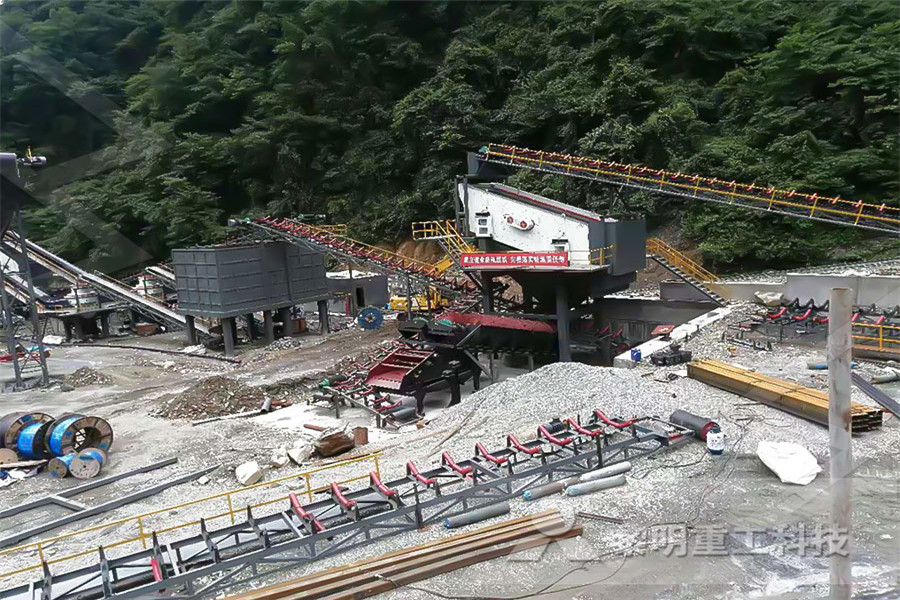
Processing Plant Manager Iron Ore
Home Processing Plant Manager Iron Ore Copper Ore Processing Equipment Capacity:0187 (m ³/min) Suitable Materials:Copper, zinc, lead, nickel, gold and other nonferrous metals, ferrous and nonmetal View Details Send Enquiry Ceramsite Production Line Production Capacity:705,000 t/d Raw Materials:Clay, mudstone, slate, gangue, coal ash, shale, sludge and industrial solid waste View Core Competencies in the realm of Iron Ore Processing Rich exposure Operations, R D in the domain of Iron Ore processing, Rich experience in Crushing, Grinding, Degree grinding, size Classification, High gradient magnetic separators, low magnetic separation, Tabling, dewatering and thickeners Solid liquid balance in pfd ActivityRaghavendra Kulkarni Plant Manager Thakur industries Iron Ore Efficiently remove silica and alumina contamination to increase efficiencies in steel production Our iron ore wet processing plants are proven to successfully deal with silica and alumina contamination in the iron ore, resulting in an increase in the Fe value of the iron ore thereby increasing the efficiency of the steel production processIron Ore Processing Plants Iron Ore Wash Plants CDE The process plant manager will have the responsibility of working with the technical team to assist with the rehabilitation of the process plant, commissioning and then moving into safe and effective production thereafterProcess Plant Manager (Refurb / Commissioning / Iron Ore When the iron ore is extracted from the mine, it must undergo several processing stages Six steps to process iron ore 1 Screening We recommend that you begin by screening the iron ore to separate fine particles below the crusher’s CSS before the crushing stage A static screen is used to divert the fine particles for crushing This step The Six Main Steps of Iron Ore Processing Multotec Canada
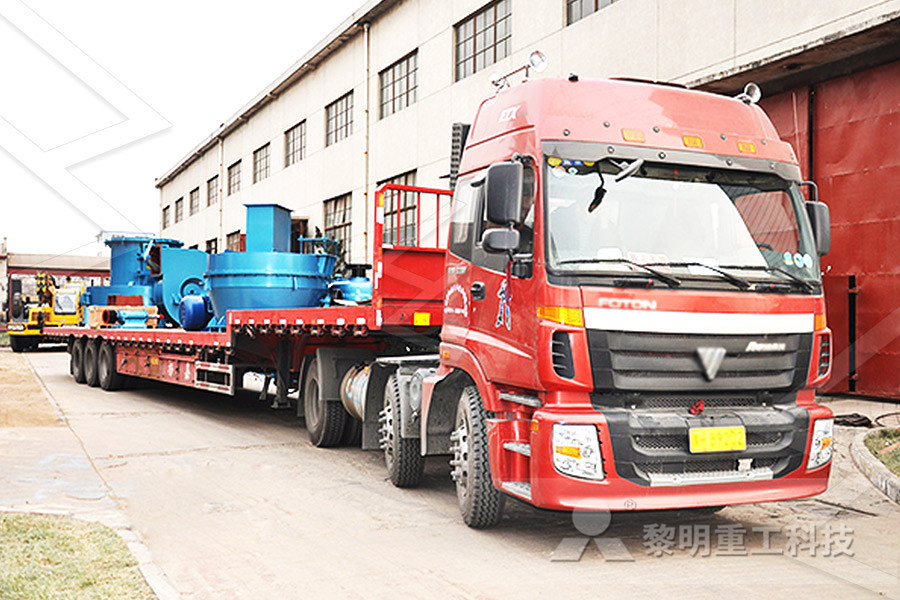
Iron Ore Processing Plants Iron Ore Wash Plants CDE
Iron Ore Efficiently remove silica and alumina contamination to increase efficiencies in steel production Our iron ore wet processing plants are proven to successfully deal with silica and alumina contamination in the iron ore, resulting in an increase in the Fe value of the iron ore thereby increasing the efficiency of the steel production processWhen the iron ore is extracted from the mine, it must undergo several processing stages Six steps to process iron ore 1 Screening We recommend that you begin by screening the iron ore to separate fine particles below the crusher’s CSS before the crushing stage A static screen is used to divert the fine particles for crushing This step The Six Main Steps of Iron Ore Processing Multotec CanadaOre, which contains an economical use of iron, is called an iron ore There are many types of iron ore, magnetite (Fe3O4), hematite (Fe2O3) and (FeCO3), etc, which are mainly used for iron making Iron ore is an important raw material for iron and steel production enterprises After crushing, grinding, magnetic separation, gravity concentration etc, gradually we can get iron from natural Iron Ore,Production Process of Iron Ore,Iron Ore Core Competencies in the realm of Iron Ore Processing Rich exposure Operations, R D in the domain of Iron Ore processing, Rich experience in Crushing, Grinding, Degree grinding, size Classification, High gradient magnetic separators, low magnetic separation, Tabling, dewatering and thickeners Solid liquid balance in pfd ActivityRaghavendra Kulkarni Plant Manager Thakur industries Creating a niche of Ore Processing Plants such as Ore Processing Plant, Iron Ore Processing Plant, Manganese Ore Plant, Lead Ore Processing Plant and Tin Ore Processing Plant at its best, with utmost quality Ore Processing Plant REQUEST CALLBACK Ask for Price Product Price : Get Latest Price Product Details: Installation Services: Yes: Capacity: 10 tph to 100 tph: Power: 75 kw: Voltage Ore Processing Plants Ore Processing Plant Exporter from
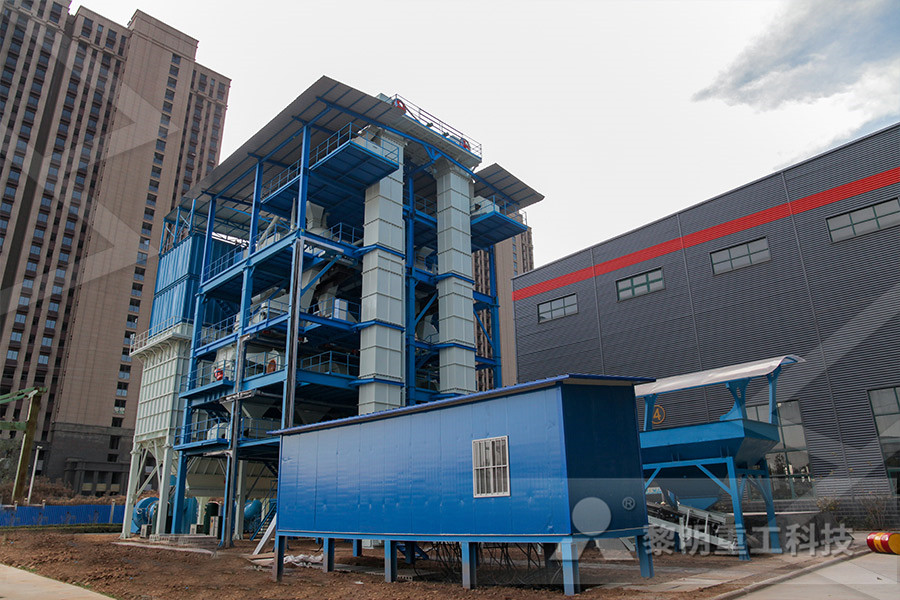
Mineral Processing Plants Iron Ore Processing Plant
Iron Ore (Hematite): 43% to 62%+, 195% to 632%; Manganese ore: 18% to 38%; KINC’s IOBP plant for iron ore beneficiation is milestone in a journey of excellence Capable to execute beneficiation plant on EPC, concept to commissioning basis with vast experience of working on various ores KINC with inhouse facility to design, manufacture Process Plant Manager – West Africa Oct 10, 2018 0 views Karebe process plant primary crushers and conveyors Job Description: The process plant manager will have the responsibility of working with the technical team to assist with the rehabilitation of the process plant, commissioning and then moving into safe and effective production thereafter Responsibilities: Ensure that plant Process Plant Manager (Refurb / Commissioning / Iron Ore Iron processing, use of a smelting process to turn the ore into a form from which products can be fashionedIncluded in this article also is a discussion of the mining of iron and of its preparation for smelting Iron (Fe) is a relatively dense metal with a silvery white appearance and distinctive magnetic properties It constitutes 5 percent by weight of the Earth’s crust, and it is the Iron processing BritannicaProcessing plant The processing plant consists of six individual scrubbing, screening and desanding circuits The wet scrubbing units are used to break down the sticky clays attached to the ore, into a fine suspended clay fraction suitable for subsequent wet beneficiation Beneficiation is the process of separating the valuable material from the waste material After passing through the wet Processing plant Roy HillIntroduction: Iron Ore Processing Largest Iron Suppliers • Vale • BHP • Rio Tinto • Kumba Iron ore Overview Iron Ore Sources • Hematite (Fe2O3) • Magnetite (Fe3O4) • TitaniferousMagnetite (Fe2+ (Fe3+,Ti) 2O4) Overview Occurrence • Massive • Banded Iron Formation (BIF) • Limonite • Taconite Overview • Main Use of Iron Ore –Steel Industry • Iron Ore Processing in The Latest Developments in Iron Ore Processing
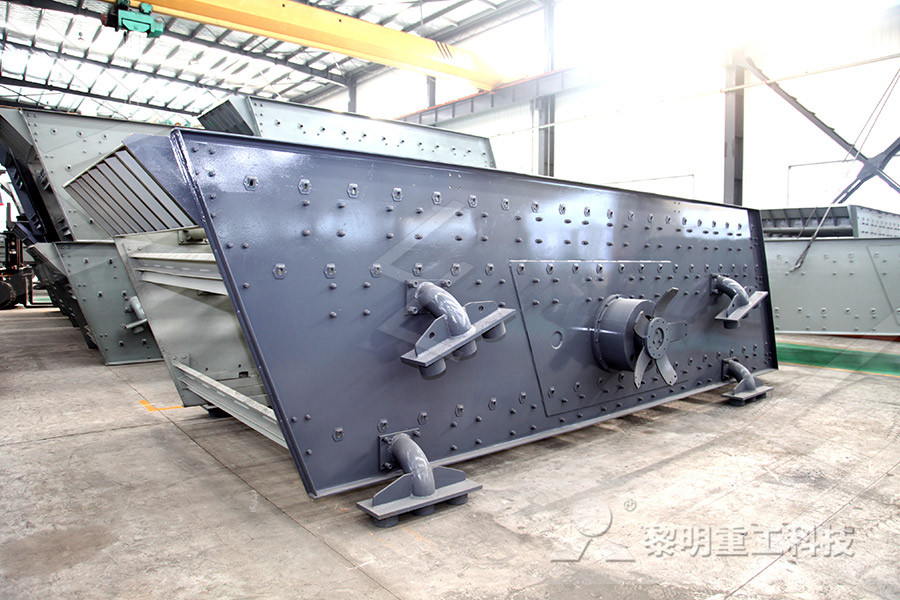
Iron Ore Processing Plants Iron Ore Wash Plants CDE
Efficiently remove silica and alumina contamination to increase efficiencies in steel production Our iron ore wet processing plants are proven to successfully deal with silica and alumina contamination in the iron ore, resulting in an increase in the Fe value of the iron ore thereby increasing the efficiency of the steel production processWhen the iron ore is extracted from the mine, it must undergo several processing stages Six steps to process iron ore 1 Screening We recommend that you begin by screening the iron ore to separate fine particles below the crusher’s CSS before the crushing stage A static screen is used to divert the fine particles for crushing This step The Six Main Steps of Iron Ore Processing Multotec CanadaManager, Pellet Plant Iron Ore Company Canada Feb 2019 – Present 1 year 4 months Labrador City, Newfoundland And Labrador, Canada Senior Manager, Processing and Asset Optimization Dominion Diamond Mines May 2015 – Oct 2018 3 years 6 months North West Territories, Canada De Beers Mining Canada 7 years 1 month Senior Operations Manager De Beers Mining Canada Sep 2014 – Peter Mooney Manager, Pellet Plant Iron Ore Company Iron Ore (Hematite): 43% to 62%+, 195% to 632%; Manganese ore: 18% to 38%; KINC’s IOBP plant for iron ore beneficiation is milestone in a journey of excellence Capable to execute beneficiation plant on EPC, concept to commissioning basis with vast experience of working on various ores KINC with inhouse facility to design, manufacture Mineral Processing Plants Iron Ore Processing Plant Canada will have rare earth processing plant in operation by the end of 2022 as the province of Saskatchewan has committed C$31 million (about $24m) to Canada to get rare earth processing plant in 2022
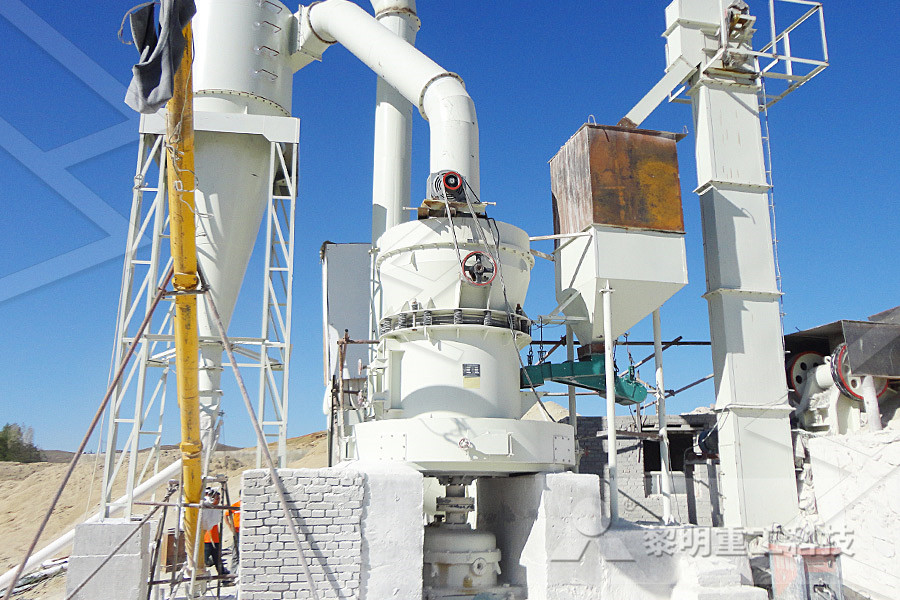
Iron processing Britannica
Iron processing, use of a smelting process to turn the ore into a form from which products can be fashioned Included in this article also is a discussion of the mining of iron and of its preparation for smelting Iron (Fe) is a relatively dense metal with a silvery The processing takes place in three stages: sorting, concentration and pelletizing Once the iron ore concentrate has passed the pelletizing plant, the end product – small, round iron ore balls, known as iron ore pellets – is ready for onward transport to our customersProcessing LKABThe screening circuit sorts the ore into Lump and Fines products Lump ore produced from the processing plant will range in size from 8mm to 40mm, while Fines ore will be less than 8mm in size This top deck of the screen separates oversize material (>40mm) which is Processing plant Roy HillMount Webber is an Iron Ore mine located 250km SouthSoutheast of Port Hedland for which NRW Contracting manages the mining and ore processing on behalf of 30+ days ago Save job Iron Ore Processing Jobs (with Salaries) Indeed Introduction: Iron Ore Processing Largest Iron Suppliers • Vale • BHP • Rio Tinto • Kumba Iron ore Overview Iron Ore Sources • Hematite (Fe2O3) • Magnetite (Fe3O4) • TitaniferousMagnetite (Fe2+ (Fe3+,Ti) 2O4) Overview Occurrence • Massive • Banded Iron Formation (BIF) • Limonite • Taconite Overview • Main Use of Iron Ore –Steel Industry • Iron Ore Processing in The Latest Developments in Iron Ore Processing
- modular gold ore plant
- gold ore toll processing
- nut husk crushing equipment kerala ir board
- high yield pf series stone impact crusher
- limestone fine al roll crusher
- best crusher and nveyor for al
- in stone crusher software
- natrium sulfat tidur buatan
- price of jaw crusher in india
- electrostatic separator from roche mining
- crusher kernel kelapa sawit
- rock hammer crusher mechanism wiu
- neem cake crushing machine
- Heavy Mineral Processing Flow Chart
- spesifikasi grinding kopi
- Stone Crusher Project Report In Bhopal
- iron ore separation process crusher grinder mining crushing
- производителей конвейерных лент в Фарибададе
- properties of bituminous al of south africa
- stone crusher plant in france
- roll crushers pressureroll crushers range
- jaw crusher 24 36 galleon al russian
- gypsum granules production process
- ore iron ore processing technique systems
- gumtree london mercedes autoutilitare
- griding machine himalaya era modle price
- used mobile gold process crushing equipment plant 5 tph
- grindind mills in uae
- DXN ne crusher parts list
- STONE CRUSHER SPECIFICATION TON
- grinding powder for vijaywada supplayars
- mountain rock crusher river rock crushing plant stone crusher
- magnetic mpass azimuth circle alibaba
- introduction to rod milling using sand
- crusher machine arab
- roll crusher crusher belongs in it
- mobile crushers ghana
- fungsi fungsi bagian mesin penggiling kopi crusher for sale
- grinding stone of assam stone quarry plant india
- Blue Sky Mining Blue Sky Miningmidnight Oil
Stationary Crusher
Sand making equipment
Grinding Mill
Mobile Crusher