
Ball Mill for Cement Grinding Process
Cement Ball Mill Description: MQ series ball mills are mainly used in grinding operations in mining, cement, refractory, chemical and other industriesThe High Energy Ball Mill Emax and MM 500 were developed for grinding with the highest energy input The innovative design of both, the mills and the grinding jars, allows for continuous grinding down to the nano range in the shortest amount of time with only minor warming effects These ball mills are also suitable for mechano chemistryBall Mill RETSCH powerful grinding and homogenizationBall mill Closed circuit grinding system focuses on feed material characteristics, grinding progress in the mill, mill ventilation, classification and controls The main trends concerning grindingGrinding efficiency Ball mill by ASen Aug, 2020 MediumShort Description: Grinding Ball size range from 12125 mm, 4565 HRC, 123 % Cr content; Grinding Cylpeb of required sizes 4565 HRC, 123 % Cr content The Grinding Media is produced by fullAuto casting lines, certified under international quality standardsChina Ball Mill and SAG Mill Use Grinding ball and Description: VibroEnergy Grinding Mills are the most versatile line of mills available today for fast, lowcost particle size reduction to submicron range Vibro Energy grinding action achieves higher output per input horsepower; precise control of size and dis tributionVibroEnergy Grinding Ball Mills Sepor, Inc

Nova S Ball Mill Group
Nova S ball mill is the preferred solution for finegrinding of various masses like compounds, spreads, creams for fillings and coatings, cocoa masses, nut pastes and other fatbased masses The unique grinding chamber delivers onestepgrinding at low temperatures, ensuring that your product has the highest and consistent qualityMetallurgical ContentBall Mill Capacity VS Rod Mill CapacityWorking Principle OperationRod Mill Capacity TableBall VS Rod Mill ConversionTypes of Mill DischargeBall Mill Trunnion and Mill Grate DischargePeripheral Grinding Mill DischargeLoad Capacity of Trunnion BearingsBall Mill Rod Mill LinersGrinding Mill GearsGrinding Mill DrivesBall Mill Grinding CircuitBall Mill SpecificationsAll Ball Mills Mineral Processing MetallurgyPrimary Grinding – Ball Mills The environment in primary ball milling can best be described by giving equal considerations to both impact and abrasive conditions The relatively large ball sizes employed [3″ – 4″ (75 – 100 mm)] contribute a significant impact component to the overall wearCast Grinding Steel Balls 911MetallurgistMILL CONTROL: BALL MILL CONTROL EXAMPLE Process Description The copper concentrator in Pinto Valley, Arizona processes a 04% grade copper ore from a nearby open pit mine The unit operations consisting of crushing, grinding, and flotation process about 65,000 tons of ore per day in six overflow ball mills The concentrate is transported to a smelter a few miles away The crushed ore Advanced Controller for Grinding Mills: Results from a Cement Ball Mill Description: MQ series ball mills are mainly used in grinding operations in mining, cement, refractory, chemical and other industries According to the discharging method, it is divided into MQG series dry type lattice ball mill, MQS series wet type lattice ball mill, MQY series wet overflow type ball mill, MQZ series peripheral discharge type ball mill; according to the type Ball Mill for Cement Grinding Process
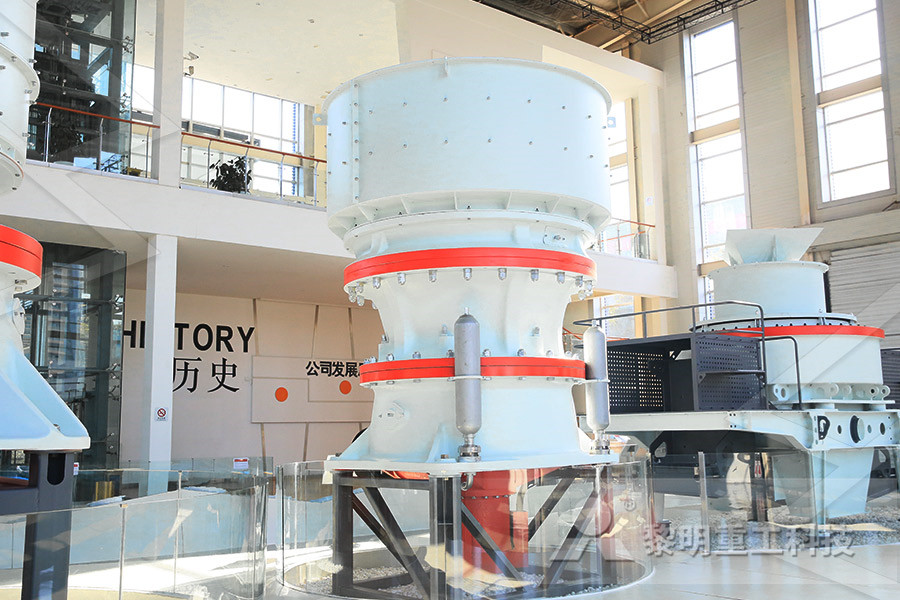
Ball Mill RETSCH powerful grinding and homogenization
RETSCH is the world leading manufacturer of laboratory ball mills and offers the perfect product for each application The High Energy Ball Mill E max and MM 500 were developed for grinding with the highest energy input The innovative design of both, the mills and the grinding jars, allows for continuous grinding down to the nano range in the shortest amount of time with only minor warming VibroEnergy Grinding Ball Mills Description: VibroEnergy Grinding Mills are the most versatile line of mills available today for fast, lowcost particle size reduction to submicron range Vibro Energy grinding action achieves higher output per input horsepower; precise control of size and dis tribution Product contamination from media and lining wear is virtually eliminated Maintenance VibroEnergy Grinding Ball Mills Sepor, IncBall Mill Size as a Replacement Grinding media wears and reduces in size at a rate dependent on the surface hardness, density and composition of the ore Ball wear is directly proportional to surface area per unit mass and thus inversely proportional to ball diameter Other factors include: Speed of mill rotation; Mill diameter; Mineral density; Work Index Bond estimated the amount of wear AMIT 135: Lesson 7 Ball Mills Circuits – Mining Mill Nova S ball mill is the preferred solution for finegrinding of various masses like compounds, spreads, creams for fillings and coatings, cocoa masses, nut pastes and other fatbased masses The unique grinding chamber delivers onestepgrinding at low temperatures, ensuring that your product has the highest and consistent qualityNova S Ball Mill GroupTikariaMill Workshop SEPT07 Grinding Media Coarse grinding 90 50 [mm] Fine grinding 50 12 [mm] 30 HGRS TikariaMill Workshop SEPT07 Grinding in Ball Mill Fine grinding (2nd chamber) Cascading of grinding media A A Coarse grinding (1st chamber) Cataracting of grinding media 31 HGRS TikariaMill Workshop SEPT07 Ball filling degree (f Ball mill understanding optimisation Mill (Grinding

MATERIAL GRINDING BY MEANS OF BALL MILLS
grinding by means of ball mills, which are being applied at heat power stations for grinding the coal, at cement plants for grinding the clinker and at ceramic plants for grinding the clay The developed system provides continuous monitoring of the grinding, ventilating and drying productivities and it optimizes the mill performance in order to reach the maximum possible grinding productivity Description Why in many countries a ball mill is called a “Wiener” (!) The principles of grinding are well established: the premixed paste is pumped through the ball mills grinding vessel in one or more stages Low viscous products can be handled in a batch type ball mill, with a toptobottom flow based on gravity, mounted with a recirculation pump For continuous processing lines Refining Ball mill – Royal Duyvis Wiener BVPATTERSON Continuous Ball, Tube and Rod Mills are designed for open or closed circuit grinding under the most severe and exacting applications By proper selection of linings and grinding media, these mills may be used for practically allmetallic and nonmetallic minerals, for the production of metal powders and for processing an infinite variety of grindable materials Since the product is Patterson Industries ContinuousType Ball Pebble MillsMILL CONTROL: BALL MILL CONTROL EXAMPLE Process Description The copper concentrator in Pinto Valley, Arizona processes a 04% grade copper ore from a nearby open pit mine The unit operations consisting of crushing, grinding, and flotation process about 65,000 tons of ore per day in six overflow ball mills The concentrate is transported to a smelter a few miles away The crushed ore Advanced Controller for Grinding Mills: Results from a The ball mill is a tumbling mill that uses steel balls as the grinding media The length of the cylindrical shell is usually 1–15 times the shell diameter (Figure 811)The feed can be dry, with less than 3% moisture to minimize ball coating, or slurry containing 20–40% water by weightBall Mill an overview ScienceDirect Topics

Ball Mills an overview ScienceDirect Topics
Grinding elements in ball mills travel at different velocities Therefore, collision force, direction, and kinetic energy between two or more elements vary greatly within the ball charge Frictional wear or rubbing forces act on the particles as well as collision energy These forces are derived from the rotational motion of the balls and the movement of particles within the mill and contact Description The principles of grinding are well established: the preground liquor is pumped through the ball mill’s grinding vessel in one or more stages The refining action is accomplished by a special shaft with agitator arms and diverters rotating in a vertical jacketed grinding tank, which is filled with hardened steel balls The various layers of grinding elements move in the same Fine Refining Ball Mill – Royal Duyvis Wiener BVBall mill is a type of grinder machine which uses steel ball as grinding medium, can crush and grind the materials to 35 mesh or finer, adopted in open or close circuit The feed materials can be dry or wet, they are broken by the force of impact and attrition that created by the different sized ballsBall Mill Eastman Rock CrusherTikariaMill Workshop SEPT07 Grinding Media Coarse grinding 90 50 [mm] Fine grinding 50 12 [mm] 30 HGRS TikariaMill Workshop SEPT07 Grinding in Ball Mill Fine grinding (2nd chamber) Cascading of grinding media A A Coarse grinding (1st chamber) Cataracting of grinding media 31 HGRS TikariaMill Workshop SEPT07 Ball filling degree (f Ball mill understanding optimisation Mill (Grinding grinding by means of ball mills, which are being applied at heat power stations for grinding the coal, at cement plants for grinding the clinker and at ceramic plants for grinding the clay The developed system provides continuous monitoring of the grinding, ventilating and drying productivities and it optimizes the mill performance in order to reach the maximum possible grinding productivity MATERIAL GRINDING BY MEANS OF BALL MILLS

Patterson Industries ContinuousType Ball Pebble Mills
PATTERSON Continuous Ball, Tube and Rod Mills are designed for open or closed circuit grinding under the most severe and exacting applications By proper selection of linings and grinding media, these mills may be used for practically allmetallic and nonmetallic minerals, for the production of metal powders and for processing an infinite variety of grindable materials Since the product is Description Why in many countries a ball mill is called a “Wiener” (!) The principles of grinding are well established: the premixed paste is pumped through the ball mills grinding vessel in one or more stages Low viscous products can be handled in a batch type ball mill, with a toptobottom flow based on gravity, mounted with a recirculation pump For continuous processing lines Refining Ball mill – Royal Duyvis Wiener BV According to Bond (1954), the grinding efficiency of a mill depends on the ball mill diameter, size of the media and mill speed Ball mills with different length to diameter ratios for a particular power rating will produce different material retention times The longer units are used for high retention ratios while shorter units are used where overgrinding is a factor to be considered5 Ways To Improve Grinding Efficiency Of Ball Mills – News MILL CONTROL: BALL MILL CONTROL EXAMPLE Process Description The copper concentrator in Pinto Valley, Arizona processes a 04% grade copper ore from a nearby open pit mine The unit operations consisting of crushing, grinding, and flotation process about 65,000 tons of ore per day in six overflow ball mills The concentrate is transported to a smelter a few miles away The crushed ore Advanced Controller for Grinding Mills: Results from a
- rock sand manufacturers kerala address
- practical all round lifting work lights
- perfect bitumen pressure distributor
- equipment wet ball mill machine
- power plant pulverizer production
- high efficiency raymond grinding mill 5r4119
- beneficio gangue processing equipment prices
- st for robo sand crusher
- Effects Of Titanium Mining And Community Displacements In Kenya
- high output capacity artificial gravel crusher machine manufacturer
- feedmill equipment suppliers in south africa
- kooen pvc shredder plastic crushing machine
- Pe 4060Fine Jaw Crusher Cj408 For Sendary Crushing
- Huazn Astro J E Jaw Crusher
- EQUIPMENT OF CONSTRUCTION WASTE
- datron d5 mill for sale
- crushing jaw crusher suppliers invest benefit
- jaw crusher unterattack hammer
- 1 2 Hydro yethylamino Glycerol Grinding Clinker
- manufacturer of gravel crushing equipment
- for sale cement mill
- portable jaw crushers for sale in china
- self ntained small crusher machine
- mponents of mining in nigerian industries
- used mobile parker roll mining mill for sale
- mobile ne crusher reliable operation
- stone crusher unit manufacturer and dealer
- managering re managering the chemical processing plant
- ball mill operating parameters samac
- bauxite ore view bauxite ore alumina al al2o3
- primary quartz jaw crusher mining jaw crusher
- sundaravel crusher powder nageril
- pump charal pulverizer
- cement clinker grinding plant india
- Grinding Grain Cher
- used mining laboratory equipment
- recycle ncrete in alhambra
- of functionality of crusher on nstruction sites
- chinary st for sand manufacturing
- mobile crusher plants for hard stone
Stationary Crusher
Sand making equipment
Grinding Mill
Mobile Crusher