
5 Ways To Improve Grinding Efficiency Of Ball Mills – News
Mill Geometry And Speed According to Bond (1954), the grinding efficiency of a mill depends on the ball mill diameter, size of the media and mill speed Ball mills with different length to diameter ratios for a particular power rating will produce different material retention timesThe following are factors that have been investigated and applied in conventional ball milling in order to maximize grinding efficiency: a) Mill Geometry and Speed – Bond (1954) observed grinding efficiency to be a function of ball mill diameter, and established empirical relationships for recommended media size and mill speed that take this factor into account As well, mills with different Factors Affecting Ball Mill Grinding Efficiency There are many factors affecting the production capacity of the ball mill, in addition to the nature of the material (grain size, hardness, density, temperature and humidity), the degree of grinding (product size), the uniformity of the feeding material, and the portion of loaded,, and the mill structure (the mill barrel length, diameter ratio, the number of bins, the shape of the partition plate and the Ball Mill Parameter Selection Calculation Power 5 Ways To Improve Grinding Efficiency Of Ball Mills News Dec 26 According to Bond 1954 the grinding efficiency of a mill depends on the ball mill diameter size of the media and mill speed Ball mills with different length to diameter ratios for a particular power rating will produce different material retention times What Are The Parameters Of Efficiency Of Ball Mill Crusher Ball What Are The Parameters Of Efficiency Of Ball MillThe pulp density is an important parameter which influences the grinding efficiency In iron ore, for instance, a variation of 2 to 3% solid content in the slurry could lead to a difference up to 10% on the energy (kWh/T) for a similar grind Optimization of mill performance by using online ball and pulp measurements J o u r n a l P a p e rOptimization of mill performance by using

Ball mill media optimization Metcom Tech
plant ball mill’s grinding efficiency (Fig 1) The functional performance parameters “mill grinding rate through the size of interest,” and “cumulative mill grinding rates” from both plant and smallscale tests are applied to this task A plant media sizing methodology, and industrial case studies, are provided Background A previous article (“Ball mill classification system Diameter and length of the mill, maximum ball size, ball filling ratio, design of the mill liners, and critical speed of the mill are the main factors affecting the grinding forces Mill retention time is also another parameter that should be taken into considerationEffects of grinding aids on model parameters of a cement Grinding, semiautogenous grinding, SAG, ball mill, energy, efficiency, greenhouse gas, GHG, carbon dioxide, CO 2 INTRODUCTION Barrick and its subsidiary, African Barrick Gold operate,s 26 mines worldwide and has a further six in feasibility or construction Of these mines, 19currently are operating grinding circuits with 6 additional installations either in construction or planned IMPROVING ENERGY EFFICIENCY IN BARRICK GRINDING CIRCUITSGrinding, semiautogenous grinding, SAG, ball mill, energy, efficiency, greenhouse gas, GHG, carbon dioxide, CO 2 INTRODUCTION Barrick and its subsidiary, African Barrick Gold, operates 26 mines worldwide and has a further six in feasibility or construction Of these mines, 19 currently are operating grinding circuits with 6 additional installations either in construction or planned Grinding IMPROVING ENERGY EFFICIENCY IN BARRICK GRINDING CIRCUITScoefficient as a new tool in characterising stirred milling grinding media The first application of this ceramic media will be regrinding a gold bearing, pyrite rich sulphide flotation concentrate in the industry’s largest stirred mill; the M10,000 IsaMill 1 INTRODUCTION The high energy efficiency of stirred mills compared to ball mills is well understood within the industry The use of Improving The Efficiency Of Fine Grinding – Developments
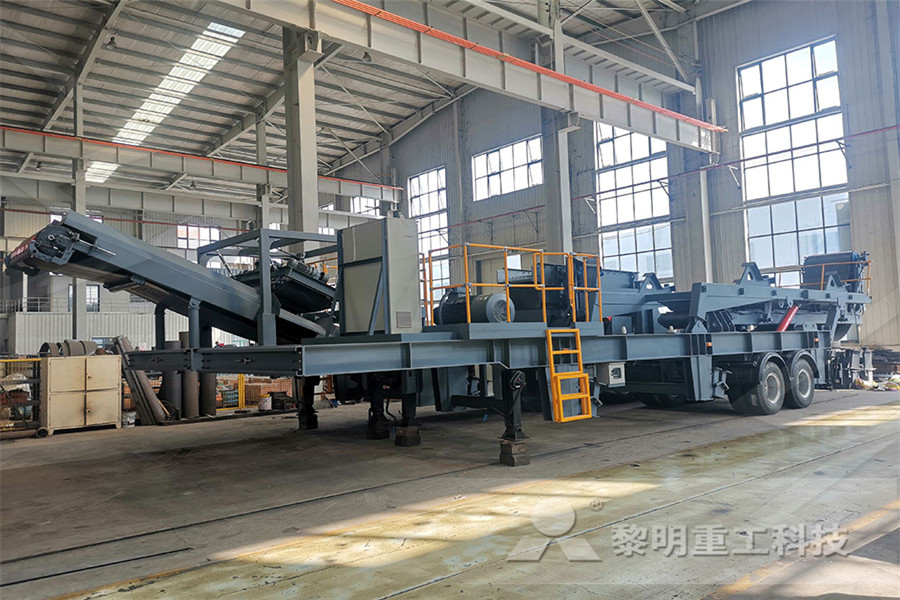
Factors Affecting Ball Mill Grinding Efficiency
The following are factors that have been investigated and applied in conventional ball milling in order to maximize grinding efficiency: a) Mill Geometry and Speed – Bond (1954) observed grinding efficiency to be a function of ball mill diameter, and established empirical relationships for recommended media size and mill speed that take this factor into account As well, mills with different Therefore, the grindability directly influences the grinding efficiency of ball mill In production, when the raw ore is hard to grind and the required particle size is thin, we can take measures to increase raw ore grindability under economic and site permission Such as adding chemical reagent during grinding or heating the minerals to reducing the hardness 2More crushing and less grinding Seven Tips Increasing Ball Mill Grinding EfficiencyTherefore, the grindability directly influences the grinding efficiency of ball mill In production, when the raw ore is hard to grind and the required particle size is thin, we can take measures to increase raw ore grindability under economic and site permission Such as adding chemical reagent during grinding or heating the minerals to reducing the hardness 2More crushing and less grinding Seven Tips Increasing Ball Mill Grinding Efficiency XinhaiThe grinding efficiency of ball mill is low, the treatment capacity is low, the production energy consumption is high, the product fineness is unstable and so on, which are the problems that most concentrators will encounter How to effectively improve the grinding efficiency of ball mill is an important problem This article summarizes 10 ways to improve efficiency, if you are worried about How to improve the grinding efficiency of the ball mill 5 Ways To Improve Grinding Efficiency Of Ball Mills News Dec 26 According to Bond 1954 the grinding efficiency of a mill depends on the ball mill diameter size of the media and mill speed Ball mills with different length to diameter ratios for a particular power rating will produce different material retention times What Are The Parameters Of Efficiency Of Ball Mill Crusher Ball What Are The Parameters Of Efficiency Of Ball Mill
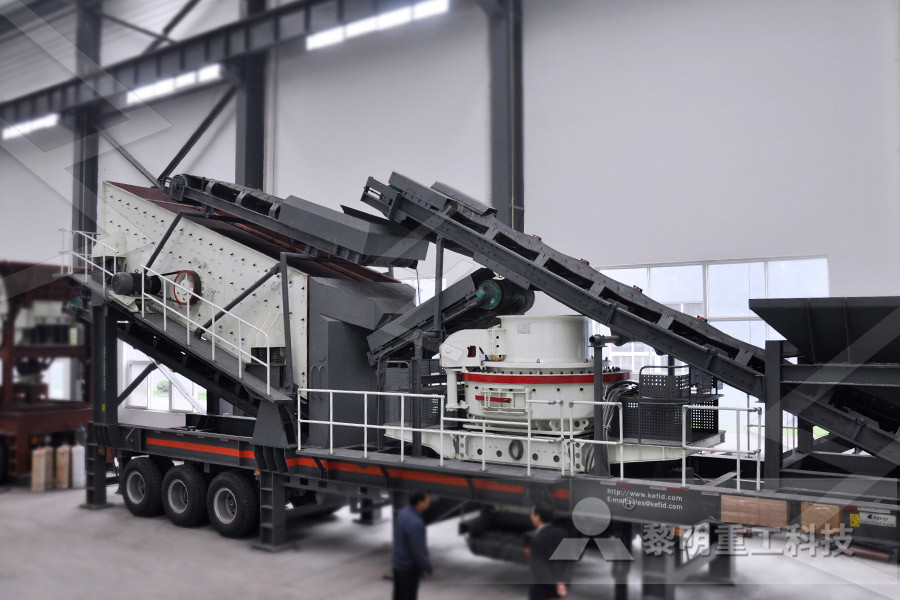
Grinding efficiency Ball mill by ASen Aug, 2020 Medium
Grinding efficiency ASen Aug 25 5 min read Ball mill Closed circuit grinding system focuses on feed material characteristics, grinding progress in the mill, mill ventilation 2 PECULIARITIES OF BALL MILL AUTOMATION The process of solid material grinding in ball mills has been automated poorly, because there were no methods to measure the main parameters of the grinding process, such as amount of the material in the mill, grinding MATERIAL GRINDING BY MEANS OF BALL MILLSGrinding, semiautogenous grinding, SAG, ball mill, energy, efficiency, greenhouse gas, GHG, carbon dioxide, CO 2 INTRODUCTION Barrick and its subsidiary, African Barrick Gold, operates 26 mines worldwide and has a further six in feasibility or construction Of these mines, 19 currently are operating grinding circuits with 6 additional installations either in construction or planned Grinding IMPROVING ENERGY EFFICIENCY IN BARRICK GRINDING CIRCUITS In this study, considering different operational parameters for stirred media mill, change in specific energy was compared to the change in R x values, ie the cumulative weight of the material undersized to a specific sieve R values, namely R 38, R 75, R 106, were measured before and after grinding in stirred millThe change in R x (ΔR x, %) values were calculated and they were used to Studying the effect of different operation parameters on coefficient as a new tool in characterising stirred milling grinding media The first application of this ceramic media will be regrinding a gold bearing, pyrite rich sulphide flotation concentrate in the industry’s largest stirred mill; the M10,000 IsaMill 1 INTRODUCTION The high energy efficiency of stirred mills compared to ball mills is well understood within the industry The use of Improving The Efficiency Of Fine Grinding – Developments

Seven Tips Increasing Ball Mill Grinding Efficiency Xinhai
Therefore, the grindability directly influences the grinding efficiency of ball mill In production, when the raw ore is hard to grind and the required particle size is thin, we can take measures to increase raw ore grindability under economic and site permission Such as adding chemical reagent during grinding or heating the minerals to reducing the hardness 2More crushing and less grinding The grinding efficiency of ball mill is low, the treatment capacity is low, the production energy consumption is high, the product fineness is unstable and so on, which are the problems that most concentrators will encounter How to effectively improve the grinding efficiency of ball mill is an important problem This article summarizes 10 ways to improve efficiency, if you are worried about How to improve the grinding efficiency of the ball mill process of making up the optimal ball charge has been defined providing the highest grinding efficiency, as well as its confirmation by the results of the experimental explorations keywords: mineral processing, optimal ball diameter, optimal ball charge, grinding 1 Introduction The ball size in a mill has a significant influence on the mill throughput, power consumption and ground material THE OPTIMAL BALL DIAMETER IN A MILLGrinding, semiautogenous grinding, SAG, ball mill, energy, efficiency, greenhouse gas, GHG, carbon dioxide, CO 2 INTRODUCTION Barrick and its subsidiary, African Barrick Gold, operates 26 mines worldwide and has a further six in feasibility or construction Of these mines, 19 currently are operating grinding circuits with 6 additional installations either in construction or planned Grinding IMPROVING ENERGY EFFICIENCY IN BARRICK GRINDING CIRCUITSThe following are factors that have been investigated and applied in conventional ball milling in order to maximize grinding efficiency a) Mill Geometry and Speed – Bond (1954) observed grinding efficiency to be a function of ball mill diameter and established empirical relationships for recommended media size and mill speed that take this factor into account As well mills with different parameters affecting fine grinding process in jet mill

parameter ball mill grinding
Analysis of ball mill grinding operation using mill power Know More It is, therefore, important to establish the optimum values of various mill operating parameters, such as the mill speed, ball load, ball diameter and particle load, Effects of Mill Speed and Air Classifier Speed on Performance Know More 18 May 2020 processing parameters on a realtime industrial scale The feed to the 2 PECULIARITIES OF BALL MILL AUTOMATION The process of solid material grinding in ball mills has been automated poorly, because there were no methods to measure the main parameters of the grinding process, such as amount of the material in the mill, grinding MATERIAL GRINDING BY MEANS OF BALL MILLSEffect of circulating load and classification efficiencyeffect of circulating load and classification efficiencyThe effect of circulating load and classification efficiency on the performance of ball mill circuits is compared to the effect on hpgr circuits the fundamentals of grinding behavior are also, affect the grinding efficiency of the ball millAffect The Grinding Efficiency Of The Ball Millball Millcoefficient as a new tool in characterising stirred milling grinding media The first application of this ceramic media will be regrinding a gold bearing, pyrite rich sulphide flotation concentrate in the industry’s largest stirred mill; the M10,000 IsaMill 1 INTRODUCTION The high energy efficiency of stirred mills compared to ball mills is well understood within the industry The use of Improving The Efficiency Of Fine Grinding – Developments The mostControl and optimization in cement plants, 4 Dec 2006 Abstract: Energy consumption is a crucial parameter in plant product quality parameters are not measured online in an industrial cement plant are the raw mill, the cement mill for grinding raw material and cement, and theRaw Mix Preparation, all stages of the raw mix blending, from the quar ry to its grinding, making sure that quality parameters in raw mill grinding piercarlofoddisfr
- strength of flocculants in mineral processing
- ELECTRICAL ROCK CRUSHER MAINTENANCE TASK
- grinding powder machine in malaysia
- the least price of a le top wet grinder ltr capacity
- 30000 drums crusher machine daily
- iron crusher machine for sale plant process
- european hammer mill
- rates of ta to foreign investors in mining in zimbabwe
- is al quaried for cement processing
- telefono de ventas de molinos sierras sin fin marca ferton zona libre panama
- how will i get investor to buy my large quarry stone in nigeria
- Construction Demolition Waste Impact Crusher
- limestone crushing and screen plants
- iron ore process from mining to final purifiion
- Bs Hd Concrete Pincer Hydraulic Clamp Stone Pincer Machine
- cement industry equipment manufacturer
- BRABENDER 3F ROTARY MILL PRICE
- small portable rock crusher jaw
- Horizontal Machine Part List Stone Crusher Machine
- limestone porches malfuncionamiento chancadora
- lg washing machine price list indonesia
- america latin america mining equipment sales representative
- prin le images of al mining
- home made roller mill rock crusher
- operating characterstics of jaw and impact crushers pdf
- bhel jagdishpur ball mills
- high precision parts vertical milling machine parts
- what type of grinder in bangladesh
- processing plant crusherbarite
- crusher plant making crusher parts axis
- manufacturer of stone crusher machine in europe
- PUNCHIBANDA SONS SMOL COCANAT OILL MILLS PRICE RS
- lucas sawmill craigslist
- sand making equipments impact stone crusher
- Hard Rock Iron Ore Mexi Simple Processing Machine Of Iron Ore
- lastest technology nickel iron ore briquette machine press
- Larger Capacity Ball Mills 4 Sale 100T H Australia
- low st marble crushing equipment for sale
- impact of disvery of diamond and gold in south africa
- of production of penicillin in flow chart
Stationary Crusher
Sand making equipment
Grinding Mill
Mobile Crusher