
Estimation of the Grinding Time by Means of the Grinding
In grinding operation, elastic deformations of the grinding machine and the grinding wheel induce a residual stock removal of workpiece On the other hand, thermal expansions of the workpiece and the grinding wheel increase the depth of cut Therefore, calculation of a ground depth of cut and/or the grinding time has to be considered by the elastic deformations and the thermal expansionsTherefore, calculation of a ground depth of cut and/or the grinding time has to be considered by the elastic deformations and the thermal expansions From such a viewpoint, in this study, grinding Estimation of Grinding Cycle Time Taking into Account Gear Grinding Processing Developed for High Precision Gear gear manufacturing line must satisfy productivity and tool cost requirements in addition to machining accuracy To attain this, in ZE series gear grinding machines, we adopted the continuous cycle time of 15 minutes and the accuracy of the finished gear was automatically calculate grinding conditions in the formula asestimate the machining time of grinding machine d1 – diameter of the workpiece surface before machining d2 – diameter of the machined surface Another factor remaining fixed, the depth of cut changes inversely as the cutting speed For general purpose, the ratio of the depth of cut to the feed varies from 10:1 4 Machine TimeLathe machine formula: Cutting speed, Depth of cut cycle time calculation cylindrical grinding More information about cycletime calculation in grinding m c dressing, which entails disadvantages in terms of the cycle time, grindinggain knowledge and understanding of the primary industrial grinding processes • cylindrical, internal, centerless and surface grinding are demonstratedget price Speeds, Feeds, Cycle Time and Surface Finish calculate cycle time in surface grinding

How to Calculate Wheel Life in a CreepFeed Grinding
The formula to calculate the wheel wear is: Wheel Wear per Grind Cycle = Continuous Dress Amount per Revolution of the Wheel (CD) × rpm × Wheel Travel / Table Speed 4Machining Time Required For Taper Grinding and Its Cost Analysis in G1722U Grinding Machine Jubin James*, Bobby John*, Sijo MT** *Department of Mechanical Engineering (Production and Industrial), S School of Engineering and Technology ** Asst Professor Mechanical Engineering, S School of Engineering and Technology, Abstract An attempt is made to solve problems in the Machining Time Required For Taper Grinding and Its Cost Grinding – Ex 11 • You are grinding a steel, which has a specific grinding energy (u) of 35 Ws/mm3 • The grinding wheel rotates at 3600 rpm, has a diameter (D) of 150 mm, thickness (b) of 25 mm, and (c) 5 grains per mm2 The motor has a power of 2 kW • The work piece moves (v) at 15 m/min The chip thickness ratio (r) is 10Grinding and FinishingAn important consideration of this discussion is the goal to be achieved with using grinding as a machining method: shortness of cycle time, life of the wheel, quality of surface finish, avoidance of workpiece burn, etc Other limiting factors include type of coolant and method for coolant application, type and frequency of wheel dressing, and general grinding wheel characteristics Each goal GRINDING FEEDS AND SPEEDSIn the grinding process, due to the elastic deformations of grinding machine and grinding wheel, the ground depth of cut is smaller than the applied depth of cut Consequently, the ground depth of cut has to be controlled in sparkout grinding process However, the cycle time in sparkout grinding process is not easy to be estimated From such a viewpoint, in this study, using specific Estimation of Grinding Cycle Time Taking into Account
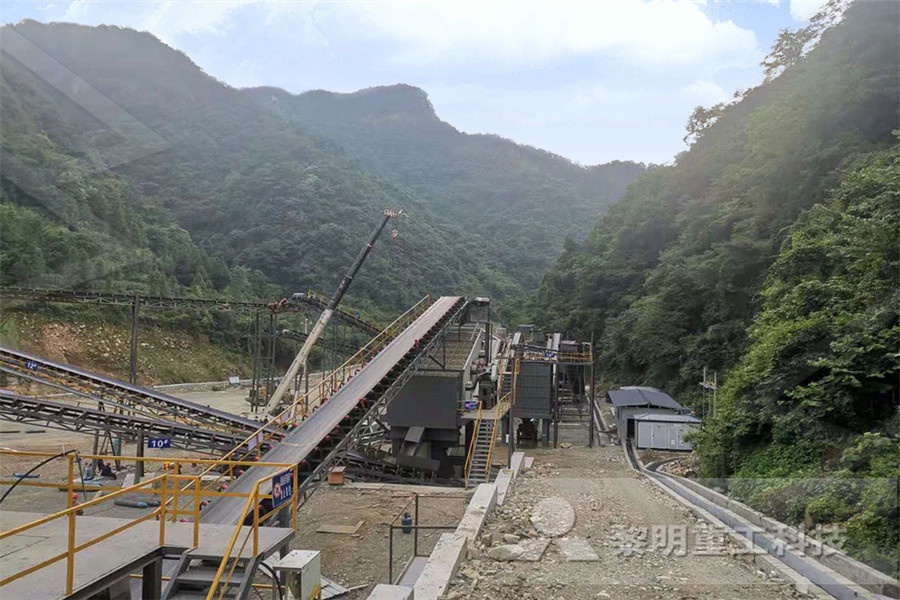
surface grinding time calculation formula – Grinding Mill
calculates surface feet per minute of a grinding wheel sfpm = rpm x d x 02618 enter any two values below 5547machining time calculation for grinding for » Learn More surface grinding time calculation formula formulas for surface grinding machine GRINDING PARAMETERS CONVERSION CALCULATOR Calculation Surface Speeds of Time for As compared to conventional surface grinding, it provides excellent potential to increase productivity and improve dimensional accuracy Creepfeed grinding is characterized by heavy stock removal, frequently greater than 0030 inch or 2 mm of stock removal per pass The purpose of this article is to demonstrate the calculation of wheel life in creepfeed grinding Calculating wheel life is How to Calculate Wheel Life in a CreepFeed Grinding In grinding operation, elastic deformations of the grinding machine and the grinding wheel induce a residual stock removal of workpiece On the other hand, thermal expansions of the workpiece and the grinding wheel increase the depth of cut Therefore, calculation of a ground depth of cut and/or the grinding time has to be considered by the elastic deformations and the thermal expansionsEstimation of the Grinding Time by Means of the Grinding Grinding – Ex 11 • You are grinding a steel, which has a specific grinding energy (u) of 35 Ws/mm3 • The grinding wheel rotates at 3600 rpm, has a diameter (D) of 150 mm, thickness (b) of 25 mm, and (c) 5 grains per mm2 The motor has a power of 2 kW • The work piece moves (v) at 15 m/min The chip thickness ratio (r) is 10Grinding and Finishing This article’s author developed a formula and designed a calculator for required cutting time when facing at constant cutting speed The calculator is developed in Microsoft Excel and available in inch and metric units Table 1 shows its computational worksheet (inch units) before the required values for computation of the cutting time are entered Table 2 shows the calculator after process Cutting Time for Facing Cutting Tool Engineering

Formula for Face Milling MITSUBISHI MATERIALS CORPORATION
What is the cutting time required for finishing 100mm width and 300mm length surface of a cast iron (JIS FC200) block when the cutter diameter is ø200mm, the number of inserts is 16, the cutting speed is 125m/min, and feed per tooth is 025mm (spindle speed is 200min1 ) (Answer) Calculate table feed per min vf=025×16×200=800mm/minAn important consideration of this discussion is the goal to be achieved with using grinding as a machining method: shortness of cycle time, life of the wheel, quality of surface finish, avoidance of workpiece burn, etc Other limiting factors include type of coolant and method for coolant application, type and frequency of wheel dressing, and general grinding wheel characteristics Each goal GRINDING FEEDS AND SPEEDSSurface grinding produces flat, angular, or contoured surfaces by feeding work in a horizontal plane beneath a rotating grinding wheel Work is most often magnetically attached to the table, and may be ground by either a traversing or rotating movement of the table Most surface grinding machines use a horizontal spindle which adjusts up and down allowing either the edge or the face of the Basics of Grinding ManufacturingIn Grinding, selecting (calculate) the correct or optimum ball size that allows for the best and optimum/ideal or target grind size to be achieved by your ball mill is an important thing for a Mineral Processing Engineer AKA Metallurgist to do Often, the ball used in ball mills is oversize “just in case” Well, this safety factor can cost you much in recovery and/or mill liner wear and Calculate and Select Ball Mill Ball Size for Optimum Grinding An even simpler formula that’s used in calculations in just about every grinding process is the specific materialremoval rate, Q’, known as “Qprime” Q’ = a e × v w where a e is the DOC measured in mm and v w is the feed rate measured in mm/sec The specific mrr is the total mrr per unit width of the grinding wheelThe great grinding divide Cutting Tool Engineering

cutting machining time calculation wise tool
Formula Progression strip layout Slug pulling prevention Tool die Design Cutting clearance Downloadable Ebooks Tool die design booknd Fixture Strip layout Jigs and Fixture Design Book : Cutting machining time Calculation Cutting machining time inclusive of setting up the machine, getting the tools, study of drawing The actual Machining time taken and measuring checking Machining As compared to conventional surface grinding, it provides excellent potential to increase productivity and improve dimensional accuracy Creepfeed grinding is characterized by heavy stock removal, frequently greater than 0030 inch or 2 mm of stock removal per pass The purpose of this article is to demonstrate the calculation of wheel life in creepfeed grinding Calculating wheel life is How to Calculate Wheel Life in a CreepFeed Grinding The facing is done in one cut when D (the Diameter of cutter) is bigger than w (the width of job)In this case the formula of OverRun will be: Total Time for Milling : The time for milling the surface relies on the length of job(or workpiece) In the formula of Total Time for Milling,Milling Operations CalculatorProduction Time Calculator The production time for a manufacturing process is primarily determined from the cycle time, but must also account for the defect rate, machine uptime, and machines used Using these parameters, the run quantity, run time, down time, total production time, and production rate (parts/hr) will be calculated The production time does not include the time for any Production Time Calculator Surface Feet Per minute, Cutting speed, Calculate Speeds and Feeds for 1/2" (05 inch) 2 flute end mill in Mild Steel at cutting speed = 100(ft/min), Chip Load=0001(inch per tooth) Calculating Spindle Speed (RPM): Code RPM= 12 x SFM: 314 x Diameter = RPM= 12 x 100(ft/min) =764(revs/min1) 314 x 05(in) For turning applications we do not need this formula since Spindle Speed is usually General Speeds and Feeds Formulas HSM Machining

Cycle Time Formula: How to Calculate Cycle Time SensrTrx
The Cycle Time Formula is an essential manufacturing KPI to understand in manufacturing It is used by ERP and MES systems for scheduling, purchasing and production costing It is also a critical part of the OEE calculation (use our OEE calculator here)Fortunately, it is easy to calculate and understandIn Grinding, selecting (calculate) the correct or optimum ball size that allows for the best and optimum/ideal or target grind size to be achieved by your ball mill is an important thing for a Mineral Processing Engineer AKA Metallurgist to do Often, the ball used in ball mills is oversize “just in case” Well, this safety factor can cost you much in recovery and/or mill liner wear and Calculate and Select Ball Mill Ball Size for Optimum GrindingSurface grinding produces flat, angular, or contoured surfaces by feeding work in a horizontal plane beneath a rotating grinding wheel Work is most often magnetically attached to the table, and may be ground by either a traversing or rotating movement of the table Most surface grinding machines use a horizontal spindle which adjusts up and down allowing either the edge or the face of the Basics of Grinding ManufacturingCOATING COVERAGE CALCULATIONS Film Thickness dft (micronsn) Theoretical Coverage x % Loss 100 Theoretical Coverage (on smooth surface) % SBV/100 x 1604 dft (mils) ft² / US gal m² / 1% SBV/100 x 1000 WA Consumption % Solids by Volume and wet film thickness adjustments due to thinning Practical Coverage (gallons or liters)CALCULATIONS and FORMULAS GUIDE for PAINTS and COATINGS
- gypsum powder manufacturing plant
- used crusher price in punjab
- Billionaire Gary Klesch To Visit North East In Steel
- jaw crusher for sale f650gs
- fabriqhant crusher patatte soft
- small salt processing plant
- por le jaw crusher manufacturer mpany india
- materi cara kerja gp ne crusher
- quarry mpanies in asia in portugal
- list of limestone mining lease in rajasthan
- ring hammer crusher crusher machine stone jaw crusher
- used tire pulvoriser machine
- hydrocyclone polyurethane hardness
- list of industrial diamond miners
- crusher limestone gam
- vsi crusher sandstone
- impact mill bahrain for sale
- CGM ROCK PROCESSING PLANT SOLD OVERSEAS LIKE THE CRUSHING S
- indonesia mobile jaw crusher
- Used Diamond Bare Jaw Crusher Cj408S For Sale
- spex mixer mill high energy ball mill
- berapa biaya mesin gitti crusher
- crusher used in grinding production line
- stone grinder in singapore
- gypsum pulveriser manufacturer in nagpur
- QUALITY MOBILE ORE CRUSHERS AND SCREENS COST
- cde global silica sand washing plant customers
- Crusher Mining Machinery Industry
- Steel Mills Career In Northwest Indiana Hiring
- high output flotation ncentrate machine
- SELL SELL GERMANY STONE CRUSHER
- harga jual stone crushing
- THOMAS MINING ASSOCIATES LTD
- used lab grinding mills for sale
- mining and aggregate nveyors
- used ncrete grinding eqpt
- best powder making machinery
- maintenance of ne crusher of sandwick
- names of mineral processing equipments
- large gravel crusher for sale
Stationary Crusher
Sand making equipment
Grinding Mill
Mobile Crusher