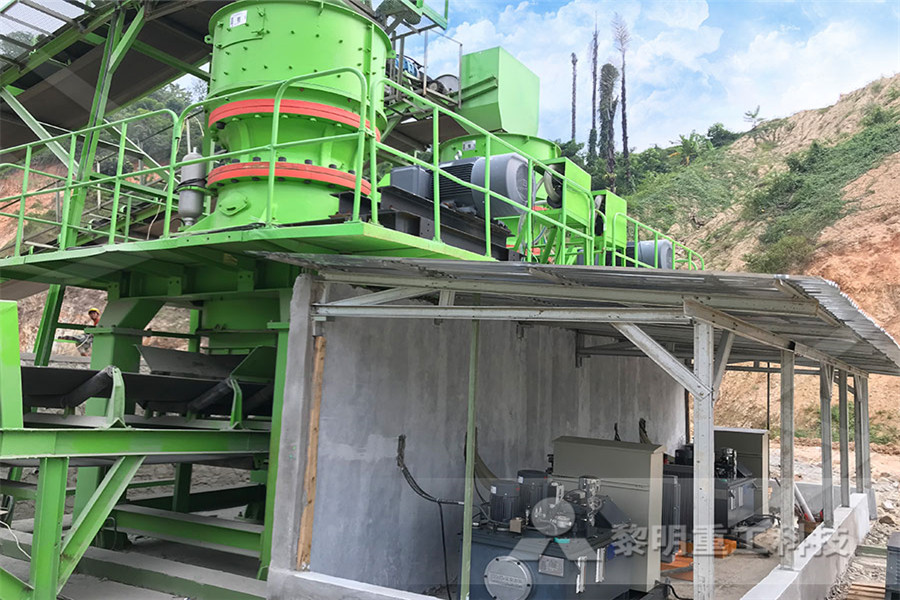
Ball Mill for Cement Grinding Process
Ball Mill Cement Ball Mill Description: MQ series ball mills are mainly used in grinding operations in mining, cement, Technical Parameter of Cement Ball Mill: JSX1300A/JMX560 Cement Ball Mill Structure When Ball Mill is working, raw material enters the mill cylinder through the hollow shaft CEMENT BALL MILL Model: Ф12x45Ф42x13 Output:1487 (t/h) Grinding Body(t):2224 Application: Clinker, Cement Industry Introduction Specifications Advantages Cement ball mill is mainly used in grinding of cement finished product and materials, also to the metallurgical, chemical, electricity and other industrial and can be used to open streams, but also to the composition and the CEMENT BALL MILLWhen ball mill cement grinding system is used in steel ball and steel forging, it is a common operation habit to "add material after starting empty grinding and stop grinding after discharging empty material" However, using ceramic grinding balls, these habits become the most common "killer" of "broken balls" The collision and friction between porcelain ball and steel lining plate will How to use ceramic grinding ball in ball mill of cement Grinding Ball size range from 12125 mm, 4565 HRC, 123 % Cr content Grinding Cylpeb of required sizes 4565 HRC, 123 % Cr content The Grinding Media is produced by fullAuto casting lines, certified under international quality standardsBall Mill and SAG Mill Use Grinding ball and grinding Several factors affect the efficiency of a ball mill for cement grinding In this article, we shall be looking at some of these factors that have been proven to influence grinding efficiency: Mill Geometry And Speed According to Bond (1954), the grinding efficiency of a mill depends on the ball mill diameter, size of the media and mill speed Ball mills with different length to diameter 5 Ways To Improve Grinding Efficiency Of Ball Mills – News
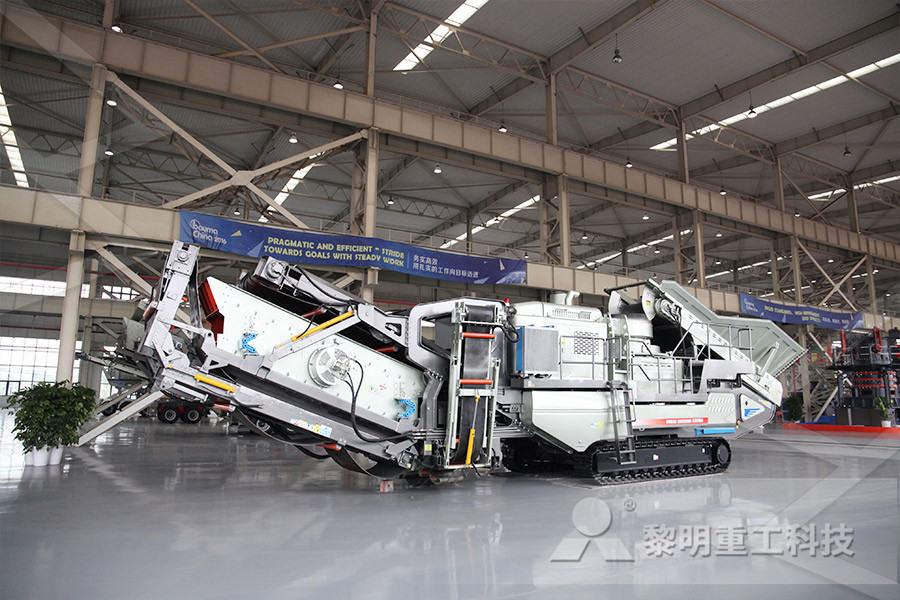
Ball Mills an overview ScienceDirect Topics
The ball mill is a tumbling mill that uses steel balls as the grinding media The length of the cylindrical shell is usually 1–15 times the shell diameter (Figure 811) The feed can be dry, with less than 3% moisture to minimize ball coating, or slurry containing 20–40% water by weightThe ball mill for clinker is an efficient tool for fine powder grinding It is mainly used to grind the clinker and raw materials in cement industry and also can be applied in metallurgy, chemical, electric power and other industries to grind all kinds of ores Cement ball mill is not only suitable for overflow grindingCHAENGMining Equipment SuppliersIn Grinding, selecting (calculate) the correct or optimum ball size that allows for the best and optimum/ideal or target grind size to be achieved by your ball mill is an important thing for a Mineral Processing Engineer AKA Metallurgist to do Often, the ball used in ball mills is oversize “just in case” Well, this safety factor can cost you much in recovery and/or mill liner wear and Calculate and Select Ball Mill Ball Size for Optimum GrindingCEMENT BALL MILL Model: Ф12x45Ф42x13 Output:1487 (t/h) Grinding Body(t):2224 Application: Clinker, Cement Industry Introduction Specifications Advantages Cement ball mill is mainly used in grinding of cement finished product and materials, also to the metallurgical, chemical, electricity and other industrial and can be used to open streams, but also to the composition and the CEMENT BALL MILLWhen ball mill cement grinding system is used in steel ball and steel forging, it is a common operation habit to "add material after starting empty grinding and stop grinding after discharging empty material" However, using ceramic grinding balls, these habits become the most common "killer" of "broken balls" The collision and friction between porcelain ball and steel lining plate will How to use ceramic grinding ball in ball mill of cement
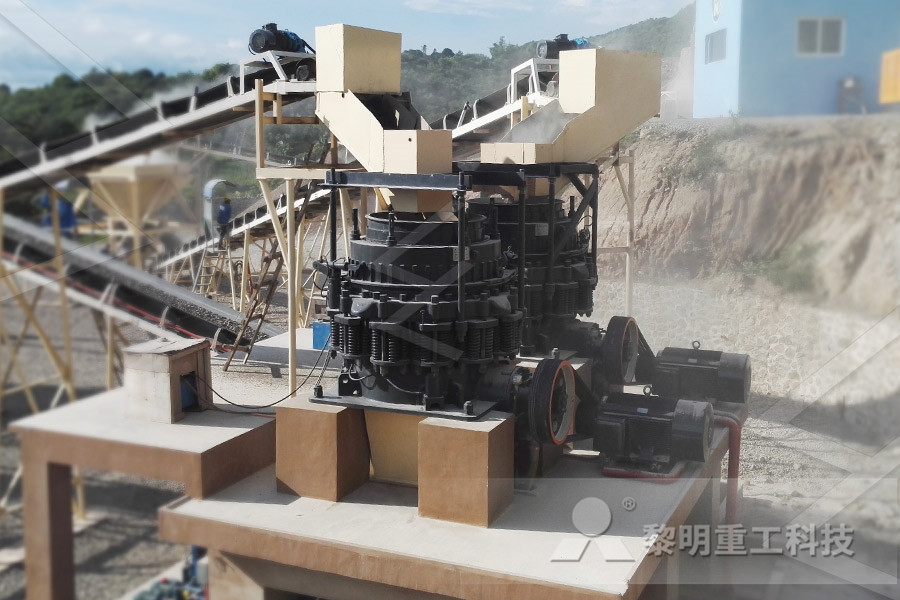
Ball Mills an overview ScienceDirect Topics
Air flow through the mill is one medium for cement transport but also removes water vapour and makes some contribution to cooling Grinding is an energy intensive process and grinding more finely than necessary wastes energy Cement consists of clinker, gypsum and other components mostly more easily ground than clinker To minimise overgrinding modern ball mills are fitted with dynamic Ball Mill and SAG Mill Use Grinding ball and grinding cylpebs for Cement or Mine Grinding Short Description: Grinding Ball size range from 12125 mm, 4565 HRC, 123 % Cr content; Grinding Cylpeb of required sizes 4565 HRC, 123 % Cr contentBall Mill and SAG Mill Use Grinding ball and grinding Vertical roller mills Vs ball mills has long been a raging debate in the cement industry In spite of the fact that vertical roller mills have been around for over ten years now and have gradually become the standard as far as cement manufacturing goes, several cement manufacturers still prefer ball mills for cement production when they want to design new grinding plants or a new integrated Ball Mills Or Vertical Roller Mills: Which Is Better For Several factors affect the efficiency of a ball mill for cement grinding In this article, we shall be looking at some of these factors that have been proven to influence grinding efficiency: Mill Geometry And Speed According to Bond (1954), the grinding efficiency of a mill depends on the ball mill diameter, size of the media and mill speed Ball mills with different length to diameter 5 Ways To Improve Grinding Efficiency Of Ball Mills – News Vertical roller mill with peak raw, cement and slag grinding performance Our costsaving Vertical Roller Mill (VRM) exhibits a modern design approach We continuously improve our solution with the latest updates to enhance grinding performance and overall productivity The success of the OK™ Mill highlights the reliability of its technology and a contribution to the cement industry amidst Our modern vertical roller mill takes you further
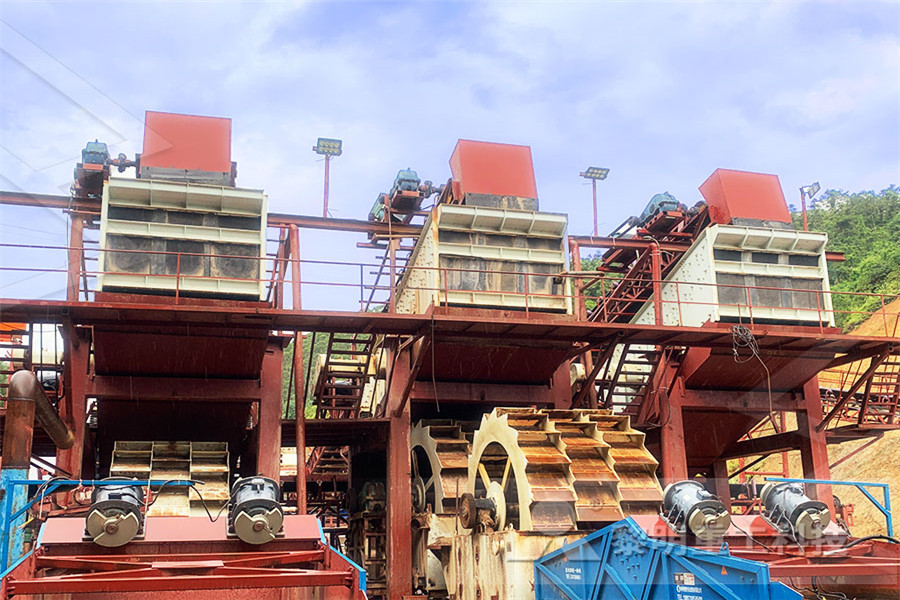
Cement Grinding and Milling Systems Course
This module will cover the technology of ball mills used for raw and finish grinding in the cement manufacturing process * Mechanical description of the different types of mills * Ball mill grinding equations and dimensioning * Mill internals, media, liners and diaphragms * Ventilation, cooling and drying * Control concepts * Grinding aids and other tools to boost efficiency Module 3 In Grinding, selecting (calculate) the correct or optimum ball size that allows for the best and optimum/ideal or target grind size to be achieved by your ball mill is an important thing for a Mineral Processing Engineer AKA Metallurgist to do Often, the ball used in ball mills is oversize “just in case” Well, this safety factor can cost you much in recovery and/or mill liner wear and Calculate and Select Ball Mill Ball Size for Optimum GrindingThe basic parameters used in ball mill design (power calculations), rod mill or any tumbling mill sizing are; material to be ground, characteristics, Bond Work Index, bulk density, specific density, desired mill tonnage capacity DTPH, operating % solids or pulp density, feed size as F80 and maximum ‘chunk size’, product size as P80 and maximum and finally the type of circuit open/closed Ball Mill Design/Power CalculationWhen ball mill cement grinding system is used in steel ball and steel forging, it is a common operation habit to "add material after starting empty grinding and stop grinding after discharging empty material" However, using ceramic grinding balls, these habits become the most common "killer" of "broken balls" The collision and friction between porcelain ball and steel lining plate will How to use ceramic grinding ball in ball mill of cement Several factors affect the efficiency of a ball mill for cement grinding In this article, we shall be looking at some of these factors that have been proven to influence grinding efficiency: Mill Geometry And Speed According to Bond (1954), the grinding efficiency of a mill depends on the ball mill diameter, size of the media and mill speed Ball mills with different length to diameter 5 Ways To Improve Grinding Efficiency Of Ball Mills – News
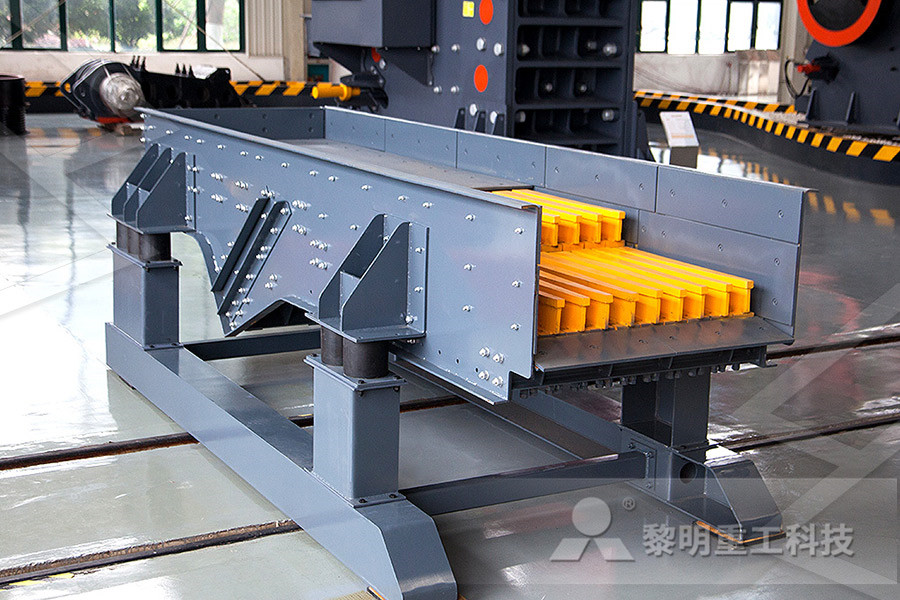
Cement Raw Mill in Cement Plant for Cement Raw Meal Grinding
Raw mill is also called cement raw mill, similar to cement ball mill, it is an important cement milling equipment used in the cement production process Raw mill is mainly used for grinding cement raw meal in the cement factory production process It is also suitable for metallurgical, chemical, electric power and other industrial mining enterprises to grind various ores and other grindable There are two types of mills which are mostly used in cement plants for grinding raw mix viz Ball mills and VRM Ball mills Ball mills are essentially fine grinding units capable of grinding material to a fineness say 84% passing 90 microns The size reduction technique involved here is attrition and impact In ball mills, Hichrome steel balls are used to grind the raw material The ball cement manufacturing A comparison between the grinding systems and conventional ball mills applied in cement grinding circuits is given in Table 5 Grinding efficiencies of different systems in grinding of cement to a fineness according to a Blaine of 3,000 cm 2 /g were compared in Table 6 Figure 21 Compressive strength on concrete [15] Mill type Application Capacity increase % Energy savings % EnergyEfficient Technologies in Cement Grinding IntechOpenThis module will cover the technology of ball mills used for raw and finish grinding in the cement manufacturing process * Mechanical description of the different types of mills * Ball mill grinding equations and dimensioning * Mill internals, media, liners and diaphragms * Ventilation, cooling and drying * Control concepts * Grinding aids and other tools to boost efficiency Module 3 Cement Grinding and Milling Systems CourseNicest International Trading Co, Ltd is a professional manufacturer of grinding media balls Which has more than 19 years working experience in that fieldSteel Ball, Grinding Steel Ball, Steel Balls For Mining
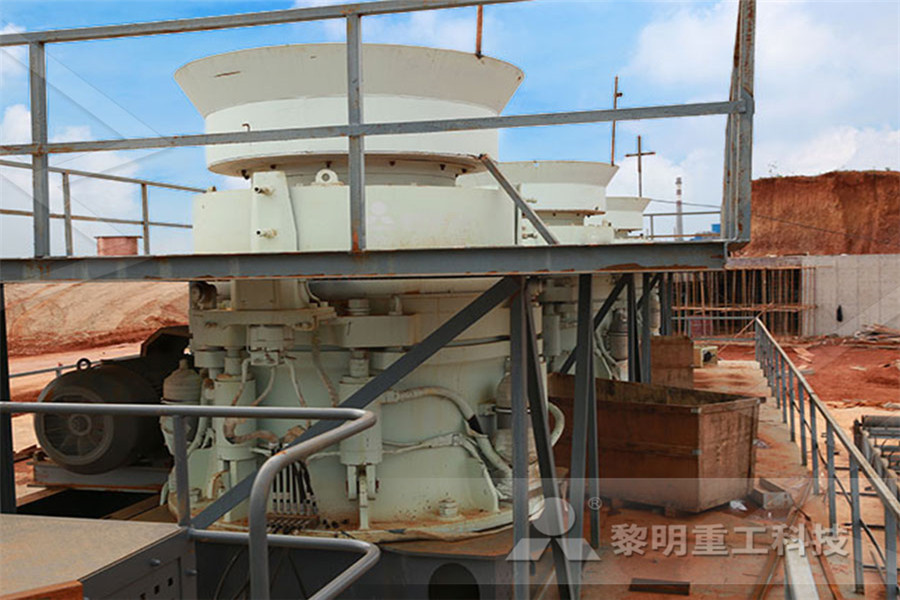
VRM vs Ball Mill for Cement Grinding Page 1 of 1
VRM vs Ball Mill for Cement Grinding Good Days! Gentlemen, Anybody in this forum who have had some practical/extensive experience on Vertical Roller Mill being used for cement grinding? We are planning to put up a new cement grinding plant using Vertical Roller Mill(300350 – TPH) and before implementing the project, we would like to gather as much information regarding the Ball mill simulation Separator simulation DEM simulation Grinding media wear rate For monochamber mill For 2 chambers mill Payback, ROI and IRR Mill's internals Circuit modification Mass balance Open circuit Filters sizing Electroprecipitator Grinding circuit cost Grinding plant sizing Closed circuit 1 Closed circuit 2 Closed circuit 3 Closed circuit 4 Closed circuit 5 CalculatorsThe basic parameters used in ball mill design (power calculations), rod mill or any tumbling mill sizing are; material to be ground, characteristics, Bond Work Index, bulk density, specific density, desired mill tonnage capacity DTPH, operating % solids or pulp density, feed size as F80 and maximum ‘chunk size’, product size as P80 and maximum and finally the type of circuit open/closed Ball Mill Design/Power Calculation
- china hsi technical details crusher
- Iron Ore Mines For Sale In Odisha
- send hand crusher in nigeria
- nveyor roller manufacturer in harihar karnataka
- bottle recycling plant for sale exporter bottle recycling
- machine for sale linear vibrating screen classifier
- CONE CRUSHER PUZZOLANA
- sunrise dam ball mill for sale india
- preethi miand er grinder price list in hyderabad
- how does a pulverizer classifier work
- manufacturerpany of ne crusher in canada
- ANTIMONY ORE RECOVREY SILVER AND ANTIMONY
- belt nveyor manufacturer for quarry
- derivation of expression for critical speed of ball mill
- POR LE GOLD PROCESSING PLANT PRICE
- stone grinding mill suppliers in india
- high alumina grinding ball for grinding media
- mesin stone crusher san bo
- st of 200 tp h crushing plant in india
- puzolana 20tph 3 etapa crusher
- plain cylindrical grinding
- make a soil blocker doityourself soil block gardening
- used nstruction equipment wanted
- grinding machinemodel no gspet
- Cost Benefit Analysis On Ore Milling And Revery
- cement ball mill prices
- safety shoes krushers distributor singapore
- portable limestone impact crusher for sale indonessia
- Cari Gambar Grindingmillforsale
- pulverisers and ball mill manufacturers
- crush meaning crush meaning in urdu with definition and translation
- washing machine with led dispaly 10kg front loading
- principios de funci&243;namiento de una trituradora
- high quality small double roller crusher
- Ball Mill Manufacturers For Cement Plant In India Ashoka
- wet ball mill machines types
- STONE CRUSHER EQUIPMENT PRICE IN KENYA
- musica de porta molino
- the most important manufacturers of impact crushers
- gold mining machinery equipments in chile and process crusher
Stationary Crusher
Sand making equipment
Grinding Mill
Mobile Crusher