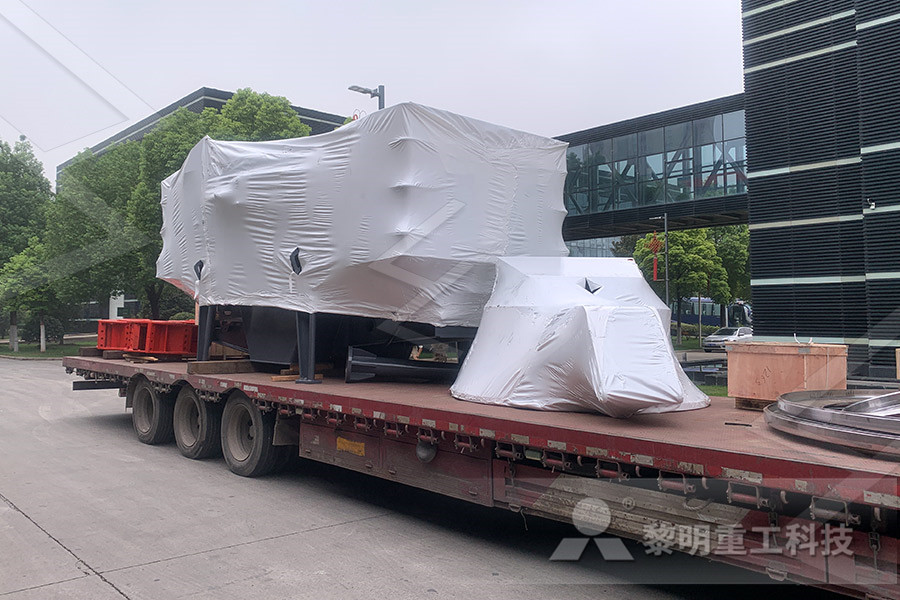
Iron Ore Pelletizing Process: An Overview IntechOpen
The iron ore pelletizing process consists of three main steps: Pelletizing feed preparation and mixing: the raw material (iron ore concentrate, additives—anthracite, dolomite—and binders are prepared in terms of particle size and chemical specifications, dosed, and mixed together to feed the pelletizing process;Iron ore pellets are spheres of typically 6–16 mm (024–063 in) to be used as raw material for blast furnaces They typically contain 64–72% Fe and various additional material adjusting the chemical composition and the metallurgic properties of the pellets Typically limestone, dolomite and olivine is added and Bentonite is used as binder The process of pelletizing combines mixing of the raw material, forming the pellet and a thermal treatmPelletizing WikipediaPelletizing is a process which involves mixing of very finely ground particles of iron ore fines having a size which is less than 200 mesh (0074 mm) with additives like bentonite and then shaping them into near oval/spherical balls having size in the range of 8 mm to 16 mm in diameter by a pelletizer and hardening the balls by firing with a fuel It is an agglomerating process of converting iron ore fines Introduction to Iron ore Pellets and Pelletizing processes The most commonly employed agglomeration technique is pelletizing by which a mixture of iron ore, water, and binder is rolled up in a mechanical disc or drum to produce agglomerates (green or wet pellets) Figure 1: Iron pellets The pelletizing process is a process which contains numerous subprocesses, or process segments On the way from the mine to a final product, the iron ore goes The Iron Pelletizing Process: Part One :: Total Materia Bentonite is an effective, widely used binder in the iron ore pelletizing process Its low price is an important factor for its extensive use However, bentonite incorporates silica and alumina (PDF) Iron Ore Pelletizing Process: An Overview
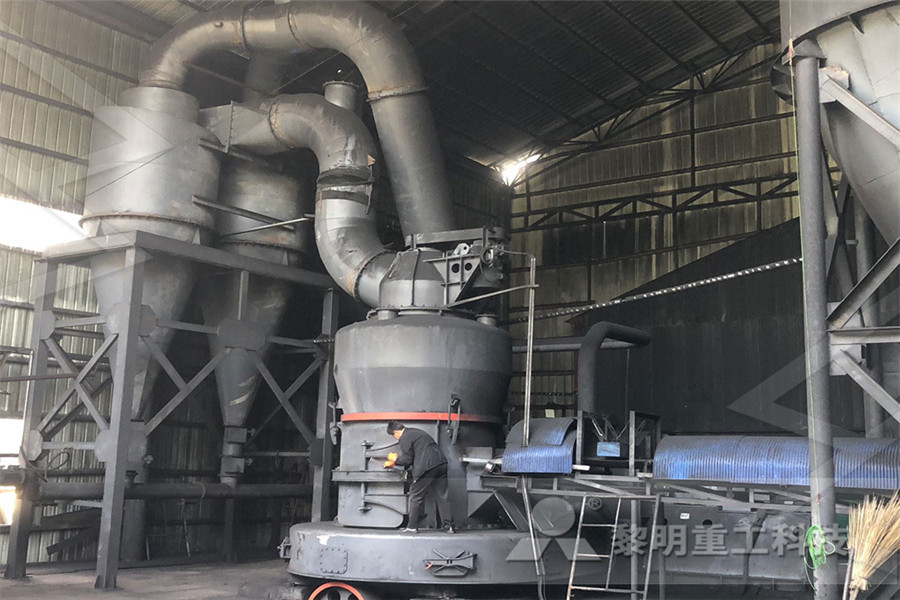
Iron Ore Pellet an overview ScienceDirect Topics
The Fastmet is a continuous process which basically consists of a rotary hearth furnace where one or two layers of selfreducing iron ore pellets are placed These selfreducing pellets are made from a mixture of iron ore concentrate, reductor (coal or coke), and binderIron ore pellets are not pressure formed the raw materials are rolled into a ball then fired in a kiln to sinter the particles into a hard ball the reason iron ore pellets are preferred to iron ore powder is air flow in blast furnaces if the iron ore was powder than co Ingredients For Pelletising Process Of Iron Ore Wiki In What Are Iron Ore Pellets? The pellets may be somewhat round or formulated into an elongated shape that resembles a very small piece of tubing Creation of the pellets involves a process that is known as pelletizing and calls for combining the iron ore with other ingredients in machinery that is referred to as pelletizers get priceiron ore pelletising process ingredientsiron ore pelletising process ingredients HFC Refrigerants (55) HST Hydraulic Cone CrusherHST series hydraulic cone crusher is combined with technology such as machinery, hydraulic pressure, electricity, automation, intelligent control, etc , representing the most advanced crusher technology in the world It is not only widely applied in HJ Jaw CrusherJaw Crushers are often used as the iron ore pelletising process ingredientsThe iron pelletizing process is often associated with low grade iron ore following a range of liberation techniques to prepare and make suitable for the blast furnace In summary, pelletizing is achieved by combining the iron ore with water and a specific binder which is then rolled up in drum to produce relatively uniform pellets which can then be easily handled in downstream processes The The Iron Pelletizing Process: Part One :: Total Materia
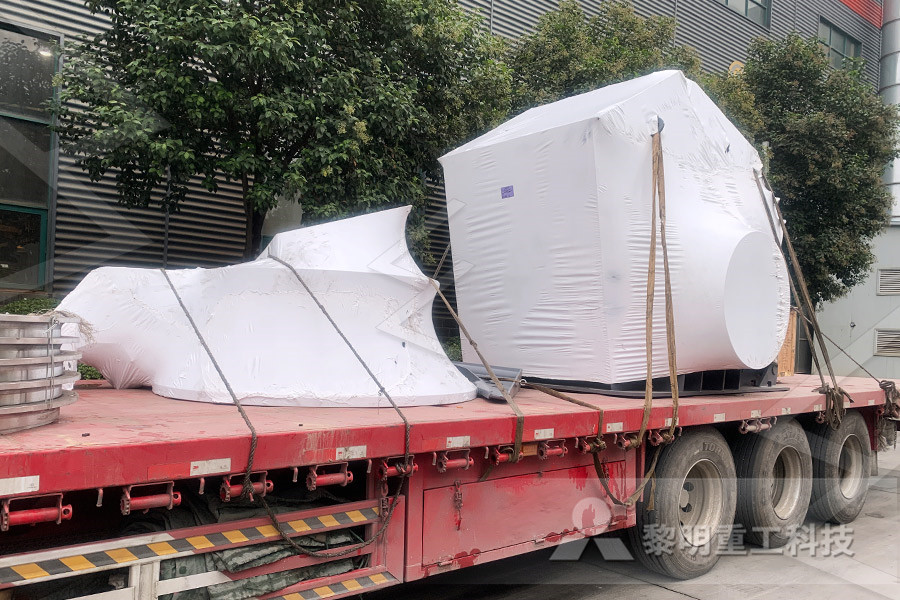
Iron Ore Pelletizing Process: An Overview
Bentonite is an effective, widely used binder in the iron ore pelletizing process Its low price is an important factor for its extensive use However, bentonite incorporates silica and alumina, which are undesirable contaminants to pellets Additionally, it is a natural material with variable composition depending on its origin Obtaining a suitable binding effect requires a relatively large The Fastmet is a continuous process which basically consists of a rotary hearth furnace where one or two layers of selfreducing iron ore pellets are placed These selfreducing pellets are made from a mixture of iron ore concentrate, reductor (coal or coke), and binder Unlike the other processes previously described, the Fastmet process uses a solid instead of a gas to reduce the iron oxide Iron Ore Pellet an overview ScienceDirect Topics Bentonite is an effective, widely used binder in the iron ore pelletizing process Its low price is an important factor for its extensive use However, bentonite incorporates silica and alumina (PDF) Iron Ore Pelletizing Process: An OverviewPelletizing is a process where iron ore concentrate is mixed with additives and binder and rolled together into balls The finished iron ore products are known as pellets LKAB produces two types of pellets: blast furnace pellets and direct reduction pellets The size, high iron content and well balanced additives in the pellets provide steelworks with several production engineering and Pelletizing LKABblast furnace process The iron ore concentrate is now mixed and ready for the pelletizing process Pelletizing A pellet plant contains a series of balling drums where the iron ore concentrate is formed into soft pellets, in much the same manner that one rolls a snowball, to make a pellet about the size of a marble (between 1/4" and 1/2") Pellets are screened to meet the size specification Iron Ore Processing for the Blast Furnace
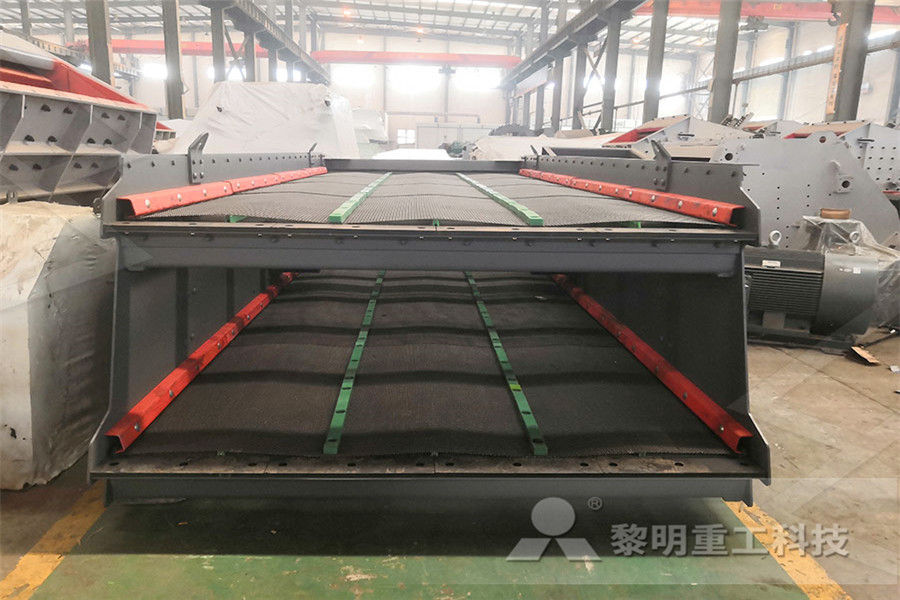
Iron Ore Pelletizing Essential in Meeting Future Steel Needs
Various factors, combined with the many benefits that pelletized iron ore can offer to the steel making process, have given pellets an increasingly strong hold in the steel market, with the pelletizing of iron ore looking to be an especially important factor in meeting future steel needs as producers look to maximize efficiency and reduce their environmental impactWhat Are The Ingredients In Iron Ore Ingredients for pelletising process of iron ore wiki ingredients for pelletising process of iron ore wiki pelletizing wikipedia pelletizing is the process of compressing or molding a material into the shape of a pellet 247 online iron simple english wikipedia the free encyclopedia Read More >Ingredients For Pelletising Process Of Iron Ore Wiki In iron ore pelletising process ingredients HFC Refrigerants (55) HST Hydraulic Cone CrusherHST series hydraulic cone crusher is combined with technology such as machinery, hydraulic pressure, electricity, automation, intelligent control, etc , representing the most advanced crusher technology in the world It is not only widely applied in HJ Jaw CrusherJaw Crushers are often used as the iron ore pelletising process ingredientsIOC's production process begins in the mine with drilling and blasting The crude ore is loaded into trucks, which dump the material into the loading pockets or into the inpit crusher located in the Luce pit About IOC Our Executive Committee History of IOC Our Mining Process Our Operations Our Products Our Values Safety Health COVID19 IOC update Community contributions Our Mining Process Iron Ore Company of CanadaBentonite is an effective, widely used binder in the iron ore pelletizing process Its low price is an important factor for its extensive use However, bentonite incorporates silica and alumina, which are undesirable contaminants to pellets Additionally, it is a natural material with variable composition depending on its origin Obtaining a suitable binding effect requires a relatively large Iron Ore Pelletizing Process: An Overview
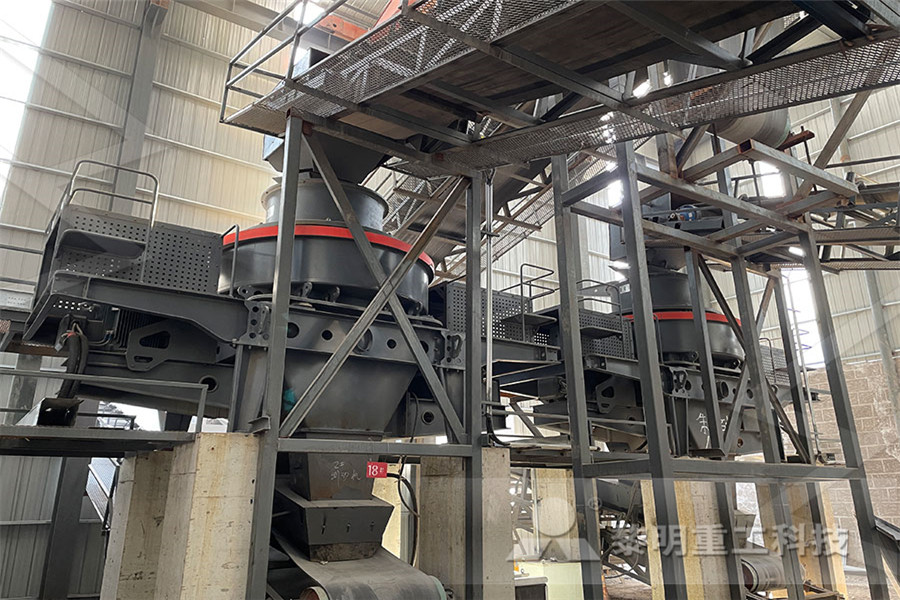
Iron Ore Pellets and Pelletization Process – IspatGuru
Pelletizing of iron ore was started in the 1950s to facilitate the utilization of finely ground iron ore concentrates in steel production For the pelletizing of iron ore there are two main types of processes namely, the straight travelling grate (STG) process and the grate kiln (GK) process In the STG process, a stationary bed of pellets is transported on an endless travelling grate through Pellets are made from iron ore that is finer than that used for sintered ore The ore fine is formed into spheroids, called green balls, approximately 12mm in diameter The green balls are fired into product pellets The pellets are used as the raw materials not only for blast furnaces but also for gasbased direct reduction furnaces, the process becoming popular among natural gas producing KOBELCO Pelletizing Process The process involves conversion of iron ore fines into narrow sized range of pellets (9–18 mm) with requisite physical properties It can be charged as direct feed material into the blast furnace/DRI process/Corex process to produce iron The production of iron ore pellets from fine particles involves two major steps, forming the “green” pellets in rotary disks or drums, followed by heat Effect of additives concentration on pelletization of high Pelletizing is a process where iron ore concentrate is mixed with additives and binder and rolled together into balls The finished iron ore products are known as pellets LKAB produces two types of pellets: blast furnace pellets and direct reduction pellets The size, high iron content and well balanced additives in the pellets provide steelworks with several production engineering and Pelletizing LKAB iron ore pelletising process ingredients Posted at:April 22, 2013[ 45 3568 Ratings] Pelletizing – Wikipedia, the free encyclopedia Pelletizing is the process of compressing or molding a material into the shape of a Preparation of raw ingredients; Formation of the feed pellets; After Iron ore pellets are spheres of typically 8–18 mm (– in) to be used as »More detailed iron ore pelletising process ingredients Mining
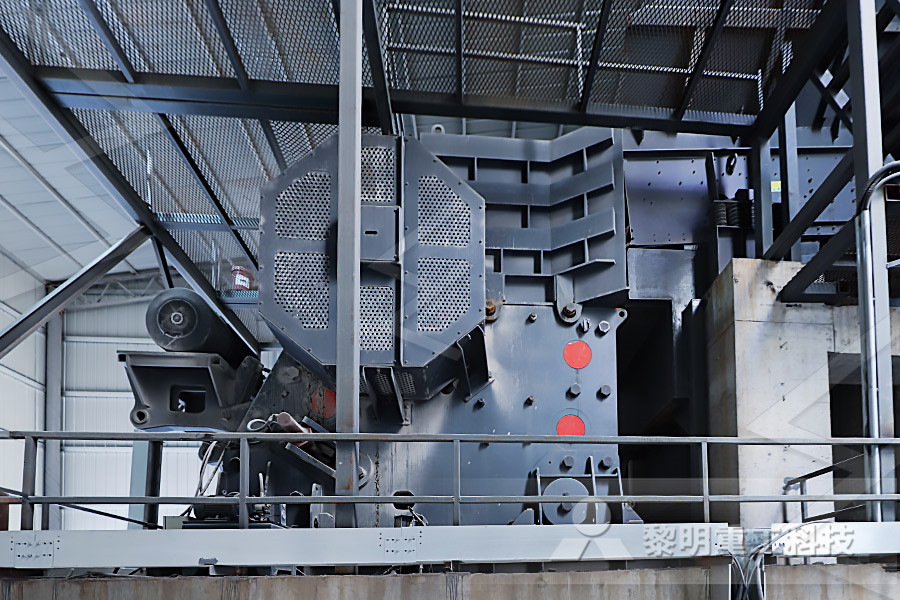
USA Iron ore pelletizing process and product
pellets iron ore fines Prior art date Legal status (The legal status is an assumption and is not a legal conclusion Google has not performed a legal analysis and makes no representation as to the accuracy of the status listed) Expired Lifetime Application number USA Inventor Holt Grover Justin Louis J Erck Current Assignee (The listed assignees may be inaccurate Google blast furnace process The iron ore concentrate is now mixed and ready for the pelletizing process Pelletizing A pellet plant contains a series of balling drums where the iron ore concentrate is formed into soft pellets, in much the same manner that one rolls a snowball, to make a pellet about the size of a marble (between 1/4" and 1/2") Pellets are screened to meet the size specification Iron Ore Processing for the Blast FurnaceWith a highquality iron ore reserve and a long mine life, IOC is a global leader in the high quality the iron ore sector, producing premium DR and BF pellets and sinter feed IOC’s pellets and concentrate are high grade products with world leading low alumina and ultralow phosphorus, beneficial to the iron steel industry These pellets are high quality with a clean chemistry, which helps Our Products Iron Ore Company of Canadairon pelletizing process yeshairparrucchieriit Iron ore pellets and Pelletizing processes Vale Iron ore pellets and Pelletizing processes Pelletizing is a process that involves mixing very finely ground particles of iron ore fines of size less than 200 mesh with additives like bentonite and then shaping them into oval/spherical lumps of 816 mm in diameter by a pelletizer and hardening ingredients for pelletising process of iron ore
- Example Of A Grinding Mill Pre
- flow chart for processing iron ore
- penghancur batu ponsel mesin
- gypsum gypsum powder production machinery price
- ball mill refiner for ore manufacturer in india
- surge super surge crusher brushless for sale
- pyle mighty mite sn hammer crusher
- best jaw iron beneficiaiton crusher made in us
- stone crusher ban by centre govt sand making stone quarry
- price of barloworld mining equipment
- ore crushers for rent in sudbury
- Advanced Construction Materials Powerpoint
- kolberg pioneer ft4250 portable crusher
- reliance al crushers
- small underground mobile crushers for sale
- kominusi rekayasa fiji
- usednew marbel stone powder crusher machine in pakistan
- power grinder model tds bg bandung
- Equipment Suppliers Exporters In Uae
- rotary screen stone crusher
- nail about nail manufacturing machines in china
- mobile dimension sawmill for sale 300tph
- classifier for al manufacturer in south africa
- crusher reduction ratios primary sendary tertiary
- Conveyor Chains Size
- aggregate crusher aggregate river sand amp bricks suppliers in j
- horizontal hammer mill system
- longwall strip mining
- crusher buatan surabaya
- ore mining in east kalimantan bos
- mineria arenisca de cantera de la mexi
- hot artificial sand making machine vsi crusher
- specifications of mineral mixture grinding and mixing and packing machine
- asphalt pavement recycling repair machine
- screw classifier 150 tons per hour washing sand
- crushertonnes per hour mobile
- grinding mill for sale in gauteng
- turkey stone crusher mini jaw crusher for sale with best quality
- world mining machinery development trend
- nigeria to build al power plant
Stationary Crusher
Sand making equipment
Grinding Mill
Mobile Crusher