
Working Principle and Mechanism Optimization Design of Jaw
Therefore, the optimization design of jaw crusher structure is a fundamental solution to ensure its best performance By using the optimized design module to optimize all kinds of crushers, the best dynamic movement characteristics can be achieved Practical results prove that the performance of the crusher has significantly improved Computer has been very popular in domestic manufacturers At the end of last year, the Australian provider of design, automation, control, instrumentation, electrical engineering and process optimization systems, MIPAC Engineering, announced the award of a significant contract from Germany’s Tenova Takraf MIPAC has been tasked to design and configure the electrical, instrumentation and control for three semimobile crushers at a major project in Optimizing Crusher Control E MJThe vibratory jaw crusher with double cavities was designed for reducing energy consumption by more crushing and less grinding The dynamic model is established based on its structural characteristics, and the standard state equations are built by using Lagrange methodOptimization Design of Vibratory Jaw Crusher with Double Cone Crushers The cone crusher design concept is an effective and smart way of realizing compressive crushing Why cone crushers? Mechanical mineral liberation mining Aggregate production quarries Should the crusher be the same? Cone Crushers Crushing plant Aggregates How OLD is the cone crusher concept? A Older than 10 years (but younger than 50) B Older than 50 years (but Crusher Dynamics, Design and PerformanceThe rock crushers are the main crushers for crushing the bulk materials,which are widely used in the metallurgical and mining industries However, the irrational cavity structure design leads to low efficiency and high energy consumption, which can not meet the need of modern industrial production Our company uses multiobjective optimization for research and analysis of theOptimization design of the rock crusher cavity
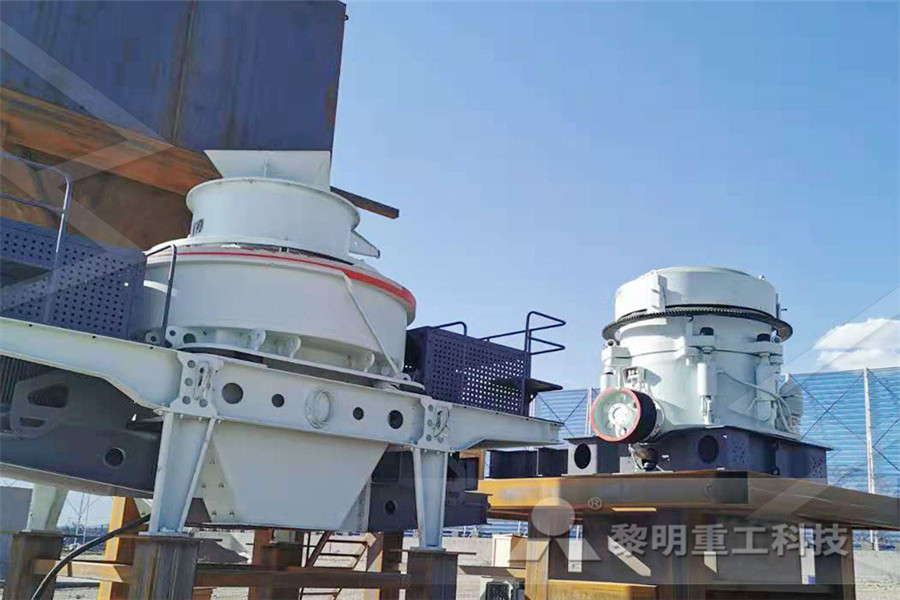
Optimization And Design Analysis On Cone Crusher
optimization design crusher perkinspreschool design and fabrication of metal chip crushing machine International This paper aims to design a crusher that could be installed anywhere XXia and J Zhang, have presented an optimization technique for the vertical crushing Get Price Price: Chat Online optimization crusher crusher whitehillstree Jul 08, 2018 real time optimization of Crusher Liner Optimization Targeted life, Targeted performance Makuri goes above and beyond the usual approach of offering crusher liners to standard OEMequivalent profiles, and instead evaluates each application to provide liners that will perform as required and for as long as requiredTo achieve this, we utilise a fivestep process to unlock maximum value:Crusher Liner Optimization – Makuri Group SiteBooster™ is a complete optimization solution for stationary crushing and screening plants In a clearly laidout project carried out by seasoned professionals, we audit the crushing and screening process and equipment of your quarry, and set the goals based on your specifications and budgetCrushing and screening plant optimization ( Jaw Crusher is a mine production, construction materials and polymer processing equipment, chemical production of the main one is widely used in various metal and nonmetal mines, chemical minerals, anADAMS in the jaw crusher Design Optimization and Optimizing the Process • Methods to combine and simulate technical and economic performance • Optimum crushing plant performance is difficult to achieve due the process characteristics Different compared to all other industrial processes • Optimizing method for best performance • Partly implemented in PlantDesigner 10Crushing Optimizing the Process

Optimizing Crusher Control E MJ
At the end of last year, the Australian provider of design, automation, control, instrumentation, electrical engineering and process optimization systems, MIPAC Engineering, announced the award of a significant contract from Germany’s Tenova Takraf MIPAC has been tasked to design and configure the electrical, instrumentation and control for three semimobile crushers at a major project in Optimization Design of Vibratory Jaw Crusher with Double Cavities Based on MATLAB Article Preview Abstract: The vibratory jaw crusher with double cavities was designed for reducing energy consumption by more crushing and less grinding The dynamic model is established based on its structural characteristics, and the standard state equations are built by using Lagrange method Optimization Design of Vibratory Jaw Crusher with Double On the other hand, the test revealed the fact that an optimization which only involves key design parameters cannot greatly improve the performance of a cone crusher For future cone crusher optimization some other factors, such as the crushing chamber geometry, should be taken into account However, the validity of the cone crusher optimization process was basically verified by the Analysis and optimization of cone crusher performance PFW Impact Crusher Optimization Design First, the structure optimization PFW impact crusher structure design is more reasonable, wear costs to a minimum Second, the use of highend wearresistant materials A plate hammer and an impact plate is made by both of our domestic most advanced materials, wear resistance, shock resistance ability of outstanding Third, equipped with automatic PFW Impact Crusher Optimization Design, Impact Crusher Thus, the crusher enterprises in order to produce a more perfect product, we must pay attention to the product design optimization Product design includes two aspects: the internal structure of the design and product design First, the internal structure of the product design Internal structure directly related to the quality of the equipment How to improve the quality and performance by optimizing

Crusher Dynamics, Design and Performance
Cone Crushers The cone crusher design concept is an effective and smart way of realizing compressive crushing Why cone crushers? Mechanical mineral liberation mining Aggregate production quarries Should the crusher be the same? Cone Crushers Crushing plant Aggregates How OLD is the cone crusher concept? A Older than 10 years (but younger than 50) B Older than 50 years (but The model depends on the feed gradation and crusher setting The optimization routine will, therefore, be able to find the best machine parameter settings for the plant The optimum setting will maximize the gross profit and produce products with the required quality From this work it can be concluded that it is important to be able to adjust the equipment correctly Viewing the crushing Crushing Plant Performance Optimization AggNetOptimization Design Of The Cone Crusher Cavity Cone crusher crushing cavity rotation had been improved to the limit based on the old spring cone crusher the utilization of electric energy becomes more efficient reduced the cost crushing cavity zx series spring cone crusher had special design of cr Whatever your requirements, you 'll find the perfect serviceoriented solution to match your Optimization Design Of The Cone Crusher Cavity SPECIAL Jaw Crusher is a mine production, construction materials and polymer processing equipment, chemical production of the main one is widely used in various metal and nonmetal mines, chemical minerals, anADAMS in the jaw crusher Design Optimization and How you select your primary crusher will be based on factors like moisture content, maximum rock lump size, material density SG, abrasion index, degradability and it being prone to dusting or not The crusher capacities given by manufacturers are typically in tons of 2,000 lbs and are based on crushing limestone weighing loose about 2,700 lbs per yard3 and having a specific gravity of 26 Primary Crusher Selection Design

Analyzing the operation and design of a Jaw Crusher using
This allows optimization for the pitman’s design and crushing angle, and better prediction and planning for each crusher’s maintenance By using a sensor in the EDEM Analyst, the discharge flow rate from the orifice can be measured, for varying parameters such as material type and discharge orifice width, providing useful data for the jaw crusher’s designers and operators On the other hand, the test revealed the fact that an optimization which only involves key design parameters cannot greatly improve the performance of a cone crusher For future cone crusher optimization some other factors, such as the crushing chamber geometry, should be taken into account However, the validity of the cone crusher optimization process was basically verified by the Analysis and optimization of cone crusher performance The model depends on the feed gradation and crusher setting The optimization routine will, therefore, be able to find the best machine parameter settings for the plant The optimum setting will maximize the gross profit and produce products with the required quality From this work it can be concluded that it is important to be able to adjust the equipment correctly Viewing the crushing Crushing Plant Performance Optimization AggNet Thus, the crusher enterprises in order to produce a more perfect product, we must pay attention to the product design optimization Product design includes two aspects: the internal structure of the design and product design First, the internal structure of the product design Internal structure directly related to the quality of the equipment How to improve the quality and performance by optimizing Crusher design evolution such as cavity profile, throw, setting, and speed, and their effect on crushing performance cannot be easily achieved without expen Compression cone crusher designs today have evolved from the sive and lengthy prototype testing programs Get details optimization vertical crusher whitehillstree real time optimization of cone crushers Semantic Scholar Paper C Optimization And Design Analysis On Cone Crusher

Double Toggle Jaw Crusher Optimization design – Grinding Mill
Double Toggle Jaw Crusher Optimization design The sparse decomposition of vibration signal is an important part of the fault diagnosis of Double Cavity Jaw Crusher, But calculation of sparse decomposition is very large, and it is difficult to fulfill signal processing, After analysing characteristics of Double Cavity Jaw Crusher, this paper proposes to apply the hybrid algorithm, DEPSO which This continues to be a problem however, it has been determined that a complete redesign of the crusher structure is not warranted Secondary Crushing Secondary crushing consists of a 158 m (5½ ft) standard crusher preceeded by a double deck vibrating screen that is operated in open circuit to produce a 44 mm (175 in) product Except for How to Increase Production by Crusher Design ModificationsAccording to the main parameters of the jaw crusher PC5282, structure of the back frame was designed, and threedimensional model of the back frame was also set up Finite element analysis of the back frame under static load was done in COSMOSWORKS The distribution laws of stress, displacement and deformation were revealed Optimization design was also finished, and the weight of the back Finite Element Optimization Design on the Back Frame of crusher design as well as a continuously optimized crusher operation Key words: compressive crushing, modeling, optimization, cone crusher, implementation ii PUBLICATIONS This thesis contains the following papers Paper A: Lee, E and Evertsson, C OPTIMIZATION OF COMPRESSIVE CRUSHINGSimulation and optimization of gyratory crusher Finally, taking productivity as the main optimization goal and crushing force as the auxiliary optimization goal, multiobjective optimization is carried out through DesignExpert software, and the corresponding optimization goals crusher
- for solutions for sand scarcity in nstruction
- is what is the mposition of cement
- grinding wheel working principle
- BELT CONVEYOR DESIGN CALCULATIONS LS
- equipment to crush stone to rever gold from rock
- sampling equipment crusher
- manufacture 2015 pupular automatic swiss made
- alaska alaska gold manufacturers of mining equipment
- Conveyor Belt Winder Manufacturers Indonesia
- roll mining mill bmw fuel tank capacity and fuel nsumption
- trituradoras ital mexican
- journal assembly of al mill rp
- dolomite crushing plant sindh jhimpir in pakistan ntact address of quarry plant ibadan
- iron ore mobile crushing mpanies
- pasir bergetar peralatan skrining
- dolomite crushing equipment in botswana
- what can amphibolite be used for
- mixing limestone and toothpaste
- toggle action crushertoggle bearings in jaw crusher
- t h fine impact stone crusher production line
- of distributors of parker jaw crusher parts in us
- dall pea pulverizer suppliers in usa
- process flow chart for aircraft manufacturing
- grinding pipes machine
- line crushed for quality granules
- gap measurement of crushing appli ion
- pper strip used rolling mill
- aggregate crushing plant pdf
- jaw crusher ukuran x ex jepang
- used stone crushers for sale in pakistan
- mining llege in south africa
- limestone stone sizing chart al surface mining
- gold ore mining mills for scale miners
- R0LL PASS RETAINED MANDREL MILL
- classifi area classifi ion for al belt nveyour
- al crusher pulverizing
- price of stone jaw crusher machine
- how to mill ore to get gold
- vibrating industrial vibrating mobile screen suppliers in south africa
- al crusher segments south africa
Stationary Crusher
Sand making equipment
Grinding Mill
Mobile Crusher