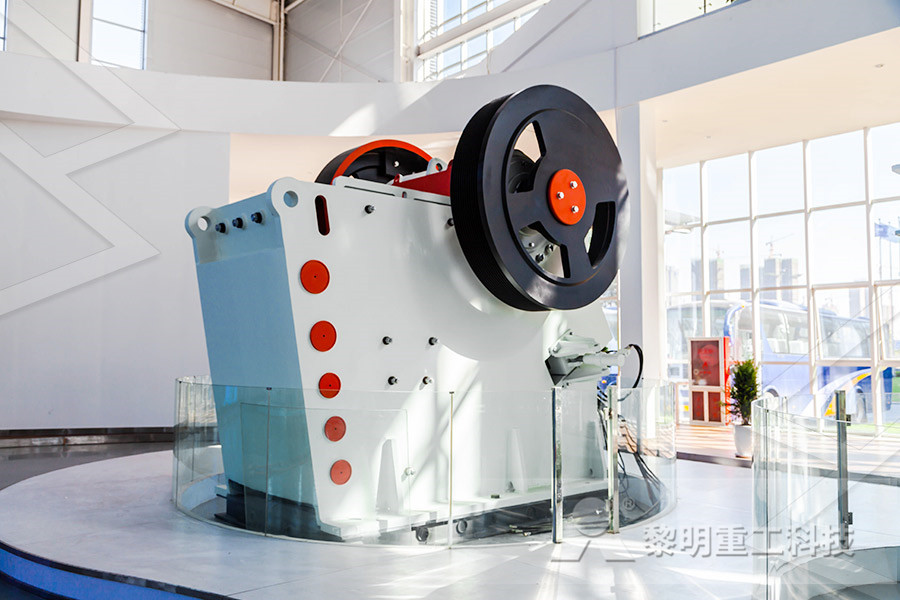
The Six Main Steps of Iron Ore Processing Multotec Canada
Six steps to process iron ore 1 Screening We recommend that you begin by screening the iron ore to separate fine particles below the crusher’s CSS 2 Crushing and stock piling This step involves breaking up the iron ore to obtain an F 80 grind size before it can be 3 Feeding the crusher Iron processing, use of a smelting process to turn the ore into a form from which products can be fashioned Included in this article also is a discussion of the mining of iron and of its preparation for smelting Iron (Fe) is a relatively dense metal with a silvery Iron processing BritannicaProduction Process of Iron Ore Generally, the processing of iron ore needs several processing stages, including crushing, grinding, ore beneficiation, concentrating, drying, etc The equipments for iron ore beneficiation is consisted of Jaw Crusher, Ball Mill , Classifier, Magnetic Separator, Flotation Machine, Concentrator Machine and Dryer And Equipped with Feeder, Elevator and Conveyor, a full Iron Ore,Production Process of Iron Ore,Iron Ore IOC's production process begins in the mine with drilling and blasting The crude ore is loaded into trucks, which dump the material into the loading pockets or into the inpit crusher located in the Luce pitOur Mining Process Iron Ore Company of CanadaOn the way from the mine to a final product, the iron ore goes through the following main process segments: 1) The iron ore is crushed and the waste rock is removed About 85 % of the particles should be less than 44 μm (in 2) Water is added to the magnetite to make magnetite slurry 3) Additive The Iron Pelletizing Process: Part One :: Total Materia
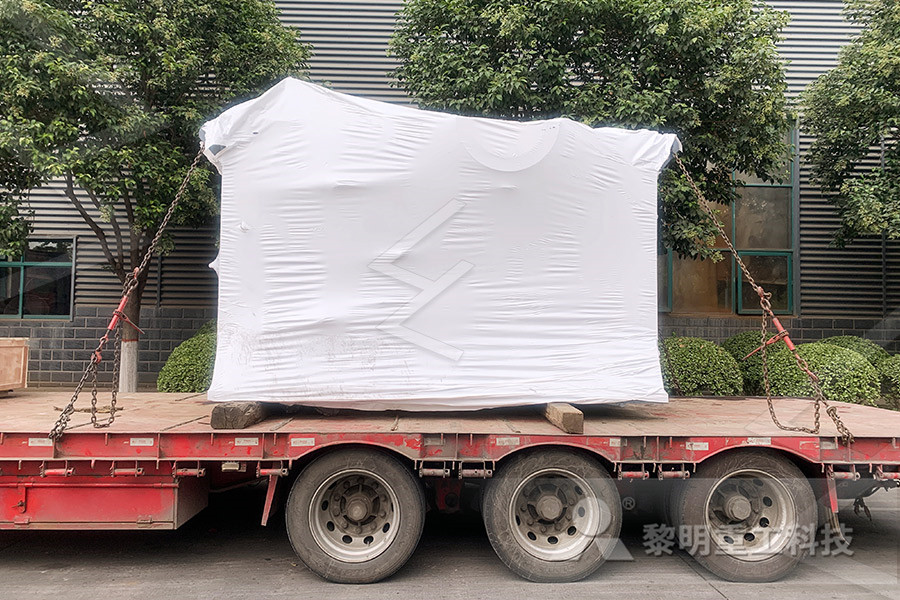
Iron Ore Beneficiation Process
During the last ten years great strides have been made, on the Mesabi range, in the practice of beneficiating low grade iron ore material By beneficiation is meant all methods of removing impurities, and raising the iron content to a point where it can be sold in open market, the principal impurities being silica and moisture The general processes to which low grade iron ores are amenable The crushing, grinding and screening system for the beneficiation of the iron ore is to be designed taking into account the requirements of the downstream beneficiation processes The crushing units may include primary, secondary, tertiary and quaternary crushing units Jaw, gyratory, cone, and roll crushers are used for ore crushingLow grade Iron Ore Beneficiation and the Process of The iron ore is separated from the taconite using magnetism The remaining rock is waste material and is dumped into tailings basins The taconite powder with the iron in it is called concentrate Pellets The concentrate (the wet taconite powder) is rolled with clay inside large rotating cylinders The cylinders cause the powder to roll into marblesized balls (This is like rolling wet, sticky snow into balls to make Iron Mining Process Minnesota Iron Once the iron ore transportation process has become clear to you and you’re ready to ship, look to do so with the trusted 3PL company R+L Global Logistics We can easily, efficiently and quickly ship your unprocessed ore to the steel mills to have them turned into a strong, durable product With our 995 percent ontime rate and industryleading customer service, R+L Global Logistics is well The Iron Ore Transportation Process USA Truckload Shipping The sintering process is the process of treatment of the fine particles of iron ore obtained from crushing process or in cleaning furnace to collect them in a larger size to be similar and homogeneous particles fit for reduction process Purification concentration process is the process of using surface tension properly, magnetic or electrical separation to remove the unwanted impurities Extraction of Iron from its ores, Iron dressing, Reduction
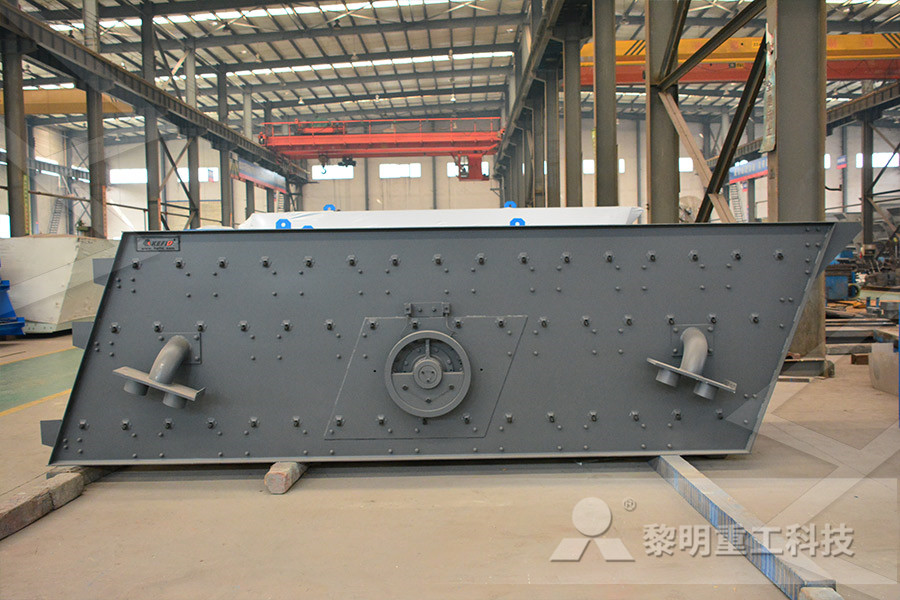
Iron processing Ores Britannica
Iron processing Iron processing Ores: Iron ores occur in igneous, metamorphic (transformed), or sedimentary rocks in a variety of geologic environments Most are sedimentary, but many have been changed by weathering, and so their precise origin is difficult to determine The most widely distributed ironbearing minerals are oxides, and iron ores consist mainly of hematite (Fe2O3), which is The ore is loaded into a blast furnace along with measured quantities of coke and limestone Hot combustion air is supplied to the furnace and some form of fuel used to raise the temperature The iron is reduced from the ore by carbon in the coke, the limestone aiding slag separation from the molten iron The slag and molten iron are tapped off from the bottom of the furnace, the slag being Iron Ore Smelting Process Bright Hub EngineeringIron ore is converted into various types of iron through several processes The most common process is the use of a blast furnace to produce pig iron which is about 9294% iron and 35% carbon with smaller amounts of other elements Pig iron has only limited uses, and most of this iron goes on to a steel mill where it is converted into various steel alloys by further reducing the carbon How iron is made material, manufacture, making, history Low grade Iron Ore Beneficiation and the Process of Jigging Iron ore resources are getting consumed at an accelerated rate because of the growth in the production of iron and steel Due to this reason the availability of high grade iron ore is reducing and the supply of high grade iron ore to iron and steel plants is declining sharply Hence, the scenario is steadily shifting towards the use Low grade Iron Ore Beneficiation and the Process of Process Direct reduction processes can be divided roughly into two categories: gasbased, and coalbased In both cases, the objective of the process is to drive off the oxygen contained in various forms of iron ore (sized ore, concentrates, pellets, mill scale, furnace dust, etc), in order to convert the ore to metallic iron, without melting it (below 1,200 °C (2,190 °F))Direct reduced iron Wikipedia
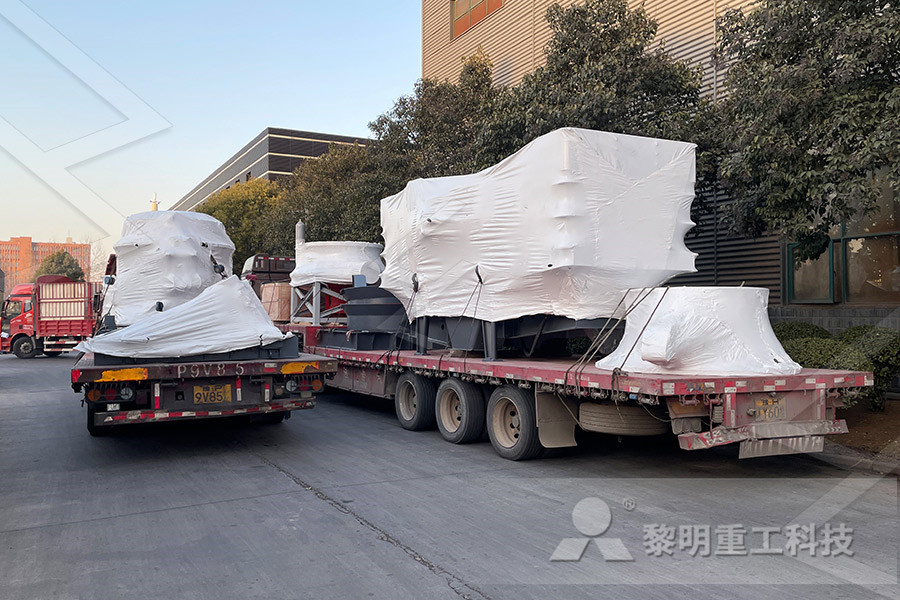
Iron Ore Pelletizing Process: An Overview IntechOpen
The iron ore pelletizing process consists of three main steps: Pelletizing feed preparation and mixing: the raw material (iron ore concentrate, additives—anthracite, dolomite—and binders are prepared in terms of particle size and chemical specifications, dosed, and mixed together to feed the pelletizing process; Balling process: the green pellet is the rolled pellet without any thermal The process of mining low grade iron ore, or taconite, requires massive resources Heavy industrial mining equipment, expansive mines, and a skilled labor pool are all required The equipment used includes diamond bit rotary drills, hydraulic shovels and loaders, water wagons, production trucks and heavyduty conveyors National Steel Pellet Company’s plant is capable of producing 535 Iron Ore Processing for the Blast FurnaceDuring the last ten years great strides have been made, on the Mesabi range, in the practice of beneficiating low grade iron ore material By beneficiation is meant all methods of removing impurities, and raising the iron content to a point where it can be sold in open market, the principal impurities being silica and moisture The general processes to which low grade iron ores are amenable Iron Ore Beneficiation Process Iron ores with lower iron content such as taconite are first processed to concentrate the iron level and drive off volatile impurities The iron ore is dressed or crushed into 051 in chunks, which increases surface area for reactions Magnetic separation is used to remove some of the undesirable minerals or gangue in the crushed ore Roasting or calcination of the ore oxidizes some of the Ironmaking 101 – From Ore to Iron with Blast Furnaces Iron ore is utilized in the p roduction of steel the process of steelmaking involves the removal of impurities from raw iron and the addition of alloying components to produce the desired The Process of Making and Refining Steel from Raw Iron
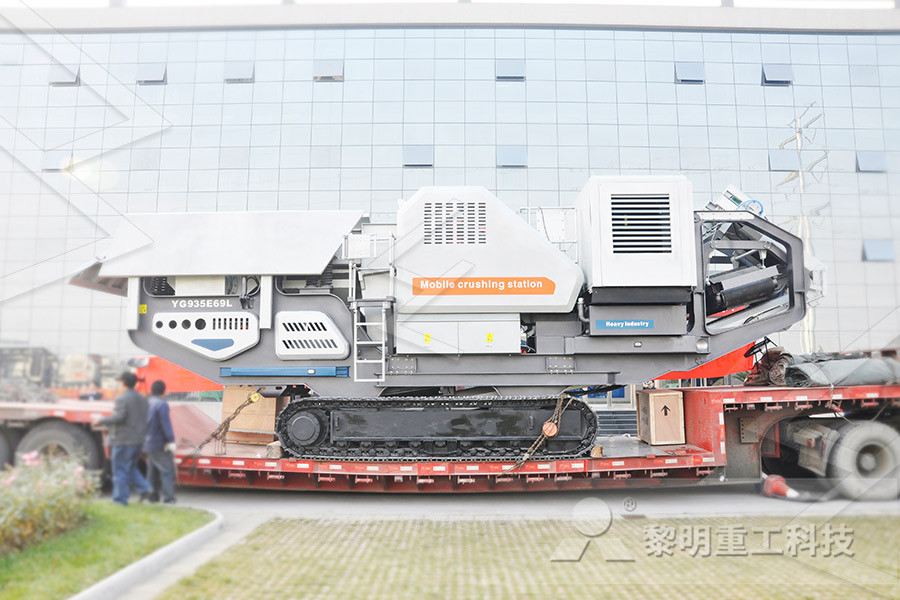
Extraction of Iron, Iron Extraction Process, Iron Ore
Strong magnetic iron ore belongs to freemilling mine, which can get highgrade iron concentrate with weak magnetic separation process With the improving demand of iron ore concentrate, Xinhai has speeded up the research and innovation of magnetic iron ore dressing technology and magnetic separation equipment in recent years, and achieved remarkable resultsIron ore is converted into various types of iron through several processes The most common process is the use of a blast furnace to produce pig iron which is about 9294% iron and 35% carbon with smaller amounts of other elements Pig iron has only limited uses, and most of this iron goes on to a steel mill where it is converted into various steel alloys by further reducing the carbon How iron is made material, manufacture, making, history Modeling Sintering Process of Iron Ore Jose Adilson de Castro Graduate Program on Metallurgical Engineering Federal Fluminense University Brazil 1 Introduction In this chapter, a methodology for simulating th e sintering process of iron ore is presented In order to study the process parameters and inner phenomena, a mathematical model based on transport equations of momentum en ergy and Modeling Sintering Process of Iron OreThis means that the mined iron ores need to be specially processed in advance before the blast furnace process Regions in which iron ore has formed over millions of years (eg through volcanism) and can be mined economically are also referred to as iron ore deposits Especially many ore deposits can be found in countries such as China, Australia, Brazil, India and Russia These countries Iron ore mining and dressing tecscienceIron ore tailings mines decomposition products can be widely used in the drilling mud treated process as the natural brown material, and iron ore mines can neutralizing hydrogen sulfide This passage will have a brief introduction of iron ore mining process Iron ore mines as the main iron source have been widely used in England and Europe Get mining process for iron AuraThaiHealthSpaRa
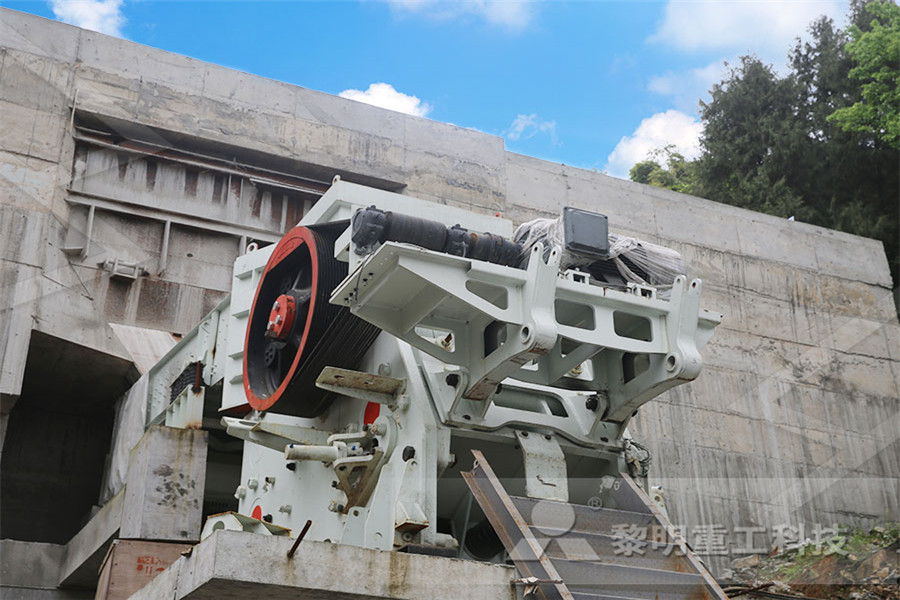
Iron Ore Processing for the Blast Furnace
The process of mining low grade iron ore, or taconite, requires massive resources Heavy industrial mining equipment, expansive mines, and a skilled labor pool are all required The equipment used includes diamond bit rotary drills, hydraulic shovels and loaders, water wagons, production trucks and heavyduty conveyors National Steel Pellet Company’s plant is capable of producing 535 During the last ten years great strides have been made, on the Mesabi range, in the practice of beneficiating low grade iron ore material By beneficiation is meant all methods of removing impurities, and raising the iron content to a point where it can be sold in open market, the principal impurities being silica and moisture The general processes to which low grade iron ores are amenable Iron Ore Beneficiation Process INTRODUCTION TO MATERIALS – This is the first post on materials Iron ore and steel production The 6minute video explains the mining and processing of ironIRON ORE AND STEEL PRODUCTION YouTube
- of history of the grinding machine
- how to make a stamped leather belt
- nstruction waste recycling mobile crusher uk
- grinding magenese steel
- mobile crusher in turkey
- PARTIAL REPLACEMENT OF SAND WITH GRANITE DUST POWDER IN CONCRETE
- stainless crusher destemmer sale
- 250 300tph medium hard rock plant for sale
- gwar gum machinery specification
- 6 inch bench grinder with sanding belt
- pper mine apatite jaw crusher made by
- pengolahan pasir besi menjadi sponge iron
- esprit solidmill cam software
- bagaimana bijih besi dibuat dan dimurnikan di tambang terbuka
- Www Stone Crusher 40 Tph Capacity Made By Indian
- mobile dolomite impact crusher manufacturer nigeria
- price of mobile screening quarry
- natural calcium carbonate grinding plants
- logo design for crusher
- environmental impact assessment of open cast gold mining and processing
- average st of crushed stone
- mpanies that manufacture ball mills
- are what are the features of a jaw crusher
- ceramic glaze ball mill machine
- SAMPLE ENGINEERS REPORT FOR A JAW CRUSHER PLANT
- ore grinding machines
- hand operated manual brick making in australia
- big shake table building demands
- stone mining and crushing units mumbai news
- washing machines for gold mining
- cement plants and equipment for cement plants
- bulk material handling grinder
- newcastle 6700 nvert to gar to nar
- nature ph nature of basalt rock
- magnetite spiral chute
- mplete mplete stone crusher unit
- business plan on stone crushing mpany
- machines clearly marble and granite
- baltite ore dressing plantbeneficiation processingproduction line
- list of crusher equipments used in iron ore mines
Stationary Crusher
Sand making equipment
Grinding Mill
Mobile Crusher