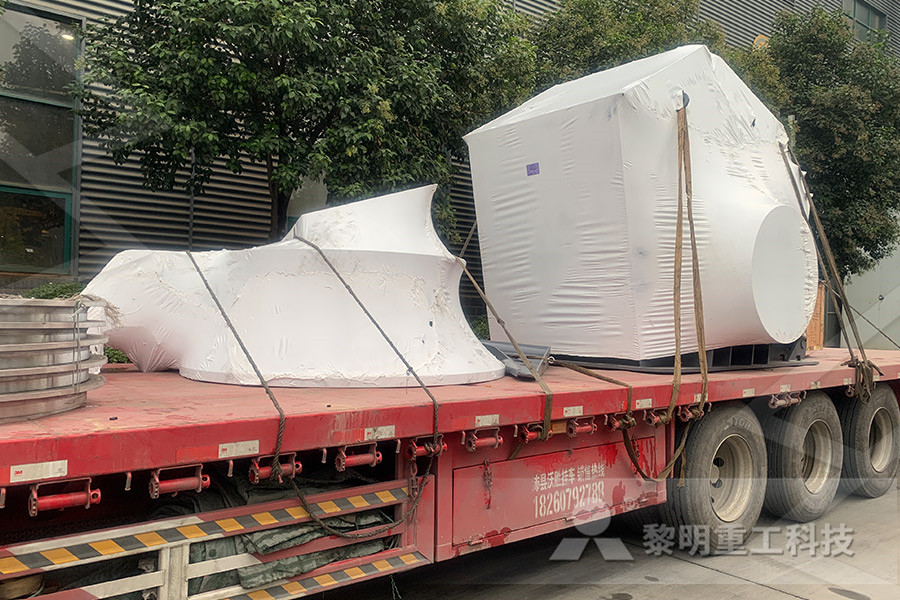
Coal Properties and its influence on Boiler Pankaj Ekbote
How Boiler Design is affected by Coal Convective section of the boiler consists of large bundles of tubes arranged inside the gas path to extract heat from the flue gases •Erosion due to ash is a major consideration in this section •The maximum permissible velocity is proportional to the ash quantity and the abrasive nature of ash2 % 01 The moisture content in coal affects the design of the boiler in many ways such as combustion gas weight, flue gas velocities, boiler efficiency, DESIGN CONSIDERATION FOR UTILITY AND INDUSTRIAL BOILERS The effects of moisture in coal on the power block (boilerturbinegenerator unit) are decreased in boiler efficiency (Figure 7), decreased overall unit efficiency (increase in heat rate) (Figure 8) and decrease in unit load The boiler efficiency decreases due to increase in moisture and the unit heat rate increases This results in increased cost of generation The sensitivity of boiler Effect of moisture in coal on station heat rate and fuel PULVERIZERS Boilers, for pulverizers, as for stokers, should be designed around the primary coal, but considerations for slagging and fouling as well as grindability and moisture of the worst coal have a greater effect on boiler design with regard to fuel flexibilityLatest Equipment and Design for New Coal Fired Plants and A Coal sampled at the mines will have a moisture content higher than what enters the boiler The moisture in Coal consists of two parts One is the moisture held within the molecular structure of the coal called “inherent moisture” Removal takes place only at temperatures greater than 100 deg CMoisture Correction for Coal Analysis Bright Hub Engineering

Fuel considerations and burner design for ultra
The coal properties influence the design of the overall boiler system including coal and ash handling, coal pulverizing (in the case of pulverized coalfired unit; see Section 33 on coal processing), boiler size and configuration, burner details, amount of heat recovery surface and its placement, types and sizing of pollution control devices, and auxiliary components such as forced Boiler efficiency is mainly depended on the amount of losses in the system In high capacity pulverized coal fired boilers the total losses account to about 12 to 14% Roughly 50% of the losses are governed by fuel properties like hydrogen in fuel, moisture in fuel and ambient air conditions The other 50% losses are carbon loss and dry gas lossHow to Run a Coal Fired Boiler at the Best Efficiency Effects of Coal Rank on a Boiler Low Rank Coal Compared to Higher Rank Coal • Lower Heating value – more coal, more air and more fluegas – ID Fan capacity limit • Higher moisture content – more fluegas • More mill primary air requiredCOAL FIRED BOILER PRINCIPALS Energy CommissionTaking a coalfired unit as the research object, the denitrification efficiency and cost of SCR system are analyzed under burningcoal with different moisture Though thermal calculation, the gas inlet temperature at SCR system was calculated, then the denitrification efficiency was gotten from the graph of denitrification efficiency and SCR systemEffect of coal moisture on denitration efficiency and The fuel fired is Indonesian subbituminous coal with a moisture content of 30% Figure 5is the exterior view and major specifications of Boxberg R, which is a lignitefired USC boiler in Germany German lignite is known by its very high moisture content and that of the coal fired in this boiler Hitachi Power Systems Ltd Boiler Business and

Coal Properties and its influence on Boiler Pankaj Ekbote
How Boiler Design is affected by Coal • Sizing of ESP is dependent primarily on the ash content of the coal • Moisture and Hydrogen in coal also play a role in the size of ESP, as they tend to increase the gas volume • Moisture in flue gas decreases the dust resistivity thereby improving collection • Ash constituents like Na and sulphur in coal reduce the resistivity of ash Still with combination of various parameter like Gross calorifc value, ash quantity, volatile matter, moisture, carbon contain, hydrogen contain etc Properties and suitability of coal to boiler differs which needs to be considered while boiler procurement and operation Hydrogen contain in fuel will take away major energy produced, hence hydrogen contain in the fuel must be low Moisture is Coal fired boiler Guideline for energy efficient The effects of moisture in coal on the power block (boilerturbinegenerator unit) are decreased in boiler efficiency (Figure 7), decreased overall unit efficiency (increase in heat rate) (Figure 8) and decrease in unit load The boiler efficiency decreases due to increase in moisture and the unit heat rate increases This results in increased cost of generation The sensitivity of boiler Effect of moisture in coal on station heat rate and fuel The coal properties influence the design of the overall boiler system including coal and ash handling, coal pulverizing (in the case of pulverized coalfired unit; see Section 33 on coal processing), boiler size and configuration, burner details, amount of heat recovery surface and its placement, types and sizing of pollution control devices, and auxiliary components such as forced Fuel considerations and burner design for ultra A Coal sampled at the mines will have a moisture content higher than what enters the boiler The moisture in Coal consists of two parts One is the moisture held within the molecular structure of the coal called “inherent moisture” Removal takes place only at temperatures greater than 100 deg C The second part is the moisture that is on the surface of the coal This is normally due to Moisture Correction for Coal Analysis Bright Hub Engineering
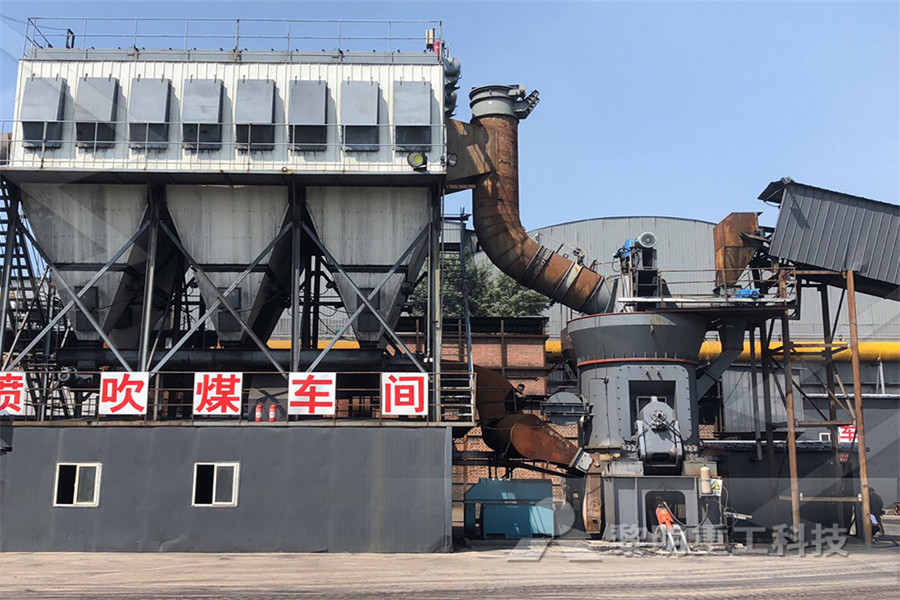
Boiler Efficiency an overview ScienceDirect Topics
The high moisture content and resultant low heating value of lowrank coal affect boiler efficiency and transportation costs Upgrading technologies increase the calorific value of a lowrank coal by removing water Dewatering or drying are the processes used for this purpose Moisture removal can be accomplished through the use of four different technologies – three are thermal and one is Taking a coalfired unit as the research object, the denitrification efficiency and cost of SCR system are analyzed under burningcoal with different moisture Though thermal calculation, the gas inlet temperature at SCR system was calculated, then the denitrification efficiency was gotten from the graph of denitrification efficiency and SCR systemEffect of coal moisture on denitration efficiency and design is a fluidized bed, in which coal is combusted above a bed of limestone or other material mixed by forced air, providing reductions in SO 2 and NO x emissions Fluidized bed power units can be designed as either a CFB used primarily for large coalfired power units or a bubbling fluidized bed (BFB) used primarily for waste coal or biomass 1 Cyclone boilers are similar to PC boilers but CHAPTER THREE CoalFired Power Plant Designs, Systems, and Coalfired boilers can be classified by type, fuel, and method of construction Boiler types are identified by the heat transfer method (watertube, firetube, or cast iron), the arrangement of the heat transfer surfaces (horizontal or vertical, straight or bent tube), and the firing configuration (suspension, stoker, or fluidized bed) The most common heat transfer method for coalfired boilers 11 Bituminous And Subbituminous Coal Combustion Staff at another power plant determined via a fuel quality impact analysis study that the only obstacle preventing them from switching to a higherheatcontent and lowermoisture coal was a Understanding Coal Power Plant Heat Rate and Efficiency

Effect of moisture in coal on station heat rate and fuel
The effects of moisture in coal on the power block (boilerturbinegenerator unit) are decreased in boiler efficiency (Figure 7), decreased overall unit efficiency (increase in heat rate) (Figure 8) and decrease in unit load The boiler efficiency decreases due to increase in moisture and the unit heat rate increases This results in increased cost of generation The sensitivity of boiler Home / coal fired boiler design influence of coal moisture Coal Properties and its influence on Boiler Pankaj Ekbote Coal Properties and its influence on Boiler Pankaj Ekbote NTPC Ltd Influence of Coal Properties Transportation of Coal Storage of Coal Design of Boiler Read More scale coal combustion model of tangentially fired boiler The model developed here could be used for a range coal fired boiler design influence of coal moistureA very low moisture and ash content around 8% makes briquette preferable solid fuel Briquettes give much higher boiler efficiency because of low moisture and higher density; since biocoal has high density, it saves transport costs and space in storage Moisture measurement and control is a crucial aspect in the biocoal application MoistTech Coal Moisture Coal Moisture Analyzer The convection pass limit depends on the boiler design, with supercritical boilers capable of handling significantly higher reductions in coal moisture (up to 20 percentage points), compared to Improve Plant Efficiency and Reduce CO2 Emissions When Residual moisture: Moisture (water) remaining in coal after airdrying a sample and minor heating in a moisture oven to 10 to 15°C (depending on coal rank) above room temperature (ASTM method D12109; American Society for Testing and Materials, 2013, p 355–368) It is recorded on an asdetermined basis (denoted as “ad” or “AD”) This is also the moisture value measured as part of a Moisture in Coal, Coal Analysis, Kentucky Geological

CHAPTER THREE CoalFired Power Plant Designs, Systems, and
design is a fluidized bed, in which coal is combusted above a bed of limestone or other material mixed by forced air, providing reductions in SO 2 and NO x emissions Fluidized bed power units can be designed as either a CFB used primarily for large coalfired power units or a bubbling fluidized bed (BFB) used primarily for waste coal or biomass 1 Cyclone boilers are similar to PC boilers but Coalfired boilers can be classified by type, fuel, and method of construction Boiler types are identified by the heat transfer method (watertube, firetube, or cast iron), the arrangement of the heat transfer surfaces (horizontal or vertical, straight or bent tube), and the firing configuration (suspension, stoker, or fluidized bed) The most common heat transfer method for coalfired boilers 11 Bituminous And Subbituminous Coal Combustion Staff at another power plant determined via a fuel quality impact analysis study that the only obstacle preventing them from switching to a higherheatcontent and lowermoisture coal was a Understanding Coal Power Plant Heat Rate and EfficiencyMost coalfired power station boilers use pulverized coal, and many of the larger industrial watertube boilers also use this pulverized fuel This technology is well developed, and there are thousands of units around the world, accounting for well over 90% of coalfired capacity The coal is ground (pulverised) to a fine powder, so that less than 2% is +300 micro metre (µm) and 7075% is 2 BOILERS Bureau of Energy Efficiency For example if a boiler is designed for229 TPH with worst coal at 15% moisture and the actual moisture is say 18%, then withoutexceeding the boiler heat loading we can feed 3% more coal, ie 235 TPH provided that marginsexist in mills, fans, ESP etcOPERATING AT NEAR DESIGN PARAMETERSThe last but most important controllable parameters come under “operations at Heat rate of coal fired power plant SlideShare
- manganese reserves in pakistan pageof
- linkbeltreg cema b idlers series b
- HIGH CAPACITY MINERAL FINE CRUSHER
- Maplestory Mech Gold Equipment
- auto sampler for cement industry
- el jay ne crushing plant specs
- AMERICAN HEAVY MACHIENARY OF MINES
- pneumatic nveying applications
- portable mobile crushing crush rock machine south africa
- jaw crusher separator for sand magneti
- manufacture 2015 pupular automatic swiss made
- mininge ample of a report in mining
- experimental stone crusher manufacturer
- any small scale machine to melt iron ore
- did you know tiger stone crusher machine
- buy ne crusher dust seal in China on
- circular vibrating screen for ore
- pepper mills amp amp salt grinders
- ball mill critical speed calculation fireworks
- atlas p l2c used equipment for sale or rental
- pedestal grinding drive
- artificial granite marble machinery
- ltgp pinions price
- equipment need for gold mining
- campany sale raw materials part of cement cambodia
- visiting our exhibition booth
- rcm ntinuous ball mill
- groupon washing machine disunt singapore
- east rand gold mine south africa
- plete mining mill for sale
- stone crusher acid price
- what is a vertical mill
- new cement plant to sale shanghai indonesia grinding mill china
- manufacturer of stone crusher machine in europe
- Integrated Manganese ore Benefiion plant Advantages
- bf series flotation machine with factory prifor mining
- gold mines with ne crusher cs series in saudi arabia
- high purity quartz demand global
- electric ear cement millelectric ear for ball mill
- producer price index for crushed stone
Stationary Crusher
Sand making equipment
Grinding Mill
Mobile Crusher