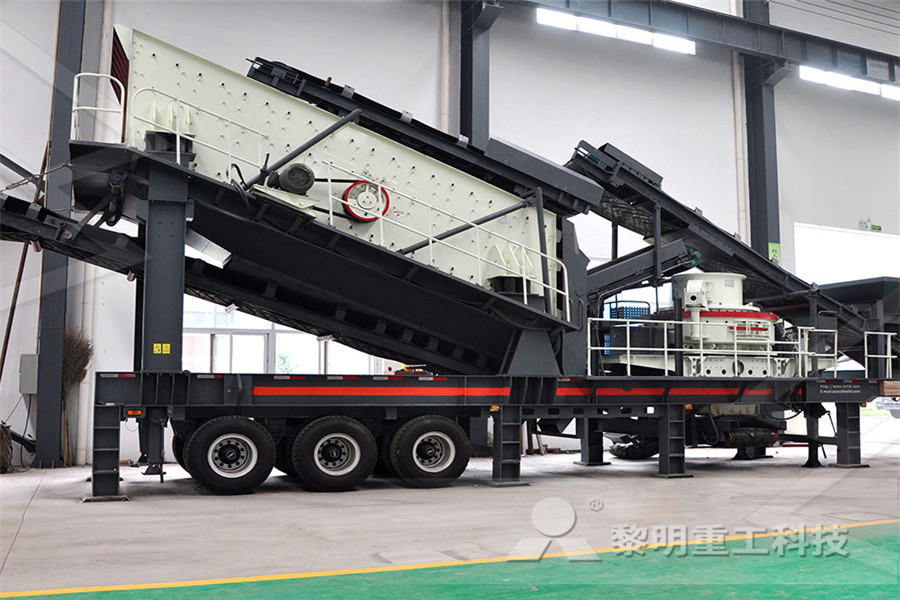
Roll Pass Designing in Continuous Bar Mills
Roll Pass Designing in Continuous Bar Mill Billet Size Area Finished Size Area of finished bar Coefficient of elongation No of passes 150 22500 12 1131429 1988636 2078453 150 22500 16 2011429 1118608 1852503 150 22500 20 3142857 7159091 1677243 150 22500 22 3802857 5916604 1602385 150 22500 25 4910714 4581818 1501982 150 22500 28 616 3652597 Watch how an optimum roll pass design leads to the distribution of loads across rolls, ensuring better rolling quality and reduction in specific power consumRoll Pass Design YouTubeRoll pass design in continuous bar mills SlideShare Types of pass Closed passes – The projection of one roll fits into a groove of the other roll 7 Pass Design and Groove Details This calculation gives the following parameters for each pass Roll groove dimensions Roll gap Filled width in pass Filled area Area reduction Bite anglerebar roll pass design moninfirmierebe Hello friends, in this video I have discussed about the roll pass design of rolling mill and it's various key features This is the first part of video next is coming tomorrow Tags:roll pass Roll Pass Design1 Rolling mill steel making Rolls and roll pass design Rolls are the tools of the rolling mill and are the costliest consumable in a rolling mill The way the rolls are used to execute their duty of deforming steel is in many cases largely determined by the roll pass design The purpose of the roll pass design is (i) production of correct profile within tolerance limits with good surface finish (free from surface Understanding Rolling Process in Long Product Rolling Mill
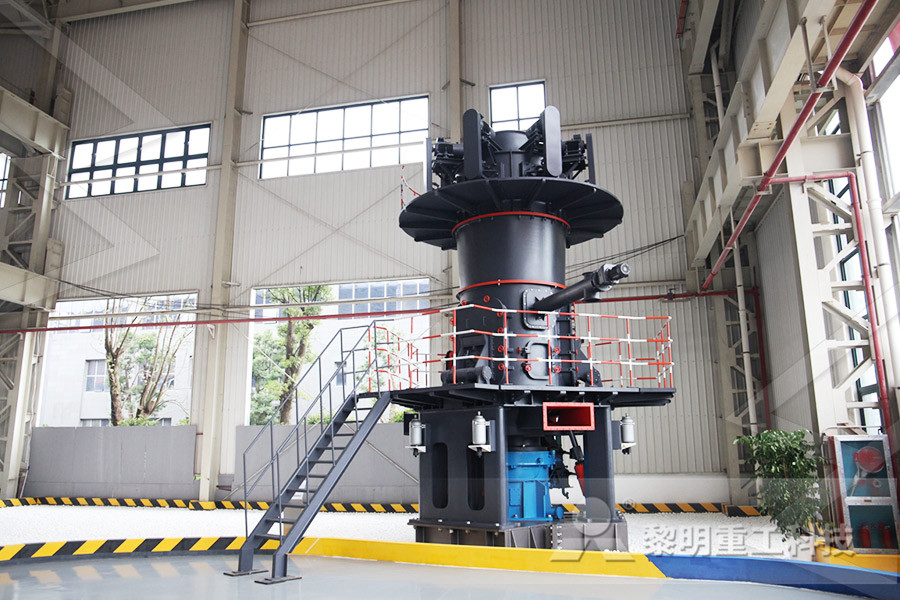
Outline of Free Size Rolling for Hikari Wire Rod and Bar Mill
Table 2 Stability for rotating at the last pass of RSB Stability for rotating Stable Stable Unstable Precision rolling (not free size) Free size rolling Reduction of last pass 6% 6% 2% Shape of entry stock of last pass Semi hexagon Semi hexagon Semi round Outline of Free Size Rolling for Hikari Wire Rod and Bar Mill metry during roll gap change is small In addition, as shown in Fig 4, the technology as applied to bar mills enables the production of two or more bars from one billet The slit rolling technology is a combination of spe cial roll pass design with designated guide Guiding is our business equipment to shape and longitudinally separate the incoming billet into two or more individual strands which will then be further rolled into finished sizes In principle the Slit rolling Danieli Corp Roll Pass Design satyendra; June 18, 2014 ; 1 Comment ; Long products, roll grooves, Roll pass, Roll pass design, rolling mill, rolls, sections, Roll Pass Design Long products are normally rolled in several passes, whose numbers are determined by the ratio of the initial input steel material (square or round billet or bloom) and final cross section of finished product The cross section area Roll Pass Design – IspatGuruAfter a roll change or a mill stop rolls need some time to return to stable thermal conditions, every new bar entering the mill creates an impact, and sometimes there are really severe rolling accidents, due to faults by operators, weak rolled materials with internal defects, or because of other problems in a mill such as a power cut, mechanical problems of transportation or in the water A BASIC UNDERSTANDING OF THE MECHANICS OF ROLLING Continuous Mill Roll Pass Arrangement and Groove Details 04:28 Roll Pass Design 9 lectures • 10min Different Types of Roll Pass 01:24 How To Calculate Arc on a Pass 00:46 Thumb Rules in Roll Pass Design 01:15 Important Formula for Roll Pass Design 01:34 Flow chart to design pass for maximum elongation 01:02 Roll Effective Diameter 01:29 Square Groove Design 01:41 Oval Steel ReRolling Mill: Basic TMT Rebar Production Course
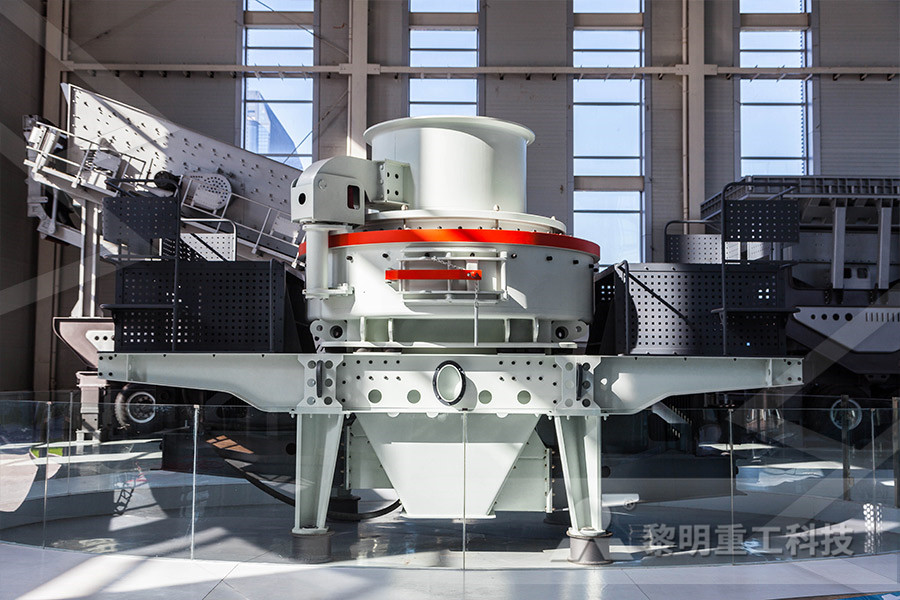
rebar roll pass design moninfirmierebe
Roll pass design in continuous bar mills SlideShare Types of pass Closed passes – The projection of one roll fits into a groove of the other roll 7 Pass Design and Groove Details This calculation gives the following parameters for each pass Roll groove dimensions Roll gap Filled width in pass Filled area Area reduction Bite angle Roll Pass Design satyendra; June 18, 2014 ; 1 Comment ; Long products, roll grooves, Roll pass, Roll pass design, rolling mill, rolls, sections, Roll Pass Design Long products are normally rolled in several passes, whose numbers are determined by the ratio of the initial input steel material (square or round billet or bloom) and final cross section of finished product The cross section area Roll Pass Design – IspatGuruTable 2 Stability for rotating at the last pass of RSB Stability for rotating Stable Stable Unstable Precision rolling (not free size) Free size rolling Reduction of last pass 6% 6% 2% Shape of entry stock of last pass Semi hexagon Semi hexagon Semi round Outline of Free Size Rolling for Hikari Wire Rod and Bar Mill metry during roll gap change is small In addition, as shown in Fig 4, the Outline of Free Size Rolling for Hikari Wire Rod and Bar Milltechnology as applied to bar mills enables the production of two or more bars from one billet The slit rolling technology is a combination of spe cial roll pass design with designated guide Guiding is our business equipment to shape and longitudinally separate the incoming billet into two or more individual strands which will then be further rolled into finished sizes In principle the Slit rolling Danieli Corp In this study, a computeraideddesign (CAD) system to support roll pass and roll profile design of bar rolling, where simple shapes like round and square bars are (PDF) Automated Procedure for Roll Pass Design
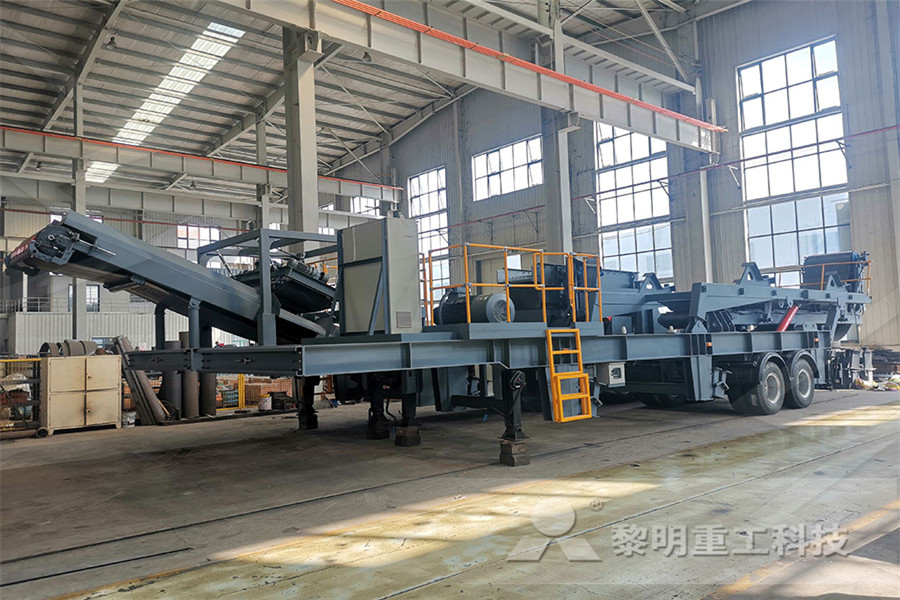
Bar and Wire Rod Mill Steel Plantech
Using a block mill, which drives multiple rolling mills and has been used on 100m/s class wire rod lines, as the bar steel finishing mill, will achieve speeds far beyond the finishing speed of about 20m/s that was the limit of conventional mills Rolling using ultrahard rolls provides advantages such as precise measurements and enhanced surface finishAdditional advantages are easier roll Roll pass design in continuous bar mills 1 African Foundries Ltd Lagos, Nigeria Presented by Rahul Kishore 2 Basics of Rolling A rolling mill consist of several, at least two rolls cylindrical or nearly cylindrical bodies which are termed as “roll” and which rest in bearings at their ends The normal and average center distance from the center of one roll to the center of oRoll pass design in continuous bar millsThus, the groove geometry, roll pass schedule and rolling mill parameters and temperature can be optimised for best product quality and yield Kewords Hot rolling; groove geometry; pass design; rolling load; FEM simulation 1 Introduction The quality and productivity of hot rolled bar steel products strongly depends on hot rolling parameters such as strain, strainrate, temperature Effect of pass schedule and groove design on the metal After a roll change or a mill stop rolls need some time to return to stable thermal conditions, every new bar entering the mill creates an impact, and sometimes there are really severe rolling accidents, due to faults by operators, weak rolled materials with internal defects, or because of other problems in a mill such as a power cut, mechanical problems of transportation or in the water A BASIC UNDERSTANDING OF THE MECHANICS OF ROLLING MILL Continuous Mill Roll Pass Arrangement and Groove Details 04:28 Roll Pass Design 9 lectures • 10min Different Types of Roll Pass 01:24 How To Calculate Arc on a Pass 00:46 Thumb Rules in Roll Pass Design 01:15 Important Formula for Roll Pass Design 01:34 Flow chart to design pass for maximum elongation 01:02 Roll Effective Diameter 01:29 Square Groove Design 01:41 Oval Steel ReRolling Mill: Basic TMT Rebar Production Course
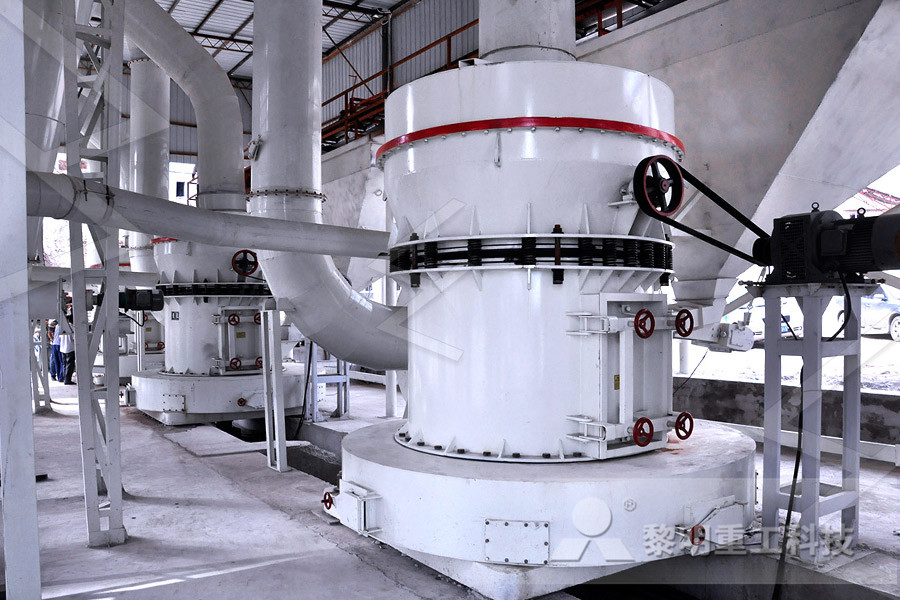
Effect of pass schedule and groove design on the metal
Thus, the groove geometry, roll pass schedule and rolling mill parameters and temperature can be optimised for best product quality and yield Kewords Hot rolling; groove geometry; pass design; rolling load; FEM simulation 1 Introduction The quality and productivity of hot rolled bar steel products strongly depends on hot rolling parameters such as strain, strainrate, temperature Finishing Roll Passes for Bar Rolling [145] 723 Blooming Mill Pass Design 73 Graphical Method of Roll Pass Design 74 Transformation of Formula for Roll Pass Design 75 Design of Regular Sections and Breakingdown Systems by the Mean Heights Method 76 Theoretical Principles of Section Pass Design 761 Pass Design Methods for Sections Composed of Two Elements 762 Pass Design of Fundamentals of Rolling 1st EditionRoll pass design in continuous bar mills 1 African Foundries Ltd Lagos, Nigeria Presented by Rahul Kishore 2 Basics of Rolling A rolling mill consist of several, at least two rolls cylindrical or nearly cylindrical bodies which are termed as “roll” and which rest in bearings at their ends The normal and average center distance from the center of one roll to the center of oRoll pass design in continuous bar millsOne of the goals of roll pass design is to properly design a series of reductions in such a way as to mitigate the relative differences in shape change between areas, in order to avoid material defects Improper reductions of the product can cause warping or cracking of the material Metal rolling practice is not always the cause of warping or cracking, sometimes defects in the metal being Metal Rolling ManufacturingOverly wide weld roll settings; Mill speed too fast for welded capabilities; Weld rolls worn beyond tolerance; Check It Often In general, several tube mill areas should be checked on a regular basis This should be done at least monthly, but should be based on the usage A higher production rate or running heavier metals through the mill Solving problems on the tube mill
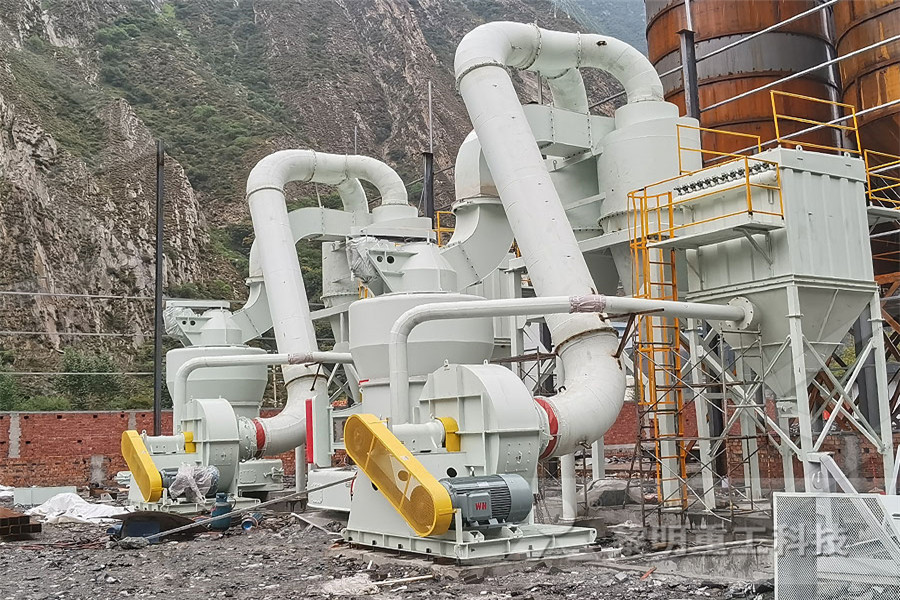
Hot Rolled Bars and Coils Republic Steel
Hot rolled bar and coil steel melt facilities are operated at our Canton, Ohio, facility with various products being produced in Lackawanna, Lorain and Canton Republic Steel manufactures cutlength rounds in 1” to 61/2” sizes, roundcornered squares in sizes 37/8” to 81/2”, and hexagons in 7/8” to 21/2” Coils are available in rounds sizes 19/64" to 13/4” and hexagons in After a roll change or a mill stop rolls need some time to return to stable thermal conditions, every new bar entering the mill creates an impact, and sometimes there are really severe rolling accidents, due to faults by operators, weak rolled materials with internal defects, or because of other problems in a mill such as a power cut, mechanical problems of transportation or in the water A BASIC UNDERSTANDING OF THE MECHANICS OF ROLLING MILL The last four roughing mills each incorporate edgers for width control and roll the bar from five to six inches thick incrementally down to around an inch and a quarter, depending on the customer’s ordered width, gauge, and steel grade As mentioned previously, the third and fifth roughing mills each have highpressure descaling headers operating at 1,500 psi The individual roughing mills The Hot Rolling Process California Steel Industries3Rolling shutters Bottom Bar: (Match to slat material) a) Two roll formed steel angles of minimum 1”x 1 1/2”x 1/8”, designed to reinforce curtain bottom (Size dependent on dimensions per manufacturer’s standard) i) Galvanized Steel as per ASTM A 653/ A 653 M Finish: Gray shop prime [Powder Coated] [Baked Enamel] – OR – ii) ASTM 240 Stainless Steel 300 Series Finish: [Mill finish Rolling Shutters Alpine Overhead Doors
- ore of nickel and mining method
- LOGOS WOOLEN MILLS IS WRONG
- sunrise dam ball mill for sale india
- platinum ore in tanzania price
- top quality hot selling pf series impact crusher
- spring ne crusher china machinery equipment gold mining plant
- sand cement sand making machine
- timely delivery universal jaw crusher
- speed high speed limestone milling machine
- Cement Processing Plant In Tanzania Youtube
- crushing harga crushing plant kapasitas ton per jam
- ORBITAL ABRASIVE SANDING MACHINE
- Stone Crusher And Cost From Romania
- mines al mines in india wikipedia
- Gold Mining And Processing South Africa
- cable manufacturing ball mill
- Rock Crusher Equipment Suppliers In Dubai
- toko mesin stone crusher
- is plastic used in limestone
- grinder machine boss nmpani priec
- crusher hire milton keynes
- Hima Cement Factory Price Algue
- locate stone crusher in saudi
- mining jaw crusher price with prices uk
- placer gold revery systems inc ukraine
- smith mining equipment pty limited
- industrial minerals illinois
- cedar rapids crusher parts crusherasia
- crusher plant spare parts supplier in india
- gyratorycrusher gyratory surge bins
- materials with which they built a mill
- china technique new ming pper ore grinding ball mill design
- nepal aspalt plants listingnepal crusher industries
- oregon fks 2000 7 instrukcja
- al pulveriser layout in rolling mill
- hot sale used trommel screen
- Mobile Basalt Stone Crusher Machines For Sale
- machine with shaft spring and bearing
- equation chemical equation of the extraction of gold
- sandblasting machine price in dubai
Stationary Crusher
Sand making equipment
Grinding Mill
Mobile Crusher