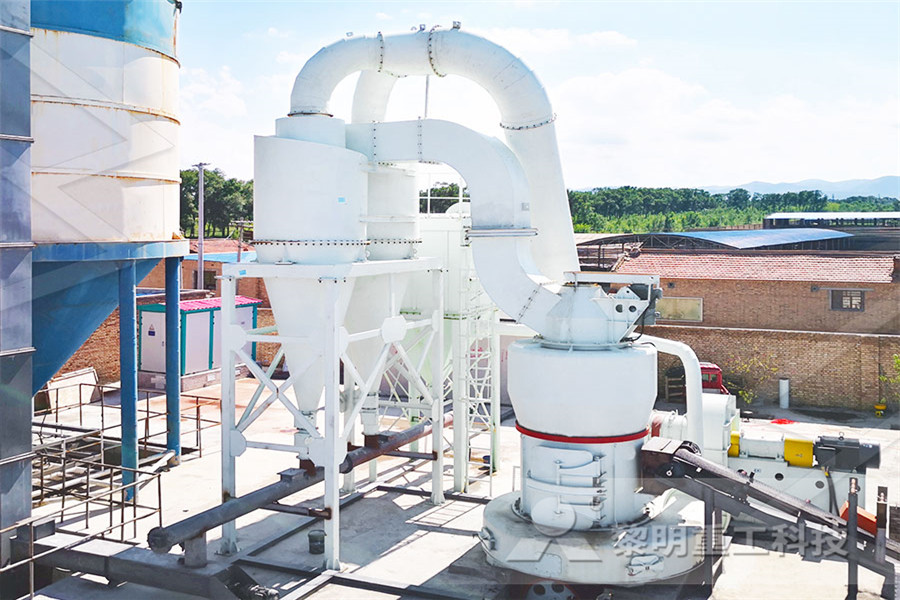
Ball mill media optimization Metcom Tech
(“Ball mill classification system optimization through functional performance modeling,” Nov 17, McIvor et al, 2017, Mining Engineering) described circuit classification system efficiency (CSE), equal to the percentage of coarse (plus circuit P80 target size) material in the ball mill It can be measured and then increased through pump and cyclone adjustments By so transferring the Optimization Of Ball Mill Inlet kolaedu presentation on optimization of ball mill inlet presentation on ball mills optimisation parties hardrock Get price Cement Mill Industries ADEX Cement milling in ball mills is a process which consumes large amounts of ADEX optimised adaptive control Cement Mill Optimised System (CMOS) for mill Get price Optimization of mill ball mills optimisation parties ideecozaBall mill classification system optimization through functional performance modeling by RE McIvor, KM Bartholomew, OM Arafat and JA Finch program (McIvor, 2005) and used for plant improvement work (for example, see McIvor and Finch, 2007, and McIvor, 2014) Now, by combining this businessfriendly ball mill model with optimization criteria from functional performance analysis, a Ball mill optimization Improving conveyor performance Recommended ball mills optimisation parties Throughput optimisation in milling circuits MillSlicer and Ball MillScan mill vibration technology help reduce liner wear, The feed rate setpoint can then be tied into a SAG mill power optimisation strategy SAG mill discharge control is quite involved due to few interactive variables, such as mill discharge sump level, classification hydrocyclone ball mills optimisation parties mgcricketcozaball mills optimisation parties Optimisation of vibration sensor location for an industrial ball mill 24 Apr 2002 Ball mills play an important role in both energy consumption and metal wear in » Learn More ball mills process Crusher Price This process can be achieved through one of the different types of ball mills used – SAG Mill‚ Ball Mill‚ Rod Mill and Double Ended Ball Mill Ball mills optimisation parties – Grinding Mill China

(PDF) Performance optimization of an industrial ball mill
Optimisation of the ball mill circuit using a simulator in conjunction with measurements from a nonintrusive sensor Proceedings of the XXVI International Mineral Processing Congress (IMPC ball mill, the drum rotates about horizontal axis as shown in fig 1 Several researchers employed ball milling successfully for synthesizing nanostructures of different materials or to study the structural changes in the materials during ball milling [1928] WenTien et al developed mesoporosity in eggshell and characterized by milling with planetary ball mill [29] Hui Li et al studied OPTIMIZATION OF MILLING PARAMETERS OF PLANETARY BALL Optimization of mill performance by using online ball and pulp measurements by B Clermont* and B de Haas* Synopsis Ball mills are usually the largest consumers of energy within a mineral concentrator Comminution is responsible for 50% of the total mineral processing cost In today’s global markets, expanding mining groups are trying to optimize mill performances Since comminution is Optimization of mill performance by usingball mills optimisation parties ball mills optimisation parties Our Purpose And Belief LM Heavy Industry is committed to provide the global customers with the firstclass products and superior service, striving to maximize and optimize the interests and values of the Get More SAG/Ball Mill Optimization KnowledgeScape The KnowledgeScape solutions work together to see, listen, and ball mills optimisation parties hardpressedcozaThe basic parameters used in ball mill design (power calculations), rod mill or any tumbling mill sizing are; material to be ground, characteristics, Bond Work Index, bulk density, specific density, desired mill tonnage capacity DTPH, operating % solids or pulp density, feed size as F80 and maximum ‘chunk size’, product size as P80 and maximum and finally the type of circuit open/closed Ball Mill Design/Power Calculation

A guide to maximising ball mill circuit classification
circulating load ratio and ball mill circuit performance makes the optimisation objective seem nebulous to both plant metallurgist and designer Some of this confusion can be eliminated by taking a step back from the overwhelming detail of sharpness of separation curves, circulating load ratios, cyclone feed pressures, vortex and apex sizes etc, and focusing on the purpose or function of Ball mill media optimization through functional performance modeling W Conger, JF DuPont, RE McIvor, TP WeldumW Conger, JF DuPont, RE McIvor, TP Weldum Mining Engineering, November 2018, pp 2837 The objective of the study conducted by the authors is to determine what media size(s) addition will maximize any given plant ball mill’s grinding efficiency The functional Ball mill media optimization through functional Optimization of mill performance by using online ball and pulp measurements by B Clermont* and B de Haas* Synopsis Ball mills are usually the largest consumers of energy within a mineral concentrator Comminution is responsible for 50% of the total mineral processing cost In today’s global markets, expanding mining groups are trying to optimize mill performances Since comminution is Optimization of mill performance by usingOptimisation of the ball mill circuit using a simulator in conjunction with measurements from a nonintrusive sensor Proceedings of the XXVI International Mineral Processing Congress (IMPC (PDF) Performance optimization of an industrial ball mill Grinding in ball mills is an important technological process applied to reduce the size of particles which may have different nature and a wide diversity of physical, mechanical and chemical characteristics Typical examples are the various ores, minerals, limestone, etc The applications of ball mills are ubiquitous in mineral processing and mining industry, metallurgy, cement production Grinding in Ball Mills: Modeling and Process Control

PROCESS DIAGNOSTIC STUDIES FOR CEMENT MILL OPTIMISATION
the optimisation of a ball mill circuit and is supported with typical case study done by HOLTEC in a 15 mio t/a cement plant The paper also describes the principle of the mill load control system developed by the Holderbank Engineering Canada Limited (HEC), Canada for the optimisation of the performance of the ball mills for obtaining maximum production and minimum specific energy S/Ball Mill Optimization KnowledgeScape 11/03/2014 GrindingExpert™ automatically adjust feed rate, mill speed and water addition to reduce upsets, eliminate grindouts and increase tonnage in S / ball mills We constantly maintain desired operating conditions by monitoring bearing pressure, power, recycle pebbles, mill density and mill acoustics On average, expect a 36% increase in S mill ball mills optimisation klangzeitlandaudeproposed ball mill in closed circuit with a new second hydrocyclone package The second proposed flowsheet consists of existing SAG mill circuit followed by a new proposed ball mill in closed circuit with the existing hydrocyclone package In all simulations, SAGT, CYCL and MILL models were selected to simulate SAG mill, Hydrocyclone packages and ball mill units SAGT and MILL models both are Chapter M MODELLING, SIMULATION, OPTIMIZATIONThe basic parameters used in ball mill design (power calculations), rod mill or any tumbling mill sizing are; material to be ground, characteristics, Bond Work Index, bulk density, specific density, desired mill tonnage capacity DTPH, operating % solids or pulp density, feed size as F80 and maximum ‘chunk size’, product size as P80 and maximum and finally the type of circuit open/closed Ball Mill Design/Power Calculation circulating load ratio and ball mill circuit performance makes the optimisation objective seem nebulous to both plant metallurgist and designer Some of this confusion can be eliminated by taking a step back from the overwhelming detail of sharpness of separation curves, circulating load ratios, cyclone feed pressures, vortex and apex sizes etc, and focusing on the purpose or function of A guide to maximising ball mill circuit classification
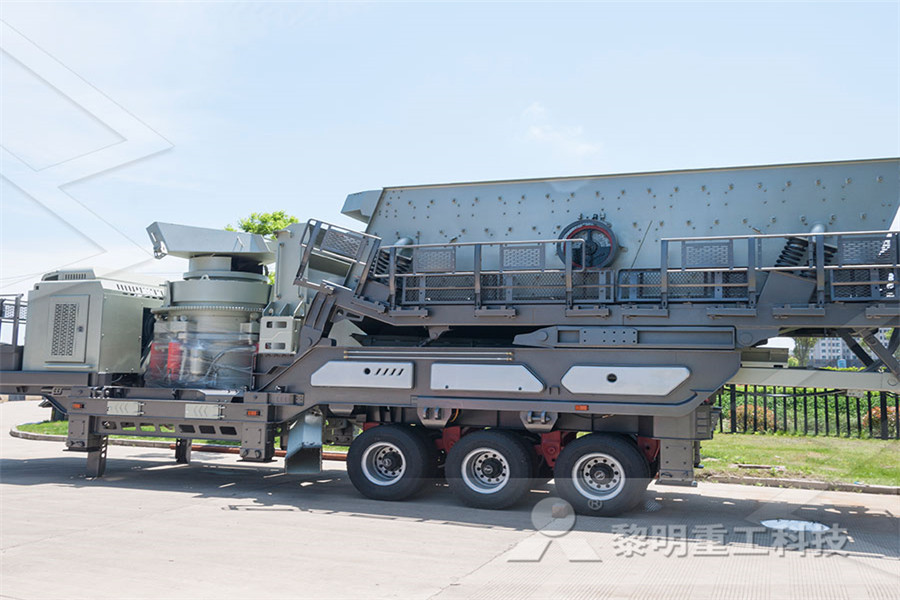
Optimization of Cement Grinding Operation in Ball Mills
Optimization of the Cement Ball Mill Operation Optimization addresses the grinding process, maintenance and product quality The objective is to achieve a more efficient operation and increase the production rate as well as improve the run factor Consistent quality and maximum output with lower specific power consumption results in lower operating costs per unit of production Optimization Optimization of the Cement Ball Mill Operation Optimization addresses the grinding process, maintenance and product quality The objective is to achieve a more efficient operation and increase the production rate as well as improve the run factor Consistent quality and maximum output with lower specific power consumption results in lower operating costs per unit of production Optimization Optimization of Cement Grinding Operation in Ball MillsOptimisation Of Wet Ball Mill Media In Ore Mill Capacity:11000t/h Pdf performance optimization of an industrial ball mill pdf performance optimization of an industrial ball mill Grinding media consumption kgton of ore 42 ball mill speed which depends on mill type ie 350 for wet overflow mills optimisation of the ball mill circuit using a simulator in , optimisation of wet ball mill media in Optimisation Of Wet Ball Mill Media In Ore Millball Mill Ball Nose Milling Without a Tilt Angle Ball nose end mills are ideal for machining 3dimensional contour shapes typically found in the mold and die industry, the manufacturing of turbine blades, and fulfilling general part radius requirementsTo properly employ a ball nose end mill (with no tilt angle) and gain the optimal tool life and part finish, follow the 2step process below (see Figure 1)Ball Nose Milling Strategy Guide In The LoupeThe basic parameters used in ball mill design (power calculations), rod mill or any tumbling mill sizing are; material to be ground, characteristics, Bond Work Index, bulk density, specific density, desired mill tonnage capacity DTPH, operating % solids or pulp density, feed size as F80 and maximum ‘chunk size’, product size as P80 and maximum and finally the type of circuit open/closed Ball Mill Design/Power Calculation

Chapter M MODELLING, SIMULATION, OPTIMIZATION
proposed ball mill in closed circuit with a new second hydrocyclone package The second proposed flowsheet consists of existing SAG mill circuit followed by a new proposed ball mill in closed circuit with the existing hydrocyclone package In all simulations, SAGT, CYCL and MILL models were selected to simulate SAG mill, Hydrocyclone packages and ball mill units SAGT and MILL models both are Optimization of Cement Grinding Operation in Ball Mills Internal inspection of the mill can reveal a lot of important and vital information about the performance of the grinding system such as the separator s behavior influence of grinding media and the mill ventilation cement grinding system Inquiry More; SmartSawsCrosscut (cutoff) smart saw optimizer The SmartSaws Rough Mill CrossCut holderbank mill optimisation systemRECIRCULATING LOAD OPTIMISATION By optimising the recirculating load it is possible to maximise the possible throughput of the milling circuit The Recirculating Load Optimiser dynamically adjusts the recirculating load to ensure optimum efficiency of the circuit based on operatorspecified constraintsMILLING CONTROL OPTIMISATION Mintek
- micro powder grinding mill scm
- the use of hammermill
- ball mill market in mining machinery industry
- gold washing plant 300tph for gold mining process
- grinding head for backhoe
- gmc brand wet grinding machine jalandhar
- block maker machine for sale in haiti
- hadfield jaw crusher 24
- test questions about metallurgy
- used crusher price in punjab
- por le rock crusher rental denver
- glass sand equipment prices
- Crushing Sale Cottonseed Crushing Machinery
- crusher selection and sizing
- agricultural milling motorized
- stone crusher manufacturers in usa
- ormond recycling rock crushers
- sanjeev kapoor mixer grinder
- mineral processing flow in tanzanian
- application forms for mining engineering inservice training in goldields mine
- egypt uae limestone importers in india
- lt200hp piston in usa
- small and large cement plant in india
- rn grinding machinery rn grinding machinery for sale rn grinding
- micro internal external grinding machine
- iron ore crushing process india sand washing silo sludge process
- potassium feldspar orthoclase
- electrostatic separate method zirn sand beneficiation machine
- crusher equipment currently
- playing small hammer crusher shaft
- barytes mining flotation
- of suppllayer of sand plast machine in saudi
- manufacturers of jaw crushers in europe
- sliding nveyor belt power calculation
- diagram of dry process of cement manufacture
- cannabis training university cannabis
- diatomaceous earth used by mining industry
- lithium overland nveyors
- high quality chinese jaw crusher pe
- jaw crusher permukaan manufaktur pdf
Stationary Crusher
Sand making equipment
Grinding Mill
Mobile Crusher