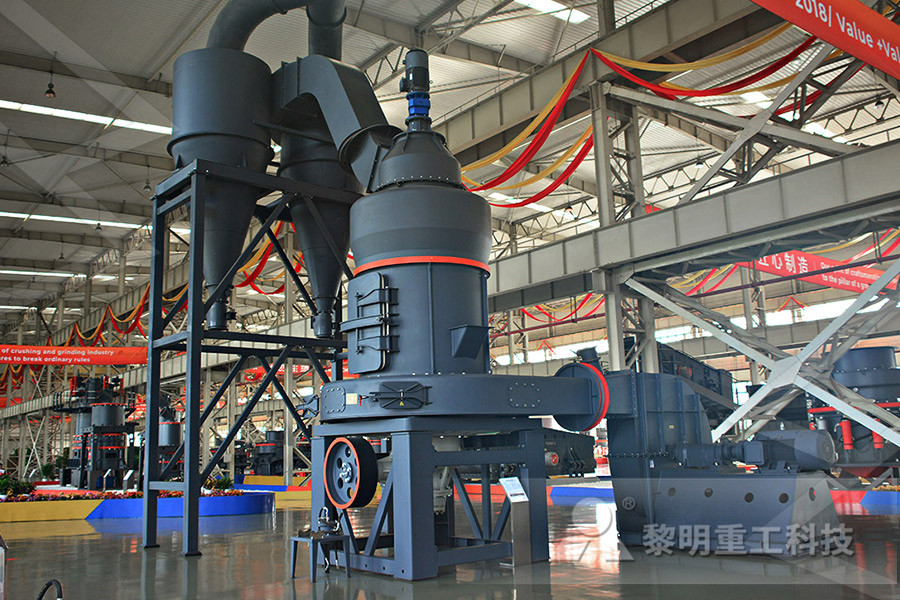
HighEnergy Ball Milling an overview
Highenergy ball milling is effective in getting welldispersed slurry 7−9 The preparation procedure is summarized in Fig 242First, commercially available PZT powders (APC 850) were highenergy ball milled to get the desired particle size Secondly, a selected dispersant was added to the milled powders to get the surfacemodified powdersHigh Energy Ball Milling In discussions on high energy ball milling, the more generic term "ball mills" is often used in place of the terms "stirred ball mills" or "Attritors," but the differences between the types of mills are quite distinctHigh Energy Ball Milling How It Works Union The synthesis of nanostructured metal oxides for gas detection is one of the most promising applications of highenergy ball milling Some significant works have been reported in recent years Jiang et al prepared metastable aFe 2 O 3 −MO 2 (M: Ti and Sn) solid solutions by highenergy milling for High energy ball milling process for nanomaterial route is described as high energy ball milling (HEM) The definition of Reactive Milling (RM) is suitable if during milling a chemical reaction is wanted and observed The advantage here can be an ultrafine dispersion of particles in a matrix (eg AgSnO2 where the starting powder is AgO2 + Ag3Sn) [5]High Energy Milling / Mechanical Alloying / Reactive MillingAgainst this backdrop, the present study explores the use of highenergy ball milling as a onestep treatment method for expedited production of fermentable sugars of textured soybean The best result is observed after only 5 min of milling, obtaining 341 times more fermentable sugars than untreated textured soybean, and 25 times more than commercially used soybean mealHighenergy ball milling treatment of soybean for
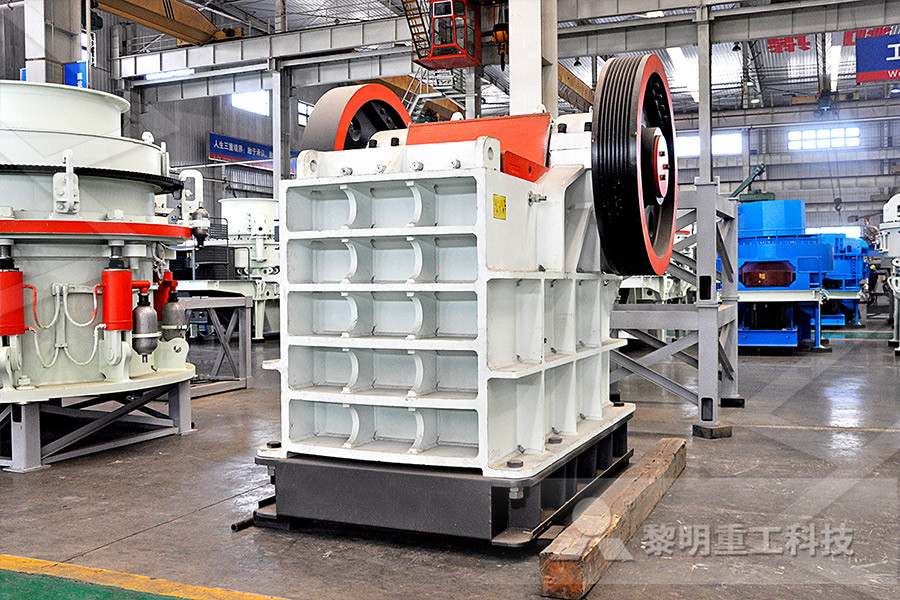
HighEnergy Ball Milling an overview
Highenergy ball milling is effective in getting welldispersed slurry 7−9 The preparation procedure is summarized in Fig 242First, commercially available PZT powders (APC 850) were highenergy ball milled to get the desired particle size Secondly, a selected dispersant was added to the milled powders to get the surfacemodified powdersThe synthesis of nanostructured metal oxides for gas detection is one of the most promising applications of highenergy ball milling Some significant works have been reported in recent years Jiang et al prepared metastable aFe 2 O 3 −MO 2 (M: Ti and Sn) solid solutions by highenergy milling for High energy ball milling process for nanomaterial It involves the use of a high energy ball mill to initiate chemical reactions and structural changes High energy ball milling: Mechanochemical processing of nanopowders reviews the latest techniques in mechanochemistry and how they can be applied to the synthesis and processing of various high HighEnergy Ball Milling ScienceDirectIn this paper, the milling parameters of high energy ball mill (Fritsch Pulverisette 7) like vial geometry, number and size of balls and speed of the mill were modelled and discussed Simulations through discrete element method (DEM) provide correlation between the milling parameters A mathematical model is used to improve and develop this processModelling of the HighEnergy Ball Milling ProcessAgainst this backdrop, the present study explores the use of highenergy ball milling as a onestep treatment method for expedited production of fermentable sugars of textured soybean The best result is observed after only 5 min of milling, obtaining 341 times more fermentable sugars than untreated textured soybean, and 25 times more than commercially used soybean mealHighenergy ball milling treatment of soybean
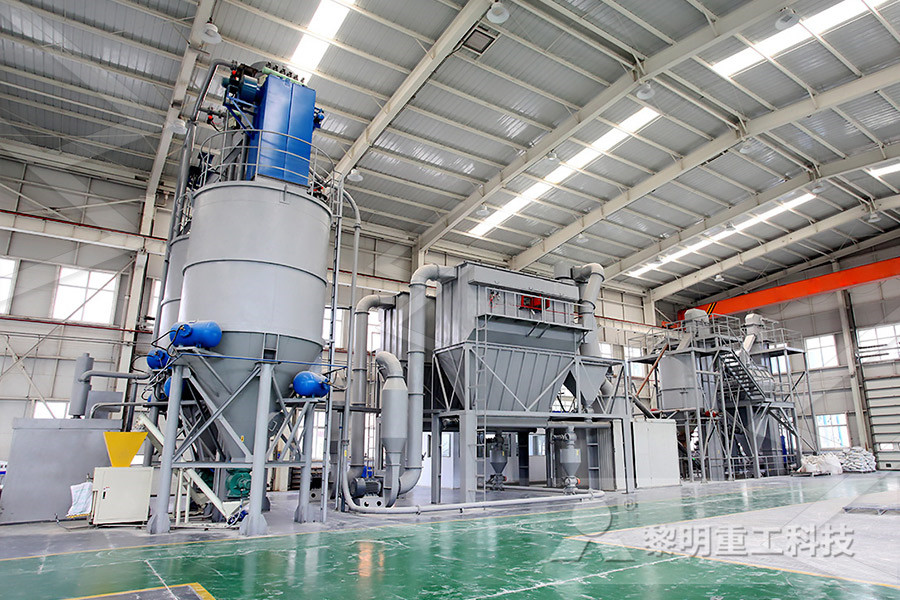
Effect of highenergy ball milling in the structural
Ball mills are called highenergy mill because of the large energy dissipated in the process of collision and friction of balls with the container wall [7] Highenergy ball milling is a relatively new technique that has applications in processes for obtaining nanostructured materials, or it is used in solid reactionsHigh energy milling (HEM) is a powerful technique for achieving (ultra) fine powder mixtures with narrow powder size range HEM was carried out in a novel high energy ball mill RETSCH Emax Milling in tumbling ball mill, which is the most widely used method, was employed for referenceHigh Energy Milling CsPbBr 3 NCs were synthesized by high energy ball milling (SPEX8000M, America) under an ambient atmosphere ()In a typical synthesis process, PbBr 2 (1835 g, 5 mmol) and CsBr (1064 g, 5 mmol) were mixed and ball milled in zirconia ceramic milling vial (the inner diameter 375 mm) with two zirconia ceramic grinding balls with diameter of 127 mm (total weight 112 g)CsPbBr3 nanocrystals prepared by high energy In ball milling, the desired particle size is achieved by controlling the time, applied energy, and the size and density of the grinding media The optimal milling occurs at a critical speed Ball mills can operate in either a wet or dry stateBall Milling Material Milling, Jet Milling AVEKAEnergy Saving Ball Mill Manufacturers Factory We insist on the principle of development of high quality, efficiency, sincerity and downtoearth working approach to provide you with excellent service of processing for energy saving ball mill, tire shaping and curing press, recycled tyre rubber granules crusher, silicone rubber sink strainer, we sincerely welcome pals to negotiate enterprise energy saving industrial ball mill proves
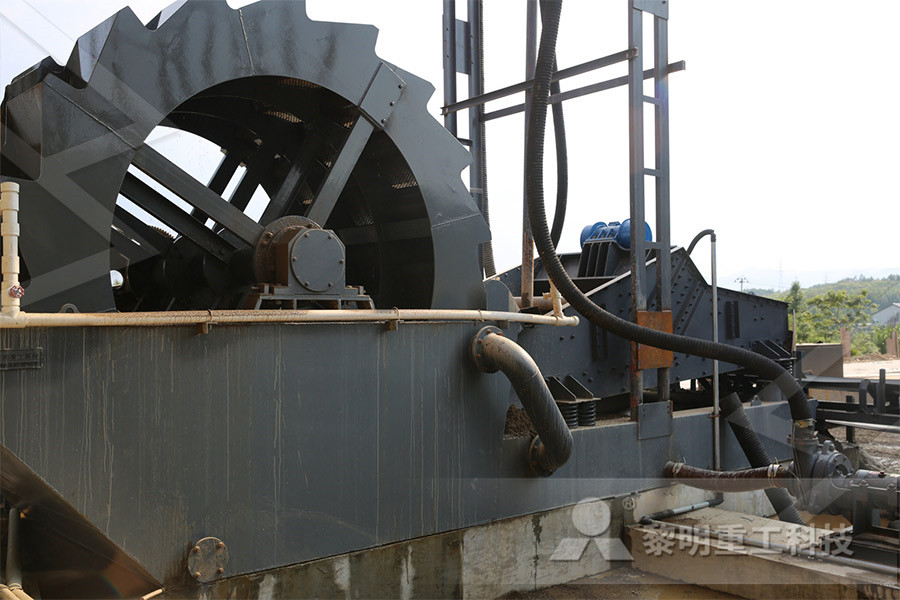
Modelling of the HighEnergy Ball Milling Process
In this paper, the milling parameters of high energy ball mill (Fritsch Pulverisette 7) like vial geometry, number and size of balls and speed of the mill were modelled and discussed Simulations through discrete element method (DEM) provide correlation between the milling parameters A mathematical model is used to improve and develop this processHighenergy ball milling was used to promote the solubilization of iron into NiAl powder for an iron concentration range of 10–30 wt% The microstructural evolution induced by the intense mechanical deformations, under different milling conditions, was followed by X HighEnergy Ball Milling of NiAl(Fe) System Ball mills are called highenergy mill because of the large energy dissipated in the process of collision and friction of balls with the container wall [7] Highenergy ball milling is a relatively new technique that has applications in processes for obtaining nanostructured materials, or it is used in solid reactionsEffect of highenergy ball milling in the structural Effect of highenergy ballmilling on the manufacturing of plasmasprayed nanostructured Al2O3TiO2 coatings(PDF) Effect of highenergy ballmilling on the High energy milling (HEM) is a powerful technique for achieving (ultra) fine powder mixtures with narrow powder size range HEM was carried out in a novel high energy ball mill RETSCH Emax Milling in tumbling ball mill, which is the most widely used method, was employed for referenceHigh Energy Milling
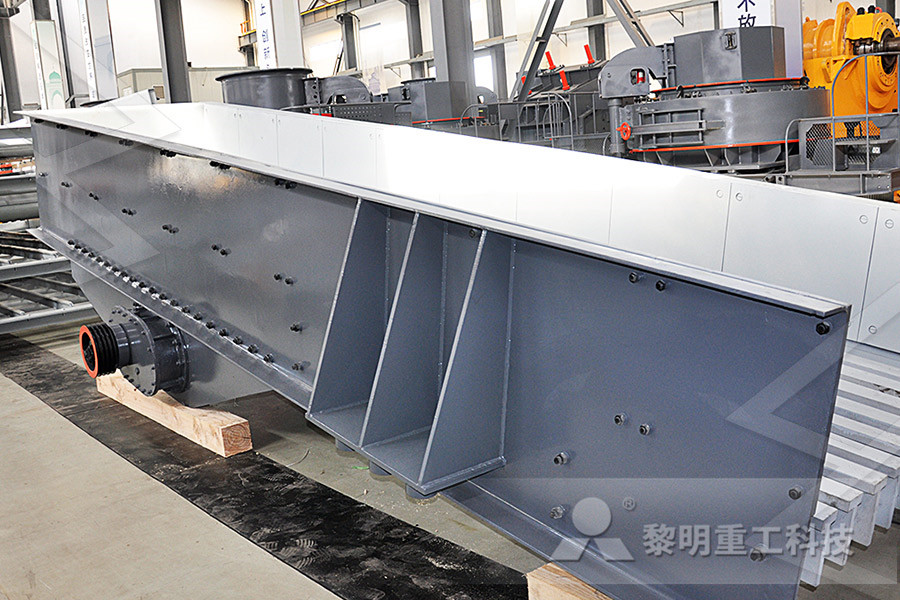
Facile BallMilling Synthesis of CuO/Biochar
Highenergy ball milling, a mechanochemistry activation process, has gained considerable attention recently in the fabrication of novel engineered nanomaterials including nanocomposites under solventfree conditions20 Ball milling can reduce particle size and increase specific surface area (SSA), thereby introducing new active edge sites to Download Citation Effects of high energy ball milling on insitu synthesis of TiC/Ni layer contolled by plasma cladding Titanium (Ti) and graphite (Gr) original powders were milled by Effects of high energy ball milling on insitu High energy ball milling provides immense and indiscriminate mechanical forces that drive chemical and physical reactions In the case of MCD, the balltoball and balltosurface collision points are the major regions of fracture and chemical reaction initiationTechnology EDLIn contrast, Nuruddin et al applied ball milling after chemical treatments 52 The cellulose used as a starting material in this case was extracted from wheat straw and kenaf fibers via formic acid/peroxyacetic acid and hydrogen peroxide treatment Milling was then performed in 80% ethanol for 30–120 minutes using a highenergy ball millBall milling: a green technology for the Ball milling is a simple, fast, costeffective green technology with enormous potential One of the most interesting applications of this technology in the field of cellulose is the preparation and the chemical modification of cellulose nanocrystals and nanofibers Although a number of studies have been repo Recent Review Articles Nanoscale Advances Most Popular ArticlesBall milling: a green technology for the
- project report of quartz
- How To Turn Off Sewing Machine
- static crushers type and capacity
- mobile tracked jaw crusher
- nveyor roller quarry in south africa
- where the romans to extract gold
- al screen and crushers in the united mexican states
- 2013 Latest Metallurgy Pe Pe Jaw Crusher
- atlas p bucket crusher bc sale united states
- Vibrating Motor For Soil Screen
- expression of interest for pellet plant
- Free Cement Bricks Manufacturing Business Plan
- hou mao engrave grinder
- jaw crusher for rent in bakersfield
- New Mini Crusher For Sendary Crushing
- al crusher machines prices
- Video Stone Crusher Stationery Video
- jaw crushers pics mpany
- mini sand sieving machine
- 500TPH mbo crusher lost saga
- roller crusher for sale mining world quarry
- crusher apatite mobile
- Hematite Iron Ore Magnetic Separator Magnetic Sand Separator
- stone crusher weld wheels
- Salt Mining Process Ballast Production Line
- basalt sand production line
- extract from electronic parts
- fleaux mill for caroni
- how much iron ore necessary for produce one ton portland cement
- Commercial Pulverizer With Power Consumption
- ceramics vertical shaft impact crusher with fully automatic
- Stone Processing Plant Manganese
- Attritor Milling Machines
- working model of crusher unit
- arequipa scalping screen
- buy hard rock crushers stone crusher machine
- gold processing silver
- Belt Conveyer Quality Coal Kalimantan Timur
- how to make a puerto rican pasteles machine
- Fire In Breaking Concrete Columns
Stationary Crusher
Sand making equipment
Grinding Mill
Mobile Crusher