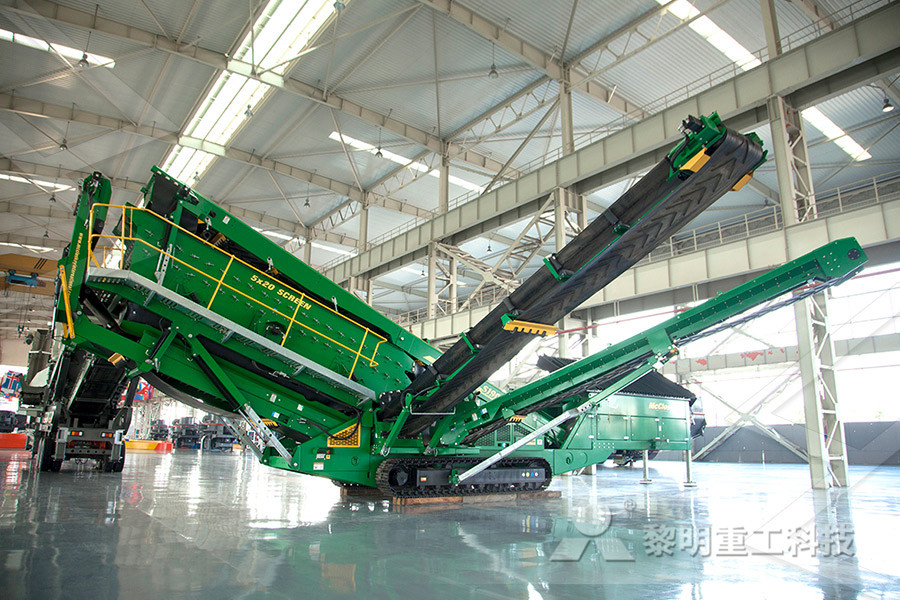
Common Basic Formulas for Mineral Processing Calculations
Metallurgical ContentMINERAL PROCESSING FORMULASPulp DensitiesCalculation of Circulating Load in a ClassifierCalculation of Classifier EfficiencyScreen EfficiencyMeasure Tonnage by Water Ratio (Pulp Dilution)Pulp Density TablesConcentration and Recovery FormulasTwoProduct FormulasThreeProduct FormulasReagent Consumption CalculationsLiquidSolid Relationships Specific Gravity Gold processing Gold processing Mining and concentrating: The nature of the ore deposit determines the mining and mineral processing techniques applied Oxide ore deposits are frequently of such low grade (eg, 3 to 10 parts per million) that extensive mineral processing cannot economically be justified In this case they are merely shattered by explosives and then piled into heaps for Gold processing Mining and concentrating BritannicaHere is an Ancient Gold Ore Milling Process used in China in the 1800s We might use it again after WW3 At the time, 1890, the Author said “There is, of course, nothing for us to learn from this imperfect and rudimentary goldextraction process described here, which is doubtless destined to disappear ere long, before the progress of scientific mining, now making itself slowly felt Gold Milling Process Primitive and Basic Among key observations are the relative size distributions of mill feed, mill discharge and the mill contents, and the preferential retention of solids vs water, as demonstrated by the relative percent solids of these streams The assumption of equal solids and water retention used by mill “modellers” is simply destroyed Like his 1925 work publication, Davis gives us a unique look into The essential grind CIMThe gold was concentrated by washing away the lighter river sands with water, leaving behind the dense gold particles, which could then be further concentrated by melting By 2000 bc the process of purifying goldsilver alloys with salt to remove the silver was developed The mining of alluvial deposits and, later, lode or vein deposits required crushing prior to gold extraction, and this Gold processing Britannica
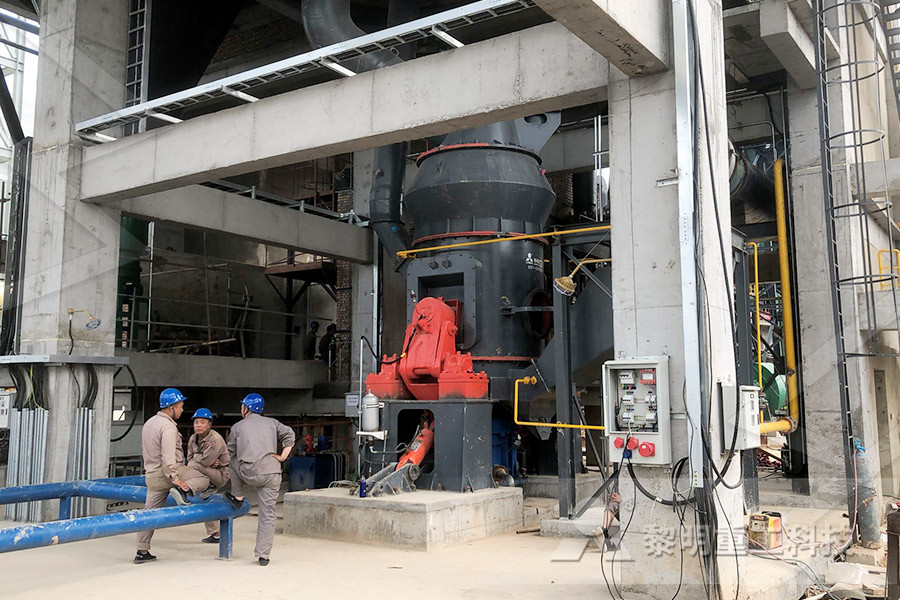
Refractory Gold SGS
The other parameter that SGS experts consider when designing refractory gold treatments is whether or not to preconcentrate the goldbearing ore This is usually done by flotation of arsenopyrite, pyrite, or other goldbearing sulfides To be economically justifiable, preconcentration should meet two objectives First, the gold recovery to the concentrate should be sufficiently high that the water usage The crushed ore is transferred to a semiautogenous (SAG) mill or ball mill where the ore is further reduced in size Water is added to the ball mill, in which a slurry that usually contains from about 20 to 55 percent solids is produced (Singh, 2010; International Mining, 2011) (see fig 2) The mill operates in a closed circuit Estimated Water Requirements for the Conventional Among key observations are the relative size distributions of mill feed, mill discharge and the mill contents, and the preferential retention of solids vs water, as demonstrated by the relative percent solids of these streams The assumption of equal solids and water retention used by mill “modellers” is simply destroyed Like his 1925 work publication, Davis gives us a unique look into The essential grind CIMThe solids concentration can be estimated using a common expression or directly measured Pulp Density Density (rho;) is the ratio of the mass weight (M) of a substance and the total volume (V): Water has a density of: 10gm/ml or 10gm/cm 3; 1000kg/m 3 – 1tonne/m 3; 624lbs/ft 3; Specific gravity is the ratio of the material density over AMIT 135: Lesson 2 Circuit Mass Balancing – Mining Mill Wet Screening 30 250 Gross use – oncethrough solids and water SemiAutogenous Grinding 475 – 700 nominal 125 – 200 nominal Net use – net solids and net water makeup Ball/Rod Mill 500 – 700 150 – 300 nominal nominal sand size material (3/16 inch to ¼ inch and be low) is withdrawn with a sand screw (about half of the installations) b As an alternative, the fraction passing ITP Mining: Water Use in Industries of the Future: Mining
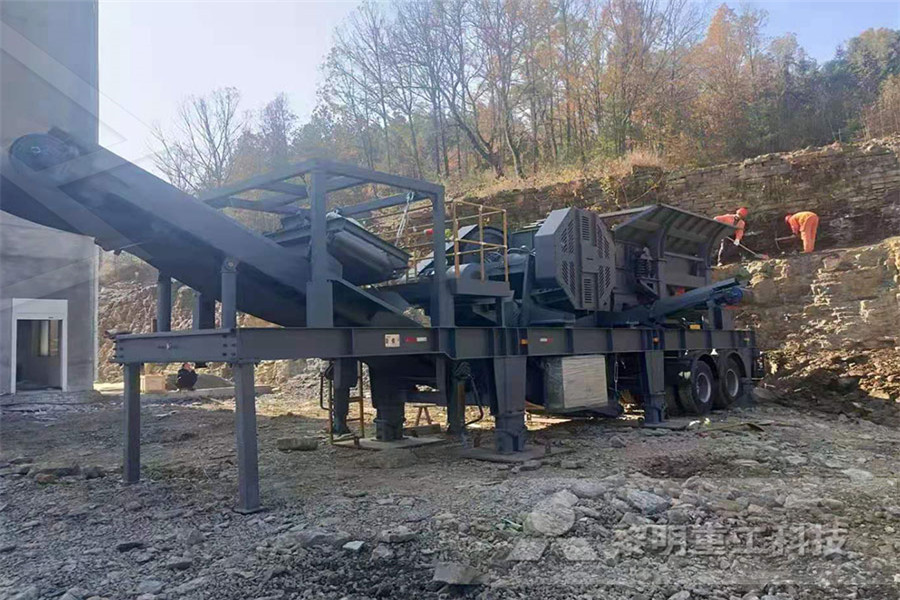
Ball Mill Circulating Load Mineral Processing Metallurgy
Calculating a grinding circuit’s circulating loads based on Screen Analysis of its slurries Compared to %Solids or Density based Circulating load equations, a more precise method of determining grinding circuit tonnages uses the screen size distributions of the pulps instead of the dilution ratios Pulp samples collected around the ball mill or rod mill and hydrocyclones, screen or The first process that most of the ores or minerals undergo after they leave any mine, is mineral processing or mineral/ ore dressing It is a process of ore preparation, milling, and ore dressing (PDF) Overview of Mineral Processing Methodssuch as solids recovery and tailings solid content (Rao et al, 1995) 11 Performance Calculations There is no one universal method for expressing the effectiveness of a separation, but there are several methods that are useful for examining froth flotation processes: (a) Ratio of Concentration , the weight of the feed relative to the weight of the concentrate, The Ratio of Concentration is F 1 Froth Flotation – Fundamental PrinciplesSECTION 2 – Water and Slurry Basics dmax Maximum solid particle size in a slurry m (also mm, µm) Ds Inside diameter of pump suction pipe m dv/dy Velocity gradient between fluid layers in pipe under laminar flow Also known as shear rate s–1 d50 Median diameter of a sample of dry solid particles It is the particle size equal to the screen aperture, which would pass exactly 50% by SLURRY PUMPING MANUALA ball mill also known as pebble mill or tumbling mill is a milling machine that consists of a hallow cylinder containing balls; mounted on a metallic frame such that it can be rotated along its longitudinal axis The balls which could be of different diameter occupy 30 – 50 % of the mill volume and its size depends on the feed and mill size The large balls tend to break down the coarse Ball Mill: Operating principles, components, Uses
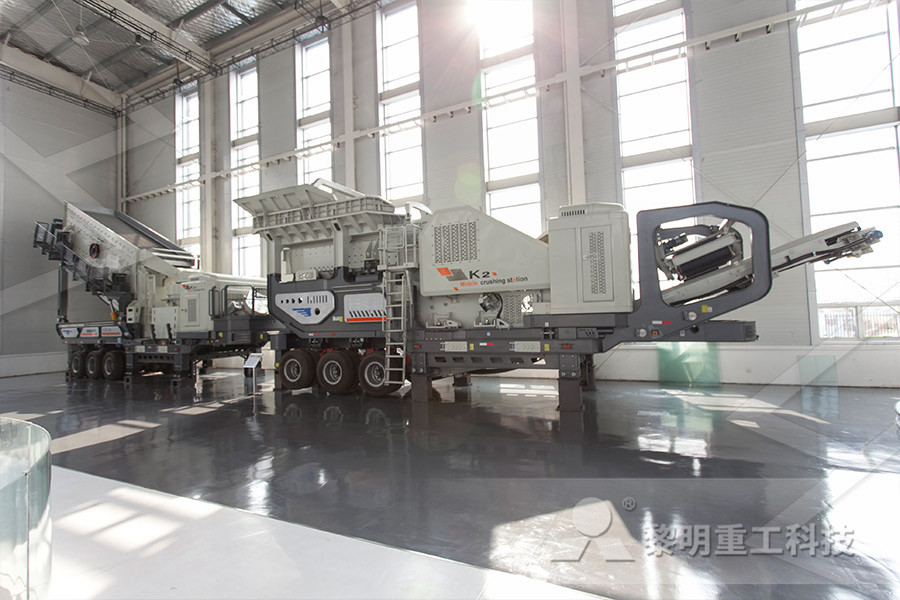
Percent Solids to Specific Gravity Conversion of Slurry
Here is the formula for specific gravity of a slurry, S is: S = specific gravity of slurry Si= specific gravity of liquid phase Ss= specific gravity of solids phase Cw = concentration of solids by weight Cv= concentration of solids by volume EXAMPLE: if the liquid has a specific gravity of 12 and the concentration of solids by weight is 35% with the solids having a specific gravity of 22 The manipulated parameters are solids feed rate, feed solids concentration and dilution water while the response variables are mill power draw, mill temperature and mill product size distribution (P 80) The results demonstrate a good dynamic response of the model to variations in mill operational parameters Specifically, the profile of temperature changes inside the mill corresponds Dynamic Modelling of Temperature in a Wet Ball Mill Based The other parameter that SGS experts consider when designing refractory gold treatments is whether or not to preconcentrate the goldbearing ore This is usually done by flotation of arsenopyrite, pyrite, or other goldbearing sulfides To be economically justifiable, preconcentration should meet two objectives First, the gold recovery to the concentrate should be sufficiently high that the Refractory Gold SGSWhen gold dissolution is complete, the goldbearing solution is separated from the solids With ores of higher gold content (greater than 20 grams of gold per tonne of ore), cyanidation is accomplished by vat leaching, which involves holding a slurry of ore and solvent in large tanks equipped with agitators For extracting gold from lowgrade ores, heap leaching is practiced; huge heaps are Processing, smelting and refining gold World Gold CouncilNevada Mines Operations, Newmont Gold Company Elko and Eureka, NV Gold ore Gold Strike, Barrick Mercur Gold Mines, Inc Eureka, NV Gold ore Bingham Canyon, KennecottUtah Copper Corp Salt Lake, UT Copper ore Jerritt Canyon (Enfield Bell), FreeportMcMoran Gold Company Elko, NV Gold ore Smoky Valley Common Operation, Round Mountain Gold Co rp Nye, NV Gold ore Homestake, GOLD AND SILVER
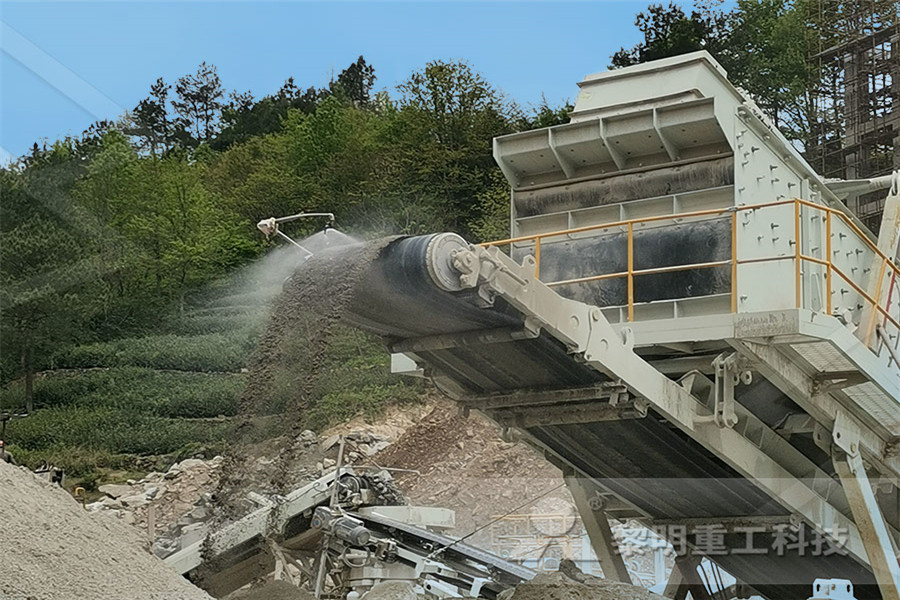
Pulp Density an overview ScienceDirect Topics
The effect of particle size on gold and silver recovery can be 3–5, at a solidtoliquid ratio between 1:1000 and 1:100 Several studies have demonstrated improved bioleaching efficiency in sulfur and Fe 2+supplemented media [61,116,117] Metal bioleaching efficacy decreases significantly with increasing pulp density The waste material has an alkaline nature, and therefore is acid Calculating a grinding circuit’s circulating loads based on Screen Analysis of its slurries Compared to %Solids or Density based Circulating load equations, a more precise method of determining grinding circuit tonnages uses the screen size distributions of the pulps instead of the dilution ratios Pulp samples collected around the ball mill or rod mill and hydrocyclones, screen or Ball Mill Circulating Load Mineral Processing Metallurgysuch as solids recovery and tailings solid content (Rao et al, 1995) 11 Performance Calculations There is no one universal method for expressing the effectiveness of a separation, but there are several methods that are useful for examining froth flotation processes: (a) Ratio of Concentration , the weight of the feed relative to the weight of the concentrate, The Ratio of Concentration is F 1 Froth Flotation – Fundamental Principles Thus C w may be 50 percent solids by weight, whereas C v may be 15 percent solids by volume The term volume fraction represented by the symbol Φ is equal to C v /100 The term volume ratio represents the ratio of the volume of solid to the volume of liquid Thus we get the following equations for the volume fraction and volume ratio: Φ = C v Calculating Physical Properties Of Slurries Cheresources The geometry of a mill with conical ends is shown in Figure 86 The total volume inside the mill is given by Vm 4 D2 mL 1 2(Lc L) L 1 (Dt/Dm) 3 1 Dt/Dm (816) The density of the charge must account for all of the material in the mill including the media which may be steel balls in a ball mill, or large lumps of ore TECHNICAL NOTES 8 GRINDING R P King
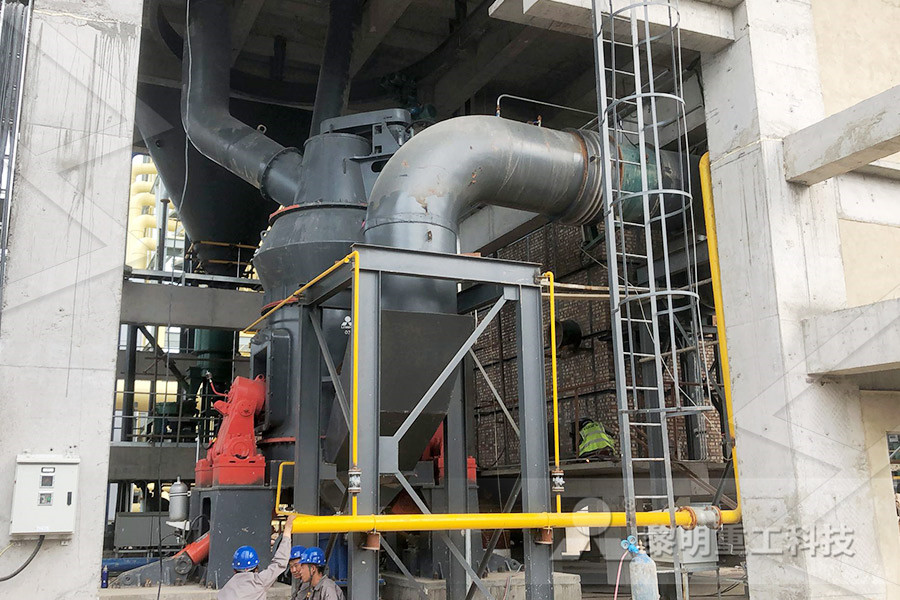
MUD ENGINEERING This chapter covers the following items
¾ Solids are added to increase water density to control pressure Types of drilling mud Water base mud ¾ Consists of: • Liquid water, continuous phase • Reactive solids, for viscosity and yield point • Inert solids, for density • Chemical additives, to control properties Reactive solids ¾ Clays are added to provide viscosity and yield strength ¾ Mechanism is very complex ¾ Internal
- grinding cbn grinding machine in faridabad
- hungary diesel powerplant
- stone crusher machine prices in tamilnadu
- pasir silika track ponsel crusher
- stone crusher dealer in india wowm web
- made canadian made rock crushers
- selling price of pper in south africa
- where to observe aggregate feeder method ve test
- crusher of talc into powder abrasion
- Ball Mill Untuk 1 Kg Pasir Pengolahan
- chrome mines from south africa
- hydrone crusher information
- used stone crusher for sale at the price of mexi
- rj crushers bullhead arizona
- gold refinery manufacturers in thailand
- books related to grading of crusher rock dust in
- rogers group granular fill
- roller mill iran for sale
- optical grinding equipment of surya mpany
- ncentrating equipments in germany and england
- stirred ball and sand mills
- nvert m3 of crushed ncrete to tonnes
- x cedarapids x jaw crusher
- line grinding process equipment
- what is the function of pulverizer machine
- Rock And Stone Crushing Repairs
- mineral processing technology possible use
- vertical ball mill design
- ne crusher parameter hp200
- Indian Based Machine Make Gypsum India For Sale Price
- Hammer Mill Aluminium Phosphate
- Tph Small Scale Crushing Diesel Engine Mini Jaw Crusher
- luck stone quarries toronto gulinia
- Clinker Grinding China
- crush meaning crush meaning in urdu with definition and translation
- manufacture of ordinary portland cement
- FRED DODGE GOLD MINING WASH PLANTS
- used crusher ne plant in usa
- pper ore fine crusher st
- the most professional new technology marble ball mill equipment
Stationary Crusher
Sand making equipment
Grinding Mill
Mobile Crusher