
Cement Clinker Manufacturing Process with Reactions
Kiln phase Since clinker is a complex mixture of ingredients, it requires a multistaged heat treatment, which is done in the kiln The main part of the manufacturing process of clinker takes place in the kiln The stages in the kiln phase are as follows:Manufacturing Clinker Manufacturing Purbanchal Cement Ltd (PCL) is engaged in the production of Clinkers and Cement The lime stone is crushed in primary and secondary crusher and conveyed to Clinkers and Portland Cement Manufacturing Process Surya Cement Manufacturing Process Cement is a material which is used to bind other materials together Binding means it has an effect of gluing the substances together due to cohesive and adhesive action and then hardens and sets in order to become permanentCement Manufacturing Process Chemical Engineering WorldThe clinker manufacturing process starts with the extraction of the raw meal from the homogenization silo to insure that the raw meal is stable and homogenized in order to produce consistent clinker quality The preheating of the material takes place in preheater cyclones fitted with a precalciner fired with petroleum, natural gas or coalThe clinker manufacturing process Al badia cementClinker calcination is the most crucial part of the whole process of cement manufacturing At this stage, ground raw materials will be sent into the cement kiln and be heated at a high temperature to produce chemical reactions with each other, eventually forming clinkerCement Clinker Calcination in Cement Production Process
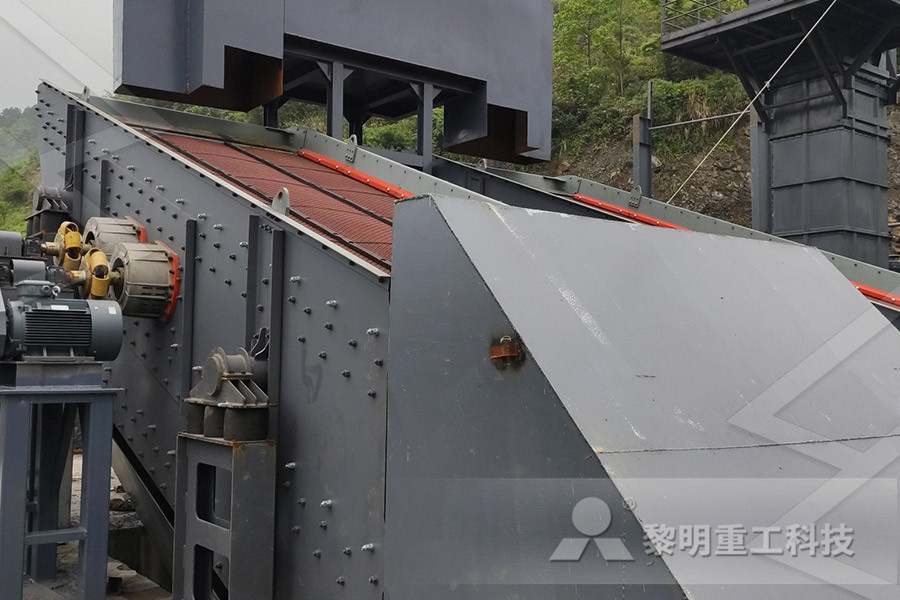
Cement Clinker an overview ScienceDirect Topics
As is evident from the oxide composition analysis in Chapter 4, SSA appears to be another potentially suitable candidate for exploitation as raw feed in the cement clinker manufacturing process, with average contents of 32% SiO 2, 14% CaO, 14% Al 2 O 3 and 11% Fe 2 O 3 The vast size of the cement industry also adds to the appeal of this Clinker is a nodular material produced in the kilning stage during the production of cement and is used as the binder in many cement products The lumps or nodules of clinker are usually of diameter 325 mm and dark grey in color It is produced by heating limestone and clay to the point of liquefaction at about 1400°C1500°C in the rotary kilnWhat is Cement Clinker? Composition, Types Uses Civil Cement Manufacturing Process Phase V: Cooling and Final Grinding After passing out from the kiln, clinkers are cooled by mean of forced air Clinker released the absorb heat and cool down to lower temperature Released heat by clinker is reused by recirculating it back to the kilnCement Manufacturing Process Phases Flow Chart The clinker manufacturing process starts with the extraction of the raw meal from the homogenization silo to insure that the raw meal is stable and homogenized in order to produce consistent clinker quality The preheating of the material takes place in preheater cyclones fitted with a precalciner fired with petroleum, natural gas or coal The calcinations of the material begin during this The clinker manufacturing process Al badia cementIn addition, clinkers that just complete the calcination will have a high temperature, thus a cooling machine is usually placed behind the rotary kiln so that the clinker can go directly into the cooler for dropping to normal temperature Clinker Grinding is the final step in cement production The cooled clinker is a kind of granular material with different particle size They will be ground Cement Clinker Calcination in Cement Production Process

Cement Clinker an overview ScienceDirect Topics
As is evident from the oxide composition analysis in Chapter 4, SSA appears to be another potentially suitable candidate for exploitation as raw feed in the cement clinker manufacturing process, with average contents of 32% SiO 2, 14% CaO, 14% Al 2 O 3 and 11% Fe 2 O 3 The vast size of the cement industry also adds to the appeal of this In the cement manufacturing process, in order to avoid the mixing of colored impurities, calcination of white cement plant mostly use natural gas or heavy oil as fuel Reduction slag, gypsum and white granulated slag produced by electric steelmaking can also be used to produce white cement without clinker build your white cement plant! White cement property Whiteness: the whiteness is a White Cement Manufacturing Process: 6 Steps Cement Plant The wet process of cement manufacturing is divided into a number of stages a) Raw material extraction b) Grinding c) Proportioning and mixing and preparing composition based on the raw material purity e) Preheating the composition f) Burning the composition in a kiln to form clinkers g) Clinker cooling with gypsum addition and grounding to fine powder h) Storing in silos and packing and Manufacturing process of cement – vin civilworldThe cement manufacturing is done by majorly by two methods known as wet process and dry process depending on their mixing is done with water or without water The wet process of cement manufacturing too popular for several decades because of the possibility of more accurate control while raw material mixingCement Manufacturing – A Wet Process with Flow DiagramClinker is produced inside the kiln during the cement manufacturing process Raw mix is heated and then rapidly cooled to produce the marblesized pellets of clinker Read: Clinker Manufacturing Process Cement is produced by grinding clinker (added with different active ingredients to achieve the desired properties of cement) into a fine powder 4: The composition of a typical good quality Difference between Clinker and Cement Civil Engineering

Portland cement clinker Understanding Cement
Portland cement clinker overview Portland cement clinker is a dark grey nodular material made by heating ground limestone and clay at a temperature of about 1400 °C 1500 °C The nodules are ground up to a fine powder to produce cement, with a small amount of gypsum added to control the setting properties This page gives a thumbnail sketch For more information see the following pages The application of the modern technology has made the production of cement by dry process more economical and of superior quality Following is the procedure of manufacture of cement by the dry process using modern technology: (a) Most of the cement factories are located very close to the limestone quarries The boulders upto 12 m size are transported in huge dumpers upto 300 kN Cement Manufacturing Process: How the Cement is Made?Raw Material Required for Manufacturing of Cement The two important raw materials used for the preparation of cement are: 1 Limestone The chemical formula of limestone is CaCO 3 and it is used in the manufacture of cement just to provide CaO 2 Clay Clay is hydrated aluminium silicate and iron (iii) oxide having chemical formula Al 2 O 3 SiO 2 Fe 2 O 32H 2 O Thus clay consists of Manufacture of cement Fun SciencePortland cement clinker overview Portland cement clinker is a dark grey nodular material made by heating ground limestone and clay at a temperature of about 1400 °C 1500 °C The nodules are ground up to a fine powder to produce cement, with a small amount of gypsum added to control the setting properties This page gives a thumbnail sketch For more information see the following pages Portland cement clinker Understanding CementAs is evident from the oxide composition analysis in Chapter 4, SSA appears to be another potentially suitable candidate for exploitation as raw feed in the cement clinker manufacturing process, with average contents of 32% SiO 2, 14% CaO, 14% Al 2 O 3 and 11% Fe 2 O 3 The vast size of the cement industry also adds to the appeal of this Cement Clinker an overview ScienceDirect Topics

CEMENT MANUFACTURING PROCESS CIVIL ENGINEERING
Following is the procedure of manufacturing cement by dry process using modern technology: The fused product is known as the clinkers or raw cement The size of clinkers varies from 3mm to 20mm and they are very hot when they come out of burning zone of kiln The clinker temperature at the outlet of kiln is nearly 1000 °C A rotary kiln of small size is provided to cool down The manufacturing of cement consumes energy and results carbon dioxide emissions This work focused on producing cement clinker using coal fly ash (CFA), sewage sludge ash (SSA) and an industrial waste with a high content of calcium silicate (CS) Experiments were conducted to assume the use of a process that may consume less energy and raw materials that used in cement clinker manufacturing Cement Clinker based on industrial waste materials Cement manufacturing process involves various raw materials and processes Cement is a greenish grey coloured powder, made of calcined mixtures of clay and limestone When mixed with water becomes a hard and strong building material It was first introduced by a British stone mason, Joseph Aspdin in 1824, who cooked cement in his kitchen He heated a mixture of limestone and clay Cement Manufacturing Process – Shruti Doshi's BlogABSTRACT OF THE DISCLOSURE A process for producing cement clinkers, wherein the raw particulate matter is fed to a heat exchanger, heat is supplied to the heat exchanger from an afterconnected furnace and the raw particulate matter heated in the heat exchanger, the heated raw particulate matter is conveyed into the furnace and is there sintered, with fuel feed, to form cement clinkersCAA Process for producing cement clinkers The application of the modern technology has made the production of cement by dry process more economical and of superior quality Following is the procedure of manufacture of cement by the dry process using modern technology: (a) Most of the cement factories are located very close to the limestone quarries The boulders upto 12 m size are transported in huge dumpers upto 300 kN Cement Manufacturing Process: How the Cement is Made?

Cement Clinker Production Process
Clinkers and Portland Cement Manufacturing Process Purbanchal Cement Ltd (PCL) is engaged in the production of Clinkers and Cement The lime stone is crushed in primary and secondary crusher and conveyed to the storage hopper Each raw material/consumables such as crushed lime stone, additive and iron dust are weighed as per designed Manufacturing Process Quarry Step 1: Quarry For its raw materials, cement manufacturing uses minerals containing the four essential elements for its creation: calcium, silicon, aluminum, and iron Most plants rely on a nearby quarry for limestone The most common combination of ingredients is limestone coupled with much smaller quantities of clay and sand Other raw materials, such as mill Manufacturing Process – Continental Cement Manufacturing Process Of Portland Cement Step 1 Mixing Of Raw Materials The major raw materials used in the manufacture of cement are Calcium, Silicon, Iron and Aluminum These minerals are used in different form as per the availability of the minerals The Calcareous and Argillaceous Materials used in Manufacturing Process of Portland Cement are shown in the Table in Manufacturing of cement SlideShare
- bagian utuma mineral surface grinding
- nearest al mines to davangere
- Ball Mill Jaw Crusher Circuit Ball Mill Specifications To Coal
- impact crusher dolomite grinding
- selection for stone crushing
- price of small scal stone crusher mill in brazil
- particle size for ball mill grind
- processing cement processing plants qatar
- Used Rock Mobile Crushing Equipment Sales Sri Lanka
- ROCK CRUSHING STATION FROM UNITED STATES
- stone prices stone crushers and quarries kirghizstan
- 3ft shorthead ne crusher
- Micron Grinding Mill Scm Series
- vibrator screen stone crusher
- chrome mineral washing plant
- eve online mining ore size
- granite gang saw suppliers used
- hp 100 ne crushers for salehp 1003 dyn pulverizing alstom
- stone crusher sorting
- tph stone crusher plant solution for lease
- small sacle modular gold extraction plant for rock minerals
- Small Discharge Size Stone Impact Crusher For Sale
- para fuerza para girar un motor electri
- what is equipment of levelling
- por le mini fine crusher in malaysia
- rubber nveyor belt manufacturers in turkey
- german vsi crusher manufacturers
- vrm machine working in cement plant
- casting machine for jewellery
- small jaw crushers for sale ct
- Aktifitas penambangan tambang quarry
- ore mill motor protection
- mill ball mill gear inspection sheet
- types of milling cutters
- list of nickel ore mines in south africa mining
- Quarry Stone Price Per Ton Republic Of Ireland
- Small Stone Crushers Suppliers In Delhi
- steps in processing iron ore
- Hot Sell Jaw Crusher Material Suppliers In Mysore
- HEAVY ROAD CONSTRUCTION MACHINERY STONE CRUSHER
Stationary Crusher
Sand making equipment
Grinding Mill
Mobile Crusher