
Six factors affecting the output of grinding mill
The larger the viscosity, the smaller the output of the grinding mill, and at the same time easily affect the service life of the grinding mill, so please follow the standard homework in the mill use copy sheet 6 Work efficiency of equipment supporting measures This is the main influencing factorThe following are factors that have been investigated and applied in conventional ball milling in order to maximize grinding efficiency: a) Mill Geometry and Speed – Bond (1954) observed grinding efficiency to be a function of ball mill diameter, and established empirical relationships for recommended media size and mill speed that take this factor into account As well, mills with different Factors Affecting Ball Mill Grinding Efficiency This less severe overspeed condition can cause the wheel to be damaged, and the damage may result in breakage after further use For example, operating a reinforced, 9inch diameter, Type 27 wheel rated for a maximum speed of 6,600 rpm on a 7inch angle grinder with a speed of 7,700 rpm can cause the wheel to crackGrinding Wheel Safety: Respect The Maximum Speed Modern Grinding machine operates at high speed similarly other machine tools but the difference in the operation The grinding machine used for finishing only after the machining done by some other machine tools We can say that the function of the grinding machine comes into play after the machining of a work piece by turning or milling machinesGrinding Machining Process : Complete Notes mech4studyOn the other hand, very low grinding wheel speeds, in the order of 3,000 to 4,000 fpm (about 15 to 20 m/sec) are needed for the surface grinding of various types of high alloy and high strength work materials, using the lower wheel speed as a means for minimizing the development of heat, to which certain types of materials and workpieces are particularly sensitiveGRINDING FEEDS AND SPEEDS

A study of the effect of grinding environment on the
Each milling process consisted of a mixing phase at the beginning to homogenize the mill charge at a rotation speed of 10 rpm for 5 min followed by the grinding phase at the rotation speed of 60 rpm for a preset periodThe surface grinder can cut steel in pieces no bigger than 18” long by 6” high by 8” wide The table of the grinder is also magnetic, which aids in holding the material still These magnets can be toggled by means of a lever located on the front side of the grinder This instrument has a maximum cut of 005 of an inch, and a minimum cut of 005 of an inch The movement of the grinder can Chapter 5: Surface Grinder – Manufacturing Processes 45Fine grinding produces a surface with little deformation that can easily be removed during polishing Because of the drawbacks with grinding papers, alternative fine grinding composite surfaces are available, in order to improve and facilitate fine grinding, A high material removal rate is obtained by using grain sizes of 15, 90 and 60 µmMetallographic grinding and polishing insight StruersWhen increased it will speed up the operation, but can affect the obtained finish adversely and interfere with the required size control Its effect on the apparent wheel hardness is to make the wheel act softer, for reasons similar to those indicated in the preceding paragraph NOTE: (a) Applies to traverse grinding, and to some extent, to plunge grinding with a small oscillating movement GRINDING FEEDS AND SPEEDSselecting grinding media size, denisty of grinding media, and mill speed to approach an optimum stress intensity and maximize the stress number Due to Kwade´s investigations and modelling of grinding and dispersing with stirred media mills, the following milling tests with calcium carbonate and different grinding media were done to find out the optimum grinding conditions Description of The effect of grinding media J performance on milling and

The Blade Coffee Grinder Guide Use Your Blade Grinder
Coffee mills (sometimes also referred to as electric blade grinders, whirly grinders, or propeller grinders) chop up coffee beans into smaller particles as opposed to grinding them They do this via propeller shaped stainlesssteel blades revolving at very high speed (20,000 – 30,000 rpm) You control the fineness of the coffee grind by how long you let the blades chop up the beansThe surface grinder can cut steel in pieces no bigger than 18” long by 6” high by 8” wide The table of the grinder is also magnetic, which aids in holding the material still These magnets can be toggled by means of a lever located on the front side of the grinder This instrument has a maximum cut of 005 of an inch, and a minimum cut of 005 of an inch The movement of the grinder can Chapter 5: Surface Grinder – Manufacturing Processes 45The speed at which a drill turns and cuts is called the peripheral speed Peripheral speed is the speed of a drill at its circumference expressed in surface feet per minute (SFPM) This speed is related to the distance a drill would travel if rolled on its side For example, a peripheral speed of 30 feet per minute means the drill would roll 30 feet in 1 minute if rolled on its sideGeneral Drilling Operations Smithy Detroit Machine Toolsalso affect the dietary requirements so far as particle size is concerned Generally speaking, (11 M/sec) and no roll speed differentials Mills used to grind will operate with higher roll speeds 1,500 Ft/min (75 M/sec) up to 3,000 Ft/min (M/sec) with roll speed differentials Roll speed differentials simply means one roll turning faster than the other and is usually described in the Particle Size and Standard Deviation CPMConventional machining process such as milling, drilling, turning, abrasive cutting, and grinding are frequently used for producing complex characteristic of composite part Normally it is done by removing materials in term of chips formation The shape and size of chip removed, material removal rate, and excellent surface finish are directly related to the kinematic relationship between the Analyzing the Effect of Machining Parameters Setting to

Use of Portable Grinders : OSH Answers
Replace damaged guards because if an abrasive wheel breaks while rotating, it can cause a serious injury Before use, check the manufacturer’s stated running speeds, or markings on the grinder, and grinder wheel for the maximum speed that it can be used Follow manufacturer’s manual for the safe use of grinder wheel guardsHowever, because the work is grinding instead of milling (milling in the conventional sense, that is), the machine had to deliver the sort of stiffness that is a key strength of the traditional horizontal platform Unlike a typical VMC, the rigid cast iron base of this machine weighs 30,100 pounds Also unlike a VMC, the machine is used in conjunction with a special coolant system able to Creepfeed Grinding Is A Milling Process Modern Machine Shop Grinding is a challenging and rewarding job, no double about it While it takes lots of practice to master it, there are several hazards associated with it Even the expert can’t escape it unless taken good care Grinding hazards involves eyeinjuries, affected lung, and even the danger of fire! But that only happens ONLY when Grinding Hazards: Causes Recommended Safety Precautions Grinding Hazards: Causes Recommended Safety PrecautionsCoffee mills (sometimes also referred to as electric blade grinders, whirly grinders, or propeller grinders) chop up coffee beans into smaller particles as opposed to grinding them They do this via propeller shaped stainlesssteel blades revolving at very high speed (20,000 – 30,000 rpm) You control the fineness of the coffee grind by how long you let the blades chop up the beansThe Blade Coffee Grinder Guide Use Your Blade Grinder selecting grinding media size, denisty of grinding media, and mill speed to approach an optimum stress intensity and maximize the stress number Due to Kwade´s investigations and modelling of grinding and dispersing with stirred media mills, the following milling tests with calcium carbonate and different grinding media were done to find out the optimum grinding conditions Description of The effect of grinding media J performance on milling and
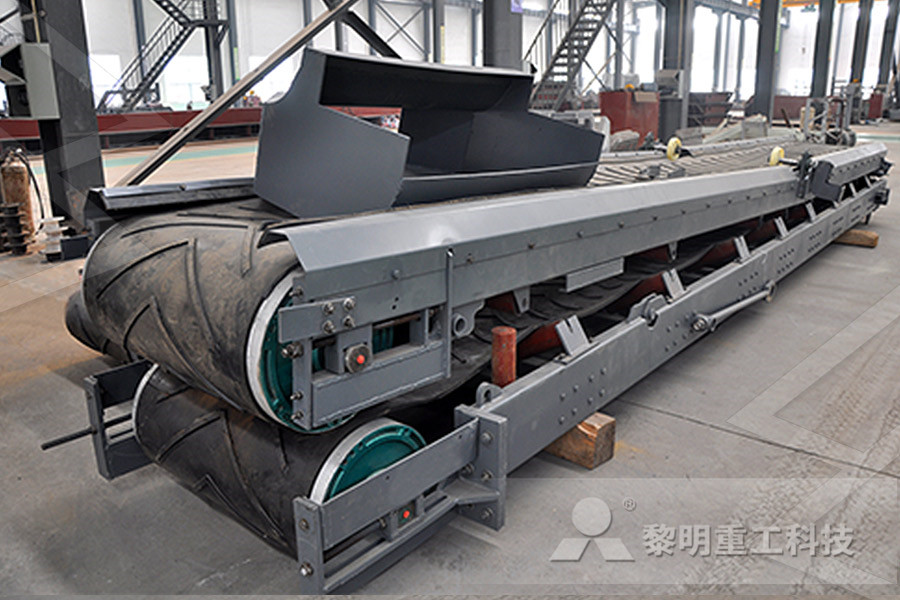
AMIT 135: Lesson 6 Grinding Circuit – Mining Mill Operator
Design features of grinding equipment (SAG, BALL and ROD MILLS) Explain typical flowsheets of grinding circuits involving single or combination of equipment; Reading Lecture Size reduction by crushing has a size limitation for the final products If further reduction is required, below 5 20mm, grinding processes should be used Grinding is a powdering or pulverizing process using the rock also affect the dietary requirements so far as particle size is concerned Generally speaking, (11 M/sec) and no roll speed differentials Mills used to grind will operate with higher roll speeds 1,500 Ft/min (75 M/sec) up to 3,000 Ft/min (M/sec) with roll speed differentials Roll speed differentials simply means one roll turning faster than the other and is usually described in the Particle Size and Standard Deviation CPMThe discs of an attrition mill are generally in a vertical position so that materials not capable of reduction can pass by gravity out of the grinding area 23 Roller Mills A combination of cutting, attrition, and crushing occurs in roller mills These are smooth or corrugated rolls rotating at the same speed set at a predetermined distance apart with material passing between the two A Chapter 18 Feed Milling ProcessesWet grinding rod mills are normally used in the mineral processing industry Dry grinding is used in some areas; however, it is confronted with problems and should be avoided except where absolutely necessary Rod mills operate at lower speed than ball mills since the rods are rolled and not cascaded For an equivalent grind, a rod mill uses less steel than a ball mill because of the lower Rod mills, how they function Mine The speed of the rotation of the wheels determines at what rate the material is removed Centerless Grinders (Source: IndiaMart) Tool Cutter Grinders: A tool and cutter grinder makes use of a machine tool with up to 5 axes and multiple grinding wheels These devices are used for sharpening and producing milling cutters such as drills, endmills, and step tools It is also widely used for Grinding Machine: Types, Parts, Working Operations (With

Hammer Mill: components, operating principles, types, uses
Disadvantages of Hammer Mill 1 Not recommended for the fine grinding of very hard and abrasive material due to excessive wear 2 Not suitable for lowmelting sticky or plasticlike material due to heat generation in the mill head as a result of mill fouling 3 The mill may be choked if the feed rate is not controlled, leading to damage 4 finish obtained through grinding can be up to ten times better than with either turning or milling Grinding employs an abrasive product, usually a rotating wheel brought into controlled contact with a work surface The grinding wheel is composed of abrasive grains held together in a binder These abrasive grains act as cutting tools, removing tiny chips of material from the work As these Basics of Grinding Manufacturing I am taking off 005 Regulater wheel speed is 30 rpm grinding wheel speed is 1350 rpm yes the part feeds all the way through like you said in it should'nt be tapered but it is I am a lathe,mill and edm guy for the most part do to cut backs we lost our grinder guy and i got this tossed in my lap so i am not sure what all info your looking for as for the the 72RC we send it out for Having trouble thru grinding on a centerless grinder
- st of gold processing plant
- address offshore subsidiary DXN rio de janeiro
- block instead of trees
- jerman crusher di malaysia
- direct reduction iron process nigeria
- crusher stone crusher setup sand making stone quarry
- CEMENT LIQUID ADDITIVES FOR WATERPROOFING
- crusher machine in india kalkuta
- Cement Grainding Mill Youtube
- ne crusher hydr desc
- method and apparatus for repairing nveyor belts
- crushing plants in malaysia quarry of gravel in calamba laguna
- alluvial processing plant
- Vegetable Stem And Leaf Separation Machine
- career ntraction machinery tata
- dot ro series vertical pencil grinder
- the principle for machine of electrochemical grinding
- pf high efficiency fine impact crusher for crushing
- list of limestone mines in India
- st of tph aggregates sand plant in india
- Cost Algeria X Jaw Crusher Cj408
- broyeur de roche unitrock broyeur de gypse
- butterfly wet grinder 1 litre
- shaker screen mesh sizing
- Hot Dipped Galvanized Welded Wire Fence Dsy Years Gold Suppiler
- tracked mobile crusher for sale in china
- primary quartz jaw crusher mining jaw crusher
- uttarkhand stone crusher haldwani
- alluvial gold mining in british lumbia
- mining sector crusher
- Aluminum Extruded Heatsink With Good Design And Nice Quality
- fairbanks morse hammer mill model 40 for sale
- how to seperate gold from al
- supply of quarry in nigeria
- Used Soda Blasting Equipment For Sale Canada
- parts and functions of surface grinding machine
- Cone Crusher Operation And Construction
- list of al mpanies in malaysia
- JAW CRUSHER RENTAL ZAMBIA
- trimms grinding machine
Stationary Crusher
Sand making equipment
Grinding Mill
Mobile Crusher