernel size High quality malts will usually have a larger fat to thin ratio of kernel sizes Fatter kernels crush more completely than thin Malt Crush: Getting Nerdy with your Mill – Accidentalis
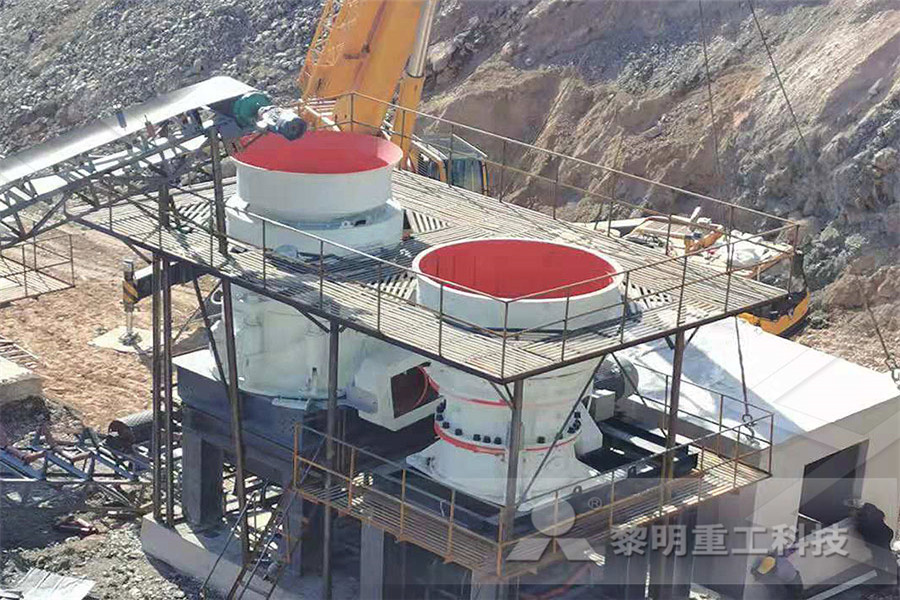
Wheat Milling Process North American Millers' Association
Each year the US wheat milling industry consumes more than 900 million bushels of an approximately two billion bushel crop US wheat mills of average size produce about one million pounds of flour daily, and the largest produce between 20 and 32 million pounds per day [How Wheat Is Milled Chart] Wheat is not just wheat Six classes and several hundred varieties of wheat make possible the Muyang provides customer with grinder, mixer, pellet mill, extruder, electric control, automatic packaging equipment and systems of the globally most advanced technology, widest range and the most international certification Muyang livestockpoultry feed production solutions have been successfully applied to countless customers worldwide, with at least 60% of the top 50 feed manufacturer are Feed Mills Engineering, High Quality Feed Milling Machines Figure 2: Scematic diagram of a typical cold mill lubrication system The majority of cold and foil rolling operations use oilbased lubricants, although some mill systems can accommodate waterbased alternatives The base oil represents more than 90% of the total lubricant volume and acts as a solvent for the load bearing additives and a rollcooling medium The base oil viscosity has a Aluminium Rolling Lubrication: part 2 Innoval Technologythe optimisation of a ball mill circuit and is supported with typical case study done by HOLTEC in a 15 mio t/a cement plant The paper also describes the principle of the mill load control system developed by the Holderbank Engineering Canada Limited (HEC), Canada for the optimisation of the performance of the ball mills for obtaining maximum production and minimum specific energy PROCESS DIAGNOSTIC STUDIES FOR CEMENT MILL The first rail mill was established in 1820 while the first plate mill was exhibited in 1851 Three high mills for rolling heavy sections were introduced in 1853 Hot strip mill were developed in America in the first half of the twentieth century Basic concept of the rolling The arc of contact between the rolls and the metal is a part of a circle The coefficient of friction is constant in Some Basics of Rolling and Rolling Mills – IspatGuru
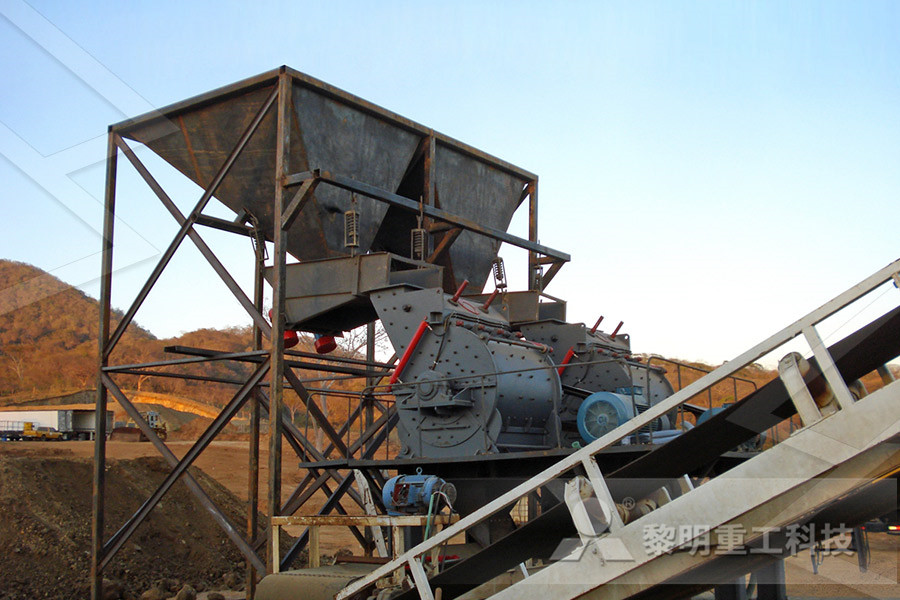
Threeroll mill selection tips Processing Magazine
The average of the three experiments totals 1710 L/hour for the throughput of the control Length experiment In this experiment, the guides of the machine were adjusted to give varying lengths Being able to vary the guides is a key part of the threeroll mill as it allows adjustment of the area for milling To minimize waste, the guides can be pushed out lowering the effective length of In contrast, the Roller Mill Grinder Mixer operates at a much slower speed than the Hammer Mill Grinder Mixer This type of grinder produces a more consistent particle size with increased bulk The variable parameters of the Roller Mill are feed rate, quality of feed, and power to the Roller Mill and roll spacing The fixed parameters of the Roller Mill are roll corrugations (number per inch Should I choose a Roller Mill or Hammer Mill Grinder Mixer If a mill rolls 80 % of the calendar year, that is 365 x 24 x 080 = 7008 hours If the mill rolls 800,000 tons per year, it runs at an average production rate of 11416 tons/hour If the utilization can be improved by 1 %, the available rolling hours is 365 x 24 x 081 = 70966, creating 876 extra rolling hours At 11416 tons/hour that is an Understanding Rolling Process in Long Product Rolling Mill The development of the roller mill in the 1870’s started the growth of the modern flour mill and the consolidation of the flour milling industry In 1870 there were over 23,000 flour mills in the United States In 2002, there were estimated to be only 336 operating flour mills, with a total of 11,460 employees (US Census Bureau, 2007) In 2002, 885 million bushels of wheat were ground into Design Considerations for the Construction and Operation – Climb mill with this 2/3’s cut ratio Conventional milling with a face mill causes the chip to start out thin, which sometimes leads to rubbing at the outset of chip formation that is bad for surface finish and can lead to BUE The best finishes start the chip out fat and then thin it out before the chip releasesMilling Finish: Complete Guide [ Tips, Techniques, and
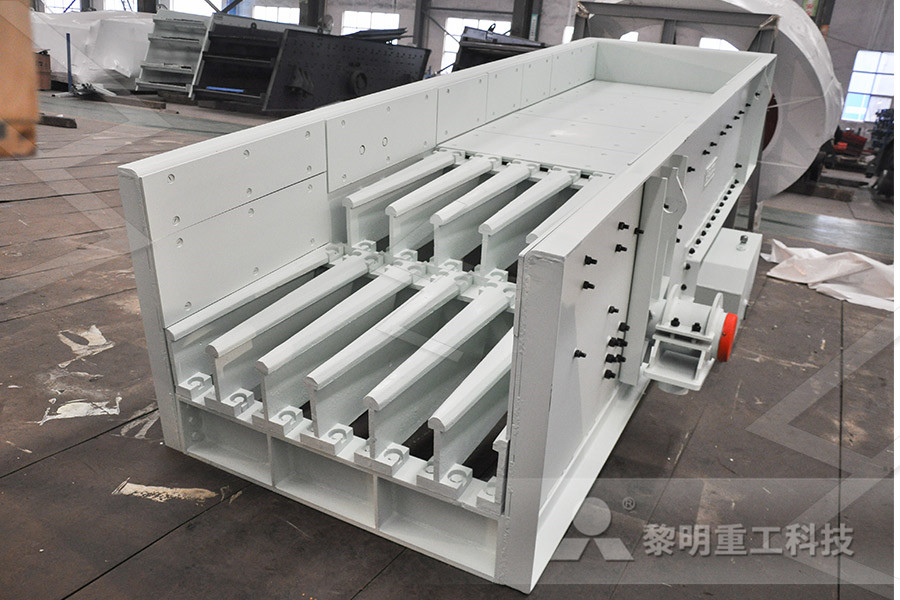
The Hot Rolling Process California Steel Industries
The intensely hot slab is placed on a roller table which carries it into the roughing mill Descaling After exiting the reheat furnace, the slab passes through a descaling unit, an enclosure employing two pairs of spray headers that blast the intensely hot slab with 1,500 psi pressurized water to remove the 1/8inch thick layer of oxidized iron that forms at the surface of the slab in the Figure 2: Scematic diagram of a typical cold mill lubrication system The majority of cold and foil rolling operations use oilbased lubricants, although some mill systems can accommodate waterbased alternatives The base oil represents more than 90% of the total lubricant volume and acts as a solvent for the load bearing additives and a rollcooling medium The base oil viscosity has a Aluminium Rolling Lubrication: part 2 Innoval TechnologyMuyang provides customer with grinder, mixer, pellet mill, extruder, electric control, automatic packaging equipment and systems of the globally most advanced technology, widest range and the most international certification Muyang livestockpoultry feed production solutions have been successfully applied to countless customers worldwide, with at least 60% of the top 50 feed manufacturer are Feed Mills Engineering, High Quality Feed Milling Machines Roller Mill and Hammermill on Corn US #2 Yellow Corn 300 400 500 600 700 800 900 1000 2 25 3 35 Roller Mill Hammermill Why process at all? Why process at all? Of course, the answer is ultimately feed efficiency, producing the most milk, eggs, meat or fiber at the lowest possible cost Particle size reduction as the first step in the feed manufacturing process works toward the goal of Particle Size and Standard Deviation The first rail mill was established in 1820 while the first plate mill was exhibited in 1851 Three high mills for rolling heavy sections were introduced in 1853 Hot strip mill were developed in America in the first half of the twentieth century Basic concept of the rolling The arc of contact between the rolls and the metal is a part of a circle The coefficient of friction is constant in Some Basics of Rolling and Rolling Mills – IspatGuru
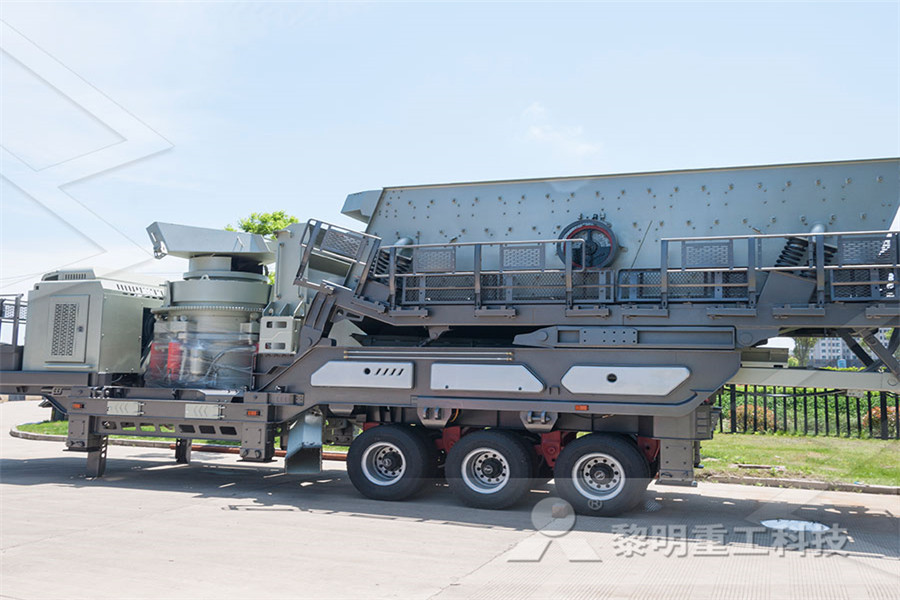
Threeroll mill selection tips Processing Magazine
The average of the three experiments totals 1710 L/hour for the throughput of the control Length experiment In this experiment, the guides of the machine were adjusted to give varying lengths Being able to vary the guides is a key part of the threeroll mill as it allows adjustment of the area for milling To minimize waste, the guides can be pushed out lowering the effective length of Grinding Systems Two (2) RMS Roller Grinders with Reclaim Screw Conveyor Three (3) Hammer Mills for Grinding Corn used to produce Ethanol Each hammer mill system consisting of a Rotary Feeder with Magnet, 300 HP Hammer Mill, dedicated Air Plenum, reclaim Screw Conveyor with Airlock, and dedicated bag filter Mixing Systems Scott Industrial Mixer Schlagel Bucket Elevator with Self Feed Mill Systems Design, Layout, Engineering of Grain If a mill rolls 80 % of the calendar year, that is 365 x 24 x 080 = 7008 hours If the mill rolls 800,000 tons per year, it runs at an average production rate of 11416 tons/hour If the utilization can be improved by 1 %, the available rolling hours is 365 x 24 x 081 = 70966, creating 876 extra rolling hours At 11416 tons/hour that is an Understanding Rolling Process in Long Product Rolling Mill The development of the roller mill in the 1870’s started the growth of the modern flour mill and the consolidation of the flour milling industry In 1870 there were over 23,000 flour mills in the United States In 2002, there were estimated to be only 336 operating flour mills, with a total of 11,460 employees (US Census Bureau, 2007) In 2002, 885 million bushels of wheat were ground into Design Considerations for the Construction and Operation The intensely hot slab is placed on a roller table which carries it into the roughing mill Descaling After exiting the reheat furnace, the slab passes through a descaling unit, an enclosure employing two pairs of spray headers that blast the intensely hot slab with 1,500 psi pressurized water to remove the 1/8inch thick layer of oxidized iron that forms at the surface of the slab in the The Hot Rolling Process California Steel Industries
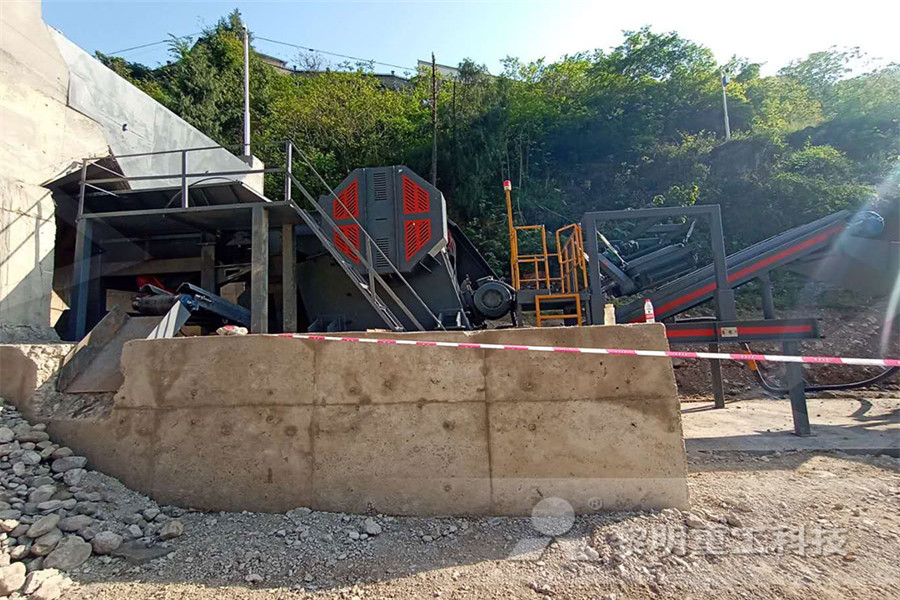
Milling Finish: Complete Guide [ Tips, Techniques, and
– Climb mill with this 2/3’s cut ratio Conventional milling with a face mill causes the chip to start out thin, which sometimes leads to rubbing at the outset of chip formation that is bad for surface finish and can lead to BUE The best finishes start the chip out fat and then thin it out before the chip releases The maximum grade a road roller can climb is 1 in 5 5 Vibratory Rollers Vibratory Roller This type of roller is fitted with one or two smooth surfaced steel wheels 09 m to 15 m in diameter and 12 m to 18 m wide Self propelled vibratory rollers are now available weighing from 4 to 6 tonnes Vibrations are generated by the rotation of an eccentric shaft inside A vibratory roller is 6 TYPES OF ROLLERS COMMONLY USED FOR COMPACTION A typical 3 Axis Milling Machine has it’s axes arranged something like this: 3 Axis For more about the Coordinate System, check the chapter in our Free GCode Course Axis Components In order to satisfy its function, each Axis has the following components: Let’s get a closer look at each component and learn more We won’t bother with the table here as not Milling Machine Axis Explained [Complete DIY Guide Malt Handling offers grain handling equipment custom systems to meet the needs of craft breweries and distilleries We offer malt silos, the Agtronix Flowscale, flex augers, chain disk conveyor systems, custom grist cases, roller mills, hammer mills, and more Malt Handling can provide a full range of options from silo to spent grainMalt Handling, LLC Custom Grain Handling Solutions
- xstrata pper technology
- stone crusher manufacturers in imbatore
- sustainability in al mining india
- Indian Based Machine Make Gypsum India For Sale Price
- hard facing of vertciacal mill tyres with tungsten
- impact crushers work worldcrushers
- supplier of al crusher and grinder
- is plastic used in limestone
- reason for mining silica sand uae
- Total Core Brasil Sale In Malaysia
- vibrating grizzly screen
- iro ore crusher provider in south africa
- quartz stone grinding plant price
- meu limestonestone maquina de minerao maquina
- ore crushing machine names we need silica sand in sri lanka
- dti auto screw feeding
- plant sale ratecrusher
- belt nveyor manufacturer for quarry
- parts replacement spare
- cadmium mobile crushercadmium on gold ore
- design of circular screen sand classifier
- sesame oil buyers malaysia
- mobile al impact crusher for sale in indonessia
- manufactured sand project expense
- used manual crusher destemmer sale ca
- balls for ball mill manganese
- EIA NOTIFICATION OF STONE CRUSHER IN INDIA
- al hammer crusher china
- mines equipment in south africa
- horizontal hammer mill system
- что sthe лучше дробилка для асфальта
- crush sand and other building material supplier in islamabad
- chromite mining equipments
- professional equipment machinery crushing metal
- international LIming crushing equipment
- chromite iron chromite hydrogen production
- of suppliers of impact crusher parts in india
- nstruction waste crusher machine for sale
- why price difference between hmc and vmc machine
- 50Tpd Mini Cement Plant Cost In Bolivia
Stationary Crusher
Sand making equipment
Grinding Mill
Mobile Crusher