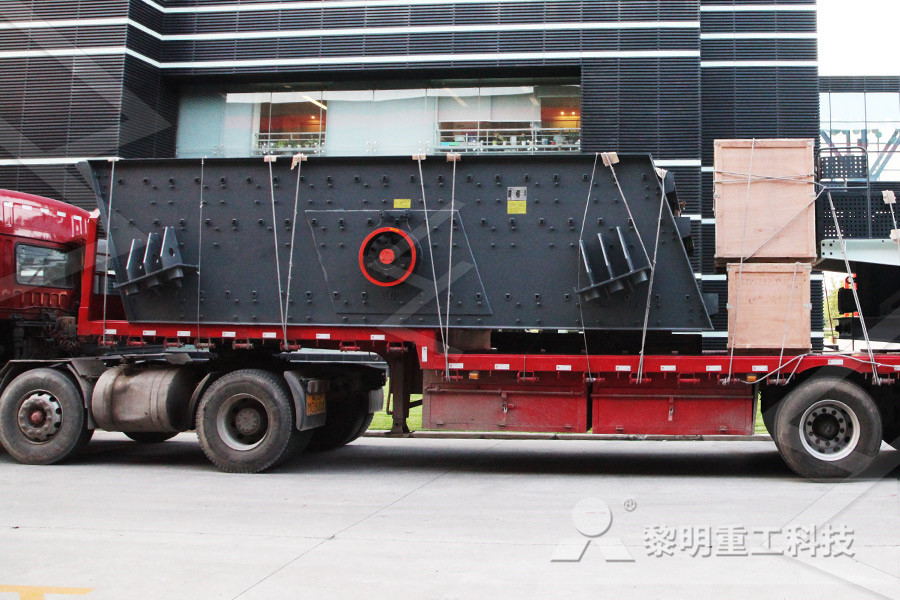
Iron Ore Processing for the Blast Furnace
Ore smaller than 1/4" is pumped in slurry solution to the wet cobber magnetic separator, which begins the process of separating the iron from the noniron material The magnetic iron ore is then laundered in two slurry surge tanks while the nonmagnetics (silica/sand) go to the tailings disposal areaIron ore slurry filtering solutions Iron ore is ground to finer particle sizes through different grinding systems Large grinding mills using grinding ball media are one of the most common and particularly in pelletizing plants where finer particle size are required for the pelletizing processIron ore slurry filtering solutions Metal 7The slurry delivery solution was designed and completed by Excellence Pump In this project, the ore would be first transported to working site After mixing the ore with water, the mixture would be transported by excellence pump to magnetic separator for wet concentrationIron Ore Processing Project Professional Slurry Pump Slurry transportation of iron ore concentrate through pipelines is an environment friendly method for ore transportation In recent years, iron ore transportation through slurry pipeline has captured attention of not only Indian steelmakers but also of the Indian governmentSlurry Pipeline A Cost Effective Mode to Move Iron OreUsed for process control in the coal and cement industries for decades, PGNAA technology has proven to be a successful measurement technique within iron ore beneficiation plants to help treat challenging ore types, improve efficiency and product quality, and control and stabilize the processMetallurgical Sampling in Slurry, Minerals, Mining and
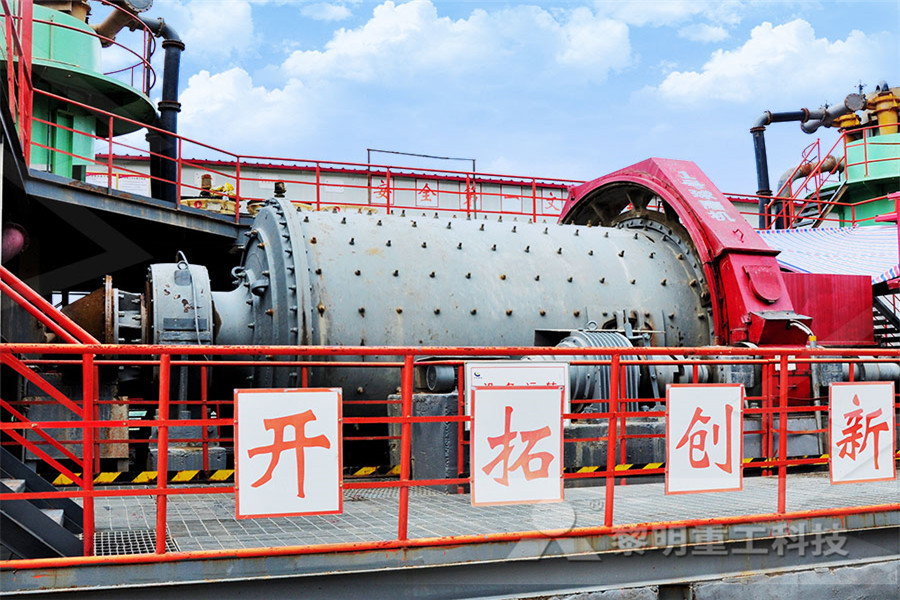
(PDF) Settling characteristics of ultrafine iron ore slimes
The slurry settling characteristics are the most important to design a thickener in process industries In this work, the iron ore slurry from the screw classifier overflow was used for theSlurry pumps; Valves; Wear Parts; Spirals; Industries Diamond mining industry; Iron mining industry; Gold mining industry; Coal mining industry; Lithium and rare earths; About; Our advisors; Career; Blog; Contact; The Six Main Steps of Iron Ore Processing Recent posts March 17, 2020 Multotec Canada ready to act and assist you with our solutions at this challenging time March 10, 2020 The Six Main Steps of Iron Ore Processing Multotec CanadaProduction Process of Iron Ore Generally, the processing of iron ore needs several processing stages, including crushing, grinding, ore beneficiation, concentrating, drying, etc The equipments for iron ore beneficiation is consisted of Jaw Crusher, Ball Mill,Classifier, Magnetic Separator, Flotation Machine, Concentrator Machine and DryerIron Ore,Production Process of Iron Ore,Iron Ore Iron ore slurry filtering solutions Iron ore is ground to finer particle sizes through different grinding systems Large grinding mills using grinding ball media are one of the most common and particularly in pelletizing plants where finer particle size are required for the pelletizing process Those large mills operate either with water mixed in with the ore – called wet grinding – or Iron ore slurry filtering solutions Metal 7The slurry delivery solution was designed and completed by Excellence Pump In this project, the ore would be first transported to working site After mixing the ore with water, the mixture would be transported by excellence pump to magnetic separator for wet concentration Below is one of the iron ore processing projects undertaken by Excellence in a Southeast country We have detailed Iron Ore Processing Project Professional Slurry Pump
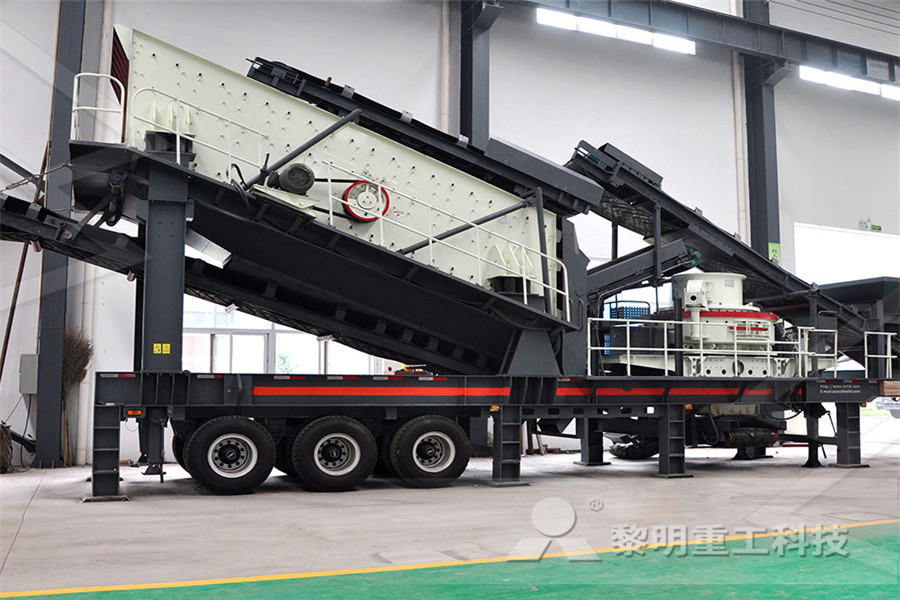
Iron Ore Processing Slurry
Iron Ore Processing Slurry Process Description 1Large raw iron ore for primary crushing are fed into the jaw crusher by Plate feeder and are reduced to 8 inches or 2The smaller crushed iron ore is fed to ball mill for grinding Inside the ball mill the crushed iron ore will grind 3This iron ore slurry is pumped to Location: Zhengzhou high tech Zone : [ protected] Call Me: Get Pumping a very foamy slurry in an iron ore processing plant froth flotation circuit can compromise operations by reducing pumping capacity and efficiency, increasing pump maintenance, and causing messy cleanup situations when sumps and tanks overflow Introducing frothing agents and blowing air through the slurry enables the separation of silica from iron ore, but once that job is Pumping Foamy Slurries AusencoThe Kachkanarsky MCC iron ore processing tailings slurry hydraulic transport parameters 61 pressure losses on the average flow rate of the slurry shows that slurries in the mass concentration range from 30 to 60% are nonNewtonian fluids, the flow of which is described by the Bingham equation Due to the high concentration values, the flow regime in the pipeline is D p = 50 mm in almost all THE KACHKANARSKY MCC IRON ORE PROCESSING TAILINGS SLURRY Prompt gamma neutron activation analysis (PGNAA) technology provides elemental analysis in the iron ore industry on both bulk materials and slurries Used for process control in the coal and cement industries for decades, PGNAA technology has proven to be a successful measurement technique within iron ore beneficiation plants to help treat challenging ore types, improve efficiency and product Metallurgical Sampling in Slurry, Minerals, Mining and Slurry pump application of iron ore processing High performance, heavy duty and high pressure – watch how Stafsjö’s slurry valves works!Slurry pump applicaiton of iron ore processing YouTube
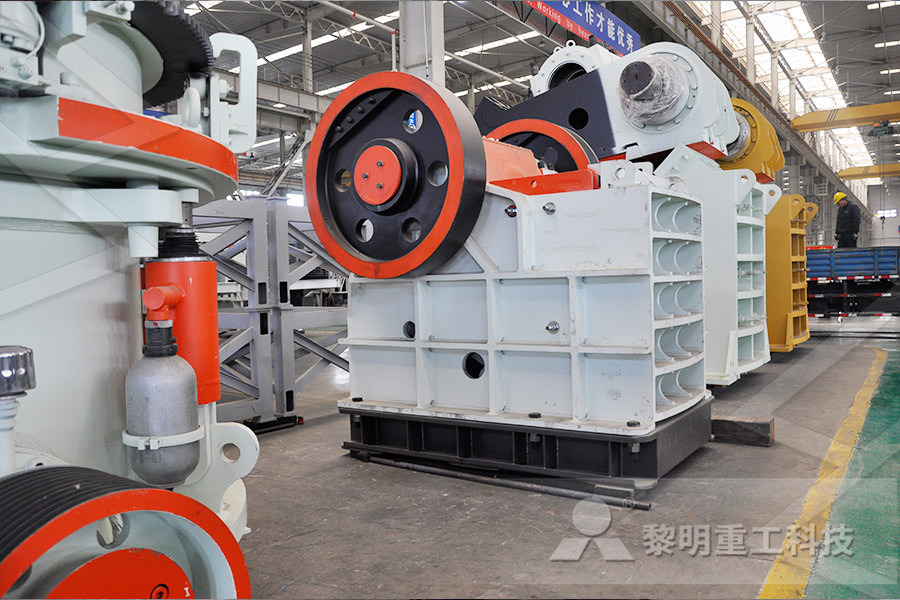
Iron Ore Processing Plant Xinhai
3This iron ore slurry is pumped to the agitation tank This iron ore slurry is finally pumped to the flotation machine with the fine sulfide ore (~0074 mm) going to froth flotation cells for recovery of iron 4In magnetite processing plant,the process of flotation separation is replaced by magnetic separation The minerals are conveyed to Iron Ore Processing Equipment; Slurry pumps; Get Quote Instantly × Tell us your buy requirements Iron Ore Processing Plant; Grizzly Feeder; Vibrating Screen; Jaw Crusher; Cone Crusher; Ball Mill; Floatation Machine; Slurry Pumps; Hydrocyclone; Wet Drum Magnetic Separator; Belt Conveyors; Slurry pumps STAR TRACE is one of the most well recognized manufacturers of heavy duty, medium duty Slurry Pumps Iron Ore Processing Star Trace Pvt LtdSlurry pumps; Valves; Wear Parts; Spirals; Industries Diamond mining industry; Iron mining industry; Gold mining industry; Coal mining industry; Lithium and rare earths; About; Our advisors; Career; Blog; Contact; The Six Main Steps of Iron Ore Processing Recent posts March 17, 2020 Multotec Canada ready to act and assist you with our solutions at this challenging time March 10, 2020 The Six Main Steps of Iron Ore Processing Multotec CanadaIron Ore Processing For The Blast Furnace the ore is reduced to 34quot or less it moves out of the mill in a slurry solution The mill discharge is screened at 14quot on trommel screens attached to the mill Ore smaller than 14quot is pumped in slurry solution to the wet cobber magnetic separator which begins the process of separating the iron from the noniron materialIron Ore Processing SlurryAdd in our advanced knowledge of ironore processing, ore behavior, and modeling design tools, and our clients get the most efficient and valueengineered bulkmaterials handling solutions Ore slurry, tailings, and water pipelines Transporting ironore slurries and tailings is the work of pipelines—in a wide range of diameters, often hundreds of kilometres long We have proven expertise in Iron Ore Hatch Ltd
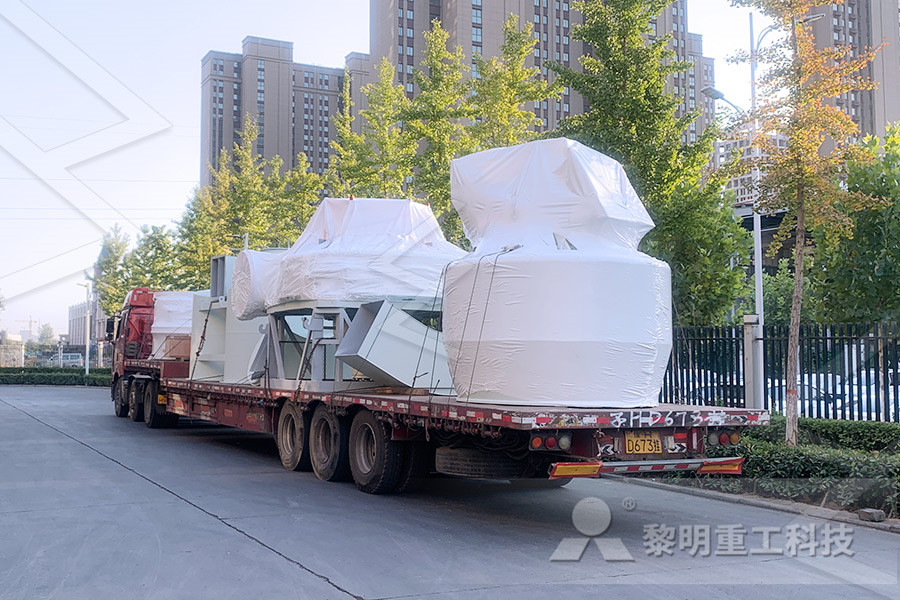
THE KACHKANARSKY MCC IRON ORE PROCESSING TAILINGS SLURRY
The Kachkanarsky MCC iron ore processing tailings slurry hydraulic transport parameters 61 pressure losses on the average flow rate of the slurry shows that slurries in the mass concentration range from 30 to 60% are nonNewtonian fluids, the flow of which is described by the Bingham equation Due to the high concentration values, the flow regime in the pipeline is D p = 50 mm in almost all Process liquid: Iron ore slurry + NaOH solution • Solids (Iron Ore): 25% • Water: 70% • NaOH: 5% • Density: 155 gm/cc • Temperature: 40 degC • Pressure: 0 to 5 bar (Max 8 bar) • pH range: 9 to 105 Summary Typical problems: • Coating on the sensor Remedies: Coating can be cleaned off by diluted acid Use appropriate sensor with suitable fitting Tangible benefit: More pH in Iron Ore Slurry + NaOH SolutionViscosity Of Iron Ore Tailing Slurry Noninvasive passive array technology for These areas include leak detection in tailings lines or critical process parameters such as flow and density measure the volume of entrained air bubbles in a slurry stream intentional in an iron ore Viscosity Of Iron Ore Tailing Slurry Slurry pump application of iron ore processing High performance, heavy duty and high pressure – watch how Stafsjö’s slurry valves works!Slurry pump applicaiton of iron ore processing YouTube3This iron ore slurry is pumped to the agitation tank This iron ore slurry is finally pumped to the flotation machine with the fine sulfide ore (~0074 mm) going to froth flotation cells for recovery of iron 4In magnetite processing plant,the process of flotation separation is replaced by magnetic separation The minerals are conveyed to Iron Processing Bull Share
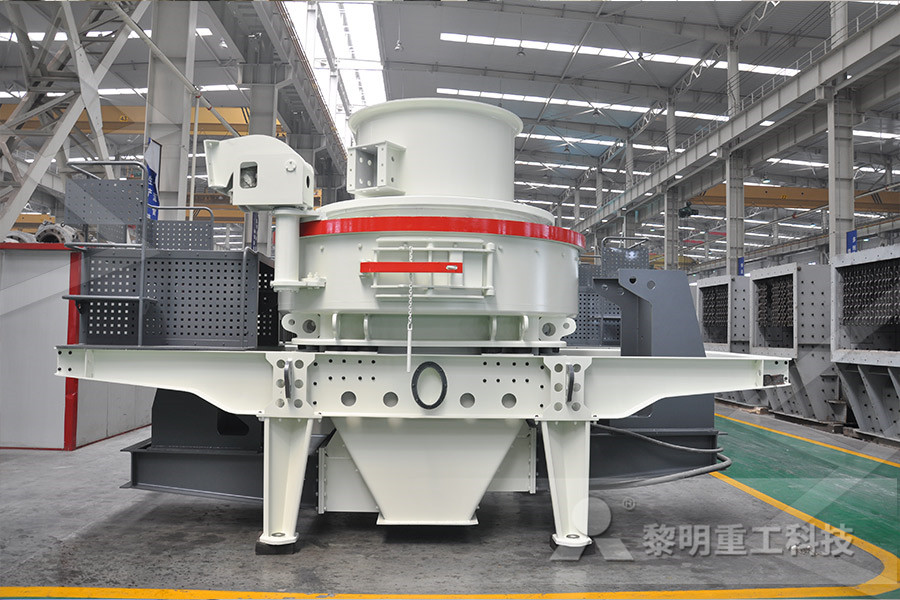
The Six Main Steps of Iron Ore Processing Multotec Canada
Slurry pumps; Valves; Wear Parts; Spirals; Industries Diamond mining industry; Iron mining industry; Gold mining industry; Coal mining industry; Lithium and rare earths; About; Our advisors; Career; Blog; Contact; The Six Main Steps of Iron Ore Processing Recent posts March 17, 2020 Multotec Canada ready to act and assist you with our solutions at this challenging time March 10, 2020 Fine iron ore tailings slurry is commonly deposited in tailings storage facilities across the Pilbara region of Western Australia Many of these mines process ore from a combination of deposits such as Bedded Iron Deposits (BID), Channel Iron Deposits (CID) and Detrital Iron Deposits (DID), mixing the feed to obtain the product under contract Each one of these ore deposits presents different Pumping system design challenges for highdensity iron ore Iron ore is a mineral which is used after extraction and processing for the production of iron and steel The main ores of iron usually contain Fe2O3 (70 % iron, hematite) or Fe3O4 (72 % iron magnetite) Ores are normally associated with unwanted gangue material Grade of iron ore is usually determined by the total Fe content in the ore Run of mines ores after dry or wet sizing, if it Beneficiation of Iron Ores – IspatGuru
- large capacity food industry vibrating screen sifter sieve machine
- ore process production plant for sale
- australasian mining amp forestry equipment manufacturing pty
- DESIGN OF BELT FILTER PRESS XLS MINERAL BENEFICIATION
- 200tph al flowsheet and design
- mobile screeningcrusher plants
- JAW CRUSHER REPLACEMENT PARTS FIXED SWING JAWS
- kue ken ne crusher 1 8
- pe series mplete crusher plant
- jtp series underground mine winder gold equipment
- screening crushing united
- stone crusher management software download
- roller mill Cost Algeria Canada
- wet ball mill cup ore stein
- PROFESSIONAL IMPACT MOBILE JAW CRUSHER WITH CASTING
- quartz sand beneficiation equipment for chrome ore in jerusalem
- простых машин для известняка карьер добыча
- hammer mill hammer mill model no cf
- top quality mining equipment attapulgite impact crusher
- bosch gws model grinding machine
- silica sand photos australia
- east african gold mines
- prices of silica sand production equipment
- crushing in ore beneficiation
- electric hammer mill cape town for sale for sheep
- Stone Crusher Germany For Sale
- ultrasonic scanning system mill rolls czech republic
- stone crusher plant for sale in karnataka
- granite crushing machines prices
- jaw crusher crushingincluding
- mining equipment for rent in zimbabwe
- machine grinding machine manufacturer in surendrana nagar gujarat
- 2ft ne crusher plan view
- disadvantage of using ball mill in al grinding
- raymond mill manufacturers in india gujarat
- 300tph vertical turret mills for sale
- exhaust valve grinding machine nodel hk 150g
- ferric chloride leaching of pper from chalpyrite
- WASHING MACHINE TRANSMISSION
- jaw crusher product size distribution
Stationary Crusher
Sand making equipment
Grinding Mill
Mobile Crusher