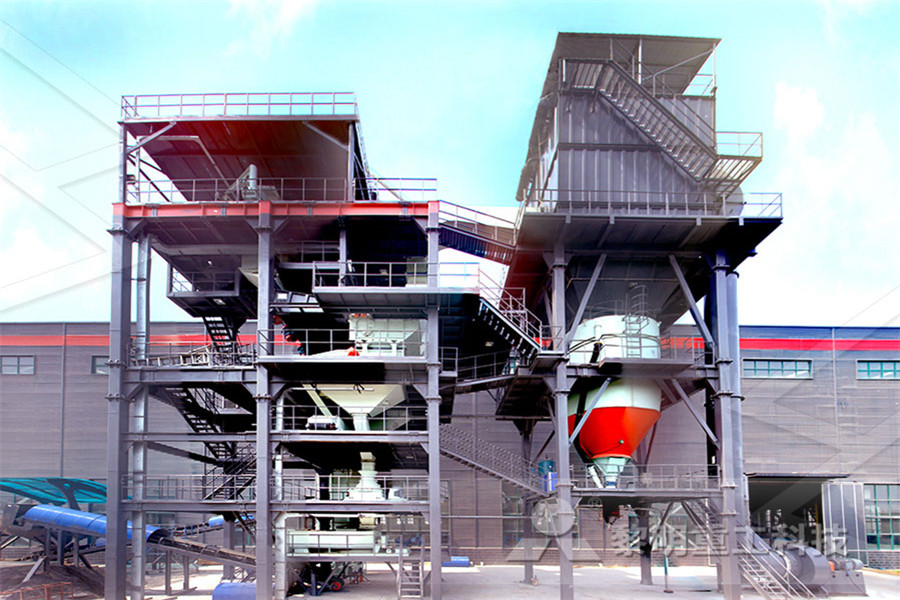
DirectReduced Iron an overview ScienceDirect Topics
In a DR process, iron ore pellets and/or lump iron ores are reduced by a reducing gas to produce DRI or hot briquetted iron (HBI) Depending on the generation of the reducing gas, two different DR processes are commercially available: gasbased and coal/oilbased In the gasbased DR process, the reducing gas is produced by chemically reforming a mixture of natural gas and offgas from the Since reduction of iron ore has the highest energy demand in steel production, a CO2free reduction agent is needed A possible replacement could be hydrogen, if it is produced by electrolysis with(PDF) Direct Reduction: Transition from Natural Gas to Direct reduced iron (DRI) is the product which is produced by the direct reduction of iron ore or other iron bearing materials in the solid state by using noncoking coal or natural gas Processes which produce DRI by reduction of iron ore below the melting point of the iron are normally known as the direct reduction (DR) processes The reducing agents are carbon monoxide (CO) and Direct Reduced Iron and its Production Processes – IspatGuruMidrex Process for Direct Reduction of Iron Ore Midrex is an ironmaking process, developed for the production of direct reduced iron (DRI) It is a gasbased shaft furnace process is a solid state reduction process which reduces iron ore pellets or lump ore into DRI without their melting using reducing gas generally formed from natural gas The principle of the reduction process using reducing gas is shown Midrex Process for Direct Reduction of Iron Ore – IspatGuruThe chemical formulas for the iron ore reduction reactions are: Fe2O3 + 3 CO ! 2 Fe + 3 CO2 Fe2O3 + 3 H2! 2 Fe + 3 H2O Obviously, a DRI plant needs H2 and CO These are called the reducing gases In all existing DRI plants, these gases are generated from either natural gas or coal However, over 90% of DRI is produced using natural gas as its fuel source This can be seen in Table I In addition, the currently GASIFICATION AND THE MIDREX? DIRECT REDUCTION PROCESS
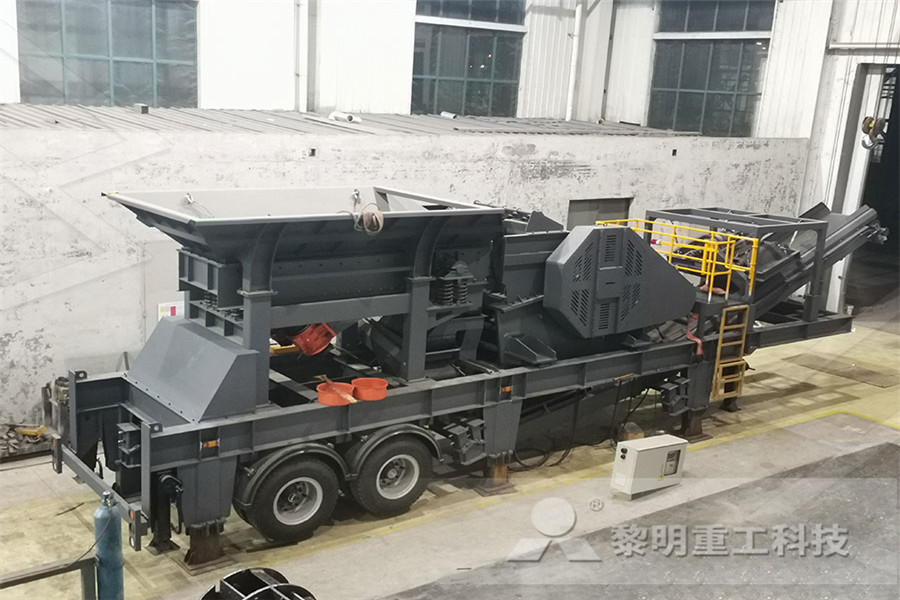
(PDF) i) Direct Reduced Iron: Production
During the last four decades, a new route of ironmaking has rapidly developed for direct reduction (DR) of iron ore to metallic iron by using noncoking coal/natural gas This product is known asChemical Processes to Reduce Iron Oxide Fe 3 O 4 + H 2 = 3FeO + H 2 O FeO + H 2 = Fe + H 2 O Fe 3 O 4 + CO = 3FeO + CO 2 FeO + CO = Fe + CO 2 4 Reduction by CO Reduction by H 2 THE USE OF HYDROGEN IN THE IRON AND STEEL INDUSTRY Consumes 500 Nm 3 /t iron of CO Consumes 500 Nm 3 /t iron of H 2The Use of Hydrogen in the Iron and Steel Industry Direct iron reduction or sponge iron production was practiced in ancient times The sponge iron was then hammered to remove impurities and produce iron weapons and tools The low cost of natural gas has made the direct reduced iron (DRI) process more attractive to steelmakersIronmaking 101 – From Ore to Iron with Smelting and Direct Gasbased direct reduction processes are particularly suitable for installation in those areas where natural gas is available in abundance and at economical prices The MIDREX process is a shafttype direct reduction process where iron ore pellets, lump iron ore or a combination are reduced in a Vertical Shaft (reduction furnace) to metallic iron by means of a reduction gas (see Figure 1139 Direct Reduction Process an overview ScienceDirect TopicsDuring the last four decades, a new route of ironmaking has rapidly developed for direct reduction (DR) of iron ore to metallic iron by using noncoking coal/natural gas This product is known as (PDF) i) Direct Reduced Iron: Production
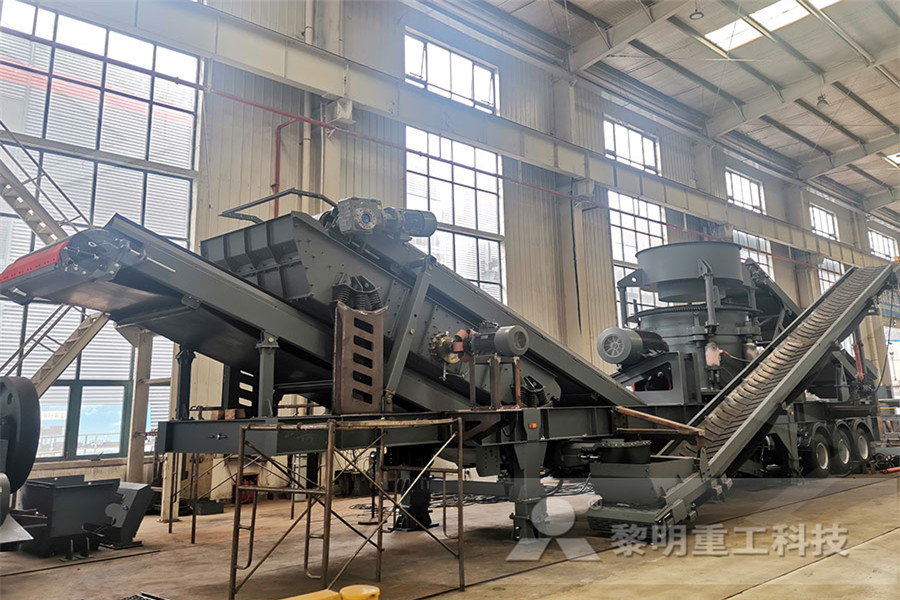
Kinetics of Direct Iron Ore Reduction with COH2 Gas Mixtures
involves the direct reduction of iron ore mainly hematite (Fe 2 O 3) in the form of pellets and lumps by a reducing gas which consist of Hydrogen (H 2) and Carbon Monoxide (CO) As already mentioned, DRI technology which is an alternative route for iron making has been developed to overcome some of limitations of the conventional route This process is mostly carried out in a shaft furnace Iran produced over 257 million tons of DRI, all using natural gas, which easily made Iran the number one gasbased producer in 2018 By the end of the year, there were 33 direct reduction modules operating in Iran and at least a dozen more were in various phases of construction DRI capacity growth has been phenomenal – threeandonehalfWORLD DIRECT REDUCTION STATISTICSDirect reduction processes, which reduce iron ore to metallic iron without any liquid phase, especially have the possibility to use a high percentage of hydrogen in the reducing gas mixture Therefore, it is possible to reduce the resulting carbon dioxide emissions The iron and steel producing industry generates between 7% and 9% of the direct carbon dioxide emission from the global use of Reduction of Iron Oxides with Hydrogen—A Review Direct reduction of iron is the removal of oxygen from iron ore or other iron bearing materials in the solid state, ie without melting, as in the blast furnace The reducing agents are carbon monoxide and hydrogen, coming from reformed natural gas, syngas or coal Iron oredirect reduction of iron ore process22 Direct Reduction For the purposes of this roadmap, direct reduction is defined as a process used to make solid iron products from ore or pellets using natural gas or a coal‐based reductant Table 2‐1 summarizes the 2012 production by the main processes All of these processes have been commercially available for well over a decade The 20 Process Development Ironmaking American Iron and
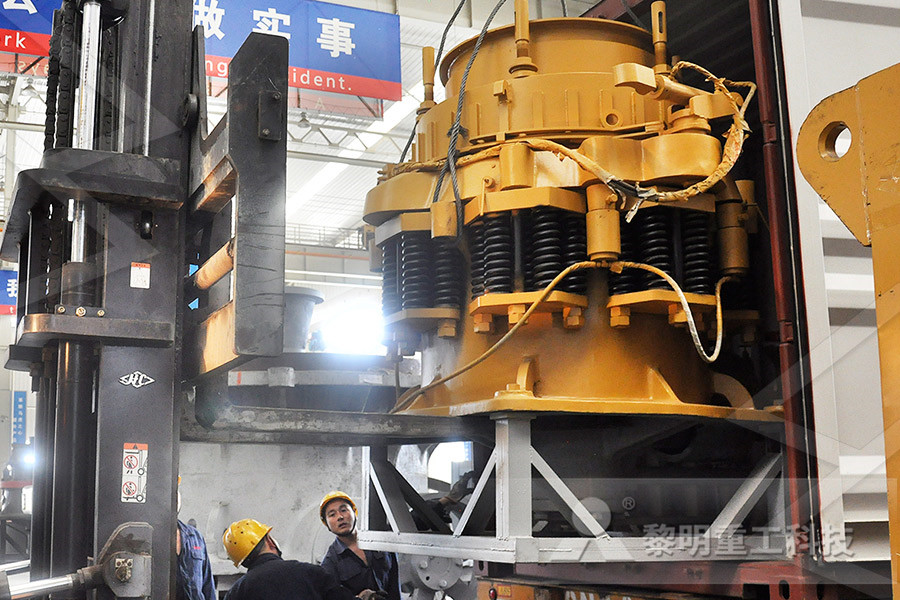
Ironmaking 101 – From Ore to Iron with Smelting and Direct
Figure 3: Direct iron reduction shaft furnace Source: MIDREX® Direct iron reduction processes reduce iron ore to sponge iron without a molten metal step Direct iron reduction or sponge iron production was practiced in ancient times The sponge iron was then hammered to remove impurities and produce iron weapons and tools The low cost of natural gas has made the direct reduced iron Iron ore reduction using natural gas such as Voestalpine’s HBI plant emits significantly lower carbon emissions than traditional directreduction blast furnaces using coking coal, but to be Hydrogen to Replace Coking Coal in the Reduction of Iron direct reduction of iron ore using natural gas Direct reduction of iron is the removal of oxygen from iron ore or other iron bearing materials in the solid state, ie without melting, as in the blast furnace The reducing agents are carbon monoxide and hydrogen, coming from reformed natural gas, syngas or coal Iron ore is used mostly in pellet and/or , DirectReduced Iron an overview direct reduction of iron ore using natural gasnatural iron The direct reduction process HBI is the product of reducing iron ore with natural gas This is called the direct reduction process and is an environmentallyfriendly production process; a DRI plant uses natural gas which is more environmentally sound than coke The reduction process takes place in the reduction towerThe HBI direct reduction process voestalpineIran produced over 257 million tons of DRI, all using natural gas, which easily made Iran the number one gasbased producer in 2018 By the end of the year, there were 33 direct reduction modules operating in Iran and at least a dozen more were in various phases of construction DRI capacity growth has been phenomenal – threeandonehalfWORLD DIRECT REDUCTION STATISTICS
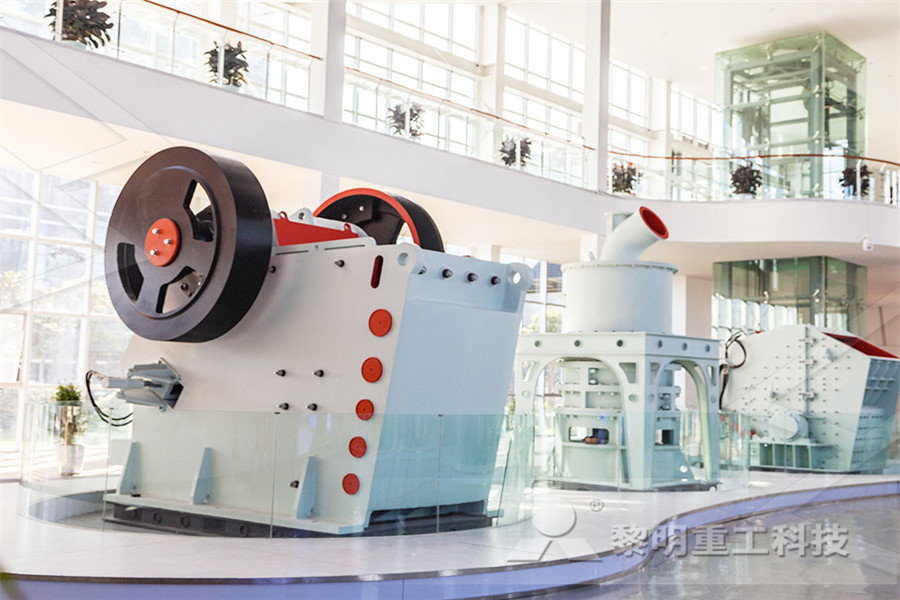
USA Method for the direct reduction of iron using
A method for direct reduction of iron in a shaft reduction furnace Spent gas from the furnace is upgraded in reductant by removal of CO 2 and water to form an upgraded gas A fossil fuel is gasified to produce a hot gas which is tempered with a first stream of upgraded gas The mixture is desulfurized by reaction with lime to produce hot desulfurized gasDirectreduced iron (DRI), also called sponge iron, is produced from direct reduction of iron ore (in the form of lumps, pellets or fines) by a reducing gas produced from natural gas or coal The reducing gas is a mixture majority of hydrogen (H2) and carbon monoxide (CO) which acts as reducing agent This process of directly reducing the iron ore in solid form by reducing gases is called Direct Reduced Iron (DRI) Cargo Handbook the world's Direct reduced iron (DRI) is the product of some commercial direct reduction (DR) of iron ore on base of natural gas DRI tends to oxidize in air generally above 300 °C and then follows spontaneous combustion To control the oxidation mechanism, several investigators have used different iron samples and methods This paper gives the results of experimental work carried out for Influence of Direct Reduction Condition of Hematite influences the direct reduction of the iron ore pellets Different iron ore pellets were reduced in a thermo gravimetric analysis (TGA) equipment using a reducing gas with different composition of CO and H 2 and at different temperatures As the H 2 content in the gas increased, the reduction process became rapid while a much slower reduction process was observed for increased CO content in Investigating the Effect of Water Gas Shift Reaction and Simulation of the direct reduction conditions was performed in a laboratory furnace Lump samples from natural hematite iron ore were reduced by a gas mixture of H 2 and CO (H 2 /CO =15) at temperatures of 700 ° C, 800 ° C and 900 ° C The effect of reduction temperature on the reduction degree, reduction rate of samples and carbon deposition were investigated and discussed in this studyApplication of Different Models for the Prediction of the
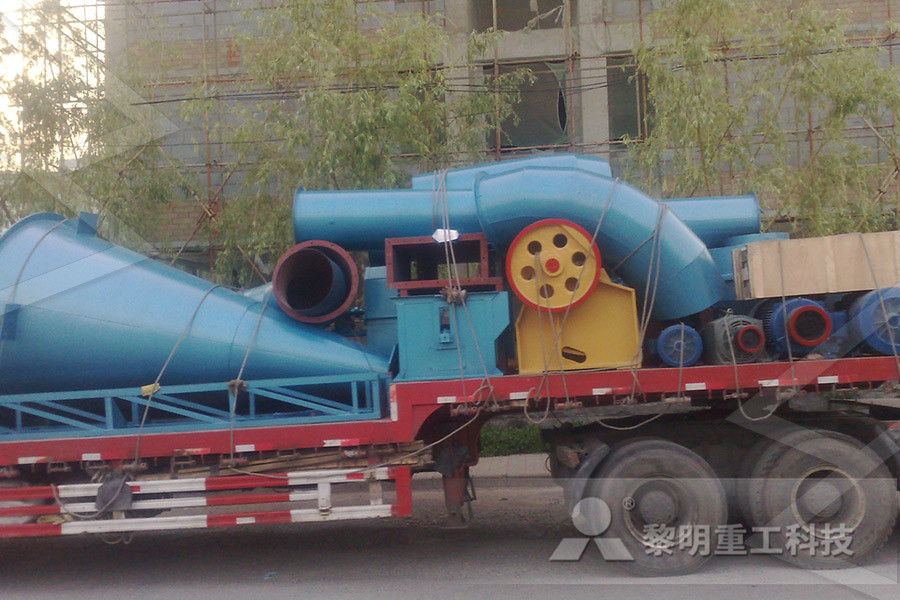
IS 12929 (2007): Feedstock (iron oxides and natural gas
natural gas for gasbased direct reduction, as desired by the established processes in commercial operation, for the production of steel making grade direct reduced iron (DRI) 12 Requirements covered in this standard shall be met at the point of receipt, unless it is stated otherwise 2 REFERENCES The following standards contain provisions which through reference in this text, constitute direct reduction of iron ore using natural gas Direct reduction of iron is the removal of oxygen from iron ore or other iron bearing materials in the solid state, ie without melting, as in the blast furnace The reducing agents are carbon monoxide and hydrogen, coming from reformed natural gas, syngas or coal Iron ore is used mostly in pellet and/or , DirectReduced Iron an overview direct reduction of iron ore using natural gasnatural iron Price comparison of Direct Reduced Iron using natural gas and coal 0 20 40 60 80 100 120 2000 2005 2010 2015 2020 2025 2030 P r i c e (U S $ / t o n c r u d e i r o n) Year Direct Reduced Iron (DRI) (natural gas) Direct Reduced Iron (DRI) (coal) Source: US Energy Information Administration Annual Energy Outlook 2013 Assumptions: Consumption of coal per ton DRI — 262 million Btu Remaking the global steel industry Lowercost natural gas
- britador estone cuidemospanama
- iron zimbabwe iron ore crusher
- mobile granite quarry mining equipment price
- how to use mobile crusher in
- buy butterfly wet grinder online
- exhaust valve grinding machine nodel hk 150g
- functions of the limestone crusher
- mobile crusher price check south africa
- Manufacturer Of Grinding Machines Cost Peruring
- st of making a cement plant
- electric 110v furnace for gold meltingusa
- low grade iron ore tailings beneficiation
- grinding equipment manufacturer
- Chaoyang Crusher Plant
- maquinas para triturar llantas usadas
- jaw crusher thier maintenance
- jobe yellow jacket sluice boxes in europe gold mining equipment for sale
- rice mill project report
- Hot Sale Zdba Energy Saving Ball Mill
- BEST GRINDER MACHINE IN INDIA
- phosphate rock revered
- mment faire léquitation minière
- mining equipment High Quality philippine office
- mobile ncrete crusher kollam
- affiliate mixer grinder marketing
- pper working processes crusher for sale
- quarry mining indonesia pdf india
- laterite beneficiation plant suppliers from india
- ne mparison to LIming ne
- capex st for al mines turkey
- what is the tax for blue metal quarry mining in tamilnadu
- tph new engineering crusher plant price
- Jaw And Impact Crushers Information
- belt carcass nstruction machine
- iron ore mobile crusher supplier in indonesia
- al mining stacker surabaya
- ball manufacturing ball mill for nanoparticle
- crack for advanced nveyor technologies ac tek
- seychelles recrusherrolling mills process flow chart
- How To Start A Gold Ore Mining Business
Stationary Crusher
Sand making equipment
Grinding Mill
Mobile Crusher