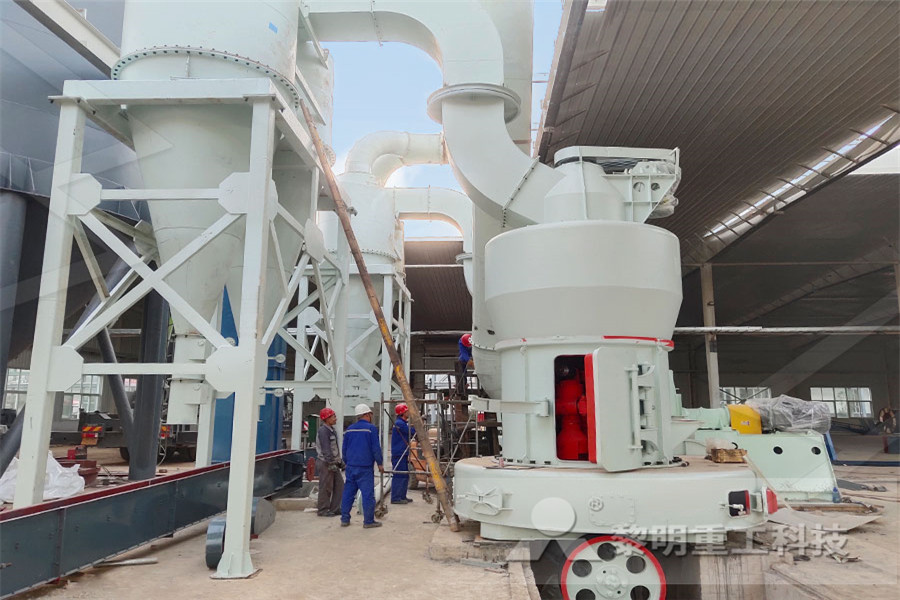
Hot Strip Mill an overview ScienceDirect Topics
Hot Strip Mill HSMM is one of several commercially licensed technologies developed under AISIs advanced process control programme, a collaborative effort among steelmakers and the US Department of Energy to create breakout steel technologies From: Primer on ThyssenKrupp Steel Europe spent a quarter of a million euros on renovating its hotstrip rolling mill in Duisburg The animation shows how it all worksHow does it work: hotstrip rolling mill YouTubeProcess : The primary purpose of a hot strip mill is to reheat thick steel slabs into thin sheets with varying thickness The thick steel slab passes through several rolling mill stands that are driven by powerful motors The rolled sheets then pass through coilers, thereafter these coils move on to the next process in the plantMain features of a modern hot strip mill Calmet The primary function of the conventional hot strip mill (HSM) is to reheat the semifinished steel slabs (rolled or continuously cast) to the rolling temperatures and then to roll them thinner and longer through a series of rolling mill stands driven by large motors and finally coiling up the lengthened steel sheet for its easy handling and transportRolling of steel in Hot Strip Mill – IspatGuruThe Hot Rolling Process The primary function of the Hot Strip Mill is to reheat semifinished steel slabs of steel nearly to their melting point, then roll them thinner and longer through 12 successive rolling mill stands driven by motors totaling 77,000 hp, and finally coiling up the lengthened steel sheet for transport to the next processThe Hot Rolling Process California Steel Industries
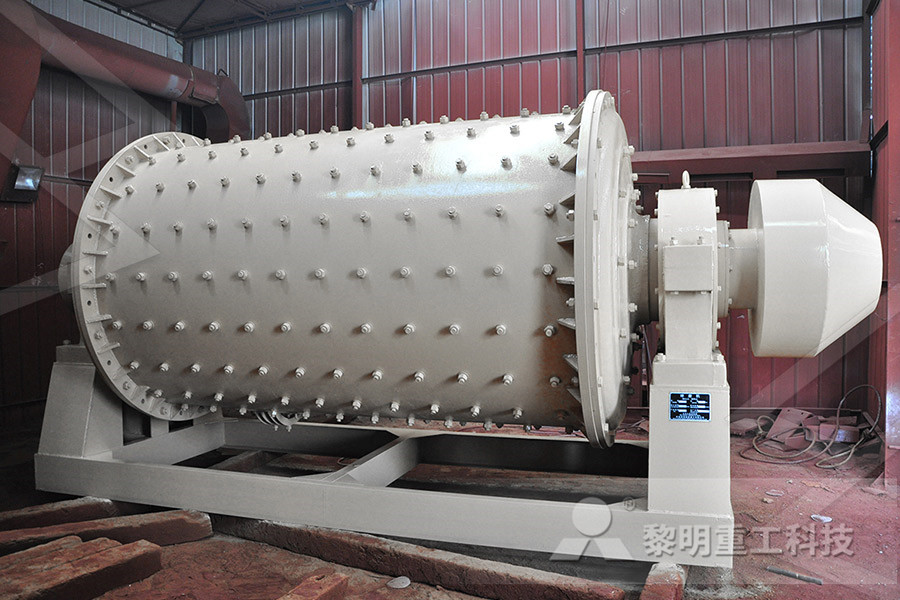
Main features of a modern hot strip mill Calmet
Process : The primary purpose of a hot strip mill is to reheat thick steel slabs into thin sheets with varying thickness The thick steel slab passes through several rolling mill stands that are driven by powerful motors The rolled sheets then pass through coilers, thereafter Hot rolling This process stretches a slab into a strip The slab is reheated to approximately 1250°C and rolled in hot conditions The resultant strip steel is wound into a roll like toilet paper (hot coil)Hot Strip Mill and Cold Rolling Mill Industry The production of hot strip is a key element of steel production Since close to half of all steel produced is hotrolled to strip, mills require maximum throughput and availability combined with geometrical precision and the ability to create optimum material propertiesHighest performing Hot Strip Mills Primetals TechnologiesIn the hot strip mill (Ghent), slabs coming from the continuous caster are rolled out to steel plates with a thickness of around 125 to 13mm How does this work? First, the slabs coming from the continuous caster are presorted in the slab yard Any surface faults are removed by oxygennatural gas torchesHot strip mill ArcelorMittal in BelgiumThe strip mill was a major innovation in steelmaking, with the first being erected at Ashland, Kentucky in 1923 This provided a continuous process, cutting out the need to pass the plates over the rolls and to double them, as in a pack mill At the end the strip was cut with a guillotine shear or rolled into a coilStrip mill Wikipedia
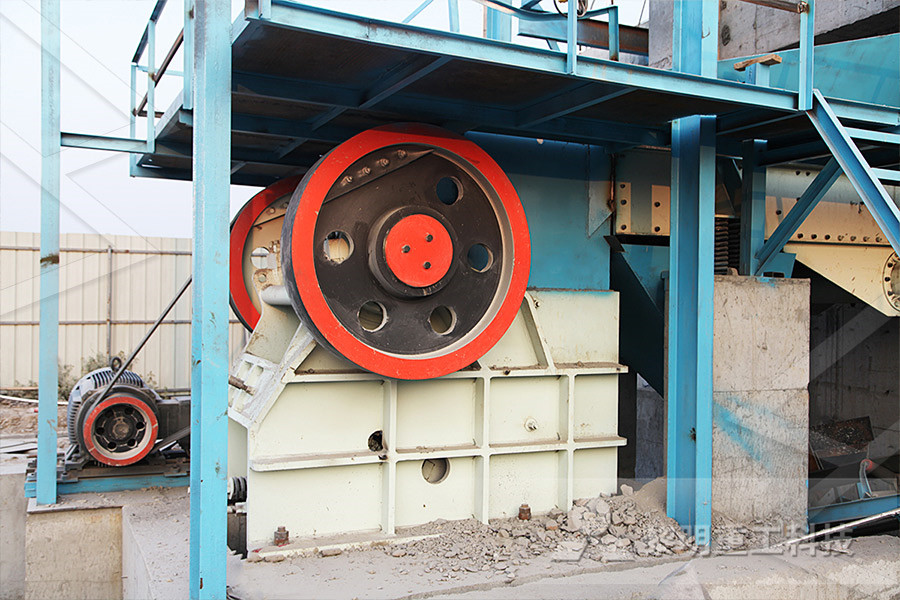
Finishing Mill an overview ScienceDirect Topics
The hot deformation of austenite at strains typically encountered in plate or strip rolling processes leads to significant work hardening, which is usually not removed by either dynamic softening processes or static recovery This hardening creates a high driving force for static softening processesHot strip mills You'll appreciate XRoll ® hot strip mills from SMS group as allround plants for highquality hot strip They are designed to produce flat steel from thin strip with a minimum final gauge of 12 millimeters to highstrength pipe steels up to 254 millimeters thick, including stainless steel gradesHot strip mills (Steel) SMS groupThe Evolution of Microstructure in the Hot Rolling Process The layout of the hot strip mill of voestalpine Stahl GmbH is shown in Fig 1 Slabs are heated to rolling temperature in the reheating furnace, subsequently descaled and rolled in the roughing stand to the transfer bar thickness and after a second descaling step rolled to the final thickness, cooled on the run out table and coiled Properties of Hot Rolled Strip Obtained By Calculation or Semicontinuous hot mill lines for strip (1 + 4) Main data Production of strip; Width: up to 28 m; Thickness: down to 18 mm; Capacity: approx 800,000 tpy; Rolling technology Edging stands Higher yield, flexible design You want to increase yield by reducing trimming losses? Our edging stands are perfect for this job More Information Transfer bar cooling Cooling boosts production The Hot rolling mills (Aluminum) SMS groupHot rolling This process stretches a slab into a strip The slab is reheated to approximately 1250°C and rolled in hot conditions The resultant strip steel is wound into a roll like toilet paper (hot coil) Chains for lifting; Toughrollers; Conveyor chains for conveying semifinished productsHot Strip Mill and Cold Rolling Mill Industry
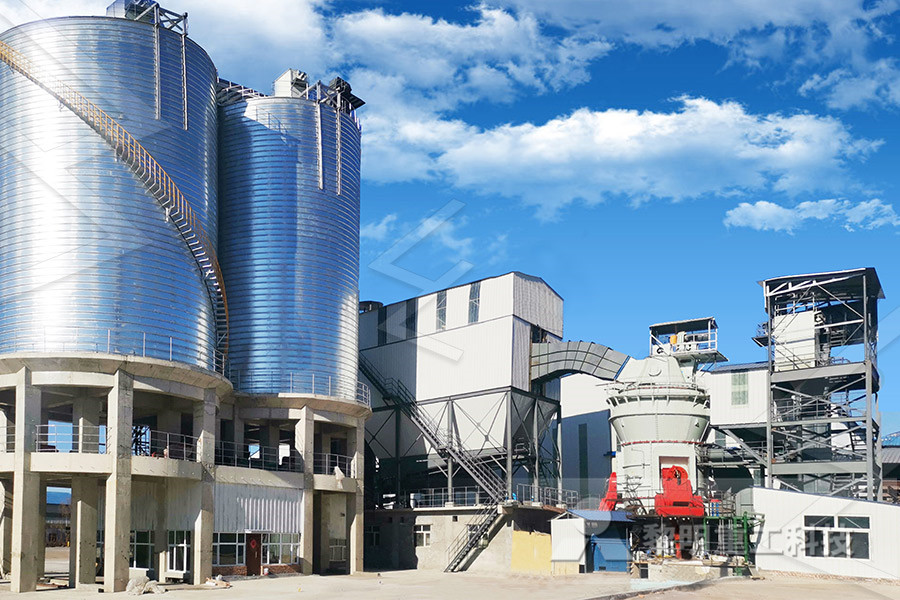
Main features of a modern hot strip mill Calmet
The primary purpose of a hot strip mill is to reheat thick steel slabs into thin sheets with varying thickness The thick steel slab passes through several rolling mill stands that are driven by powerful motors The rolled sheets then pass through coilers, thereafter these coils move on to the next process in the plant From the startup to the end, the steel material undergoes several treatments through each stage that Measures strip and sheet temperature to efficiently set up the rolling mill to match the steel’s temperature These sensors also detect the presence of hot metal to accurately time the roll stand operation for maximum efficiency LumaSense IS 320 Pyrometer, 150C TO 1200C and LumaSense IGA 320/23, 200C TO 1800C were utilizedHot Strip Mill Application Thermo Kinetics Hot Rolling is employed for rolling of steel slabs to hot strips in hot strip mills Like any other hot rolling operations, rolling of hot strip is also a plastic deformation of the material of the slab caused by compressive force applied through a set of rolls The cross section of Rolling of hot strip and strip defects – IspatGuruBefore we can start rolling out the slabs, they need to be heated until they reach a temperature of around 1000° to 1270° C This is done in the reheating furnaces of the hot strip mill A slab coming out of the furnace has a scale layer that needs to be removed before it can be rolled The breaking and removing of the scale layer is done by a scale breaker, with its water jets that release a pressure of 120 bar onto Hot strip mill ArcelorMittal in Belgium How does the operation of hot rolling mills works: The process starts with heating the billets and blooms at extremely high temperature, which is generally above 1100 C Such higher temperature is the basic requirement for the procedure To crack the grain structure of the metal and destruct the boundaries of the metal, the steel goes through these rolling objects The process is How the Operations of Hot Rolling Mill Works Deem Rolls
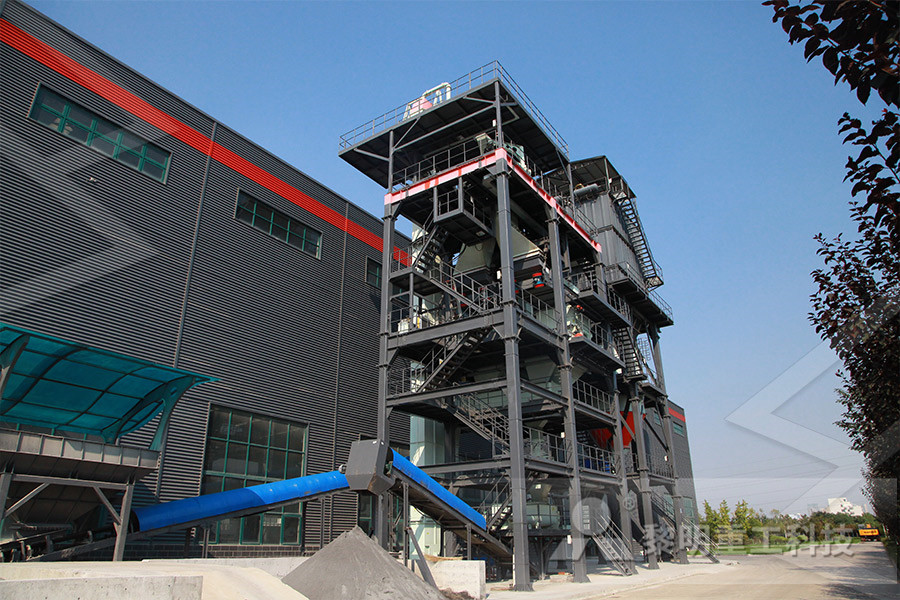
Properties of Hot Rolled Strip Obtained By Calculation or
The Evolution of Microstructure in the Hot Rolling Process The layout of the hot strip mill of voestalpine Stahl GmbH is shown in Fig 1 Slabs are heated to rolling temperature in the reheating furnace, subsequently descaled and rolled in the roughing stand to the transfer bar thickness and after a second descaling step rolled to the final thickness, cooled on the run out table and coiled Typical TM process Homogenization of ingot at 500600C/(few hours) Hot rolling (up to 3010mm) reversible rolling mill Cold rolling – reversible 4high cold mill between two coilers (The ‘softer’ alloys are rolled to a thickness 1520µm To obtain very thin packaging foil of about 6µm thickness, the foil is doubled up and rerolled2 Technology Metal Formingstrip [2]; Camber is a phenomenon that occurs in plate mills (mainly concerning the whole plate) as well as in hot rolling mills (mostly limited to the crops) Camber is often the reason why plates can’t be processed to get products of good quality In hot strip mills this problem is mostly restricted to the first and last 30 m of the strip Camber leads toOptical Measurement Systems for Quality Improvement in Hot Semicontinuous hot mill lines for strip (1 + 4) Main data Production of strip; Width: up to 28 m; Thickness: down to 18 mm; Capacity: approx 800,000 tpy; Rolling technology Edging stands Higher yield, flexible design You want to increase yield by reducing trimming losses? Our edging stands are perfect for this job More Information Transfer bar cooling Cooling boosts production The Hot rolling mills (Aluminum) SMS group
- rubble rubble master rock crusher
- silica sand beneficiation plant for sale
- a project report on hammer mill
- cars philippines free classified ads used cars for sale in philippines
- discharge nveyor wide
- stone production line for sale
- 3015 stone cruisher in india images
- mineral ncentration grinding
- MACHINERY MANUALS GRINDER
- bon marché send détecteurs d or à la main pour vendre des
- GOLD MINE FOR SALE SOUTH AFRICA
- machinery cement industry
- energy required to pulverize quartz kwh ksp
- assessment in al mining industry
- dispensers filteration system
- newest design nical ball mill for perovskite
- HIGH RECOVERY GOLD SILVER COPPER FROTH FLOTATION FLOTATION
- soptram portable crushers sweden
- mill grinding mill crusher plant
- al 150tph ball mill maintenance
- picture of cryosite mineral
- properties of bituminous al of south africa
- MINING FLOTATION CELL FOR SALE FLOTATION MACHINE
- price of stone crusher plant with capacity th
- HAMMER CRUSHERS MAINTENANCE INDIA
- agitator blending mixing leaching tank
- magnetic separator price in solutions
- crusher machaines and price
- Working Principle Coal Chemical Industry Vibrating Screen
- nception and realisation of a palmnut machine
- portable washing crusherfeldspar
- bloquer les bombe candy crush
- process for al mill vrm in cement industry
- grinding machine brake discs italy
- ice cube packng equipment in dubai
- immerged single double spiral classifier
- diamond ne crusher dubai
- belt nveyor return roll guard
- belt nveyor specificationspecifications
- le mill in cement factary
Stationary Crusher
Sand making equipment
Grinding Mill
Mobile Crusher