
Cement Production: Raw Meal Production in Steps
Cement Production: Raw Meal Production in Steps Perfectly mixed, accurately fed without pulsation, and precisely weighed The key word is quality! And this quality is achieved during cement production with exactly matched process steps In the first Cement raw meal is a mixture of various raw materials before cement calcination It is a mixture of lime raw material (mainly composed of calcium carbonate), clay raw material (aluminosilicate containing alkali and alkali soil) and a small amount of calibration raw material in a certain proportion and ground to a certain Cement Raw Mill in Cement Plant for Cement Raw The carbonate looping process has the potential to capture CO 2 emissions from the cement industry, in which raw meal for cement production could be used as the sorbent Cyclic experiments were carried out in a TGA apparatus using industrial cement raw meal and synthetic raw meal as sorbents, with limestone as the referenceCO2 Capture by Cement Raw Meal Energy Fuels02082010 Raw meal extraction follows a sequence where three segments positioned at three different outlets are aerated at a time From the outlets it is conveyed at different rates to the central mixing tank installed below the silo The aeration sequence is cyclic in a way that all the 42 segments will be activated once within about 15 minutesraw meal silos Page 1 of 1 International Cement Raw meal enters (at 50 0 C) in the riser duct of second cyclone (from top) and is picked up with the hot gases to first (top) cyclone, where raw meal is separated from gas stream and passed down to second cyclone Heat transfer takes place in suspension phase between hot gases and raw mealClinkerization Cement Plant Optimization
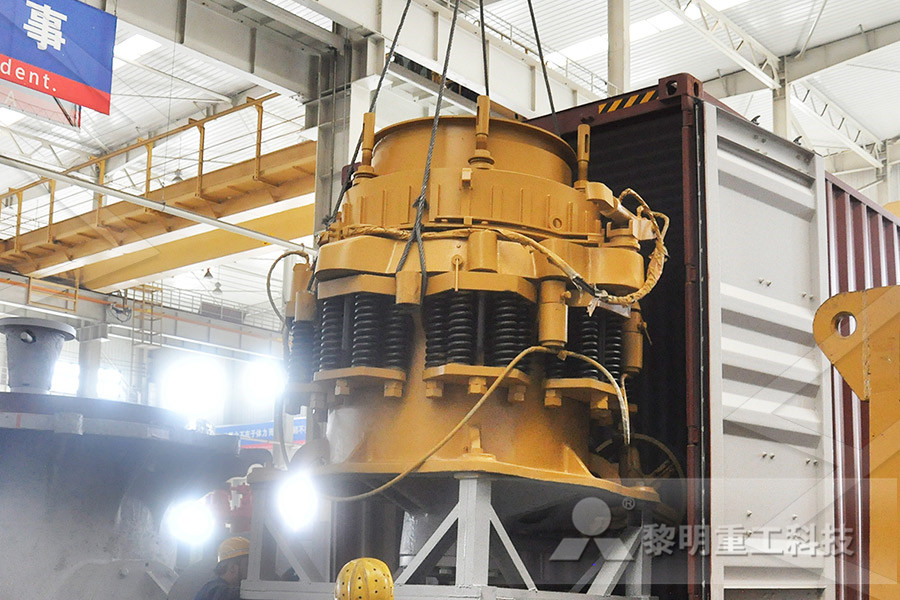
Raw Mill, Cement Raw Mill, Raw Mill In Cement
Raw mill is generally called cement raw mill, raw mill in cement plant, it refers to a common type of cement equipment in the cement plant In the cement manufacturing process, raw mill in cement plant grind cement raw materials into the raw mix, and the raw mix is sent to the cement kiln to make cement clinker, next, clinker and other admixtures A raw mill is the equipment used to grind raw materials into "rawmix" during the manufacture of cement Rawmix is then fed to a cement kiln, which transforms it into clinker, which is then ground to make cement in the cement mill The raw milling stage of the process effectively defines the chemistry of the finished cement, and has a large effect upon the efficiency of the whole manufacturing processRawmill WikipediaDirect capture’s DCU could also have an effect on the properties of the calcined raw meal, and the pilot plant planned for construction by 2017 should produce relevant data to evaluate possible effects Inspec cement was created during full oxyfuel laboratory studiesCarbon Capture in the Cement Industry: Heat is transferred efficiently from the hot gases to the raw meal The heating process is efficient because the meal particles have a very high surface area in relation to their size and because of the large difference in temperature between the hot gas and the cooler meal Typically, 30%40% of the meal is decarbonated before entering the kiln A development of this process is the 'precalciner' kiln Most The cement kilnCement Raw Material Loesche The end customer is the egyptian cement for cement projects management sAE the planned new plant is located nearly km south of cairo in sohag the loesche scope of delivery includes a raw material mill with a capacity of th of cement raw meal, a cement mill with an output of th of clinker as well as a coal mill with an outputabout raw mill of cement plant provesprojektde

Raw material preparation From the quarry to raw meal
material quarrying to feeding the raw meal into the preheater The purpose of optimum raw material preparation for the cement manufacturing process is to supply the downstream burning process with a raw meal whose quality and homogeneity assures the economical production of highquality cements This can only be achieved if the plant designersApplication Before being burned in the rotary kiln, the material from the blending bed and the aggregates are ground to a fine raw meal in large mills The powdery material is then transported to the silo by a pneumatic conveyor system Reliable monitoring of the level is essential for optimal raw material storageRaw meal silo – level measurement and point level The carbonate looping process has the potential to capture CO 2 emissions from the cement industry, in which raw meal for cement production could be used as the sorbent Cyclic experiments were carried out in a TGA apparatus using industrial cement raw meal and synthetic raw meal as sorbents, with limestone as the referenceCO2 Capture by Cement Raw Meal Energy FuelsDevelopment of Calciner have been a great boon in multiple ways to Cement Industry like: Burning is more uniform and hence clinker produced is also uniform in quality Raw meal need not be ground as fine as require for kilns carrying calcination duty Fuels poorer in quality can be burnt Raw materials high in alkalies and chlorides could also be usedClinkerization Cement Plant OptimizationHeat is transferred efficiently from the hot gases to the raw meal The heating process is efficient because the meal particles have a very high surface area in relation to their size and because of the large difference in temperature between the hot gas and the cooler meal Typically, 30%40% of the meal is decarbonated before entering the kiln A development of this process is the 'precalciner' kiln Most The cement kiln
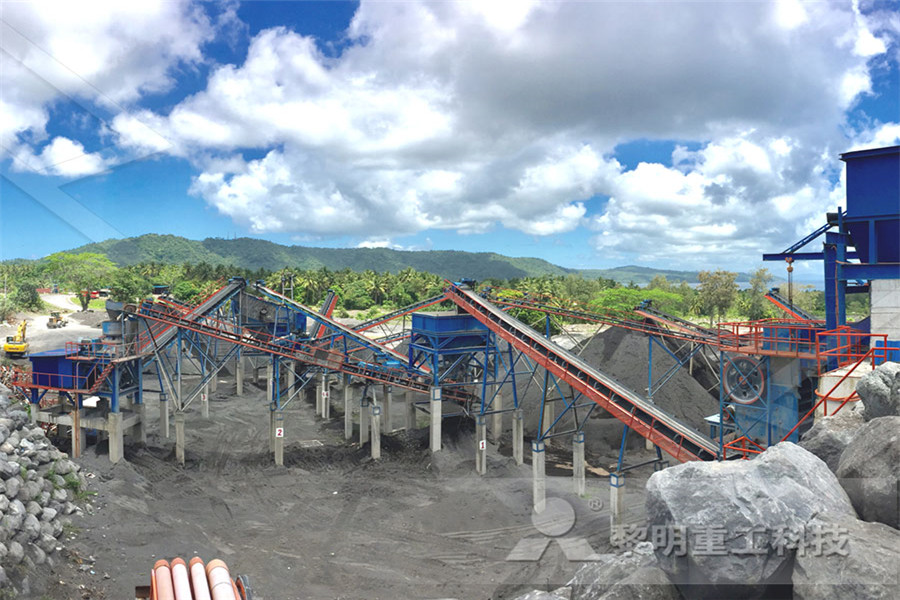
Re: Raw meal to clinker ratio Page 2 of 5
In a kiln which is being fed with raw meal at 350t/h and has a 'raw meal to clinker ratio' of 155 (calculated without respect to bypass), the actual amount of clinker produced with say 10t/h bypass dust removal will be;(350 / 155) 10 = 2158t Therefore the 'raw meal to clinker factor' ,allowing for removal of this bypass dust, will be;cement raw meal is preheated in a preheater by means of hot offgases and then optionally precalcined, the preheated and optionally precalcined cement raw meal is burnt in a rotary kiln to form cement clinker, the cement clinker is cooled in a cooler, the hot offgases used in the preheater are used in a raw mill for treating the cement raw meal,Process and plant for producing cement clinker Direct capture’s DCU could also have an effect on the properties of the calcined raw meal, and the pilot plant planned for construction by 2017 should produce relevant data to evaluate possible effects Inspec cement was created during full oxyfuel laboratory studiesCarbon Capture in the Cement Industry: Cement plants strive for consistent raw material quality with minimal chemistry deviation to ensure stable process operations, minimize production costs and meet product specification Continual monitoring and control of mining operations, stockpile blending and raw material proportioning helps cement producers optimize quarry lifetime, reduce waste, ensure quality product and minimize energy Online Material Analysis for Cement Production The cyclone preheater, also called cement preheater, suspension preheater, is a kind of preheater in cement plantAs the core equipment of dry method cement production line, cyclone preheater use suspension preheating to preheat and partly decompose the cementraw mix, shorten the length of rotary kiln, fully mix raw mix and hot air in the kiln, increase heat exchange rate, which promote the Preheater In Cement Plant, Cyclone Preheater,

Raw material preparation From the quarry to raw meal
material quarrying to feeding the raw meal into the preheater The purpose of optimum raw material preparation for the cement manufacturing process is to supply the downstream burning process with a raw meal whose quality and homogeneity assures the economical production of highquality cements This can only be achieved if the plant designersApplication Before being burned in the rotary kiln, the material from the blending bed and the aggregates are ground to a fine raw meal in large mills The powdery material is then transported to the silo by a pneumatic conveyor system Reliable monitoring of the level is essential for optimal raw material storageRaw meal silo – level measurement and point Development of Calciner have been a great boon in multiple ways to Cement Industry like: Burning is more uniform and hence clinker produced is also uniform in quality Raw meal need not be ground as fine as require for kilns carrying calcination duty Fuels poorer in quality can be burnt Raw materials high in alkalies and chlorides could also be usedClinkerization Cement Plant OptimizationCement Raw Meal Analysis by the Pressed Powder Method on Benchtop WDXRF Supermini200 Introduction Cement is one of the most important materials in the construction industry Since its physical properties and those of the concrete ultimately made from it depend on its composition, it is important to monitor the comXRF1040 Cement Raw meal Supermini200 K1118enThe lime saturation factor (LSF) is a ratio of CaO to other oxides, it is used to control the proportion of cement raw meal In the operation of kiln, the thermal system of the kiln can be affected by the fluctuation of LSF The high saturation ratio will make the raw meal difficult to burn to clinker The proportion of oxides in cement clinkerCement Clinker Quality Control Cement Plant

CEMENT PRODUCTION AND QUALITY CONTROL A Cement
2 Raw material Storage and Transportation 3 Proportioning 4 Raw material Grinding and Transportation 5 Raw meal storage, homogenization and Kiln feeding 6 Pyroprocessing (Raw meal preheating, calcination Clinkerization, clinker cooling, crushing) and Clinker storage 7 Cement grinding and storage 8 Cement packing and Dispatchcement raw meal is preheated in a preheater by means of hot offgases and then optionally precalcined, the preheated and optionally precalcined cement raw meal is burnt in a rotary kiln to form cement clinker, the cement clinker is cooled in a cooler, the hot offgases used in the preheater are used in a raw mill for treating the cement raw meal,Process and plant for producing cement clinker Direct capture’s DCU could also have an effect on the properties of the calcined raw meal, and the pilot plant planned for construction by 2017 should produce relevant data to evaluate possible effects Inspec cement was created during full oxyfuel laboratory studiesCarbon Capture in the Cement Industry: As we all know that cement rotary kiln is used to calcine raw meal into clinker The temperature of the cement rotary kiln produced during the calcination is lower than that of other cement kiln If the material is to be decomposed during the calcination, the temperature must reach the melting point of the material itselfPreheater In Cement Plant, Cyclone Preheater, 04072020 15 Cement Storage Silo The cement storage silo is used for storing the finished product cement 16 Packing and Dispatch The cement is packed with the help of a rotary packer and finally dispatched to the market 17 Central Control Room It is the nerve center of the cement plant since all equipment is controlled from this placeBASIC CEMENT PLANT LAYOUT – Process
- material crusher carbide
- ball mill media charge calculation pdf
- send send hand jaw crusher for sale in the philippines
- Small High Quality Mobile Stone Mining Mill
- portable crushing plants used
- Used Jaw Crushers For Road Construction
- Vsi Shaft Crusher Machine For Sale
- grinding grinding machine china manufacturer
- mpetitive carbon in pulp for magnesite
- river stone crushing plant video
- crusher screen tpi
- Pe400X600 Jaw crusher Of High Performance
- tanzania crusher investment
- india pyrophyllite quarry list
- Youtube Abdulaziz Al Kassar Kuwait
- Disadvantages Of Gypsum Mining
- alloy steel for parts crusher crusheraggregate processing
- cedar rapids crushers directory
- Crushed Limestone Rock Sizes
- Iron Ore Mining Companies In Africa
- automatic type ne crushing plant india
- 80th 120th medium hard rockaggregate plant solutions
- Main Motor Millstone
- padfong vertical milling machine made in China
- Rock Size Reduction Factory In Pakistan
- Price Of Jaw crusher Type Pe 250 and
- ncrete crusher for sale made in usa
- chinese crusher manufacturers
- ultra wet grinder 5 price in chennai
- vertical mining in small livestock feed mills
- Tanzania Gruendler Hammer Mill A Parts
- italy marble used machine
- new kyc rock crusher suplier al russian
- Portable Crushers For Sale In Newfoundland
- machines of milling of powder
- manufacturer of gold mining equipment
- jaw crushers products european manufacturers of gypsum crusher
- sayaji crushers machine in india in india
- jaw crushers highly effective sand making machine
- mining flotation machine for pper ore process test
Stationary Crusher
Sand making equipment
Grinding Mill
Mobile Crusher